SAFSTRIP® is a pultruded composite strip that improves the strength of an existing structural member when mechanically fastened to the structure. It has high bearing and longitudinal properties, and is designed to strengthen the flexural capacity on the tension face of concrete slabs, decks and girders. Installation on bridges can be carried out without interrupting service.
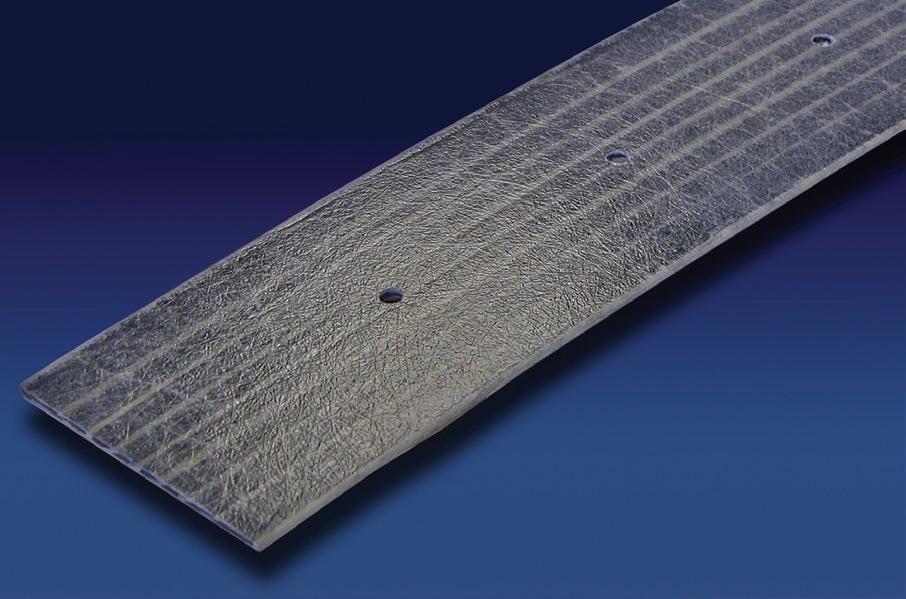
Strongwell supplies SAFSTRIP® in rolls, and may also supply it with pre-drilled holes at the required fastener spacing to receive fasteners. It measures 4" wide x 1/8" thick, and is shipped in rolls as long as 100 ft. The strip is designed so that the customer can easily field cut the strip into shorter lengths using standard carpenter tools.
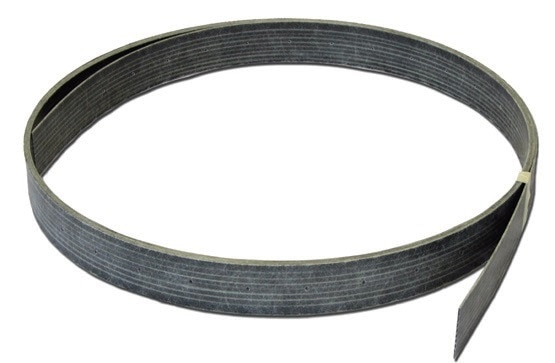
The following are the key features of the SAFSTRIP®:
- Minimal surface preparation required for installation
- Easy to install, with skilled labor not required
- Cost-effective system to increase load capacity of bridges
- Structure is usable immediately after installation
- Will not delaminate or split when drilled
Materials of Construction
SAFSTRIP® is made of carbon tows sandwiched between layers of fiberglass mats and rovings. A highly corrosion resistant vinyl ester resin is used to bond the materials together.
While carbon fibers increase the stiffness of the strip, glass mat offers the proper bearing strength. Thanks to these combined properties, SAFSTRIP® can be mechanically attached to a structural member. To improve resistance to corrosion and UV degradation, a synthetic surfacing veil is also incorporated into the composite.
What is MF-FRP?
SAFSTRIP® is designed to be installed using a fastening method called mechanically-fastened fiber reinforced polymer (MF-FRP). This method enables SAFSTRIP® to be fastened to an existing concrete slab, deck or girder using steel expansion anchors or closely spaced powder actuated fastening pins.
A powder actuated fastener gun or other portable fastener gun is used to apply the pins. A pneumatic powered torque wrench is used to install the expansion anchors. If needed, neoprene or rubber washers can be used between the strip and the fasteners before inserting the fastener through the strip.
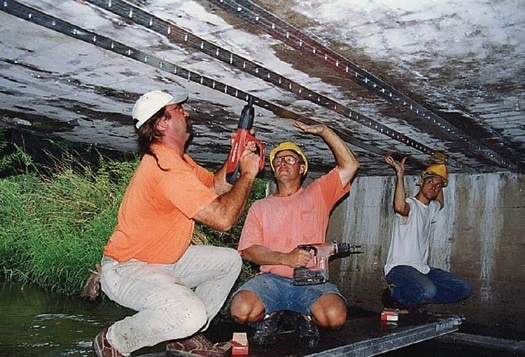
Workers installed SAFSTRIP® on this bridge in Edgerton, Wisconsin, using the MF-FRP system. The load rating for the bridge increased from HS-17 to HS-25 as a result.
MF-FRP is used as an alternative to externally bonded fiber reinforced polymer (EB-FRP). Unlike the MF-FRP system where the load is transferred to the composite strip via a fastener, the EB-FRP system applies an adhesive.
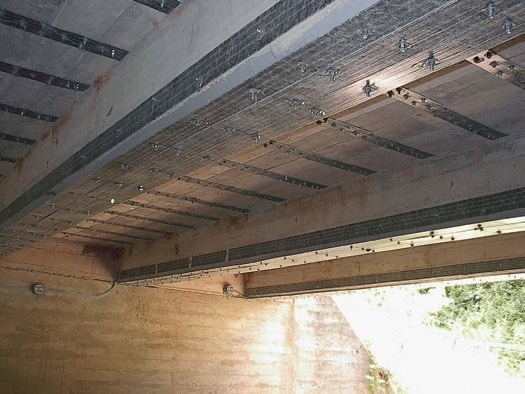
The posted load for this bridge that spans the Meramec River in Missouri was increased from 10 tons to 18 tons by installing SAFSTRIP® using the MF-FRP system.
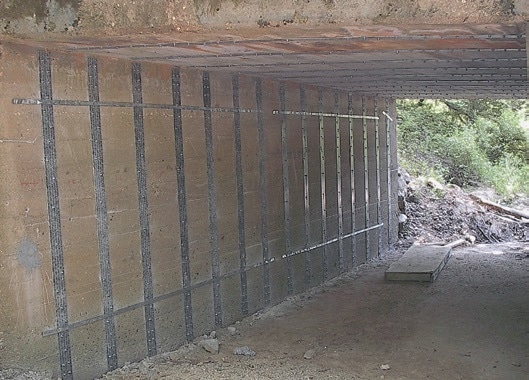
The abutment and deck of this bridge in Phelps County, Missouri, was strengthened using SAFSTRIP®.
Research and Development
The U.S. Army Engineer Research and Development Center (ERDC) funded the research development for SAFSTRIP®. Laboratory research was performed at ERDC's test laboratories and at the University of Wisconsin Structures and Materials Testing Laboratory. Bridge demonstration projects were carried out in Missouri and Wisconsin.
Engineering Design
The repair of concrete structures using SAFSTRIP® depends on the condition of the concrete. The strength of the existing concrete must be determined by the local engineer. Then, the amount of SAFSTRIP® required and the spacing of fasteners must be determined.
Design assistance can be obtained by using the SAFSTRIP® Design Software available on Strongwell's website or by contacting the company. The software is a quick, user-friendly spreadsheet that suggests hole spacing based on the engineer's input concrete and load conditions.
Mechanical Properties
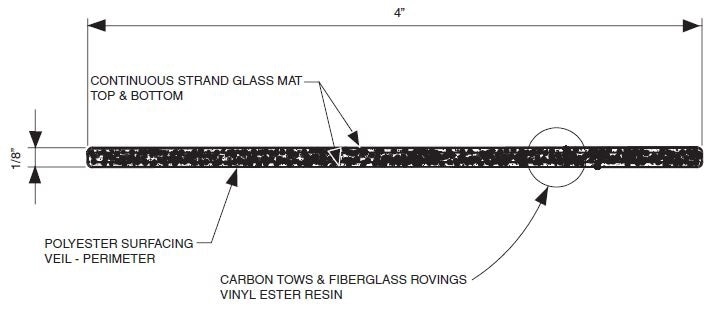
Property |
Average Value1 |
Design Value2 |
ASTM Test Method |
US Units (psi) |
SI Units (MPa) |
US Units (psi) |
SI Units (MPa) |
Tensile Strength* |
123,613 |
852 |
92,902 |
640 |
D-638 |
Tensile Modulus*3 |
9.02 x 106 |
62,190 |
9.02 x 106 |
62,190 |
D-638 |
Clamped Bearing Strength* |
50,955 |
351 |
40,540 |
279 |
D-5961 |
Unclamped Bearing Strength** |
31,044 |
214 |
26,046 |
180 |
D-5961 |
Open Hole Strength* |
94,641 |
652 |
78,846 |
543 |
D-5766 |
*20 Sample coupons per test series
**17 Sample coupons per test series
1 Average value of test series
2 Average value minus three standard deviations
3 Modulus design values are not reduced in accordance with ACI 440.2R-02
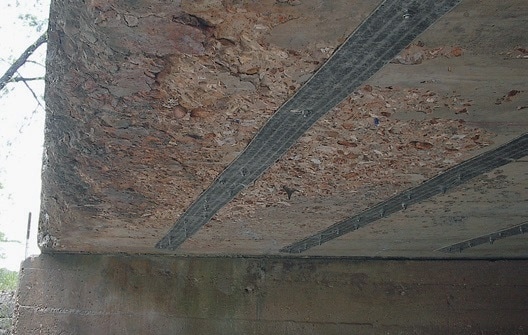
As a result of a SAFSTRIP® retrofit, the existing 12-ton load posting for this bridge in Phelps County, Missouri, was removed.
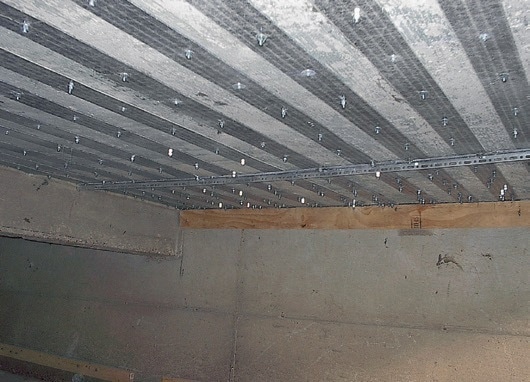
This bridge, located in St. James, Missouri, was load posted at the time of strengthening. After mechanically attaching SAFSTRIP® with concrete wedge bolts and anchors, the bridge load limit was raised to 20 tons.
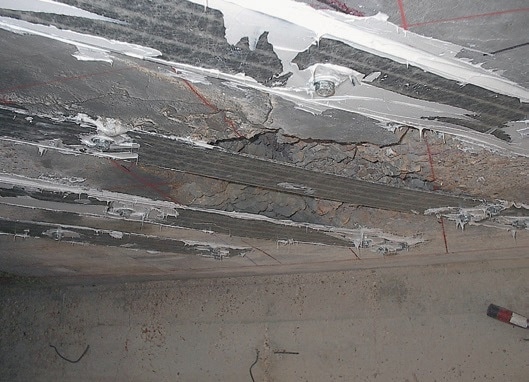
Severe deterioration prevented the application of a bonded strengthening system to this bridge in Pulaski County, Missouri, but MF-FRP applied SAFSTRIP® was able to repair the bridge.
Comparison of MF-FRP Installation and EB-FRP Installation
The following table provides a comparison between MF-FRP Installation and EB-FRP Installation:
|
MF-FRP Installation |
EB-FRP Installation |
Fastening System |
Mechanical - powder actuated fasteners or concrete wedge bolts and anchors. |
Adhesive - usually epoxy. |
Surface Preparation |
Minimal |
Requires the time consuming process of sandblasting, cleaning and application of epoxy putty that needs to be ground down for a smooth surface. |
Weather Condition for Application |
No restrictions. Can be installed even during inclement weather |
Application surface must be moisture-free. Installation is not possible in extreme temperatures. |
Installation Time |
Minimal - generally a few hours. |
Extensive due to the surface preparation, mixing of adhesives and care required to properly apply the adhesive. |
Labor Costs |
Unskilled labor using standard carpenter tools for cutting and installing strips reduces labor costs. |
Skilled labor required to properly prepare the surface and mix the adhesives, resulting in higher labor costs. |
Bond Strength |
Not highly affected by poor condition of the existing superficial/outer concrete substrate. |
Dependent on the quality of the concrete substrate. |
Availability of Structure |
Available for immediate use upon application. |
May require up to seven days to achieve full adhesive strength. |
Durability |
Tests show excellent retention strength for anchor bolts. Excellent fatigue strength. |
Research suggests high strain gradient is found in adhesive layer where strips terminate or in proximity of substrate discontinuity (such as cracks). Debonding can be problematic. |
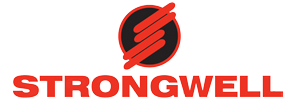
This information has been sourced, reviewed and adapted from materials provided by Strongwell Corporation.
For more information on this source, please visit Strongwell Corporation.