Carbon fibers are anisotropic carbon ranging between 92 and 100 wt%. Generally, carbon fibers have exceptional tensile property, high thermal and chemical stability, good thermal and electrical conductivity, low density, and superior creep resistance.
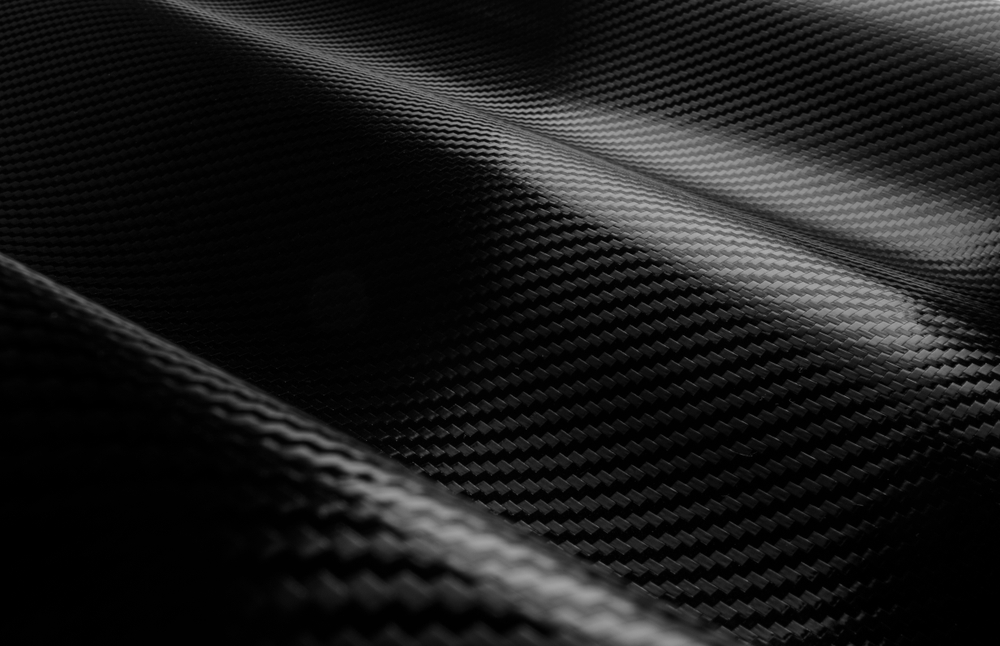
Image Credit: Shutterstock/Septimiu Balica
Several industries such as military, construction, aerospace, medical, automotive, and sporting goods are eager to use the outstanding properties of carbon fibers.
Polyacrylonitrile (PAN) is the most important precursor required to manufacture carbon fibers. The consumption of carbon fiber is growing, while the automotive industry struggles with rising costs and the lack of a high-speed fabrication methods. In order to reduce the manufacturing cost and scale up production a clear understanding of the carbon fiber manufacturing method is vital.
Carbon fiber production using PAN is performed in a carbonization line, which includes three characteristic steps: ovens, LT, and HT. Each manufacturing step has its own set of challenges. To successfully accomplish the production, the focus should be on the LT furnace where most of the fiber mass loss occurs. The temperature within the LT furnace is usually between 400 and 800°C with mass loss of 30 to 40%.
The furnace has a single tow band with residence time between 60 and 90 seconds. It is crucial to achieve consistent fiber quality throughout the system widths, which have been increasing due to the growing capacity needs. The new systems are 3 to 4 m wide compared to the conventional 1 to 2 m wide systems.
It is challenging to achieve uniform conditions across increasing widths, considering the height of the system is minimal. By maintaining consistent process gas conditions and temperature, consistent fiber properties can be achieved.
The first part of this article deals with the definition of the properties of the off-gas, and the second part deals with computational fluid dynamics (CFD) analysis of a unit cell across the length of an LT furnace system with focus on gas composition and temperature. The research will continue for full, across the width models for consistency considerations.
Off-gas Constituents and Concentration
Off-gas is discharged from stabilized PAN fiber (SPF) during the process of carbonization within the LT furnace. Several papers highlight off-gas constituents as a function of operating temperature. The common chemical species in this step of the carbonization process are CH4, CO2, CO, NH3, H2, H2O and HCN.
The amount of each species strongly relies on parameters in stabilization process. Some of these parameters include oxygen amount, residence time, heating rate, and temperature.
Several differences exist within the industry for the oxidation process, based on the final properties of the target fiber. To develop a basis, the Stabilized PAN is assumed as based on the analysis of Stabilized PAN fiber from Griffing and Overcash.
In this simulation, the off-gas, which is also referred to as evolved gas and volatiles, are assigned as composing from 10 chemical species: 7 common components and N2, C2H4, and C2H6. The total chemical reaction for carbonization of stabilized PAN (C2.99H1.16NO0.29)n can be written as follow;
(C2.99H1.16NO0.29)n + Heat → IF + γHCNHCN + γH2O H2O + γH2 H2 + γNH3NH3 γCOCO + γCO2CO2 + γCH4CH4 + γN2N2 + γC2H4C2H4 γC2H6C2H6
where IF represents intermediate fiber for the LT furnace, and Υi represents the stoichiometric coefficient for ith chemical species.
However, the composition of intermediate fibers at the exit of the LT is not known. The intermediate fiber’s chemical composition is a complex function of LT furnace working conditions (residence time, temperature etc.) and stabilized precursor as well. The huge volume of the mass loss occurs within the LT furnace system.
To carry out off-gas compositional analysis a simplifying assumption was made that the mass loss within the HT furnace is much smaller than in the LT furnace. Assuming the entire mass loss occurs inside the LT furnace, the intermediate fiber is assumed to have an identical composition to the end product (containing 5 wt% nitrogen and 95 wt% carbon). The current study uses this assumption.
With the output fiber and input fiber defined the stoichiometric coefficients, Υi, for all species requires definition for off-gas composition estimates. 11 stoichiometric coefficients, product fiber and 10 off-gas species, and 5 equations are available: 4 atomic (C, H, O, N) balances and total mass balance; 6 more independent mathematical relationships are needed for mathematical unique solution of 11 stoichiometric coefficients.
As stated earlier, off-gas compositions are functions of operating conditions mainly fiber composition, residence time, and temperature of local fiber. It is essential to consider local fiber composition, residence time, and temperature effects, in addition to the six independent mathematical equations.
Generally, these relationships are defined as chemical reaction kinetics equations. The chemical kinetic relationships for carbonization of stabilized PAN are not readily available through a literature search on the subject. This complex subject was analyzed and the results were used to develop the foundation of the composition.
The literature of off-gas composition highlights considerable differences of potential composition. This is inevitable as the composition is a function of the exact composition of the PAN, temperature, stabilization process, time, and even tension to a certain extent.
Off-gas variations are certain to exist with all of these variables and different product varieties targeted. For this analysis, the discharged volume of off-gas constituents is taken from Griffing and Overcash and is presented in Table 1. These values are produced by using the conditions from Chung to drive their analytical model.
Table 1. Chemical composition of Stabilized PAN, product fiber and off-gas.
|
Species |
Mw [g/mol] |
100 g STB PAN basis [g/100 gPAN] |
mol basis [mol/PAN] |
input |
C(2.99)H(1.16)O(0.29)N |
55.71133 |
100 |
1 |
(solid) outlet |
CF (95wt% C 5%N) |
12.09689 |
56.766 |
2.614316 |
(gas) outlet |
H2 |
2.01588 |
0.013 |
0.003593 |
|
N2 |
28.0134 |
13.8 |
0.274446 |
|
CO |
28.0101 |
2.06 |
0.040973 |
|
CH4 |
16.0425 |
2.36 |
0.081957 |
|
CO2 |
44.0095 |
3.24 |
0.041015 |
|
NH3 |
17.0305 |
1.317 |
0.043083 |
|
H2O |
18.0153 |
5.29 |
0.16359 |
|
HCN |
27.0253 |
14.3 |
0.294788 |
|
C2H4 |
28.0532 |
0.412 |
0.008182 |
|
C2H6 |
30.069 |
0.442 |
0.008189 |
Physical Properties of Off-Gas
The physical properties of the off-gas include specific heat, viscosity, diffusivity, and thermal conductivity, which are crucial parameters in the system’s modeling.
Pure gaseous substances are split into real gas and ideal gas. In the case of ideal gas, several physical properties for pure substances are temperature function only. This gas is distinctive when it is not close to a saturated condition and/or is a low density gas. Therefore, gases at low pressure condition and high temperature meet these conditions.
Two unique criteria are applied to establish the ideal gas state using Reduced Pressure Pr = P / Pc and Reduced Temperature Tr = T / Tc as follows,
Pr « 1
Pr < 1 and Tr ≥ 2
Critical temperature and pressure data and its decreased temperature and pressure (@ 1 bar and 300°C) are assessed for all off-gas constituents.Based on these calculations, it is rational assumption that the off-gas is in ideal gas state within the LT furnace. The NASA gas property data was used for specific thermal conductivity, heat, and viscosity for this research.
Heat of Reaction
Heat of reaction, also known as standard enthalpy of reaction, is defined as enthalpy change occurring chemical reaction under normal condition based on a single mole of limiting reactant. It is measured using standard stoichiometric coefficients and enthalpy formation for all involved chemical species.
Conversely, it is indeed a challenging task to assess heat of reaction for carbonization since enthalpies of formation for stabilized PAN fiber (reactant for LT furnace) and the intermediate fiber (product from LT furnace) are not known. Intermediate fiber exiting from LT furnace could be considered as carbon fiber like previously by assuming mass loss is negligible within the HT furnace.
Further estimation is required to examine standard enthalpy of formation for intermediate fiber product, as it is also unknown. It is possible to calculate the enthalpy by considering that carbon fiber consists of only carbon atom despite 5 wt% of nitrogen. Based on these two assumptions, standard enthalpy of formation for intermediate fiber product from LT furnace is approximated as similar to that of solid carbon, graphite.
For stabilized PAN fiber, it is a lot more complicated and needs successive assessments from a well-defined state. The conventional enthalpy of formation for acrylonitrile is known for both liquid and gaseous states. Estimation of standard enthalpy of formation for stabilized PAN fiber should commence from acrylonitrile.
Liquid acrylonitrile undergoes polymerization forming solid PAN (polyacrylonitrile) and the heat effect of this polymerization reaction is reported by Roberts as -17.3 kcal/(mol of monomer) @ 76.8°C. In principle, it is not standard heat of formation as it was not measured at standard temperature, but here the assumption is made of negligible change in heat of polymerization.
The standard enthalpy of formation in the case of solid PAN fiber is 72.38 kJ/mol lower than liquid acrylonitrile because it is exothermic reaction. 140 kJ/mol is heat of formation for liquid acrylonitrile, so heat of formation for solid PAN fiber could be assessed as 67.62 kJ/mol (of monomer).
Precursor PAN is stabilized when traveling through oxidation ovens; this process has a number of reactions: Oxidation, Dehydrogenation and Cyclization. Reactions inside the oven are called exothermic reactions, highlighting the fact that thermal management inside the oven is very important. Evaluation of thermal effect on stabilization could be performed through a variety of approaches. The value reported by Dunham and Edie was considered in this study.
Dunham and Edie focused on established reactions taking place in parallel and series, and heat effects of individual reaction. From Dunham and Edie, PAN stabilization heat effect can be expressed as follows:
ΔHstbPAN = ΔHcyc + ΔHdehydro + εoxiΔHoxi
where ΔHstbPAN represents the standard heat of reaction for stabilization reaction, ΔHcyc, ΔHdehydro, ΔHoxi are heat of reactions for cyclization, dehydrogenation and oxidation, respectively, and εoxi is extent of oxidation reaction.
Based on the structure reported by Gupta, it is possible to achieve the extent of oxidation as 0.45 ~ 0.5. Taking 0.5 extent of oxidation total heat effect depending on Dunham and Edie’s technique can be achieved as –77.3 kJ/mol (of monomer).
The heat of formation of stabilized PAN is 77.3 kJ, which is found to be lower than that of PAN per mole of monomer. This process is explained in Figure 1. Standard heat of formations for products exiting from LT furnace are needed to evaluate the standard heat of reaction.
The off-gas products of LT furnace are well-defined, and all standard heat of formations for 10 gaseous chemical species is obtained from NASA database. In this study, intermediate fiber is assumed as 5 wt% nitrogen and 95 wt% carbon, but standard heat of formation is obtained for pure solid carbon (graphite).
.jpg)
Figure 1. Estimation of heat of carbonization reaction of stabilized PAN fiber.
Image Credit: Harper
Heat effect of exact chemical reaction differs from the standard heat of reaction discussed earlier. Standard enthalpy of reaction is generally measured based on standard state, although actual reaction does not take place at that temperature.
Sensible heat effects for both products and reactants should be considered for actual heat effect of the chemical reaction. Actual heat effect consists of three separate heat effects: sensible heat effect for product (and unreacted reactant), heat of reaction, and sensible heat effect for reactant. Heat capacities for products species to evaluate sensible heat effect for product are obtained from NASA database.
Specific heat for stabilized PAN fiber is the main complication. Zoltek’s whitepaper has a few thermal properties of their products. Heat capacity for Panex® 35 is given in Zolteck’s whitepaper. In fact, (Panex® 35) is more like carbon fiber and not like oxidized PAN. Zoltek’s whitepaper has specific heat @ two different temperatures and linearized specific heat is used to heat capacity for stabilized PAN.
These properties are limited in publications. The measured standard heat of reaction is 124 kJ/kg of StbPAN @ 25°C and heat effect changing stabilized PAN from 240°C into 500°C products would need 867.9 kJ/kg of StbPAN.
Conclusion
The CFD simulation results are revealed for the carbonization furnace for PAN-based carbon fiber manufacturing method. Temperature, velocity, and volatiles volume fraction are displayed as contours. CFD simulation aims at the gas phase within the carbonization furnace.
To support this research, several scientific efforts were considered to establish the physical properties of off-gas at carbonization process of stabilized PAN. Fiber is eliminated from the simulation for sake of simplicity, but several assumptions were derived due to the elimination of fiber, the off-gas discharge rate, and the local temperature of the fiber. This simplified off-gas discharge rate revealed a composition difference from the top to bottom of the system.
The off-gas volume fraction grew to a maximum at the vent as predicted. The off-gas discharge also impacted the gas temperature, as shown variations in temperatures in the tapered and uniform cases. In this simulation, the coupling from the off-gas to the flow and temperature is a one-way coupling without feedback.
The off-gas discharge rate is provided rather than assessed from the local mass fraction of fiber and temperature. This two-way coupling would be provided by chemical kinetic of carbonization.
This kind of CFD simulation even with basic condition would stimulate and promote development of kinetic expression and enhance design and performance of industrial furnace. Additional research is needed to look at difference along the furnace width which would impact the consistency of the system. A tow band width model would be needed to carry on with this difference along the width.
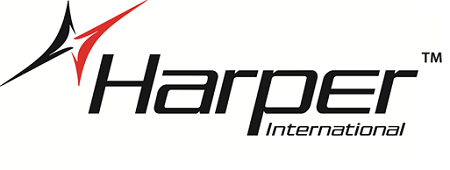
This information has been sourced, reviewed and adapted from materials provided by Harper International.
For more information on this source, please visit Harper International.