For a very long time, coal fired plants have been aware of the effect of mercury on operations, but until now gas and oil production, processing and transport operations have been unaware of the contamination of mercury in process streams (Figure 1). Iincreased amounts of mercury can be produced by some regions in gas and oil wells, but as wells become old the content of mercury increases.
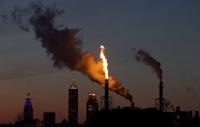
Figure 1. Coal fired plant
Impact of Mercury in Oil and Gas Streams
It is possible to emit mercury to the atmosphere either during steam cleaning or through flares. Mercury amounting to 1 ppb or less can accumulate in downstream, midstream, and upstream processing systems. The accumulation of mercury takes place over a number of years, and this makes a sub part per billion "minor" mercury contamination problem a major 500 ppb+ contamination and clean up. As a result of this, up to 11 tons of mercury are annually produced in gas and oil processing plants. It is possible to release increased amounts of mercury during venting and maintenance, jeopardizing the environment and personnel.
Paying the Piper
A major impact can occur when a pipeline or a plant has to be decommissioned (Figure 2). Mercury is promptly absorbed into steel and stainless steel surfaces, increasing the price and complications of the mercury decontamination of processes. Some of the mercury can be removed by just heating the surface, but huge amounts of this element would still be present.
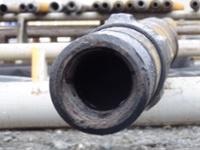
Figure 2. Decommissioning a plant or pipeline
What to do?
It is necessary to be aware of mercury contamination in holding tanks, piping, and systems. Emission sources should be frequently tested to evaluate the contamination potential. Just a small amount of mercury can lead to major accumulation of mercury over time. In fact, 4 ppb of mercury in feedstock can produce a concentration as high as 1000 ppb in process streams. In every plant, it is essential to test feedstock emission sources during mercury maintenance cycles. This way, the accumulation of mercury can be prevented. A remediation company can be employed if there is an increase in the level of mercury contamination. This remediation company will help to remove mercury in the plant from time to time.
Maximize Reliability
Trace mercury builds up in systems over time, and it is imperative to detect trace mercury in order to enhance the monitoring and evaluation of build-up over time (Figure 3). However, executing a reliable, precise mercury testing process can be a challenging task. Trace mercury detection becomes more difficult when mercury reacts or is adsorbed into flowpath surfaces. Flowpaths lined with an inert coating like SilcoNert® 2000 help to prevent mercury adsorption in sample transfer systems, guaranteeing reliable measurements.
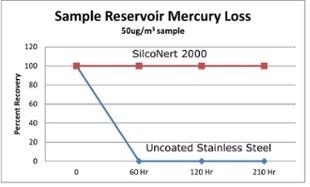
Figure 3. Sample reservoir mercury loss
Take Precautions
Potential mercury emissions should be maintained at flares, and during a potential for release. It is essential to be aware of potential mercury exposure sources, and the fact that upstream mercury content and feedstock can potentially change over time.
Get Help
Mercury accumulation in a plant must be measured by testing feedstock, flares, and the maintenance process. If the level of mercury contamination increases, a remediation company can be employed to regularly remove the mercury present in the plant.
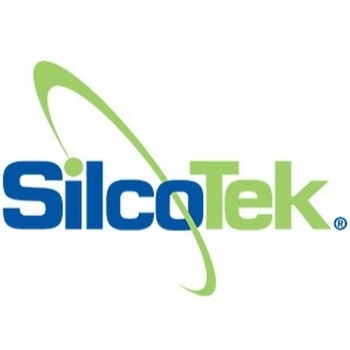
This information has been sourced, reviewed and adapted from materials provided by SilcoTek.
For more information on this source, please visit SilcoTek.