The potential for forming processes based upon semi-solid metal alloys was first recognised in the early 1970s. The microstructure of a suitable alloy comprises spheroidal particles of solid surrounded by liquid phase of a lower melting point, rather than the interlocking tree-like dendrites of conventionally cast alloy. It is this microstructure that gives the material its thixotropic properties, i.e. when sheared the material flows, but when allowed to stand, it thickens. Thixoforming is one member of a family of semi-solid forming processes and it possesses characteristics of both casting and forging. The non-dendritic feedstock necessary for thixoforming is usually produced using electromagnetic stirring in a continuous casting process. The Thixoforming Process The thixoforming process incorporates four operations, figure 1. • Firstly, a bar of thixoformable raw material is cut into appropriate slug lengths. • Then the slugs are heated in a controlled manner, using either an induction coil or a muffle furnace, into a uniform ‘mushy’ state. • The heated slug is transferred to the shot sleeve of a suitably modified die casting machine and injected into a die. • The component feeder and gating systems are then removed using a clipping press or band saw. 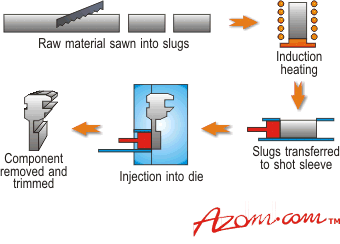 | Figure 1. Schematic of a thixoforming process cell. | Mould Materials Thixoforming allows the use of softer, cheaper die materials due to the reduced mechanical stresses acting on the die during filling and the lower alloy processing temperature, e.g. for example, graphite, easily machinable stainless steels and disposable one shot non-metallic dies have all been used. This permits the application of thixoforming to the small production volumes required by rapid prototyping and mass customised production. Advantages of Thixoforming The advantageous attributes of thixoforming have been described as follows: • It is an energy efficient process which is easily automated and controlled to achieve consistency • Production rates are similar to pressure die casting or better • Smooth filling of the die with no air entrapment and low shrinkage porosity gives parts of high integrity • Lower processing temperatures reduce the thermal shock of the die, promote die life and allow the processing of high melting point alloys (such as tool steels and stellites) that are difficult to form by other means • Fine, uniform microstructures give enhanced component properties • Weight savings can be achieved through optimised component design. The high mechanical, geometric and surface quality of components produced through thixoforming can justify the removal of additional production processes such as machining steps and the need for reinforcing inserts. A simpler, more flexible production process requires fewer resources for control and allows a more rapid response to changing customer requirements. The extent to which these benefits are achieved depends upon the design of the component and its dies, the optimisation of the processing conditions, the integration of the technology into an existing production process and the demands of the organisation's business environment. Not only are such benefits difficult to quantify in an analysis, but they are also dependent upon managerial decisions. Limitations of the Thixoforming Process A number of drawbacks currently limit the commercial viability of thixoforming: • The high cost of raw material and the low number of its suppliers • The considerable research effort and expense required to implement a viable manufacturing process due to the limited process knowledge • The higher die development costs than for conventional forming technologies because of the lack of available process experience and design rules • The higher level of training required for personnel employed to operate and maintain a thixoforming plant compared to traditional operators. Despite the recent development of product quality and customer service as sources of manufacturing competitiveness, in many industries cost is still regarded as the primary consideration. The relatively high price of suitable feed stock for the thixoforming process is therefore perceived to be the major barrier to its commercialisation. As these prices are related to volumes of raw material production, they are unlikely to fall until demand increases significantly. Concluding Remarks The characteristics of the thixoforming process allow savings to be made in many other areas (e.g. removing machining operations, increased sales, reduced material use, surface treatments, energy savings) and so will often offer economic benefits overall. The automotive component illustrated in figure 2 is an example where the near-net-shape, mechanical integrity, high strength, optimum ductility and high volume of production characteristics of thixoforming have enabled a cost effective design solution to be achieved. The issue for potential industrial users is therefore to evaluate accurately the full extent of the costs and benefits to be gained through implementing the technology. The difficulties in achieving this arise from the reliability of predictions of future cash flows and evaluation of what are often considered to' be ‘intangible’ benefits. 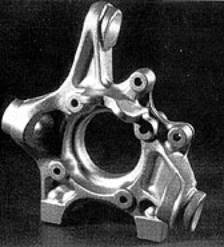 | Figure 2. An example of a thixoformed automotive component. | |