As one of the most hyped technologies of the last few years, 3D printing has received great attention. But did you know that it has a ‘bigger brother’, so to speak, in additive manufacturing.
3D printers are ideal tools for small scale and home-based printing, but additive manufacturing encompasses a broader range of techniques, which promise large scale production of robust and complex components.
.jpg)
Image credit: Shutterstock / ThamKC
Additive manufacturing can fabricate components from a range of materials (including metals and plastics) and combinations of each. These machines can produce very accurate and precise intrinsic structures that has never been possible before by either machine or human fabrication.
The differences between fabrication methods used today and additive manufacturing can be easily overlooked. Normal fabrication methods, independent of the material used, generally use processes that are cut, chipped, ground or polished from a larger material in a bottom-down approach.
This is the case for common materials such as wood, metal, plastic and stone. Additive manufacturing, however, uses a bottom-up, layer-by-layer (LbL) approach which sequentially builds the material from nothing.
The governing processes involved in additive manufacturing are becoming more complex, and researchers on the West Coast of the US are developing novel techniques that can fabricate microscopic details to create unique properties into the finished products.
Optical Blueprints
A digital design of the intended product is the cornerstone of any computer-aided manufacturing process. To produce a useable blueprint, the 3D structure is first sliced into a horizontal cross-sectional layer of equal thickness. Each slice becomes the blueprint for its corresponding layer and the layers are then fabricated sequentially using specific techniques. One method, known as projection micro-stereolithography, can fabricate complete structures in minutes.
Micro-stereolithography utilises light sensitive materials (certain polymers) to produce the structure. Flooding of the surface of a dynamically lowered platform, with a thin layer of fluidic material, is the first step. This is followed by laser-curing to harden and stabilise the structure.
The blueprint slice is used as a light filter and only exposes the areas of the layer that should contain material. The fluid not exposed to the light remains does no change phase and is washed away. More complicated techniques use sophisticated optics to focus the laser light and produce micrometer structural changes.
Pen and Paper Micro-manufacturing
A different fabrication method that draws out the material structure and extrudes the material as a fluidic ink through a nozzle, like that of a pen, is known as ‘direct ink writing’. The method builds up successive layers to create the full structure. The method can also be used with ceramics as well plastics. Complex scaffold materials can be made by precise placements from a robotic arm, something which is not possible by other methods.
Applications as human tissue implants has thus far been the most prominent field of research for additive manufacturing. The design allows for the shape and size of the missing tissue on the patient to be precisely fabricated using biocompatible materials. A recent breakthrough from this West Coast research institution has afforded potential further applications as energy absorbing materials. The fabrication of such materials has the potential for many commercial applications, including shoe soles, crash helmets, mattresses, safety equipment to name a few.
Complex Bonding
The final process is laser-initiated deposition. This method allows advance coatings composed of alloys and ceramics to be chemically bound to a metal surface. Strong bonding interactions lead to a myriad of properties including induced conductivity, corrosion-resistance, anti-slip and thermal resistance. Like the other techniques, these coatings can be applied in uniform or complex patterns to produce printed circuit boards (PCBs), anti-skid surfaces, ultra-efficient heat exchangers and fusion reactor systems.
The researchers from the US institution have expertise in all of these techniques and the ability to develop materials with unique microscopic details and lattice structures. The materials produced in this way behave like no other known material. They also possess an excellent combination of mechanical properties, such as high strength and low density.
About IN-PART
IN-PART is the leading platform for university-industry collaboration. On IN-PART, Offices of Technology Transfer from universities around the world publish innovation and expertise developed by researchers who are actively looking to partner with businesses.
Professionals in industry can gain free access to IN-PART through a simple registration, and so browse, review and connect with the latest technology from universities for potential collaborations.
For more information and to gain access, register here.
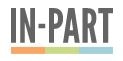
This information has been sourced, reviewed and adapted from materials provided by In-Part.
For more information on this source, please visit In-Part.