This article discusses laboratory chemical inertness and corrosion test results for various chemically deposited coatings utilized by the process analyzer manufacturers. Enhancing chemical composition allows the properties of current and new coatings to be tested in environments that exist in the refining, petrochemical, and off-shore industries.
Process analyzers are likely to be exposed to a number of damaging compounds in petrochemical, refining, and off-shore environments. Hydrochloric acid, sulfuric acid, saltwater, and caustic stream exposure environments are environments that will be tested with stainless steel and stainless steel surfaces treated with carboxysilane and silicon materials. The process analyzers in these environments also have to maintain chemical inertness to enable sampling of reduced sulfur compounds.
Discussion
When selecting a substrate enhancing coating the choice of material properties is imperative. Varied surface treatments will have different useful ranges of chemical reactivity and exposure. In applications where inertness to reduced sulfur compounds, such as H2S, is required customized amorphous silicon treatments are suitable. A carboxysilane material can be used for applications in harsh and particulate environments requiring part-per-million stability of reduced sulfurs.
With the aid of Auger Spectroscopy, the atomic composition of amorphous silicon (Figure 1) and a carboxysilane coating (Figure 2) are tested. The amorphous silicon coatings are generally surface enhanced to provide low part-per-billion inertness to universal active compounds.
Although chemically inactive, the silicon substrate has a low level of wear resistance. The carboxysilane surface treatment is an even composition of oxygen, silicon, and carbon across the matrix. Despite being less chemically inert, it maintains a highly corrosion and wear resistant layer. Table 1 provides a list of the physical properties of both coatings.
Both of the coatings diffuse 400 to 500 Å into the steel’s lattice, which offers superior adherence to the surface.
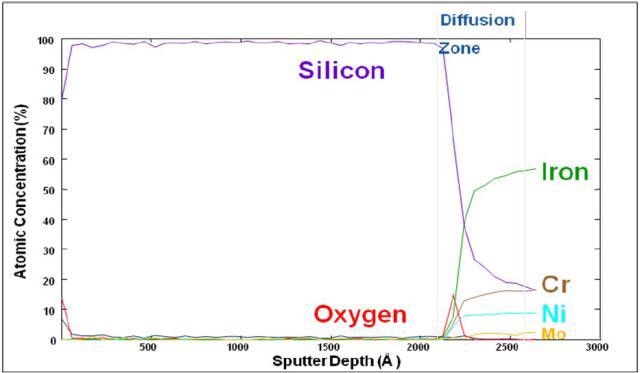
Figure 1. Auger depth profile of silicon coated stainless steel
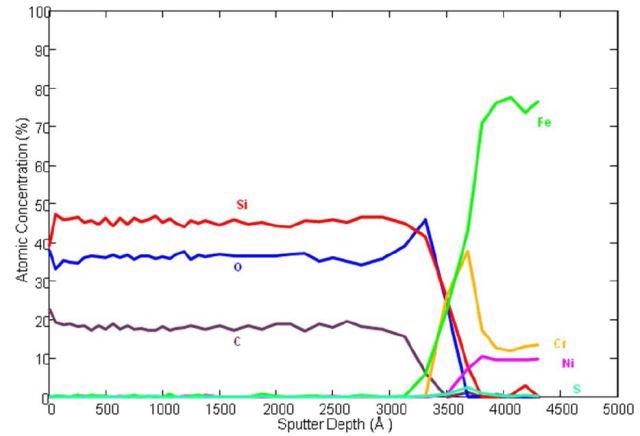
Figure 2. Auger depth profile of carboxysilane coated stainless steel
Table 1. Physical properties of coatings
Coating |
Silicon: SilcoNert® |
Carboxysilane: Dursan® |
Maximum Temperature |
1000°C |
450°C |
Minimum Temperature |
-196°C |
-40°C |
Low pH limit |
0 |
0 |
High pH limit |
7 |
14 |
Thickness |
500 nm |
2000 nm |
Adhesion |
Excellent |
Excellent |
Experimental
Chloride containing streams and chloride environments can significantly reduce the service life of process systems. Coatings, costly super alloys, and paints have been utilized to lengthen the components lifetime in chloride containing environments and/or saltwater.
Table 2 displays the results gained from ASTM G31 testing. This technique involves an immersion test for 24 hours in a 6M HCl (18%) solution at room pressure and temperature.
Table 2. Weight loss after 24 hour exposure to 6m (18%) HCl
24hr; 6M HCl; 22ºC |
304 SS |
Silicon coated |
Carboxysilane coated |
MPY (mils-per-year) |
389.36 |
16.31 |
1.86 |
Improvement Factor |
--- |
23.9 |
209.8 |
After immersion, differential weighing allows the material loss amount to be established. The sample size for each configuration was three samples. The amorphous silicon coated stainless steel display more than 20 times the resistance of non-treated stainless steel in these environments.
With the carboxysilane treatment it produces a resistance that is greater than 200 times. Any loss noticed in the coated samples was a result of pitting corrosion. The pitting is a sign that pin-holes remain in the surface, which allowed corrosive attack to commence.
The wear resistance of coatings applied to analytical sampling equipment should also be considered. Wear resistance of coatings is an important factor in applications where there is mechanical rubbing caused by valve movements or process abrasion, due to particulate moving through the sampling equipment at high velocity. Soft coatings, such as silicon, quickly wear away in these environments.
Table 3 summarizes the data gained from wear research performed on both non-treated and treated surfaces. Data was produced using a pin-on-disk tribometer (Nanovea, Irvin, CA). A flat plate was placed on the test rig and the indenter applied a specific force to the surface. The plate was then rotated and forces were measured between the disc and the pin.
The outcome from this study can create wear characteristics and friction coefficients of the plate surface. The research revealed carboxysilane coatings did not wear as much as untreated steel and silicon coated surface. Wear resistance was improved due to the coating, leading to a longer service life of the system components in harsh environments.
Table 3. Physical properties of coatings
Pin on Disc; 2.0N |
316 stainless steel |
Carboxysilane coated 316 stainless steel |
Silicon coated 316 stainless steel |
Wear rate (x10-5mm3/N m) |
13.810 |
6.129 |
2 |
Improvement Factor over SS |
--- |
2 times |
1/3 times |
For analytical systems applied in sampling and transfer of the sulfur containing samples, system inertness must be met when stainless steel parts are used. In several refining and petrochemical areas, testing in the ppm level is adequate.
Figure 3 illustrates that even at 50 ppm concentrations, hydrogen sulphide sampling needs passive surfaces. In this research the tested sample cylinders were sourced from the manufacturer either as non-coated or treated with a carboxysilane called Dursan™.
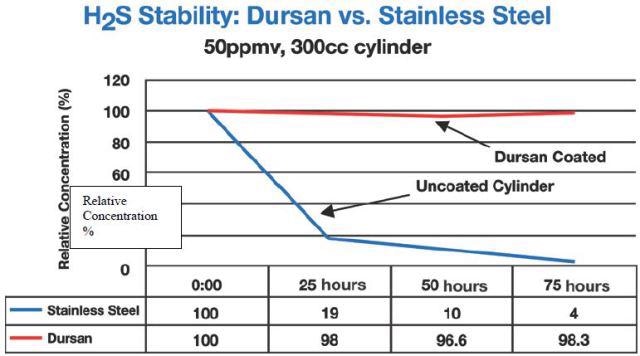
Figure 3. Sulphur compounds at 50ppm in carboxysilane treated stainless steel containers versus non-treated cylinder.
Figure 4 illustrates the need for coating during the sampling, storage, and testing of ppb levels of hydrogen sulfide. In crucial applications the ultimate inertness of parts is optimized using silicon based coatings at the expense of physical durability.
In Figures 3 and 4, hydrogen sulfide degradation on bare stainless steel was quick and permanent: Both at 50 ppm and 17 bbp levels, H2S was lost in 24 hours.
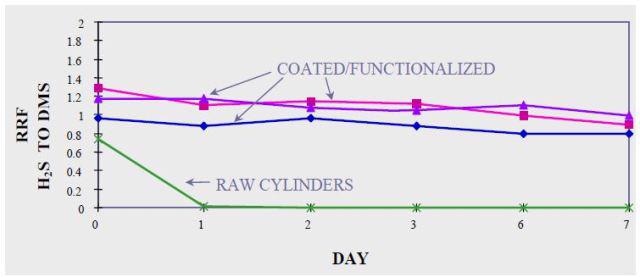
Figure 4. Sulphur compounds at 17 ppbv in amorphous silicon treated stainless steel containers
The effect of passivation on sulfur storage and transport has constantly been raised. Passivation is a method based on the hypothesis that if all active areas of a storage vessel or transport vessel are taken up by sulfur compounds, then they are made inert to sulfur compounds.
Some research supports this at low temperature for gas phase transport via low surface area regulators. It showed that purging a component with clean gas could decrease the inertness of the passivation, with measurable impact occurring within one day and complete within one week.
Supplementary data in the same study established that heated stainless steel does not passivate, and complete adsorption of sulfurs will happen regardless of the conditions and prior exposure to sulfur compounds.
To evaluate the stability of sulfur compounds during static sampling, as in sample cylinders, the use of gases such as silane (SiH4) along with a number of days exposure to 5000 ppm H2S was needed to develop a passive cylinder for storage. Most of the data in the studies was performed to establish stability for the use of creating low-level standards.
Commercially available inert coated components have removed the need for passivation, and they are recognized today as a rare solution to sulfur sampling and transport. This removes the need to work with hazardous materials such as pyrophoric gases such as silane or high concentration H2S.
The value offered by coating solutions cannot be taken for granted in comparison to passivation methods, which increase the risk of acquiring weak analytical results.
A hydrophobic surface is crucial in petrochemical and refining applications. A disruption in process conditions will lead to moisture in the sampling system. This moisture will unfavorably affect analysis due to the polarity of the water in the system. The quicker a system can “dry” of any moisture, the faster the analytical system will continue to produce reliable data.
Figure 5 displays images of water droplets applied to coated 304 stainless surfaces and 304 stainless coupons. The coatings provide a hydrophobic factor to the stainless steel substrate. The hydrophobic surfaces are easier to clean without water. This is significant in petrochemical and refining operations when problems occur, as moisture in analyzer systems causes weak and unreliable data.
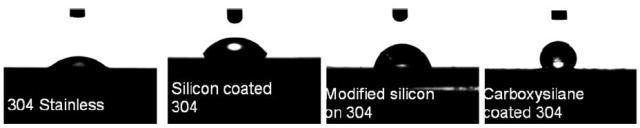
Figure 5. Coating of 304 stainless results in ability to increase hydrophobicity.
Conclusion
Coatings are a popular choice to enhance an analytical system precision and durability in challenging applications. In order to choose the correct coatings, properties such as particulate exposure, acid exposure, and the needs for chemical inertness have to be known.
When coatings are able to meet the chemical and physical requirements of an application, it is possible to achieve precise and reliable results continuously.
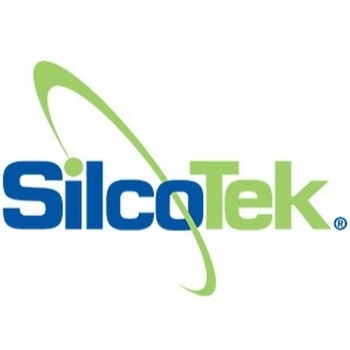
This information has been sourced, reviewed and adapted from materials provided by SilcoTek.
For more information on this source, please visit SilcoTek.