.jpg)
In today’s competitive environment, manufacturers put significant efforts into minimizing production costs to remain competitive. These efforts might involve changing material suppliers or specifying a different material or type of finish.
Unfortunately, changes can be implemented without adequate consideration of how they will impact long-term product performance.
When evaluating resistance to scratch and mar, the objective is to make certain the product maintains a minimum visual appearance over its estimated life. Regardless of whether the material (or coating) is for cosmetic appeal or functional performance, surface damage that occurs too soon will detract from a consumer’s perception of product quality.
While laboratory techniques usually do not exactly duplicate the mechanics seen in real-life, a controlled test allows the user to approximate field conditions and evaluate materials using the same set of criteria. This approach can provide considerable insight into the various factors that contribute to a material’s performance. Especially when there are many opportunities for damage to occur; beginning at the point when the part is manufactured to after it is placed into service.
Analysis
The objectives of most scratch and mar resistance lab studies are to: (1) determine the behavior of the material under specific test conditions; (2) establish a relative ranking of similar materials; or (3) determine the failure limit of the material or surface coating.
For a laboratory scratch test, a stylus with a defined geometry is drawn across a specimen surface at a known speed and with a known force. Mar tests might utilize a counter-faced material such as steel wool that produces damage over a greater area. The ultimate goal of either test is to simulate damage that might occur during normal usage and handling, shipping or assembly procedures.
Customers familiar with Taber Industries have relied on the company’s expertise for low cost, affordable test solutions.
Taber’s Shear / Scratch Tester is commonly used to measure a material’s resistance to gouging, scratching, or shearing. A precision diamond tool is affixed to a balanced scale beam. Test pieces are mounted to a turntable, which rotates at a constant speed when actuated. By changing the position of a sliding weight, loads from 0 to 1000 grams may be applied to the cutting tool.
.jpg)
Taber’s Shear / Scratch Tester
Evaluation is determined by the minimal load to produce a continuous mark on the coating surface. By changing the position of the scratch tool on the test specimen, the operator can create a series of circular scratch marks. The depth of the scratch marks can be reduced from one line to the next by reducing the load, up to the point where no scratch mark remains visible or is noticeable under an accepted definition. This makes it possible to identify small differences in scratch resistance.
Originally developed by Ford Motor Co., Taber’s Five Finger Scratch and Mar Tester includes a pneumatically driven, movable sled and five “fingers” that include either 1.0 mm tungsten carbide scratch pins or 7.0 mm mar tips. Each tool is loaded with different weights, so they exert a constant, vertical standard force on the test surface ranging from 0.6N to 25N. After lowering the scratch tips onto the specimen surface, compressed air drives the platform under the scratch tips at a speed of 100 mm/second to generate the damage on the specimen surface.
.jpg)
Taber Industries' Five Finger Scratch and Mar Tester
Taber Industries’ Linear Abraser incorporates a horizontal arm that reciprocates in a linear motion. Attached to the end of the arm is a ‘free-floating’ test system that is placed onto the specimen at the start of the test. As the arm cycles back-and-forth, a spline shaft raises or lowers as the test attachment follows the contours of the specimen being tested.
This feature permits the testing of actual production parts and allows the operator greater flexibility with test set-up. To simulate real-world conditions, parameters such as speed, stroke length and load can be altered according to the material and test being conducted. For soft materials, a 1.0mm diameter hemisphere Scratch Tip is suggested. For harder materials, a conical tool such as the Diamond Scratch Kit or various Tungsten Carbide Scratch Tips may be used.
.jpg)
The Linear Abrasion Tester from Taber Industries
The Multi-Mar Attachment allows the operator to conduct similar tests as the balance beam tester using mar and scratch tools such as a paperclip, loop stylus, needle stylus, Hoffman type stylus and coin. In addition, optional accessories are available to generate different types of scratch or mar damage. These include the steel wool holder, Scotchbrite® pad kit, Crockmeter kit, coin holder, pencil hardness kit, 3 mm Borosilicate sphere holder, and others
Benefit
Employing a meaningful test program is a necessary step to validate your product quality, and to ensure that the surface finish you specify meets the customer’s expectations.
While accelerated laboratory tests may not always identify potential problems or provide predictive performance results, they can be an inexpensive means to generate useful data in a relatively short period. Testing also provides an opportunity to create value with your product, and can be invaluable in avoiding material or coating issues.
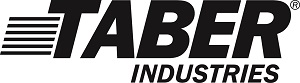
This information has been sourced, reviewed and adapted from materials provided by Taber Industries.
For more information on this source, please visit Taber Industries.