Historically, the corrosion protection of iron- and nickel-based alloys has been improved by aluminide diffusion coatings. The formation of iron or nickel aluminides through controlled diffusion of aluminum into the iron- and nickel-based alloy enhances their resistance to carburization, sulfidation, and oxidation. The main disadvantage of these diffusion coatings is that they are usually formed using expensive techniques, such as vapor-phase or CVD aluminization and pack cementation. These techniques are designed to produce small, high-value components, but are not suitable for inexpensive, high-volume production processes. As a result, these technologies are restricted to applications where the value imparted offsets the high cost of the techniques.
In contrast, the AlumiLok™ coating technology developed by Nexceris produces aluminization coatings with simple application techniques and heat-treatment methods. This technology enables exceptional oxidation protection for a broader range of nickel alloys and stainless steels. The method can be adapted to cover the coating region, and is well suited to different pre- and post-coating manufacturing processes. This technology is used extensively in components that need protection from oxidation or corrosion during large-scale manufacturing processes.
The AlumiLok™ Coating Process
The AlumiLok™ coating technology utilizes simple slurry coating and heat-treatment procedures to produce coatings with the corrosion resistance and microstructure similar to the ones produced by expensive vapor-phase and pack-aluminization procedures (Figure 1). The coating produced using the AlumiLok™ coating technology has exceptional resistance to chromium volatilization, oxidation, and coking on a broader range of common stainless steels. Due to its proven scalability and cost-effectiveness, AlumiLok™ coating technology could reduce manufacturing costs for materials engineers, allowing Inconel components to be replaced with common stainless steels.
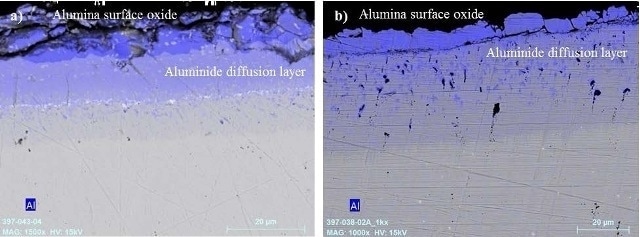
Figure 1. Cross-section SEM with superimposed Al EDS compositional map of coatings formed on 316SS by (a) Nexceris’s AlumiLok™ technology and (b) vapor-phase aluminization.
The AlumiLok™ coating process includes a coating stage and heat-treatment stage. The coating technology allows simple deposition processes to form well-defined coating patterns on both simple and complex parts. Dip coating, roller-painting (Figure 2a), drain casting (Figure 2b), and aerosol spray deposition (Figure 2c) are processes that have been validated in the lab. The AlumiLok™ coating materials have also been successfully scaled to various semi-continuous and continuous automated spray systems.
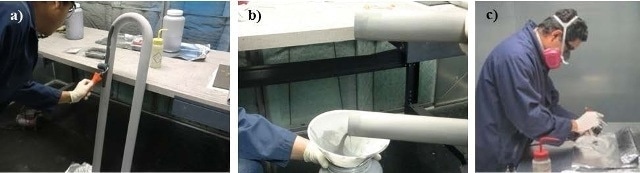
Figure 2. Examples of coating application: (a) roller-coating exterior surfaces, (b) slip-coating interior surfaces, and (c) hand-spraying.
AlumiLok™ suspensions are designed to be easily patterned to enhance process flexibility. Figure 3 illustrates the masking flexibility of the AlumiLok™ coating process. Here two different ceramic coatings are applied: the AlumiLok™ coating and a high-temperature electrical conductor coating. The as-deposited coating can be masked simply, and can be removed by washing up to the heat-treatment stage. Common abrasive techniques can also be employed to remove the heat-treated coating post-processing.
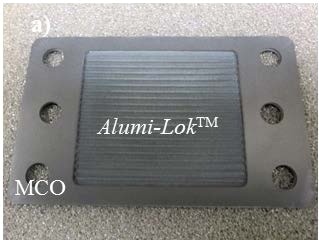
Figure 3. Dual coated metal component, demonstrating masking control of deposition area. The ribbed central region is the AlumiLok™ coated area. The perimeter is coated with (Mn,Co)3O4 (MCO).
An assessment of the AlumiLok™ coating technology was made in coordination with standard manufacturing techniques to further enhance the AlumiLok™ coating process flexibility. This technology was found to have distinct cost-effectiveness when coating tube stock or sheet metal and during the subsequent formation of the final component from the coated material. To check the viability of this process, certain initial experiments were performed.
An AlumiLok™ coated 304 stainless steel sheet successfully rolled into a cylinder with a diameter of 5.5” is shown in Figure 4. Figure 5 illustrates the microstructural analysis of the coated material. There was no evident damage to the AlumiLok™ coating microstructure during the forming operation. Spot welding of the coiled component was then performed by standard processing to produce a thin-walled combustion liner.
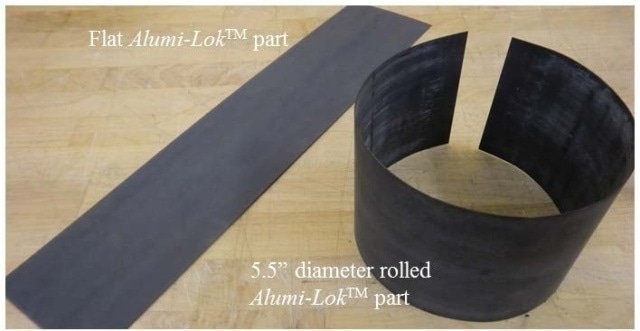
Figure 4. Flat and formed (rolled into 5.5” diameter cylinder) AlumiLok™ coated 304SS sheet.
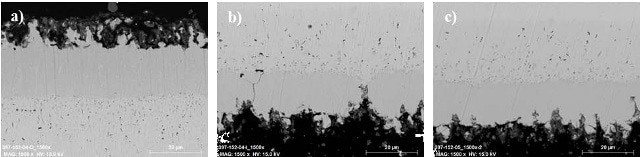
Figure 5. Cross-section SEM micrographs of AlumiLok™ coating microstructure on formed (rolled) (a) inside surface, (b) outside surface, and (c) flat non-formed surface of 304SS sheet.
AlumiLok™ Coating Performance
High Temperature Oxidation Resistance
Figure 6 illustrates a comparison of the long-term isothermal oxidation performance of AlumiLok™ coated 316 stainless steel, with vapor-phase aluminized, uncoated 316 stainless steel. The photographic inserts in the figure depict the appearance of the samples after being exposed to humidified air for 4000 hours at 900°C. Unable to withstand these conditions, weight loss was evident in the case of uncoated 316 stainless steel, indicating spallation of oxidation products within 500 hours. Vapor-phase aluminization (VPA) was found to enhance the oxidation resistance of 316 stainless steel, as stable oxidation behavior was noted up to 3000 hours. However, rapid degradation and weight loss were evident in the case of the VPA 316 stainless steel samples beyond 3000 hours. Stable oxidation behavior and exceptional oxidation resistance were exhibited by the AlumiLok™ coating up to 4000 hours.

Figure 6. Isothermal oxidation weight change for uncoated 316, AlumiLok™ coated and vapor-phase aluminized 316SS at 900°C for 1000 hours in humidified air.
Resistance of Active Corrosion (Combustion Environments)
The investigation was repeated under a high chloride environment, representing biomass combustion environments. The predominant mechanisms of corrosion are hot corrosion caused by molten salt deposits and chlorine-catalyzed active oxidation. Figure 7 shows a comparison of the corrosion resistance of AlumiLok™ coated 430 and 304 stainless steels with aluminized steel, uncoated stainless steel, and FeCrAl samples exposed to an atmospheric air containing potassium chloride (KCl deposit) at 650°C.
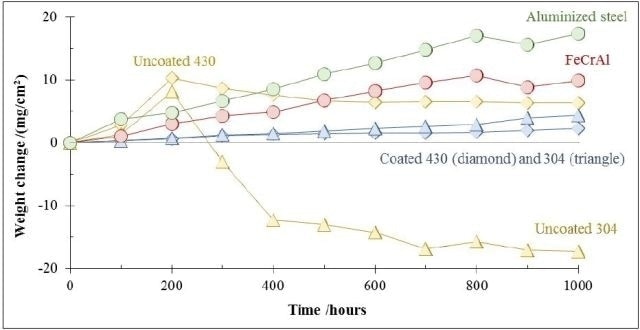
Figure 7. Corrosion behavior of uncoated and AlumiLok™ coated 430 and 304 stainless steels, aluminized steel and FeCrAl samples under biomass combustion environments, at a temperature of 650°C in an atmosphere of air containing potassium chloride. The chloride rich atmosphere is achieved by resting the samples over a deposit of potassium chloride crystals.
In this highly corrosive environment, uncoated 430 and 304 stainless steels are easily degraded. This results in the formation of a thick, non-protective dual-oxide scale exhibiting rapid exfoliation within 200 hours. In the case of the AlumiLok™ coating, a stable alumina/aluminide surface microstructure is formed. This microstructure formation eliminates non-protective oxide formation, successfully preventing corrosion and exfoliation on both 430 and 304 stainless steels. In this combustion environment, AlumiLok™ coated 430 and 304 stainless steels exhibit a higher corrosion resistance compared to FeCrAl and aluminized steel samples.
Download the White Paper for More Information
Commercial Implications
In high-temperature industries, the material requirements are highly critical. The materials are expected to withstand highly corrosive and high-temperature environments for long periods of time. The AlumiLok™ coating technology developed by Nexceris is a cost-effective alternative to enable scalable high temperature, coking, oxidation, and corrosion protection. This allows expensive nickel-based alloys to be replaced with low-cost stainless steels.
The AlumiLok™ coating technology provides unique coating protection, with matte oxide coatings for enhanced coking resistance and corrosion protection. This technique also enables a reservoir of self-repairing aluminum to be imbued into the underlying alloy, eliminating the micro-scale defects.
Nexceris’ product development strategies are developed with the scalability and simplicity of the manufacturing process in mind. Ongoing applications include the protection of burner components, high-temperature electrical components, and heat transfer devices, where in addition to corrosion protection, the coating also ensures improved emissivity.
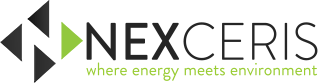
This information has been sourced, reviewed and adapted from materials provided by Nexceris, LLC.
For more information on this source, please visit Nexceris, LLC.