This article reviews hydrogen supply basics for the semiconductor sector, and introduces an on-site method of hydrogen carrier gas supply for producing semiconductor devices that are being used at more than 50 semiconductor facilities across the globe. On-site hydrogen can provide:
- Adequate pressure for all reactor inlet purification techniques
- Ultra-pure gas for best process results
- True zero-inventory design – hydrogen is generated as it is employed by the process
- Much lower pressure compared to stored hydrogen techniques, removing self-ignition hazard
- The ability to save money by reducing inlet gas purification cost
- Eliminates risk of introducing oxygen into piping during storage system change-out
Hydrogen in Semiconductor Production
Semiconductor processes, including epitaxy, employ active gases and a carrier gas stream containing high purity hydrogen to produce semiconductor devices. The carrier gas stream contains hydrogen that scavenges and reduces residual oxygen, protecting the devices from oxygen damage.
Growing compound semiconductor and solar cell markets are not only driving higher operating rates at current photonic manufacturing facilities but are also creating opportunities for new and expanded facilities.
These facilities have to compete with the complex safety issues posed by the carrier and active gases required. Due to their highly hazardous characteristics, process gases for epitaxy pose unique challenges. Many of these gases are toxic, while some are pyrophoric.
These substances are subject to strict usage and storage limitations. The combined storage of flammable hydrogen and the poison process gases in a facility makes for delayed permits and is also a matter of great concern.
Facility operators, whether a startup, an academic facility, or an established photonics manufacturer, are looking for ways to reduce the hazards, but ultimately every hazard reduction means a faster and less-expensive route to an operating permit.
Scrubbers, gas bunkers, and gas cabinets are the typical solutions, and are an expensive but effective way to reduce the hazards of a release. Not much can be done about the requirement of aggressive process gases in epitaxy; the process gases are critical components in the technology.
However, one thing that can be prevented is the need for storing large quantities of flammable hydrogen carrier gas. By reducing the inventory of the stored hydrogen gas, it is possible to reduce the flammability hazard as well as the degree of the overall hazard.
The customary method of supplying hydrogen for epitaxy is with the use of stored hydrogen, typically cylinder or tube trailers, occasionally liquid hydrogen. All stored hydrogen techniques use hydrogen that has been produced elsewhere and delivered to the customer’s location.
As per the delivered hydrogen supply method, enough hydrogen has to be stored onsite to meet the process requirements for two to four weeks between deliveries. The stored hydrogen, spanning from 3,000 to 1,000,000 standard cubic feet and kept in compressed to 2400 psig, creates a major hazard in and of itself.
Why Hydrogen is Preferred over Alternative Gases in Semiconductor Processing
Many semiconductor processes use hydrogen, from a carrier gas for transport of active doping gases to a cover gas for furnace processing. Several unique hydrogen properties are used by semiconductor applications:
- Very high heat transfer capability
- Reducing gas – oxygen removal
- Modest cost
- Low density for low pressure drop
Hydrogen’s capabilities are important for wafer annealing, sintering, semiconductor fabrication, semiconductor packaging, and many other semiconductor operations. Compared to nitrogen, argon, helium or another inert gas, hydrogen offers a better combination of oxygen removal properties, extremely low density, superior heat transfer properties, and relatively low price when compared to a rare gas or helium.
Issues with Stored Hydrogen
Like all other flammable gases, hydrogen is governed by a range of acceptable practices and regulations. In the United States, most guidance for hydrogen safety is based on the National Fire Protection Association that publishes guidelines for industrial practice at locations that use hydrogen.
NFPA Standard 55, Standard for the Storage, Use, and Handling of Compressed Gases and Cryogenic Fluids in Portable and Stationary Containers, Cylinders, and Tanks is the primary NFPA reference for hydrogen storage.
This article outlines the requirements for siting and operation of stored hydrogen systems, whether liquid hydrogen, cylinders, or gas storage tubes. Insurance providers and governmental permit authorities will often base their decisions and guidance on NFPA guidelines.
Changes to, or operations within, a facility could be subject to regulation of a local authority having jurisdiction (AHJ), typically a local governmental agency. Operation at top government facilities or academic institutions may be further regulated by an internal AHJ, like a fire marshal’s office at a state university. Periodic safety inspections are normally conducted by the AHJ to ensure that the operation conforms to the local codes and the permits granted.
For many new or increasing semiconductor hydrogen users, it is hard to acquire and comply with guidance regarding the use and storage of gas. Hydrogen together with other pyrophorics flammables and poisons, in the form of the doping gases, are used by semiconductor manufacturing facilities.
Additional hazards further complicate understanding and practicing safe operational procedures. The local AHJ will not design compliance practices for facilities. They will advise if what has been developed is acceptable or not, but the design of the compliance procedure is the facilities problem.
One challenge of hydrogen storage, particularly for new, growing or academic facilities, is that there are several, and occasionally contradictory, sets of rules that apply. Ultimately, the local AHJ is “the Decider”. You cannot operate, until your operation complies with the opinion of the local AHJ.
By eliminating large amounts of hydrogen storage, on-site hydrogen generation can minimize the risk and cost of complying with applicable rules and reduce confusion.
Hydrogen Purity Levels
Some semiconductor processing operations require high gas purity; others less so. The exact purity and impurity requirements of each operation must be understood to prevent underbuying purity (at a risk of manufacturing bad product), or overbuying purity (at a penalty of paying in excess for raw materials and impacting profitability).
Both assay (% purity) should be specified and contaminates of concern should be identified. In the US industry hydrogen purity levels for commerce are defined by the Compressed Gas Association; in Japan by the Japan Industrial and Medical Gases Association; and in Europe by ISO and the European Industrial Gas Association.
US standards define 7 industry-standard specifications for hydrogen quality - 3 purity levels for liquefied hydrogen, and 4 standard quality levels for gaseous hydrogen. Liquefied hydrogen tends to be much purer hydrogen than gaseous hydrogen due to the particular production process. This is because hydrogen impurities present in gaseous hydrogen are condensed out and eliminated during the liquid hydrogen liquefaction process.
Gas suppliers have their own marketing nomenclature for gas purity grades, such as UHP, ULSI, Semi-grade, and Prepurified, contrary to the CGA-defined standard industry production grades. With each supplier having their own terminology, the marketing grades cannot be directly compared with each another.
A grade of gas must be selected from your supplier that satisfies users’ requirements for assay as well for specific contaminates. For instance, fuel cell applications are immune to nitrogen content, but the smallest amount of CO could be damaging.
In contrast, near-zero nitrogen content is required in some compound semiconductor applications. It must be understood that the species and type of contaminates may be as, or more important than the % assay. A complete understanding requires a statement of % assay requirement and also the type of impurities that are not allowed to be present.
Due to existing supply system logistics, most hydrogen supplied to US customers is distributed as liquid hydrogen from the hydrogen source to industrial gas depots and then vaporized as a high-pressure gas into cylinders and tube trailers for local deliveries. So, most hydrogen users usually receive gaseous hydrogen of nearly liquid quality.
Essentially, most users often get highly pure hydrogen, regardless of what grade they ordered. This naturally suggests why pay extra for the good stuff if one can get the good stuff without the premium cost?
However, liquid hydrogen purity for gaseous hydrogen users can become an issue if supply sources shift or if logistics change, and gaseous hydrogen generated from a gaseous hydrogen source is delivered to the customer. While the product will meet the purchase specification, it may upset the production procedure. The customers got what they paid for.
Hydrogen is largely employed for industrial applications, but semiconductors impose the most rigorous purity requirements of all the major hydrogen applications. Users of semiconductor hydrogen should think about their purity requirements, and purchase the hydrogen grade that fulfills their requirements. If a lower grade of hydrogen is purchased, users may find that one day the “right” grade of gas is supplied, and their process is impacted.
The Cost of Purity
Most semiconductor processes are developed by scientists working in a laboratory. During process development, technologists use gases that serve their laboratories, usually high purity gases that are delivered to meet the laboratory’s highest purity requirements.
Once the process is developed, it is worth critically analyzing the actual process requirements, considering process yield as well as gas cost considerations, to specify the most economical gas that meets the needs of the process. However, supplying purity in excess of the process requirements does not serve any purpose.
In the US, hydrogen gas supplied for commercial sale ranges from industrial grade (99.95% assay, -65C dewpoint, no other contaminant identifications) to ULSI or semi grade product of 99.99999+% purity, with strict definition and limitation on all contaminants present. The grade that meets both the process requirements and fits the budget should be selected.
Although prices will differ largely based on monthly use rate and geographic location, a useful rule of thumb is that the prices double for each extra “nine” of purity procured. So if 99.95% purity costs ~$12/100 scf, then 99.99% costs $25/100 scf, 99.999% costs $50/100 scf, 99.9999% costs $100/100 scf, and 99.99999% costs ~$200/100 scf.
After commercializing a hydrogen-using process, users should take an aggressive stance toward the definition of hydrogen quality so that they do not pay more than necessary given the process needs.
Hydrogen Purity Certification
When a customer purchases higher purity hydrogen, the difference may not be entirely clear
- How is the gas analysis determined?
- Does it mean that the hydrogen is especially “cleaned” somehow to accommodate the process?
- What does a certificate of analysis mean when applied to hydrogen cylinders?
- What assurance does a certificate of analysis provide?
During the filling process at the hydrogen source terminal, tube trailers or cylinders are filed with bulk, high purity hydrogen (usually vaporized liquid hydrogen).
While high purity hydrogen is used to fill most cylinders, it is not electronics grade. Typically, electronics-grade cylinders are filled in specialized facilities using electropolished liquid hydrogen tanks and gas cylinders, and high purity pumps, gas and liquid lines and fittings, and subjected to further filling scrutiny.
Only a few of these specialized facilities are available in the US and electronics grade hydrogen cylinders are shipped long distances for delivery. Therefore, electronics grade hydrogen cylinders usually cost $300 or more for each cylinder.
Several types of quality verification are possible for cylinder hydrogen, and customers should know what they are purchasing. Currently, many hydrogen suppliers fill hydrogen cylinders in a palletized manner, and they assume that all of the cylinders are being filled with the same hydrogen.
If cylinders have been prepped or cleaned and all of the fill lines and fittings are kept clean and tight, then the hydrogen filled in each cylinder should be identical to all of the others. The incoming gas used to fill the cylinders may be sampled and analyzed by hydrogen suppliers, who will then use that analysis as a measure of the quality of the gas delivered.
Alternatively, and more expensively, one of the cylinders from each group may be analyzed by the supplier, who will use that analysis as a typical of the batch.
A cylinder analysis that indicates the contents of each cylinder supplied is the most expensive option. As each analysis may cost the supplier upwards of several hours to perform the electronics standards (the lower the detection level, the longer the analysis run), the cost of each cylinder may also increase based on the type of analytical assurance required by the customer.
While the number of containers to be cleaned, filled and checked for quality can be reduced by tube trailer delivery, it also introduces compromises. Generally, tube trailers and tube banks are not available with electropolished internals, which means contamination may be present in the porous mill finish internal of the tube assembly.
To prevent the possibility of moisture or air ingress, careful execution will be required while supplying the gas from the delivery vehicle into the customer storage tubes.
On-site hydrogen removes the requirement for hydrogen compression/liquefaction, storage, and delivery compared to delivered hydrogen. It also prevents the need to fix and evacuate hydrogen gas lines, providing confidence that consistent hydrogen will be supplied to the process through an on-site hydrogen supply generator, at the same purity of hydrogen made in the generator.
Buy it Purer or Clean it Up?
Very high purity hydrogen may be specified by the highest purity semiconductor applications. Purifiers can also be included in the facility hydrogen systems as guard beds, so that the product is not contaminated with impure hydrogen.
For facility operators, these purifiers serve as guard beds and not as purifiers, because a purifier is meant to remove impurities from the gas, whereas a guard bed is used as a last option by insurance policy to prevent bad gas from reaching the process. Once the proper quality gas is delivered to the process, a guard bed is used to prevent the “one-in-a-million” situation from damaging the system.
If the levels or types of impurities are unknown in the incoming hydrogen, the industry’s attitude towards gas guard beds is justified. For delivered hydrogen, users must believe that that is the case, for there are various areas in the packaging, transfer of custody, shipping, and house piping procedures where contamination can occur in hydrogen. However, users assume the worst and use guard beds to protect the product and process from contaminated hydrogen.
But what if semiconductor users are convinced about the incoming hydrogen quality and its precise composition, and if users do not have to worry about packaging, piping, or shipping related contamination problems? In such a case, the user may want to use a purifier as a cleanup method - a polisher used to polish the delivered hydrogen to the required hydrogen purity, just like a water purification system used for purifying water of known composition to a higher purity specification by eliminating known contamination.
In both cases, the incoming stream should be relatively homogeneous and consistent so that configuration can be done to the purification system for the specific duty required.
Chemical Cartridge Gas Purification Systems Versus Palladium Purification
There are two major gas purification methods for semiconductor use - palladium alloy purifiers and chemical contaminate removal cartridges. These approaches work in a different way.
Palladium alloy purifiers are excellent hydrogen filters. When heated to 300 to 400°C, the crystal lattice structure of the palladium metal expands, but just enough to enable hydrogen molecules to travel through the structure, while keeping all of the bigger molecules behind.
Palladium alloy purifiers are capable of removing all hydrogen contaminants, whether known or unknown composition, and almost irrespective of the level of contamination (certain contaminants, if present, can be removed upstream of the palladium alloy purifier to prevent overheating).
In terms of process insurance and versatility, palladium alloy purifiers may be preferred but they are expensive to buy, install, and operate. In addition, they are subject to damage from process upsets and also introduce a 50+ psig pressure drop in the hydrogen gas supply line they serve.
Chemical cartridges operate by reacting with, and immobilizing, certain contaminants in the gas stream. Either physical or chemical reactions may occur. To remove each contaminant in the gas stream, a suitable chemical “antagonist” in the chemical cartridge is required.
In order to use a chemical cartridge approach, users should know what is going to be in the gas. If a chemical cartridge contains an impurity that it was not designed for, it will allow that impurity to pass through without removal, or the contaminant itself may deprive the cartridge of the required capacity to remove another impurity.
Generally, chemical cartridges introduce a small pressure drop in the hydrogen system and are initially low prices, but costs can increase quickly if poorly-selected cartridges are exhausted after cleaning impure gas streams.
If a gas system is supplied with hydrogen of known composition, and users know the exact hydrogen purity needed for their processes, then the most cost-effective approach would be to supply an engineered system of chemical hydrogen cleanup modules to bring the contaminates below the concern level. This system design offers a robust, low cost system, of predictable life, delivering hydrogen of preferred purity.
Stored Hydrogen Systems Versus On-Site Production
Normally, small hydrogen users and startups use the hydrogen supplied in cylinders, as that is the preferred method they use when developing their individual processes. Cylinder hydrogen can be used up to a use rate of 30,000 scf each month. From the perspective of high purity users, cylinders come with both pros and cons:
- Cylinders can be specifically processed for the grade of gas they are to contain – for example, electronics grade gas cylinders are emptied, subjected to vacuum, and baked out prior to being refilled with gas. This way, no gas from a customer will impact subsequent customers to get the cylinder. Often, lower grades are filled on top of prior gas.
- The cylinders themselves can be developed to improve the purity of the gas held within - for the highest purity gas grades, electropolished cylinders are employed.
- Cylinders offer an almost variable cost approach to hydrogen supply. While cylinders serve as a low cost storage mechanism, they provide relatively high cost hydrogen.
Despite the specific technology used to make the hydrogen, Onsite hydrogen production removes many possibilities of contaminating clean hydrogen accidentally. Onsite hydrogen overcomes the common sources of contamination by removing the filling, containerization and delivery steps.
At the user location, onsite hydrogen is directly sent from the production equipment, via purification/guard bed systems or analytical equipment as appropriate, to the process used. Onsite hydrogen eliminates a key risk point for contamination by removing the need to make and break connections.
Why Choose Onsite?
Onsite hydrogen production is practical as it can be achieved cost-effectively, and if the resulting raw material quality is appropriate for the use. Onsite is increasingly preferred due to rising transportation costs, limitations on storage volumes, gas pricing volatility, and the need of many producers to become independent of external influences on their business.
One key benefit of supplying hydrogen to semiconductor processing is PEM electrolysis on-site supply, thanks to its pressure capability and high purity. On-site supply removes human factors that can lead to air ingress and leaky connections, removes the need to store large quantities of flammable hydrogen, creates the highest purity hydrogen available, and prevents the need to order, manhandle, manage, move and connect or disconnect flammable hydrogen cylinders.
Conclusion
- Understand process requirements, and procure hydrogen based on the process-critical assay and contaminates
- Consider onsite hydrogen if the purity and cost meet process requirements
- Reduce hydrogen inventory to minimize process hazards
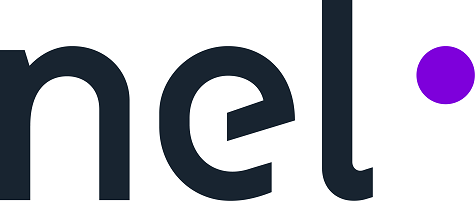
This information has been sourced, reviewed and adapted from materials provided by Nel Hydrogen.
For more information on this source, please visit Nel Hydrogen.