Interview conducted by Mychealla RiceAug 16 2016
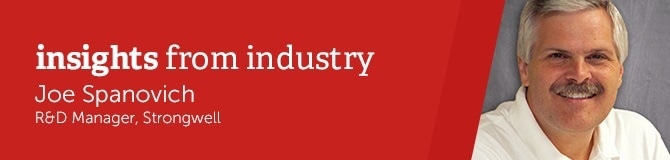
Joe Spanovich, Research and Development Manager at Strongwell talks to AZoM about the Corrosion Performance of Fiberglass
Please can you provide a brief background about Strongwell?
Strongwell is the world's largest pultrusion company and the recognized leader in the pultrusion industry. Strongwell has pultruded fiber reinforced polymer (FRP) composite structural products since 1956. The company has three U.S. plant facilities: Bristol, Virginia; Abingdon, Virginia; Chatfield, Minnesota. Each facility is ISO 9001:2008 quality certified and ISO 14001:2004 environmentally certified.
What qualities does Fiberglass hold that other materials may lack?
When EXTREN® or a custom Strongwell pultrusion is being considered as an alternate to “traditional” materials, the significant product features are:
- Corrosion resistance: FRP won’t corrode like steel and aluminium.
- Lightweight: EXTREN® weighs 75-80% less than steel and 30% less than aluminum.
- Extremely low thermal/electrical conductivity
- High Strength: the strength can also be customized in any direction by varying the makeup or directions of the reinforcements
- Dimensional Stability: wood is very unstable as its moisture content changes.
- Low Maintenance: generally, FRP does not need painting because it uses UV stabilizers and surfacing veils
- Custom Colors: the resin used in FRP is pigmented, which means the color will show through the entire part, even if it is scratched or scraped.
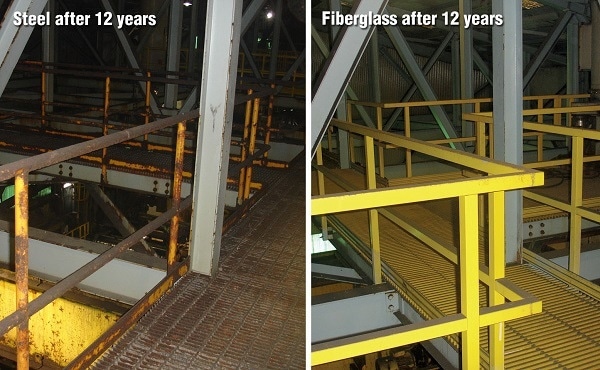
Why is resistance to corrosion important when selecting a material?
According to a 2002 federal study, initiated by the National Association of Corrosion Engineers International (NACE International), the total annual estimated direct cost of corrosion in the U.S. is $276 billion. This is approximately 3.1% of the nation’s 1998 Gross Domestic Product (GDP). The study further states that the current per capita direct cost of corrosion for U.S. residents, based on July 1, 2001 figures from the U.S. census, is approximately $970 per person per year! While this data is a bit old, it still bears out how important corrosion is to consider when choosing a material.
Corrosion is not the only consideration when making a material selection for an application, but it is a critical one. If the wrong material is selected, premature failure of the material can occur. This can also apply if the appropriate environmental factors are not considered, such as the chemical environment and temperature. The degree of corrosive attack from chemicals is temperature dependent; with elevated temperatures, corrosion activity is increased.
Strongwell assists customers with the correct selection of EXTREN® and custom materials based on the specific chemicals and concentrations involved in the application, temperature of the application, and other specific details of the application.
What makes Fiberglass naturally resistant to corrosion?
Although there are numerous different raw materials that make up an FRP composite, the corrosion resistance is essentially determined by the choice of resin and reinforcement used. There are numerous resins available which can provide long term resistance in many chemical and temperature environments. There is much less latitude in the choice of reinforcements but can make a difference in some chemical environments. In fact, some chemicals will attack the glass more aggressively than the resin. Strongwell incorporates a synthetic veil on the surface of all EXTREN® structural shapes providing a resin-rich layer to enhance corrosion protection.
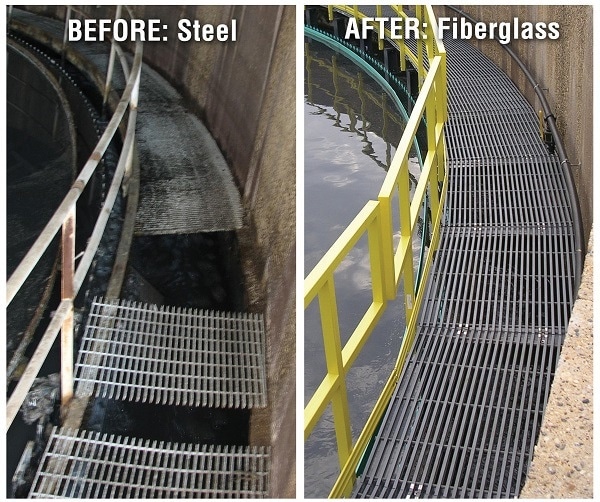
When purchasing Fiberglass, what benefits will a Company gain from the products’ resistance to corrosion?
FRP is resistant to a broad range of chemicals. FRP will not rust or corrode like metals or rot like wood. This inherent durability makes FRP the material of choice because it lasts longer than other traditional materials in a variety of settings. Properly designed FRP composites have a very long service life and minimum maintenance requirements compared to traditional materials.
It is true that purchasers of Strongwell pultrusions will often spend more up front (speaking strictly of material cost) than if purchasing traditional materials. However, this doesn’t consider the installation costs or life-cycle costs of composites compared with traditional options. Generally, if installation and life-cycle costs are calculated, FRP composites can actually be less expensive than traditional materials – sometimes dramatically less.
Compare the difference between Strongwell’s Fiberglass and any other Fiberglass in regards to corrosion?
Strongwell competes with numerous smaller companies that offer similar structural shapes. The industry has even adopted nomenclature of EXTREN® series numbers (500, 525, 625) similar to EXTREN® in order to get their product used when EXTREN® is specified. Purchasing on the following basis is recommended so that there won’t be any surprises in the long term:
QUALITY - Strongwell is widely recognized for consistently high quality parts. Strongwell manufacturing locations are ISO 9001:2008 quality certified. All incoming raw materials are certified to conform to specified properties. A series of physical property tests (First Article Testing) is performed on each production run of every item.
SERVICE - Strongwell has a commitment to provide superior, unmatched service. A technical sales team, along with supporting structural, R&D, and process engineers is available. Supporting this commitment are multiple plant locations with pultrusion operations covering approximately 650,000 square feet of manufacturing space, and a large EXTREN® inventory from which shipments can be made quickly.
SIZE AND AVAILABILITY - EXTREN® is available in nearly 150 standard shapes with many of these available from stock for immediate shipment. Strongwell offers the most comprehensive range of shapes and the largest sizes available in the industry. In addition, custom pultrusions are continuously being developed.
PRODUCT DEVELOPMENT - Strongwell is known to be the world’s leader in pultrusion technology and is constantly investigating and evaluating new raw materials and potential process improvements. The resulting product improvements are incorporated into EXTREN® and custom shapes well in advance of competitive products. A fully staffed lab and dedicated lab pultrusion machine keeps Strongwell in the forefront of technology.
EXTREN® DESIGN MANUAL - Strongwell offers the most comprehensive, up-to-date Design Manual for use with EXTREN® shapes. This Design Manual, recognized as the “Bible” for designing with EXTREN® fiberglass shapes, has been developed from theoretical computations made by Strongwell’s licensed engineers and from empirical data generated from extensive testing of the latest EXTREN® composites. That said, data from this Design Manual should be used only in conjunction with EXTREN® shapes.
Strongwell offers different Series of EXTREN® material which can be used based on the specific corrosion requirements of the application. EXTREN® Series 500/525 utilizes a high quality Isophthalic polyester resin which provides adequate corrosion resistance in many applications. As a general rule, EXTREN® Series 500/525 is resistant to most acidic chemicals.
EXTREN® Series 625 utilizes a premium grade vinyl ester resin which has higher strength properties, retains strength better at elevated temperatures and provides a wider range of corrosion resistance. As a general rule, EXTREN® Series 625 is resistant to acids and bases.
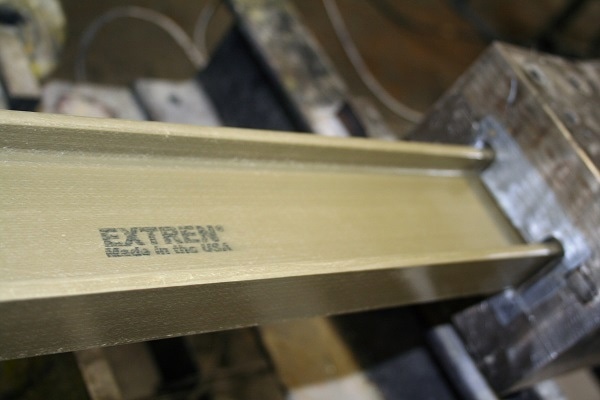
Where can our readers go to find out more about Fiberglass and its performance against corrosion?
Strongwell has an all-encompassing website that includes our Design Manual and a Corrosion Resistance Guide. The Corrosion Resistance Guide references numerous chemical environments and temperatures along with the recommended limitations of Strongwell’s product line. Strongwell has also partnered with our resin suppliers and can review any corrosion environment which is not covered in the Corrosion Resistance Guide.
About Joe Spanovich
Joe Spanovich has been with Strongwell since 1992 when he began his career as a pultrusion Process Engineer. He is now the R&D Manager over the Strongwell Lab.
Joe is a graduate of The Ohio State University and has over 30 years of composites experience.
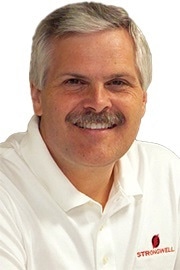
Disclaimer: The views expressed here are those of the interviewee and do not necessarily represent the views of AZoM.com Limited (T/A) AZoNetwork, the owner and operator of this website. This disclaimer forms part of the Terms and Conditions of use of this website.