.jpg)
Shutterstock | Stihl024 2nd
Organic coatings are typically used to protect or beautify surfaces in many industrial and commercial applications. Varnishes, paints, stains, and industrial coatings, are some of the most common types utilized.
Companies often place significantly more emphasis on the final appearance of a coating product rather than focusing on its performance. Questions such as “which colors should be offered” or “where the company logo should be painted on” are given higher priority than the coating’s ability to resist damage. This can be a major mistake. Coatings protect against surface harm such as abrasion, scratches, and corrosion, while at the same time enhancing the appearance of a product.
.jpg)
Analysis
One of the most common tests to evaluate the abrasion resistance of coatings is ASTM D4060 Standard Test Method for Abrasion Resistance of Organic Coatings by the Taber Abraser. Referred to as the “Taber Test”, a plain, rigid surface is selected and a coating applied to it. The test specimen is placed on the Taber Abraser turntable and rotated at a fixed speed under a weighted CS-10 or CS-17 abrading wheel. Any loose debris generated during testing is removed by a vacuum system. An S-11 refacing disc is used to standardize the wheel surfaces by resurfacing the abrading wheels before each test and after every 500 cycles. Wear resistance, at the conclusion of the test, is expressed as:
- Wear Index: the weight loss per specified number of revolutions (usually 1000) under a specified load (500 or 1000 g);
- Wear cycles per mil: the number of cycles required to wear through a 1-mil thickness of coating; or,
- Cycles to failure: the number of test cycles to wear away the coating or to expose the substrate
However, the test is not as simple as it appears to be. Variation can occur in the test results even when the Taber Abraser has been calibrated. Sources that are often overlooked include:
(1) type of test plate (must be rigid and have both surfaces substantially plain and parallel)
(2) surface preparation of test plate
(3) method of application of the test film (dipping, spraying or film applicator)
(4) cure time of coating
Many customers are choosing Taber’s Linear Abraser, when testing a 4 " test plate is not feasible. The Linear Abraser uses the same high-quality Taber abrasive media found in the company’s other well-known wheels, and can test contoured products, providing an alternative way of determining the robustness of a product’s coating. Many companies are realizing that cycles to failure is a sufficient method of evaluating the coating performance when testing with the Linear Abraser, though an ASTM method is yet to be established.
Benefit
A belief held by most consumers is that the price paid for a product has a direct bearing on its inherent level of quality. An essential element of this perception is the resilience of the product finish, i.e. the amount of time before it becomes “worn out” or damaged. To remain competitive, manufacturers are making substantial efforts to minimize production costs. These can include specifying a different type of finish or changing material suppliers. Unfortunately, due consideration is not given to the question of whether these changes will impact upon product performance. To validate product quality, it is necessary to employ a meaningful test program, which can also ensure that the specified coating satisfies both the customer’s and the company’s expectations.
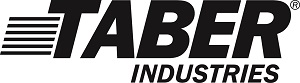
This information has been sourced, reviewed and adapted from materials provided by Taber Industries.
For more information on this source, please visit Taber Industries.