Refiners are in the process of ensuring compliance with Sub Part Ja of the EPA's Title 40, which regulates flare emissions from petroleum refineries. Even though these flare projects will soon be completed, refiners will have a new objective to meet, as deadlines for implementation of Tier 3 gasoline standards are rapidly approaching.
By 2017, refiners will have to cut down the amount of sulfur in gasoline from 30 ppm, as allowed under Tier 2 rules, to just 10 ppm.
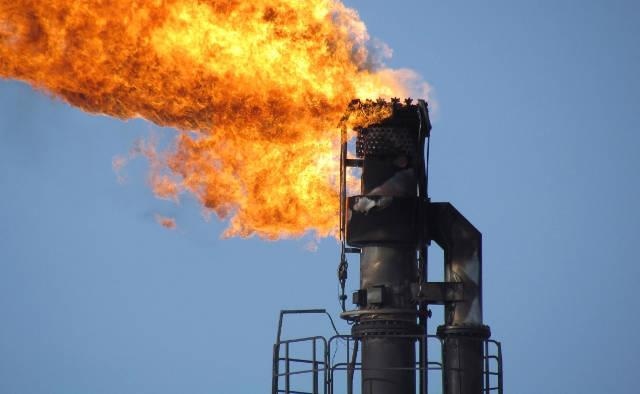
Projects to make refineries compliant with Sub Part Ja are now nearing completion, but tighter regulations on sulfur in gasoline are on the horizon. Image credit: Leonid Eremeychuk/Shutterstock.com
The EPA predicts that the requirements of the new standard can be fulfilled if refiners make "minimal" changes to operations. Refiners feel that they will have to expand hydrotreating processes, most specifically in naptha created in fluidized catalytic cracking (FCC) units.
Refiners believe that they would need to spend up to $10 billion in enhancements and an extra $2.1 billion per year in terms of operating costs. The project is expected to continue for more than 2 years. Hence, this is the perfect time to start Tier 3 planning.
In the midst of significant ongoing capital projects, it is easy to forget the sampling system, which is a vital aspect of compliance.
Reduction in the sulfur detection limit will increase the impact of active sites in the sample flowpath. What was believed to be a minor source of sulfur adsorption/loss under Tier 2 level will become a significant issue under Tier 3.
The impact of one adsorption site under Tier 3 could be the difference between a significant shutdown and compliance (Figure 2).
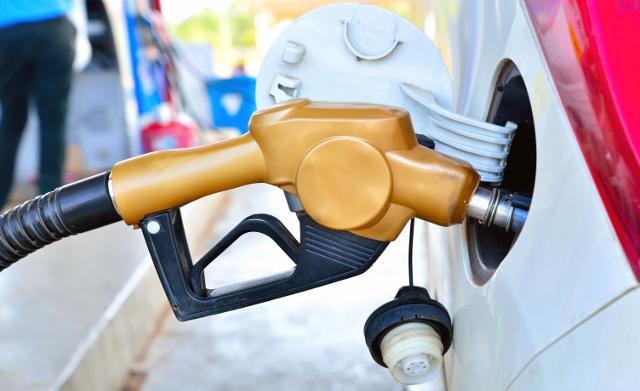
Figure 2. Tier 3 gasoline regulations will require a much lower sulfur concentration, which will have implications for the required sampling methods. Image credit: moomsabuy/Shutterstock.com
SilcoTek® coatings play a key role in obtaining Tier 3 refinery compliance. Dursan® and SilcoNert® 2000 are inert coatings that coat the whole sample pathway to ensure an inert flowpath.
Ultimate Inertness
Adsorption of H2S and various other compounds in tubing, sample cylinders, and a wide range of other sampling surfaces is prevented by SilcoNert® 2000.
SilcoNert prevents H2S loss in such an efficient manner that it allows samples to be stored for a period of 14 days or even longer without affecting sample integrity (Figure 3). Without SilcoNert, the sample will be fully adsorbed into the stainless steel sample cylinder within a matter of hours.
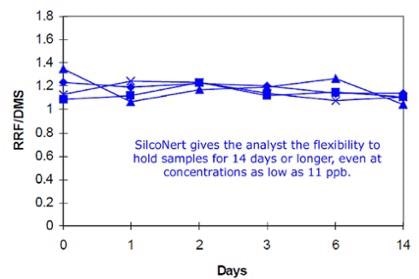
Figure 3. SilcoNert effective in preventing H2S loss.
Incomparable Response
The old wise saying, do you want it right or do you want it now has been turned on it’s head. With SilcoTek coatings, operators can instantly obtain the right sample.
In contrast to uncoated tubing, which can take hours, response time via SilcoNert® coated tubing is brought down to seconds (Figure 4). A near zero adsorption surface enables oil and gas professionals, coal operators, and refiners to instantly examine and rectify eh variable process conditions. Failure to react promptly can lead to product quality issues and also cost refiners and other operators millions of money in shutdown costs.
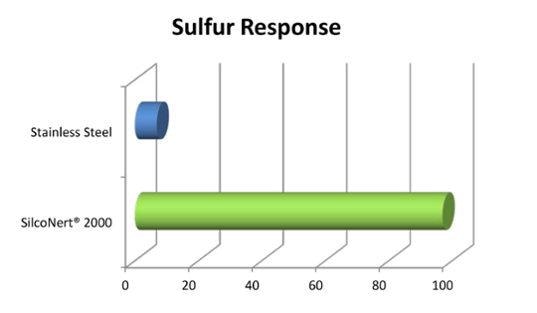
Figure 4. Sulfur response time
Conventional Sulfur Management is Insufficient
Not coating the entire sample flowpath results in major issues. It is not possible to achieve significant sample results by using sampling methods for 30 to 50 ppm sensitivity.
Given below are a few ways that will not be effective for monitoring at the 10 ppm level:
-
Uncoated analyzer tubing - Just a few inches of uncoated stainless steel tubing lead to sample loss.
-
Untreated filters - Fritted filters comprise a huge surface area. Not coating that filter results in adsorption of most, if not all the sample.
-
Uncoated regulators - Even components with a short exposure to the sample will hinder the quality.
-
Rusty sample cylinders - Rust particles absorb active compounds, making sampling a futile exercise.
-
Steam cleaning with dirty steam - Active sample compounds are absorbed by particulates in steam which is another source of futility.
-
Uncoated fittings - One uncoated fitting is capable of adsorbing a large amount of H2S.
-
Priming - At 10ppm, an uncoated fritted filter will adsorb active compounds like sulfur for months before the users receives a signal.
Conclusion
Dursan® and SilcoNert® have been proved to enhance response and sensitivity. Coating the complete sampling flowpath guarantees compliance and enables operators to concentrate on operations, not troubleshooting an inconsistent sampling system.
Download the SilcoTek Refinery application note for more information about SilcoNert® 2000 for sulfur sampling.
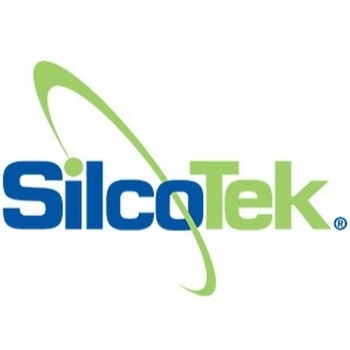
This information has been sourced, reviewed and adapted from materials provided by SilcoTek.
For more information on this source, please visit SilcoTek.