The petrochemical industry powers the modern world. Petrochemicals not only contribute to the transportation industry, but also a vast majority of basic human needs, including food, housing, hygiene, and health. The conversion of crude oil into valuable products involves complex, multistage chemistry, and processing.
Engineers need to rapidly and accurately measure the chemical contents present in process streams so that productivity can be maintained and legal requirements can be met.
SilcoTek® offers advanced coatings that provide protection to production, analyzer, and sampling components from the negative yet unavoidable consequences of processing highly reactive chemicals like mercury and sulfur without compromising the prerequisites of environmental regulatory standards.
This article covers the materials challenges faced by the people involved in the petrochemical industry and the solutions provided by SilcoTek coatings.
When the desired surface properties cannot be achieved with the materials used for the engineering and construction of petrochemical processing and analyzer systems, SilcoTek® coatings provide the ideal solution for optimizing cost and performance.
These versatile coatings offer robust chemical resistance, corrosion resistance, and stability to a range of substrates and applications. They are effective as complex geometries and tortuous pathways can be completely coated with a thin, flexible, and durable coating, and save money by improving the service life and performance of equipment while ensuring compliance to regulatory standards.
Materials Challenges in the Petrochemical Industry
The following are the material challenges in the petrochemical industry:
- Frequent maintenance: Untreated stainless steel tends to corrode when exposed to oil and gas processing streams, yet exotic materials like Hastelloy® are expensive and largely affect profitability
- Lost time and performance: It is necessary to measure regulated chemical compounds like H2S at ultra-sensitive levels, but instruments made up of untreated stainless steel fail to deliver adequate results
- Poor reliability: Commonly preferred solutions, such as PTFE, cannot withstand high temperatures, do not have durability, and can easily delaminate in challenging environments that are prevalent in petrochemical processing
Applications where SilcoTek Coatings Boost Performance
SilcoTek coatings improve performance in the following applications:
- General process monitoring
- Odorant sampling
- Olefin and aromatic production
- Ammonia slip monitoring
- Downhole crude sampling and testing
- Fence line monitoring (EPA 325)
- Off shore / splash zone
- Flare gas sampling (40 CFR Part 60 Subpart -Ja)
- ULSD / ULSG (Tier 3)
- Ethylene and propylene purity
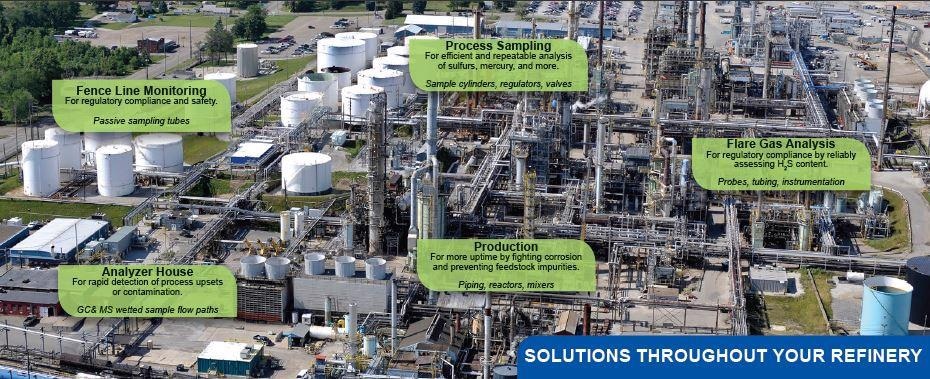
Common Parts that Benefit from SilcoTek Coatings
Common components that benefit from SilcoTek coatings include GC & MS components, fittings, filters, valves, pressure regulators, injectors, sample cylinders, downhole/wireline tools, reactors, tubing, probes, and custom parts.
The following table lists the problems and the results that can be achieved with SilcoTek Coatings:
Problem |
Solution |
Result |
Poor analytical accuracy with H2S, Hg, NOx, etc. |
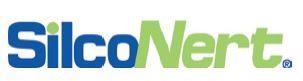 |
Improved sampling reliability and output |
Corrosion |
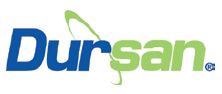 |
Longer lifetimes and lower costs |
Slow instrument response |
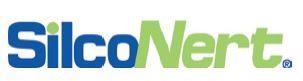 |
Drastically faster signals and higher efficiency |
Regulations e.g. Tier 3, EPA 325 |
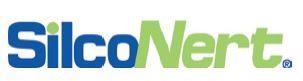 |
Assured compliance with accurate results |
Oxidation |
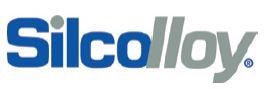 |
Sustained appearance and performance in extreme conditions |
Moisture |
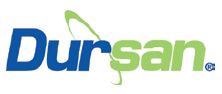 |
Reduced contamination, corrosion, and sample loss |
Advanced Surfaces for Advanced Performance
SilcoTek’s patented chemical vapor deposition (CVD) coatings are advantageous in many ways over alternatives, providing petrochemical customers with superior performance in addition to offering flexibility in system design, production, and installation.
Innovative Deposition Process Makes Integration Easy
The CVD process binds the coating to the base metal’s molecular structure, creating a flexible layer that is bendable with tubing without flaking as opposed to PTFE. In addition, complex geometries and narrow internal passageways can be completely coated, thanks to the gas-phase process.
Maximum Chemical Inertness for Reliable Analysis
Trace levels of ammonia, mercury, and sulfur need to be analyzed for quality control and to satisfy regulatory requirements in the refinery. Uncoated instrumentation does not calibrate quickly and fails to provide the resolution and accuracy of inert-coated systems.
Super Alloy Corrosion Resistance at a Fraction of the Price
SilcoTek-coated stainless steel provides a cost-effective alternative solution for expensive materials like Hastelloy®. In addition to providing a dense barrier to attack, SilcoTek coatings also prevent nickel, iron, and other metal ions leaching out of equipment into the process stream.
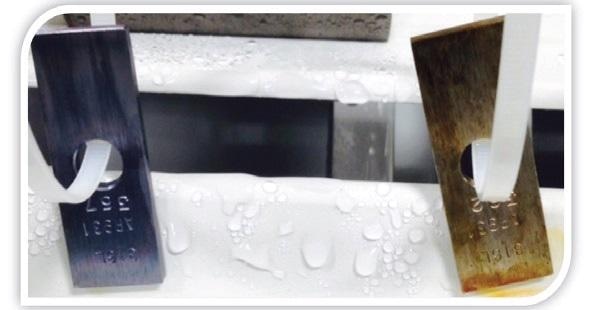
SilcoTek coatings drastically outperform uncoated 316L SS in ASTM G85-A2 acidified salt spray testing. Upgrading stainless steel with Dursan® or Silcolloy® is an eff ective alternative to costly super alloys.
Conclusion
SilcoTek coatings were created in the laboratory but grew up in the refinery. They provide solutions to perform better sulfur analysis in order to meet the regulations or to extend the service life of components in corrosive environments without the need for system redesign and without affecting the supply chain.
By providing a unique service experience, SilcoTek gives priority to customers and the quality of their parts and is committed to offering fast, superior quality, and mistake-free coatings daily. The company’s ZIP Code – Zero Disappointments, Integrity in all we do, and Plus 1 customer service – embodies these values and drives its mission.
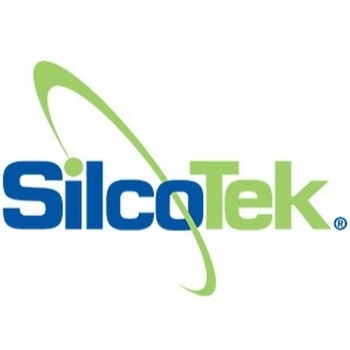
This information has been sourced, reviewed and adapted from materials provided by SilcoTek.
For more information on this source, please visit SilcoTek.