Interview conducted by Mychealla RiceMar 29 2017
In this interview Dr. Sivakumara Krishnamoorthy, Manager of New Applications at Evonik Performance Foams talks to AZoM about their newest technology, PulPress™ for Automotive and Aerospace industries.
Dr. Sivakumara explains the benefits and advancements PulPress™ offers over previous methods for producing complex composite components.
By using a core material that can withstand high temperatures and pressurised environments, Evonik’s PulPress™ Technology employs the latest in innovative high performance materials and technology to produce composite components cost-effectively.
Could you give a brief overview about the new PulPress™ technology Evonik has recently introduced?
PulPress™ technology is a unique new processing method developed by Evonik that enables manufacturers to produce complex 3-dimensional, molded composite parts in high volumes.
The first components made using PulPress™ technology are already making their way into series production this year and cost savings are up to 60 percent over established methods traditionally used in the past.
What was the incentive behind creating the PulPress™ Technology?
Our customers in the mobility sector are increasingly looking for lightweight solutions and have begun relying more and more on composites as a means of reducing fuel consumption and CO2 emissions. Until now, composites were primarily used in high-end segments and luxury-class automobiles because established composite manufacturing technologies can be expensive and complex.
With the introduction of PulPress™ technology, manufacturers now have a new option that gives them an efficient and easy-to-use process. Making design decisions that replace metal components with high performance composites no longer carries a high price tag.
.jpg)
What does the PulPress™ Technology offer that other technologies do not?
The PulPress™ method makes it possible to produce a high-quality complex composite component quickly, economically and with no waste. This simply isn’t possible with standard processes used in the past.
For example, Resin Transfer Molding (RTM) involves a number of intermediate steps, relatively long cycle times and generates a lot of scrap. So the cost of parts are pretty high if using RTM.
Another standard process called Pultrusion is fast, continuous and economic, but the freedom of design is very limited – so only simple parts are possible. However, PulPress™ technology uniquely combines two traditional production techniques: compression molding and pultrusion. The result is an efficient solution that creates complex composite parts that are affordable.
Does PulPress™ Technology require a specific material for the core of the components?
Critical to success in implementing PulPress™ technology is using a core material that can withstand the high temperature and pressure environment.
Evonik’s high performance ROHACELL® polymethacrylimide (PMI) foam is the perfect material solution. This extreme processing environment is where ROHACELL® performs better than any other structural foam available and is easily thermoformed.
What are the technical advantages and manufacturing benefits of PulPress™?
Particularly impressive aspects include design flexibility, efficiency and superior mechanical properties of the finished parts. The composite parts are around 75 percent lighter than traditional steel structures, yet they provide the same strong and dependable support. Mechanically, these low density components demonstrate excellent load carrying capacity and have excellent crash behavior during impact.
Additionally, the Pulpress™ process generates almost no waste of the core material, fibers or resin. This obviously has ecological and economic advantages for manufacturers.
As an added advantage, the method allows easy integration of polymer or metal inserts for mechanical load transmission between components, so post-processing steps and the costs incurred are eliminated.
Can you explain the economic benefits of PulPress™?
Three major factors contribute to significant cost reduction when making composite parts using PulPress™ technology. First, the method eliminates material waste and several steps in NC-machining for shaping complex foam geometries.
Furthermore, the raw fibers and resin are 100% utilized when building the composite parts. Second, cycle times are significantly improved thanks to the ability of ROHACELL® to quickly process at high temperatures and pressures. A single compact production line has an output of more than 30 components per hour.
Third, the simplicity of the technology eliminates several intermediate processing steps used in standard methods including preforming, draping, binder-activation, lay-up, etc.
.jpg)
kvsan/shutterstock.com
How will the automotive industry benefit from Evonik’s new PulPress™ Technology?
In the automotive industry, complex composite profiles can be used as lightweight structural components within the car body design or as add-on parts for bumpers, impact beams, strut braces, roof racks and roof bows.
PulPress™ also makes it possible to achieve lower “packaging space” in a vehicle body while maintaining identical structural performance. This reduction in required space results in more design freedom to shape new attractive exteriors for car bodies.
Even chassis components, such as stiffness bars and shafts, can be made in PulPress™ method. Benefits of PulPress™ technology have already won over a number of Evonik customers in the automotive industry.
Does PulPress™ offer any advantages to the aviation industry?
The technical & economic benefits of PulPress™ technology are certainly applicable to component manufacturers in the aviation industry. Very narrow dimensional and mechanical tolerances characterize the high quality PulPress™ parts.
So the process could conceivably be successfully applied in aircraft component construction as a cost-effective method for producing non-variable parts. Even variable parts with a common “base” geometry can be economically produced using modular tooling.
PulPress™ opens up new opportunities for structural solutions, where the move from metals to CFRP have been until now cost-prohibitive. Low cost processing of high performance materials could be a key enabler for mid- to long-term technology targets.
.jpg)
stockphoto mania/shutterstock.com
Why should a company use Evonik’s PulPress™ Technology?
Making ultra-lightweight, high performance parts using sandwich composites is a well-proven construction principle. PulPress™ process makes it possible to transfer the technology from high-end segments to mass production with fast, economic & resource-efficient production of composite components.
This brings new opportunities for component manufacturers as well as aircraft and automotive OEM’s in their quest to meet future demands in lightweight construction.
Evonik offers access to PulPress™ technology as an efficient part production solution. While we do not sell the actual finished parts, we can supply ROHACELL® foam cores for input and work closely with customers to offer technical engineering support to implement PulPress™ technology in their production.
Where can our readers go to find out more?
To learn more about Evonik’s PulPress™ Technology please contact a ROHACELL® representative in your area by calling +49 (6151) 18-1005 or emailing [email protected]
About Sivakumara "Siva" Krishnamoorthy
Dr. Sivakumara Krishnamoorthy is manager of the division New Applications within the Performance Foams business in Evonik’s Resource Efficiency segment and is responsible for PulPress™ technology. He began his career with Evonik in 2013 as a senior project manager responsible for new products & technologies within Project House Composites of Evonik Creavis GmbH. In 2016, he took over his current role in the marketing and sales unit of Evonik’s Performance Foams business.
Siva completed his Bachelor degree in mechanical engineering from the College of Engineering, Guindy, India in 2002 and then earned his Master of Science in computational mechanics of materials and structures from the University of Stuttgart, Germany in 2004. He later received his doctorate in engineering sciences from the RWTH Aachen University, Germany in 2010. Subsequently, he worked as a project manager & research associate at the German Aerospace Center in Stuttgart dealing with the development of lightweight vehicle structures.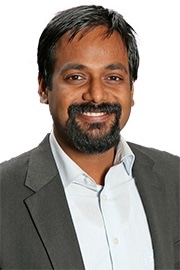
Disclaimer: The views expressed here are those of the interviewee and do not necessarily represent the views of AZoM.com Limited (T/A) AZoNetwork, the owner and operator of this website. This disclaimer forms part of the Terms and Conditions of use of this website.