Feb 15 2002
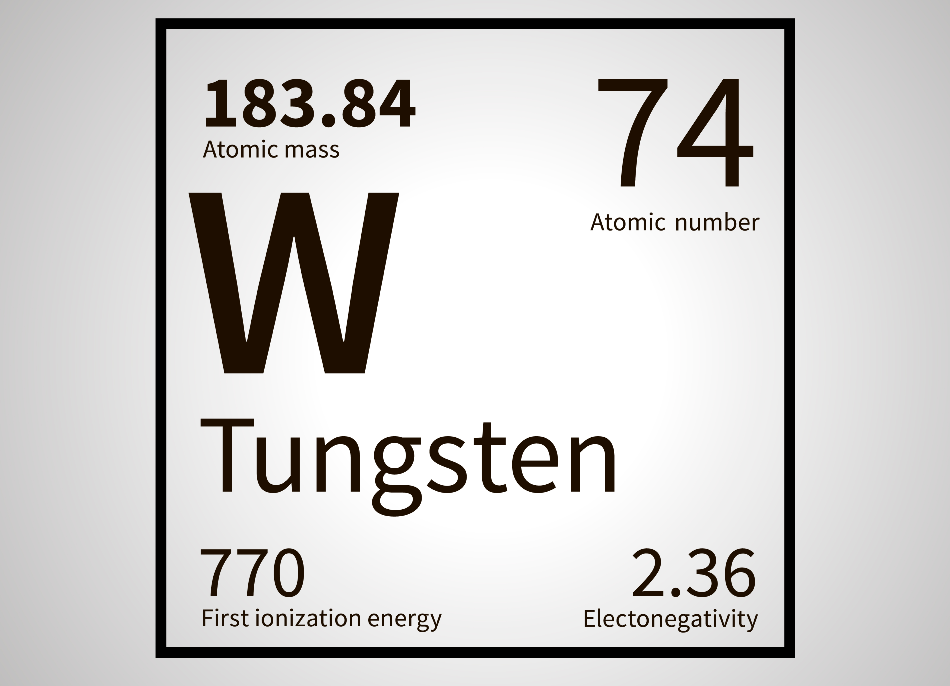
Lars Poyansky / Shutterstock
Cobalt-chromium-tungsten alloys often referred to as stellite, are a group of wear-resistant alloys used in valve seats and pistons, bearings, mill inliners, etc. That is, applications where a tough wear-resistant material is necessary.
Superalloys are cobalt, nickel, or iron-based alloys with high contents of tungsten, tantalum, molybdenum and, currently, also rhenium. They are used in applications where high mechanical strength along with superior erosion resistance at high temperatures is required, such as, in turbine blades for space vehicles, aircraft, etc.
Tungsten heavy metal (heavimet, densalloy) is a sintered pseudo-alloy of tungsten containing an iron-nickel or iron-copper binder for applications where a non-brittle high-density material is needed, for example, for darts, for counterweights in airplanes, or for weights in golf club heads. Tungsten heavy metal is also employed in armament applications, for instance, as high-velocity penetrators in anti-tank weapons. The density of the available grades ranges between 17 g/cu. cm and 19 g/cu. cm.
Tungsten is often used as an additive to niobium (maximum 15% W) and tantalum (maximum 10% W) to enhance creep resistance and high-temperature strength.
Wear Protection
Several methods are applied to guard equipment against wear.
Structural or functional parts can be made entirely from stellite, cemented carbide, or a superalloy. Alternatively, cemented carbide parts can be soldered onto certain surface areas.
Hardfacing by welding is often used to protect certain areas with a hard layer in the millimeter thickness range. For this reason, sintered or tube-type welding electrodes are available to create wear-resistant surface layers. Tungsten monocarbide or cast tungsten carbide is a hard constituent, while most often, iron or an iron-based alloy serves as a binder.
Thermal spraying is applied to form thinner wear-resistant surfaces. Powders for hardfacing are, for instance, made using pure tungsten or more often tungsten monocarbide and/or cast carbide integrated with nickel, cobalt, or a Ni-Cr-B-Si alloy. A large range of grades is available to fulfill nearly all requirements.
Chemical vapor deposition, beginning from tungsten halogenides or alkoxides, is a less common technique to provide hard, acid-resistant tungsten coatings on bearings, rolls, dies, gauges, etc.
Diamond Tools
In some cases, even tungsten carbide tools are not sufficiently hard. This is where the more costly diamond tools find their use. A majority of these diamond tools contain tungsten and/or tungsten carbide to enhance their properties.
- Diamond drill bits for hard rock drilling: Coarse diamonds form the tool’s surface, while metal (like bronze) infiltrated cast tungsten carbide forms the tool’s body. The tool’s shoulder is metal infiltrated coarse tungsten metal powder.
- Diamond tools for construction, like, natural stone and concrete cutting: Common tools are tube-shaped saws for hole-cutting, or circular saw blades for straight cuts. Both of them are tipped with cemented diamond segments, where tungsten monocarbide (WC) and/or cast carbide grains are often used to support the diamonds in the comparatively soft cobalt or bronze binder.
- Diamond or cubic boron nitride (CBN) cutting tools typically have a cemented carbide body because of its high-pressure strength, fitted with a cutting edge made from sintered diamond or CBN.