There are millions of transformers present in existing electrical grids that interconnect power generation, distribution, and transmission. As these transformers are important assets, they have to be properly maintained to provide long and continuous electrical service.
This article outlines the standard structure of a large transformer and discusses the importance of monitoring dissolved gases. It also looks the characteristics of sensors that do this online, and describes the CoreSense online dissolved gas analyzer developed by ABB.
Transformer Insulation
Fundamentally, transformer insulation contains an oil impregnated cellulose paper that surrounds conductors and layers of multiple conductors, which form the transformer windings. Cellulose is also present in large quantities in wood, pressboards, and mechanical supports that are used during the manufacturing process (Figure 1).
.jpg)
Figure 1. Transformer solid insulation – windings, barriers and supports. Image Credit: ABB Ltd.
Insulating oil is used to thoroughly impregnate the entire structure. This oil is also used as a cooling agent to extract heat from the windings during the operation of the transformer.
There are two ways to extract heat – through oil circulation and forced air in the presence of pumps or fans, or through natural convection of the oil.
During the typical operation of power transformers, the insulating system undergoes natural aging due to load and temperature cycles. This aging results in some combustible and non-combustible gases that only become a major cause of concern during higher rates of gas formation compared to standard conditions.
Formation of Gases in Oil
Cellulose and mineral oil both have carbon-based, hydrogen-rich molecular structures, as shown in Figure 2. When cellulose and oil decompose a large number of byproducts are formed, including non-combustible and combustible gases. Most of those compounds contain naturally-occuring hydrogen.
.jpg)
Figure 2. Naphthenic aromatic molecule of insulating mineral oil (there are several other aromatic rings present in mineral oil, all rich in hydrogen). Image Credit: ABB Ltd.
Cellulose is extremely sensitive to moisture, oxygen, and heat. Temperature is proportional to the aging process - if the temperature is higher, the paper’s aging process will become faster (thermal aging).
When higher amounts of moisture and oxygen are present, the paper decomposes through oxidation and hydrolytic processes, generating more acids, moisture, and other constituents that speed up the aging process even further.
The molecular structure of the insulating fluid also degrades when higher temperatures and electrical faults are present, such as arcing of several degrees of intensity and partial discharges.
In addition to this, insulating oil and cellulose can break down in the presence of contaminants, for example due to maintenance activities, penetration of moisture through leaks, etc.
.jpg)
Figure 3. Molecular structure of cellulose. Image Credit: ABB Ltd.
One thing that is common in almost all types of insulation degradation is the formation of gases. These gases subsequently dissolve in the oil, enabling the detection and analysis of the defect through adequate monitoring of the evolution and amounts of these gases. This procedure is referred to as dissolved gas analysis (DGA).
Dissolved Gas Analysis (DGA)
DGA is one of the most powerful tools used for detecting faults in power transformers. DGA analytical methods and interpretation techniques are continuously being studied and enhanced.
Online monitors are especially useful for applications where the formation of gas in remote electrical devices needs to be monitored at regular intervals of time (for example where major faults have already been identified, or in expensive or strategic equipment) which is otherwise not viable with off-line laboratory analysis. IEEE C57.104 and IEC60599 have fully summarized the results of many years of experience of the power industry.
The fundamental gas, hydrogen forms in the presence of electrical and thermal problems, leading to the degradation of cellulose and oil and therefore plays a major role in the early detection of failure modes or unusual conditions within the transformer.
DGA Laboratory Issues
The key problems related to laboratory DGA analysis are:
- Contamination of sample during and/or after sampling on-site
- The time, cost, and resources involved to manually obtain samples, especially in remote locations
- Degradation of sample between the time of analysis and the time of sampling
- Laboratory reproducibility
- Laboratory accuracy and precision (or repeatability)
It is well known in the industry that many laboratories provide reasonably accurate DGA results to their customers but that many others provide quite inaccurate results. Even the best laboratories produce results with some inaccuracy, which, therefore, needs to be known to determine the reliability and accuracy of the diagnoses. It is strongly recommended that each laboratory evaluate and provide its own accuracy figures. When this is not possible, default accuracy values based on international surveys can be used.
M. Duval, 2005
In collaboration with 25 leading laboratories from 15 countries, Cigre SCD1 TF15.01.07 performed a survey using gas-in-oil standards. The survey revealed an average repeatability of ±27% at low gas concentrations (1 – 10 ppm) and ±7% at medium gas concentrations (10 – 100 ppm).
The average accuracy found was ±15% and ±30% at medium gas concentrations and low gas concentrations, respectively.
.jpg)
Figure 4. Illustration of the interplay between precision and accuracy. Image Credit: ABB Ltd.
Repeatability or precision is associated with observed variations when several samples of the same oil are investigated by the same lab over a short period of time - usually less than a single day.
Accuracy is related to variations found between the nominal value contained in the gas-in-oil sample prepared in accordance with standard procedures and the values determined by a given laboratory.
In addition to the lab-scale limitations of accuracy and repeatability, the sample of insulating oil will degrade eventually due to the high mobility of hydrogen gas in particular and the mobility of the dissolved gases in general. These gases gradually escape into the atmosphere, even from a sealed container.
Online Gas Monitors
Online gas monitors provide regular readings (usually several readings for each day) of the concentrations of gas dissolved in the transformer oil without the need for a manual sample. These monitors are either fitted on a transformer in service or at the factory.
Compared to laboratory analysis, online monitors can detect the abnormal formation of gases or any fault that occurs in near real time between manual oil samplings. Manual samplings are often carried out every six months or every year for regular maintenance with laboratory analysis.
With online gas monitors, gas analysis is carried out more often, providing a powerful early detection system that prevents extreme manual samplings and site visits, along with the benefit of conducting an almost constant monitoring of levels and trends of gases.
When commissioning, installing, and operating gas monitoring systems, several issues have to be addressed so that fault conditions (false negatives) are not overlooked, and false alarms that occur in the absence of a fault (false positives) are avoided.
- In order to reduce the possibility of oil leaks, the monitoring system oil sampling mechanism should be developed in a fail-safe manner. Even a small percentage of leaks can reduce the oil level of the main transformer tank over time. If the oil falls below a certain critical threshold, a safety shut down of the transformer will be automatically started, or if there is no safety system the transformer will fail completely.
- The monitor-sampled oil should be representative. If the installed monitor is continuously sampling the same pocket of stagnant oil, then it is highly possible that developing fault conditions will not be noticed and will give a false sense of security.
- The monitor’s gas-sensing elements should have long-term stability under real world transformer conditions. The same conditions that promote the aging of the transformer can deteriorate or age the sensors and electronics integrated into the monitoring system. There are certain conditions that need to be considered:
- Presence of oxygen and moisture dissolved in the transformer oil
- Temperature cycling
- Presence of reactive chemicals in the transformer oil produced by the breakdown and aging of the cellulose insulation and the oil itself; for example organic acids, alcohols, furans, carbon monoxide, etc.
- The monitoring system should not consume the gas to quantify it, as this can deplete the oil sample that is being read by the sensor, and result in false trends in the gas levels.
- The monitoring system should have long-term reliability and must be able to self-diagnose itself. This will prevent a dead sensor from being interpreted as “condition normal, no gas detected”.
- Cross interference should not be displayed by the gas-sensing elements; for example reacting to other gases that could exist and give an inaccurate reading.
The industry uses three types of online gas monitors - gas combination, one gas, and multi-gas monitors, with each monitor having its own advantages and disadvantages.
One Gas Monitors
One gas monitors are extensively deployed due to their high reliability and low cost. Most of these monitors can determine the hydrogen gas in oil, as this gas plays a major role in detecting the transformers’ abnormal operation. Whenever a fault occurs, hydrogen is almost always present and it is also the first gas to form, because C-H bonds are much easier to break compared to C-O or C-C bonds that exist in the cellulose and insulating oil.
One gas monitors are simple monitoring systems that can even be installed in remote locations where access to maintenance is slow, complicated, and expensive. This creates some major considerations when selecting one gas monitoring systems:
- Long-term reliability is important to keep maintenance requirements to a minimum, which means avoiding the use of monitoring systems that use complex oil handling or moving parts, such as valves, membranes, cooling fans, mechanical circulation, etc.
- The monitoring system should not use any consumables that require regular replacement
- The monitoring system should not need regular calibrations to stay within the preferred specifications
Gas Combination Monitors
Another type of online gas monitor, which is often deployed to transformers for early fault warning purposes is gas combination sensors or Total Combustible (oxidizable) gas sensors. These instruments use sensors that provide a single readout in response to a mixture of all the oxidizable gases. Their typical response may appear like this:
Readout = A x H2 + B x CO + C x CH4 + D x C2H2 + E x C2H4 + F x C2H6
The readout relies on the concentrations of all the gases that have varying relative sensitivities for individual gases. The idea is, irrespective of the type of gas being formed, the readout will provide a warning of the formation of gas. A drawback of this sensor is that it is difficult to interpret the readout, because in a standard transformer some background gas will always be present in its oil.
.jpg)
Figure 5. Approximate gas formation temperature in °C. Image Credit: ABB Ltd.
An issue is that a high hydrogen condition cannot be distinguished from a high carbon monoxide condition, for instance. Under standard conditions, carbon monoxide may contribute to a high reading of a gas combination monitor (Table 1).
Table 1. Ranges of 90% typical gas concentration values observed in power transformers in µl/l (Source IEC60599:2007)
|
C2H2 |
H2 |
CH4 |
C2H4 |
C2H6 |
CO |
CO2 |
All transformers |
|
50-
-150 |
30-
-130 |
60-
-280 |
20-
-90 |
400-
-600 |
3,800-
-14,000 |
No OLTC |
2-
-20 |
|
|
|
|
|
|
Communicating OLTC |
60-
-280 |
|
|
|
|
|
|
This could conceal the initial rise in hydrogen, which would otherwise indicate a fault development, leading to reduced sensitivity which reduces the overall confidence and usefulness in the monitoring system (Figure 6). This reduced sensitivity is not experienced by the one-gas hydrogen specific sensor.
.jpg)
.jpg)
Figure 6. Example of masking effect on hydrogen trend by carbon monoxide in gas combination monitors. Image Credit: ABB Ltd.
An oxidizing fuel cell is used by gas combination sensors as a type of sensor mechanism. This sensor works by consuming oxidizable gases to generate electricity.
If the speed of depletion by the sensor exceeds than that of the speed of local replenishment, the gases will deplete and lead to inaccurate readouts.
Multi-Gas Monitors
Separate readouts for up to 9 gases are simultaneously provided by multi-gas sensors. These sensors provide complete data about the dissolved gases in a similar form to what is acquired from a laboratory DGA analysis, but in real time.This considerably increases the viability of the monitoring system.
Empowered by this capability, asset owners can perform real-time diagnostics on major transformers semi-continuously. The high cost and complexity of commercially available multi-gas sensors somehow mitigate this advantage. The outcome is that this kind of monitor is usually deployed for assets that develop faults, or for the most critical of assets.
At present, simple and cost-effective one-gas monitors are used by most utilities to provide a warning and then do a laboratory DGA analysis to obtain an additional diagnostic. It has been predicted that adoption rates will increase with the advancement of multi-gas sensor technology.
The ABB CoreSense Hydrogen and Moisture Sensor
The new gas monitoring system, ABB CoreSense hydrogen and moisture sensor provides a solution to the challenges of developing an ideal online gas in oil analyzer. Two solid-state sensors are used by the CoreSense to directly determine moisture and hydrogen levels in the transformer insulating oil, without any need for complicated sample handling to isolate the dissolved gas from the oil or to condition the oil.
The sensor uses an innovative thermal pump to address the question of representative sampling and stagnant oil. This thermal pump ensures that the sensors and fresh oil always remain in contact through forced convection. This is a simple and reliable method, as it has no moving parts or a membrane (Figures 7 and 8).
.jpg)
Figure 7. Computer simulation showing stagnant oil when no thermal pump is used. Image Credit: ABB Ltd.
.jpg)
Figure 8. Computer simulation of the CoreSense thermal pump showing oil inflow at bottom and outflow at top. Image Credit: ABB Ltd.
The ABB CoreSense can be safely positioned on all types of valves, as this does not obstruct the transformer or the valve. The CoreSense eliminates the need for special protective actions before oil treatment activities and customers can easily install it. This provides an added advantage when compared to membrane-based systems that can be affected by variations in pressure.
As described before, the CoreSense uses the solid-state hydrogen sensor that has been rigorously tested and defined to provide stability and reliability over long term.
The CoreSense uses a patented protective coating to prevent the effects of aging and degradation from acids, reactive gases, and other components that may exist in the transformer oil, and a reversible hydrogen specific phase change in a palladium metal alloy to identify hydrogen levels. It is stabilized by temperature to prevent thermal effects on hydrogen readings.
Hydrogen is not consumed by this sensor, eliminating the possibility that the hydrogen reading could be inaccurate as a result of local depletion.
An embedded computer in the CoreSense constantly monitors all of its functions. Three super bright LEDs in the CoreSense enable the sensor to provide status at a glance capability, report about the sensor condition, and moisture and hydrogen levels in the transformer oil.
An integrated web server in the CoreSense publishes a basic man machine interface to allow both remote and local network access to the moisture and gas levels, in addition to the present conditions of the monitoring system.
The intuitive interface is efficient and can be read easily. Users can access the web pages via any internet browser and do not have to install any specific software.
.jpg)
Figure 9. Screenshot of the web HMI. Image Credit: ABB Ltd.
Designed for long-life and durability, the CoreSense has no moving parts, uses solid state microelectronic gas in oil sensors that operate directly in situ in the transformer oil, and features a strong all metal IP67 rated submersible waterproof enclosure.
This concept was applied to all design aspects, including the integration of a super-capacitor to maintain time during unanticipated power interruption rather than a battery that has a limited lifetime and would need to be replaced frequently.
.jpg)
.jpg)
Figure 10. The ABB CoreSense with solid metal enclosure. Image Credit: ABB Ltd.
Conclusion
The ABB CoreSense hydrogen and moisture sensor can accurately determine the presence of hydrogen gas in oil down to a detection limit of 25 ppm, with a fast T90 time within a minute and an error of ±10 ppm.
The sensor can offer accurate readings for 10 to 15 years without any calibration, regular maintenance, and consumables. These features make the ABB CoreSense suitable for extensive deployments in remote locations or flood areas with potential access difficulties and weather extremes.
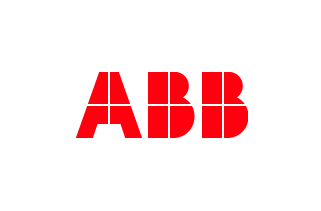
This information has been sourced, reviewed and adapted from materials provided by ABB Measurement & Analytics - Analytical Measurement Products
For more information on this source, please visit ABB Measurement & Analytics - Analytical Measurement Products.