While general materials for education and orthopedic testing – usually cadaver specimens, wood, and animal bones – are useful, they are not suitable for today’s students and researchers. They have many shortfalls, including scarcity, consistency across specimens, and cost.
.jpg)
Image Credit: Sawbones®
When it comes to supply and demand, cadavers are available either by donation or through bodies that are not claimed after death. Scarcity in the supply funnel results in increased cost per specimen. Associated regulations for shipping, storing, and disposing of human specimens also contribute to the increased costs. Finally, all specimens are not created equal.
Variations exist across specimens either due to changes attributed to embalming processes or due to individual differences. In addition, the fact that a large number of cadaver bones come from the infirm and elderly, which is not necessarily representative of the population at large, can also negatively impact the consistency required for statistical robustness and medical accuracy (Horn, 2010; Elfar, 2014).
A Suitable Substitute
Many medical researchers and educators, who have been searching for a more reliable medium, have found polyurethane foam as the composite material of choice for orthopedic models. Polyurethane promptly addresses the disadvantages of conventional materials in that:
- There is no shortage of supply; commercial sellers readily supply polyurethane foam that meets the different requirements of both researchers and educators
- Depending on the selected manufacturer’s methods, batch-to-batch consistency may be ensured across materials
- When compared to acquiring cadaver specimens, batches can be generated at a significantly lower cost
Additionally, polyurethane foam is resistant to mold and moisture and is not subject to the stringent regulations of cadaver bones. This makes storage, shipping, and disposal of the polyurethane foam simple and inexpensive (Elfar, 2014).
However, the most important question is whether the polyurethane foam is an appropriate analog for bone. Does it imitate the bone properties required for accurate biomechanical testing? The answer is yes.
Numerous studies have found that polyurethane foam is a suitable alternative for human cancellous bone, in terms of its mechanical properties and also as a substrate for implant testing (Shim, 2012; Horn). Polyurethane can be easily processed to emulate both the elastic modulus and compressive strength of bones.
It can also imitate healthy bone, and by modifying the density of foam, conditions like osteoporotic bone can be reconstructed for analysis (Patel, 2008). The American Society of Testing Methods (ASTM) has approved rigid polyurethane foam for use as a standard material for testing orthopedic devices and instruments (ASTM, 2012).
.jpg)
Image Credit: Sawbones®
An Experienced Partner
General Plastics can be considered as a partner and supplier for companies prepared to make the switch from conventional materials to polyurethane foam for orthopedic testing and education purposes. General Plastics, with over 80 years of experience as an innovator in the plastics industry, has perfected quality assurance processes in place and has a long track record of meeting the most stringent requirements of customers.
In orthopedics, the LAST-A- FOAM® FR-3700 polyurethane foam series is frequently used as artificial media for testing bones. It is available in different densities ranging from 3 to 40 lb/ft3, and can be made to imitate human bone across different conditions and testing requirements.
Polyurethane foam has a reliable cellular structure that closely mimics human bone, and is suitable for medical students to develop their surgical skills as well as for research purposes.
According to a recent study (Iweju, 2014), General Plastic's Last-a-Foam® series was found to be better than other grades of polyurethane foam and polymer materials for artificial joint testing. General Plastics' Last-a- Foam® products (PU2 and PU3 shown in the charts below) were a suitable substitute for human cancellous bone across several qualities critical in orthopedic research, including compressive strength, tensile strength, and density.
.jpg)
.jpg)
Image Credit: General Plastics
General Plastics has the products and experience to meet osteopathic research and educational requirements.
References
ASTM International. Standard Specification for Rigid Polyurethane Foam for Use as a Standard Material for Testing Orthopaedic Devices and Instruments. West Conshohocken, PA: ASTM International; 2012.
J. Elfar, MD, S. Stanbury, MD, R.M. Garcia Menorca, J. D. Reed. Composite Bone Models in Orthopaedic Surgery Research and Education. J Am Acad Orthop Surg. 2014 February ; 22(2): 111–120.
T. Horn, O. L.A. Harrysson, J.P. Little, H. A. West II, D. J. Marcellin-Little; Design and Manufacturing of Bone Analog Models for the Mechanical Evaluation of Custom Medical Implants. 2010 September; https://www.researchgate.net/publication/267794405
C.C. Iwejua. Alternative to Bone for Laboratory Testing of Artificial Joints. 2014 September.
PS Patel, DE Shepherd, DW Hukins. Compressive properties of commercially available polyurethane foams as mechanical models for osteoporotic human cancellous bone. BMC Musculoskelet Disord. 2008; 9:137. doi:10.1186/1471- 2474-9-137
V. Shim, J. Boheme, C. Josten and I. Anderson (2012). Use of Polyurethane Foam in Orthopaedic Biomechanical Experimentation and Simulation, Polyurethane, Dr. Fahmina Zafar (Ed.), InTech, DOI: 10.5772/47953.
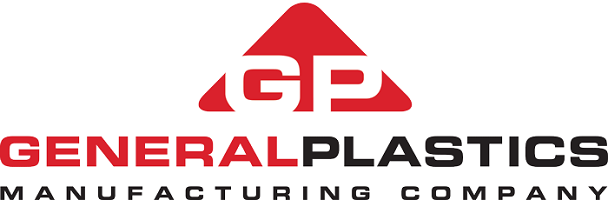
This information has been sourced, reviewed and adapted from materials provided by General Plastics Manufacturing.
For more information on this source, please visit General Plastics Manufacturing.