Induction heating is considered to be a growth sector for several good reasons. The technique is extremely fast, reproducible, reliable, energy efficient and has an unlimited range of possible applications.
For instance, induction can be used on parts to heat, harden, braze, join, or even melt them. The inductor is a vital component in these processes. Its design plays a significant role in determining how precisely a part is heated. Thus, complex manufacturing processes are used to develop this central tool with precision to a tenth of a millimeter - a task perfectly suited to the experts at eldec, with facilities in Auburn Hills, Michigan, USA, and in Dornstetten, Germany. At these EMAG subsidiary units, technicians have a complete understanding of the various applications of induction heating. For more than three decades, they have been manufacturing inductors to match, which are adapted to the geometry of the workpiece with meticulous dimensional accuracy.
The word “precision” summarizes the crucial quality in induction heating in the best way possible. The technology is used in all places where an increased amount of heat or energy needs to be applied to a workpiece within a short time period. Temperature accuracy plays a crucial role here and is often process critical – and precise heating is only possible with the right mix of power, frequency, inductor geometry, and magnetic field characteristics. Additionally, the application of energy through induction guarantees economical energy consumption, minimal workpiece distortion and rapid production processes.
The process largely relies on the inductor and also on the generator used (as the power source), since the form of this tool plays a vital role in determining which areas of the workpiece are heated. As a result, it should not be surprising that the inductors used are as many and varied as the corresponding components or parts. For instance, eldec develops shaped inductors and ring inductors that enclose the part being heated with millimeter precision. Rod inductors are placed inside the part during the process, heating the metal from the inside out. Flat inductors are also commonly used, for instance, in induction brazing. They heat large areas of the part surface simultaneously and evenly.
Experience is Key
In total, we produce up to 1,000 inductors every year – and the numbers are rising. The crucial quality that many customers put their trust in is the experience of our fitters and engineers. Inductor manufacture is a demanding process that can't be automated because it depends on so many highly precise details. When you're brazing or assembling the inductor, every move has to be right.
Stefan Tzschupke, Head of Business Development Generators, eldec
eldec's customers get benefits from the initial stage itself, for instance, when they present a part drawing or blank. A production process is then proposed by the application engineers at eldec who ask and answer the following questions:
- What is the size and shape of the inductor?
- How is the induction process carried out in detail?
- What is the power capacity of the generator and what sort of temperatures need to be reached?
Once these questions are answered, we begin designing the inductor with the aid of the latest 3D CAD software and CNC machine tools. We test the end result on the real part. If the quality of the manufactured part doesn't satisfy us 100 percent, we make changes and rework the inductor, on a milling center for example. In the case of highly complex inductors, like those used for induction hardening for instance, this can be a matter of a few tenths of a millimeter.
Stefan Tzschupke, Head of Business Development Generators, eldec
Currently, specialists at eldec are testing new simulation software that they use to check the working of a virtual inductor model on a computer. This application will soon be put into practical use.
"That will take us to the next level. The users will ultimately benefit from even faster processes in development and even more precise induction processes." Said Tzschupke.
The use of sintering to manufacture the coils is another innovation at eldec. This allows the production of remarkably complex inductor geometry.
A Growth Area for the Company
The high degree of flexibility offered in inductor design and production is considered to be another important aspect of eldec's services. Customers needing a particular number of tools each year can sign an agreement with eldec to develop new inductors on a just-in-time basis. Users also have the option of developing additional inductors themselves. All in all, inductor manufacture is an extremely vital growth area for eldec. There are obvious reasons for this: First, an increasing number of companies in industries such as aerospace or automobile production are discovering the vast potential of induction heating. Increasingly complex parts are being annealed, hardened, or heated. Second, these developments highlight the need for specialized expertise in inductor manufacturing.
eldec is ideally positioned for these developments. We apply the knowledge gained from our experience to all aspects of the process, ensuring highly efficient and reliable production processes as a result.
Stefan Tzschupke, Head of Business Development Generators, eldec
.jpg)
The geometry of the inductors is as varied as the parts to be made with them. Ring or shaped inductors enclose the heated part with millimeter precision.
.jpg)
Another innovation at eldec is the use of sintering to manufacture the coils. This allows exceptionally complex inductor geometry to be produced.
.jpg)
Inductor manufacture is a demanding process that cannot be automated. When brazing or assembling the inductor, every move has to be right.
.jpg)
CAD workstation at eldec: the inductors are custom-designed on the computer.
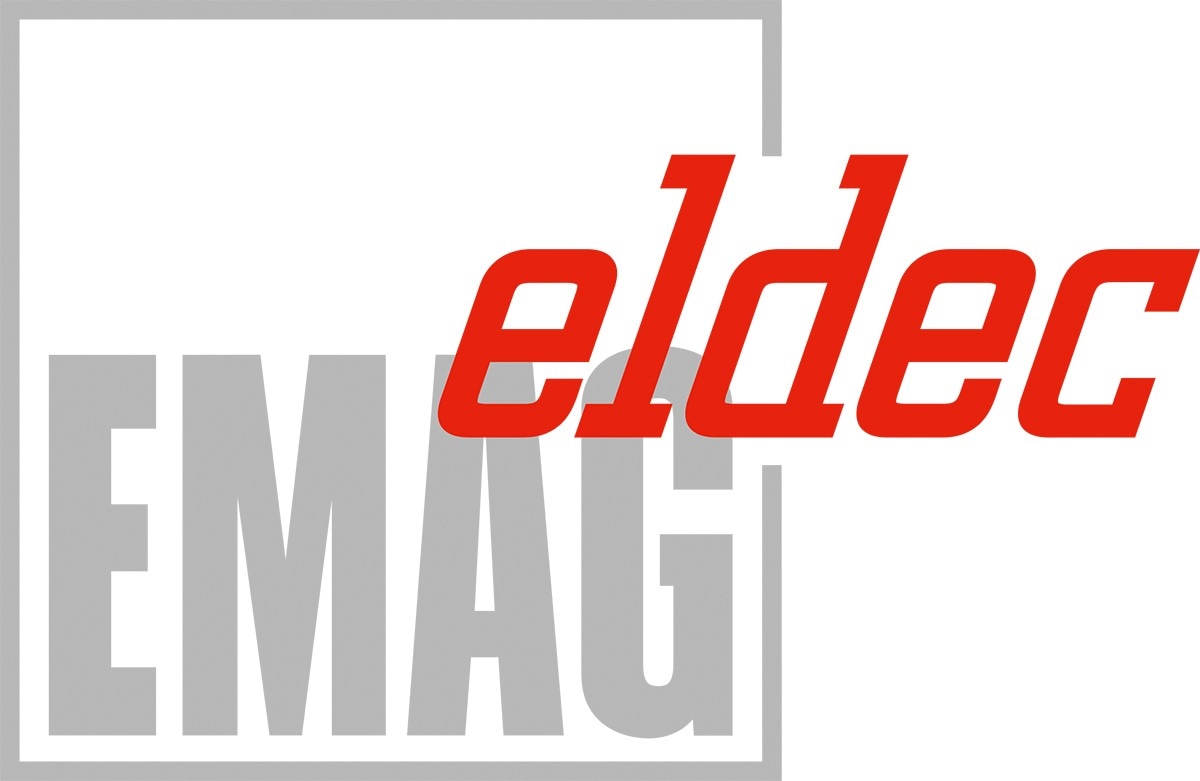
This information has been sourced, reviewed and adapted from materials provided by Eldec Induction USA, Inc.
For more information on this source, please visit Eldec Induction USA, Inc.