Researchers from an Australian university have developed a novel one-step printing process that has the potential to significantly decrease the time and cost of optical lens manufacturing.
.jpg)
Image credit: Shutterstock / Chernov Victor
Utilised in everyday life, from the mouse that you are currently navigating your computer with to endoscopes and life-saving diagnostic tests in healthcare all use miniature optics lenses. Even in the communication networks between this data and your computer, the transmission is being facilitated by lenses coupled with adjoining optical fibers.
At present, the manufacturing of optical lenses requires a complex multi-stage process that involves injection, moulding, diamond milling and polishing. The cost of optical lens devices is currently high due to short time constraints and expensive manufacturing equipment.
The single-step printing method developed by the Australian researchers will reduce the cost of such devices, as the lens production will become simpler and be easily tailored to a given application.
Capillary surface tension and gravity forces are utilised with transparent silicon droplets to produce lenses, in seven seconds, that are durable, scratch-resistant, flexible and of high quality.
These lenses have a high optical clarity and can be moulded into any desired shape. They also have an improved surface roughness compared to lenses currently available. They provide up to 160x magnification and can image structures at the micrometre level.
This property has the potential to transform smartphone cameras into high-powered microscopes (see figure below). The market for personalised diagnostics using smartphones is always expanding and is expected to be worth in excess of $26 billion by 2017.
Companies are currently using 3D printers and other prototypes to reduce the time and cost involved with optical lens production. Unfortunately, many face application limitations which can including the limitation of use to one part of the electromagnetic spectrum. The lenses produced by this new method can be used in applications spanning across all UV to IR wavelengths.
The Australian academics are currently scaling up their process with help from an industrial partner. They are currently seeking other industry partners for high throughout manufacturing, and to take this technology to the commercial market.
To find out more information about the process and how to collaborate with the researchers and to receive industry-exclusive access to IN-PART, simply register for free.
About IN-PART
IN-PART is the leading platform for university-industry collaboration. On IN-PART, Offices of Technology Transfer from universities around the world publish innovation and expertise developed by researchers who are actively looking to partner with businesses.
Professionals in industry can gain free access to IN-PART through a simple registration, and so browse, review and connect with the latest technology from universities for potential collaborations.
For more information and to gain access, register here.
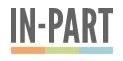
This information has been sourced, reviewed and adapted from materials provided by In-Part.
For more information on this source, please visit In-Part.