Waterjet technology has always been considered an eco-friendly technology, but it is becoming even greener as more shops are investing in green accessories that provide environmental benefits and are also good for their profits.
Closed-Loop Filtration
Perhaps, the greenest of all waterjet accessories is the closed-loop filtration systems, which allow the waterjet shops to filter, cool and recycle water, removing the need to push it down the drain. They are essential for desert environments, and are needed for ISO-9000 certification and required by many municipalities. Waterjet shops that do not have a floor drain can use closed-loop filtration systems.
When I have a closed loop filtration system and chiller, I am taking the water after the cutting process, giving it a three-stage cleaning and providing a filtration level of 50 parts per million, total dissolved solids. I’m chilling the water as well and providing that back to the cutting loop of the pump, re-pressurizing it and completing the loop. Reusing the water and zero discharge to the environment is what it’s all about.
Bradley Schwartz, Jet Edge
One of the many waterjet shops that are insisting on closed-loop filtration for environmental reasons is the Twelve Strike Bowling Services of Long Beach, California.
“We are in the desert here and water is a huge issue,” explained Twelve Strike’s owner Ron Richmond. “I also did not want to be dumping water down the drain. I do not have an environmental issue here and I do not want one.”
An ingenious system has been developed by Precision Waterjet Concepts to use its waterjet chiller. To heat its Northern Minnesota waterjet shop, the company uses the hot water generated by its five waterjet systems. Using this arrangement, the company saves a lot on its heating bill during the cold winter season in Minnesota.
Garnet Recycling
The most expensive operational expenditure item of a waterjet system is the garnet. Abrasive waterjets experience 0.5 to 1.5 pounds (0.25 to 0.68 kg) per minute of the abrasive material, and depending on the grade, can cost anywhere between 20 cents to over 40 cents per pound. Fortunately, garnet can be effectively recycled.
In order to reclaim 50 - 70 percent of the garnet, Garnett Gerke of G.O. H20 of Edmonton, Alberta, Canada, employs a garnet abrasive recycling system. The used garnet is mixed with new garnet with the added benefit of no reduction in cutting speed. Using this technique, the cost of the recycling system was recovered in one year, and now it is used to recycle abrasive from two waterjet machines.
.jpg)
Gerke explained that to minimize downtime for shoveling out the tank and reduce disposal costs, he had to develop this technique to remove the garnet from the tank and reuse it. "In our first two years [cutting 24/7], we had had to shut down every seven to 10 days to clean out the tank," Gerke recalled. "We would be down 8-12 hours. We had a sump truck come in and pump out the tank and haul the garnet off to the landfill. The first year, he charged $400 per visit. Two years later, it was three times the cost."
According to Schwartz, it is definitely worth to recycle the material if the disposal costs are high in a particular area.
Only about 30% of the abrasive is actually doing the work and the rest is going right into your tank. You can reclaim this.
Bradley Schwartz, Jet Edge
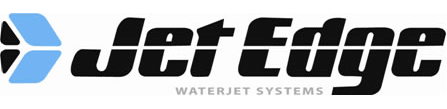
This information has been sourced, reviewed and adapted from materials provided by Jet Edge, Inc.
For more information on this source, please visit Jet Edge, Inc.