Hydrogen (H2) is a chemical element that is used in a wide range of applications, such as in the synthesis of ammonia, hydrogenation of unsaturated organic compounds, hydro-treating of petroleum feedstocks to remove nitrogen and sulfur, and as a fuel for proton exchange membrane (PEM) fuel cells. Currently, more than 90% of H2 is produced through steam reforming of hydrocarbons and natural gas. The syngas (carbon monoxide (CO) + H2) generated by steam reforming is processed via low-temperature water gas shift (WGS) and high-temperature WGS reactions to further use CO in the syngas to generate additional H2 from water. This is later followed by purification of H2.
Fe2O3-Cr2O3 is a high-temperature WGS catalyst that is commercially available in the market, while CuO-ZnO-Al2O3 is a low-temperature WGS catalyst. Although these catalysts are employed in commercial hydrogen plants, they are not suitable for applications that require compact reactors, for instance in fuel production for PEM fuel cells, due to the low activities of these catalysts. For mobile or distributed applications, reactors using conventional WGS catalysts are large and bulky. In addition, both conventional catalysts experience a pyrophoric issue when exposed to air, which may cause safety issues. Pre-reduction must also be performed for these catalysts.
To simplify the design of the system, engineers at Nexceris have developed a highly active WGS catalyst, based on proprietary nanoscale mixtures of evenly integrated precious metals and mixed oxides.
Reformance-WGS™ Performance
To exploit the performance improvement in the Reformance-WGS™ catalysts, specialized metal supported technologies have been integrated into them to provide excellent heat transfer and mechanical robustness. Benefits include:
Advantage #1: Excellent Intrinsic WGS Catalysts Activity
In order to improve the WGS activity, Nexceris engineers have exploited the designs of mixed oxides and precious metal catalysts that were initially designed for on-board fuel reforming for PEM fuel cell applications. To test the performance of WGS, a tubular reactor was filled with Reformance-WGS™ granules of 35-60 mesh size (Figures 1 and 2).
.jpg)
Figure 1. Water gas shift activities on Reformance-WGS™ and a commercial FeCrOx catalyst under the conditions of 1 atm, 6.9%CO, 31.0%H2O, 10.3%CO2, 50.3%H2, 1.4%N2 and GHSV = 60,000 ml/g-hr.
.jpg)
Figure 2. Water gas shift activities of Reformance-WGS™ and a commercial CuZnAlOx catalyst under the conditions of 1atm, 6.9%CO, 31.0%H2O, 10.3%CO2, 50.3%H2, 1.4%N2 and GHSV = 300,000ml/g-hr.
In Figure 1, higher CO conversion is exhibited by Reformance-WGS™ compared to the competing Fe-Cr oxides at temperatures of 200 to 375°C, and also (in Figure 2) outperform Cu-Zn-Al oxides when the temperature is over 280°C. These factors make Reformance-WGS™ an excellent medium temperature catalyst for single-stage reactor systems. This catalyst was washcoated on a cordierite monolith and then tested (Figure 3).
.jpg)
Figure 3. Water gas shift activities of Nexceris catalyst wash coated monolith under the conditions of 1atm, 6.9%CO, 31.0%H2O, 10.3%CO2, 50.3%H2, 1.4%N2 and GHSV = 20,000h- 1.
As shown, equilibrium conversions of CO were acquired at a GHSV of 20,000 h-1 and at a temperature of 290°C with Reformance-WGS™, while the competing conventional CuO-ZnO-Al2O3 catalyst is unable to achieve such high conversions. The outcomes have shown that Nexceris’ catalyst offers a number of benefits over the commercial WGS catalysts. These benefits include:
- Activation not required before use
- Improved activities at medium temperatures, where kinetics are more optimized
- Non-pyrophoric properties when exposure to air
- Activity ideal for catalyst washcoating technologies, like enhanced ruggedness and reduced weight and size
Advantage #2: Improved Heat Transfer from Aluminized Metal Substrates
Foam structures, metallic monolith, and high thermal conductivity serve as excellent substrates for both exothermic and endothermic reactions (Figure 4).
.jpg)
Figure 4. Metal monolith supported catalyst
The metallic substrates provide the following advantages for WGS reactions:
- They have good thermal conductivity, enhancing the transfer of heat. As the reactions will be occurring under thermodynamically favorable conditions, the production of H2 will improve considerably. Unnecessary formation of methane and slow catalyst sintering deactivation in the case of PGM catalysts is reduced through reduction of hot spots in the WGS bed.
- High geometric specific surface area in the metallic substrates produces excellent contact between the gas and the surface and also improves mass transfer.
- Thanks to the open structures, pressure drop is reduced, which reduces the operating costs. The metal components are also expected to pack in a more uniform manner, enhancing pressure drop consistency in the reactor.
- Excellent mechanical strength is exhibited by the supports.
- Instead of thick sintered beads, ultra-fine catalyst coatings improve intra-particle diffusion of products and reactants, enhancing the activity of the catalyst. When the metal substrates are coated, a low pressure drop can be acquired and at the same time, high catalyst surface area can be preserved.
- The metallic substrates offer a low-cost substrate and an affordable format for catalysts that are extremely active in WGS but prove costly as bulk pellets or shapes. If a catalyst-coated metal substrate is used to develop a reactor, then buried catalyst can be prevented and the amount of catalyst required is reduced by as much as 85 to 90%.
Advantage #3: Customized Substrate/Catalyst Interfaces
Increased catalyst loading on the substrate can translate into increased reactor activity, but dense layers can produce poor adhesion because the thermal difference between the catalyst layer and the metallic substrate surmounts the bond’s shear strength at the interface between them. While a ceramic layer can be created at the surface, by oxidizing traditional metallic substrates, these layers tend to be relatively thick and smooth and have restricted anchoring sites for the coating.
Nexceris has devised an Alumi-Lok™ aluminization process for metals, which is cost-effective and also delivers high performance. The pure metal surfaces are coated with an aluminum precursor coating, and they are oxidized to produce a three-layered microstructure, containing a highly porous alumina top-coat (Figure 5a—Region I), a diffusion layer of aluminide (Region II), and a skeleton of metallic nickel alloy (Region III).
.jpg)
Figure 5. Cross-section SEM images with overlay compositional EDS maps of aluminized steel foam achieved using Alumi-Lok™ aluminization technology.
The porous layer of Al2O3 is a high-surface area that is suitable to washcoat an interlocking layer of catalyst. The Region II aluminide diffusion layer and the Region III metal skeleton layers sustain good mechanical ruggedness and thermal conductivity. These features collectively produce useful and unique substrates for the applications.
Structured-catalyst developed by Nexceris exhibits excellent properties for the production of H2. Metallic substrates have a high thermal conductivity that can mitigate hot spots and power the WGS reactions toward a thermal-equilibrium-favorable direction. Using the new technique of material synthesis, Nexceris can generate WGS catalyst that has better intrinsic stability and activity. By using the Alumi-Lok™ aluminization process to customize the catalyst and substrate interface, loading and adhesion of catalysts on the substrates can be increased. H2 productivity is considerably increased on Nexceris’ novel catalyst when it is applied to fixed-bed reactors as opposed to the traditional WGS catalysts.
Download the White Paper for More Information
Commercial Implications
The shift catalyst developed by Nexceris can be produced in the form of pellets and ceramic or metallic washcoated monoliths. Monolithic designs enable better utilization of the catalyst and also minimize reactor backpressure. When small reactors are required to produce H2, metal supported catalysts can be applied to fixed bed reactors to change CO into H2 at 300 to 400°C. This packaging method provides significant size and weight benefits. Based on the computations, the size of the reactor can be reduced to 5 to 10% of the existing two-stage WGS systems.
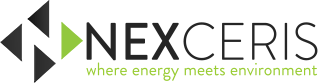
This information has been sourced, reviewed and adapted from materials provided by Nexceris, LLC.
For more information on this source, please visit Nexceris, LLC.