On 14 July 1865, while descending from the first ascent of the Matterhorn in Switzerland, four climbers plunged to their deaths after their safety rope snapped during a slip. It was this incident that generated the first enquiries into the safety and efficacy of mountaineering and climbing equipment. Today, with the recent introduction of European Norm (EN) standards for Personal Protective Equipment (PPE), the focus on equipment has become even more important, particularly in relation to halting a falling climber. Since that fateful day more than 130 years ago, mountaineering, rock climbing and other related sports have developed into widespread and popular activities, the degrees of physical and technical difficulty increasing apace. The development of specialised equipment during this time has aided this expansion, enabling climbing to become harder, longer and safer. The rudimentary equipment employed in the early years of the sport, has now been replaced by the sophisticated array of equipment used today, with a multi-million dollar industry now concerned with the improvement and innovation of designs and materials. Development of Standards and Testing Climbing equipment has seen some of the greatest changes, including the development of standards and testing methods designed to produce performance criteria for components in such a way as to replicate extreme use. Owing to the nature of the activity such developments have reduced, but not eliminated, the inherent risk involved in climbing and mountaineering, and the conflicting requirements on equipment such as strength, weight and ‘nonstandard’ loading have made the composition of such standards problematic. Rope From the earliest days of climbing the primary piece of equipment required to halt a falling climber has been the rope. Originally produced from natural fibres such as hemp or manila twisted and ‘hawser laid’, the introduction of the synthetic fibre nylon, by DuPont during World War Two, marked a great step forward in providing a rope that gave a safe means of fall arrest. With the innovation of the ‘Kernmantel’ construction, (figure 1), in 1951 the modern climbing rope was born. 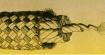 | Figure 1. Kernmantel rope construction | Requirements A rope suitable for breaking a climbers fall in such an environment requires some distinct mechanical and material properties if fatal consequences are to be avoided. A rope must both withstand the dynamic force of a falling body without breaking, and must do so without exerting an unacceptably high force on the body. Peak Force In the 1950s a good model illustrating the load generated by a falling climber was first produced. By considering the energy of a falling body and its absorption in elastic strain, an expression for the ‘peak force’ (Pmax) generated during a fall can be derived: 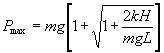 where : m = mass of falling climber k = rope stiffness (=Young’s modulus x rope cross-sectional area) H = height of fall L = length of rope The static force of the climber's weight is mg, therefore the rest of the expression can be considered as a magnification factor owing to dynamic loading. Here the critical factors are the rope stiffness and the ratio between rope length and fall height - known as the ‘fall factor’. It also shows that even the smallest fall will result in a minimum dynamic load at least twice the static load. In the case of a falling body, military parachute experiments into the impact forces generated during canopy opening have indicated that the body can withstand a maximum load of 12kN without serious injury. Using the maximum fall factor produced in an extreme fall, i.e. the fall factor equals two, a `safe' maximum rope stiffness (kmax) can be derived, bearing in mind that minimum percentage elongation is also desirable. Figure 2 shows the comparison between various rope materials and the loading generated at various fall factors. As illustrated, the kernmantel rope provides a significant improvement in comparison to earlier ropes. 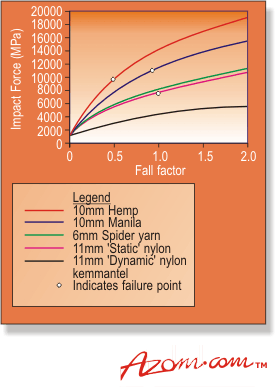 | Figure 2. Impact force versus fall factor for a variety of rope yarns. | Modern Rope Construction A modern dynamic climbing rope is made from continuous-drawn nylon yarns. A consequence of drawing the nylon is strengthening and stiffening as the molecular chains of this semi-crystalline polymer become orientated. These fibres can be spun to create high strength, low stretch ‘static’ rope, which is widely used in caving and industrial rope access where shock loading is unlikely and percentage elongation is required to be at a minimum. In addition these yarns can be woven to produce webbing, which is used for harnesses and anchor slings. More recently the use of stronger fibres such as Dyneema, a yarn made of a mixture of nylon and polyethylene fibres, has given significant weight savings, though its often small percentage elongation has made it poor in absorbing energy from dynamic loading. Producing Desired Properties To create a yarn with elastic properties suitable for arresting a fall safely, the drawn nylon is heat treated up to 120°C. Loss of chain orientation and strain-induced crystallinity as a result of the annealing process, gives the drawn nylon yarn a reduced Young’s modulus. This process increases the energy absorption properties of the yarn and reduces the impact force on the body during a fall. Testing Standards The EN892 standard specifies the drop test requirements a rope should withstand before it is approved for sale in Europe. The test requires the rope to be held statically and passed over a l0mm diameter edge, 300mm from the anchor. The falling mass is dropped to give a fall factor of 1.78. The standard requires the drop test to be repeated five times - the impact force on the first drop must not exceed 12kN for a single rope (10-llmm) and UN for a half rope (8-9mm). In addition, other factors such as knottability, sheath slippage and static elongation are measured and have minimum requirements. Even with the development of improved rope constructions and materials, due to the very nature of climbing, rope degradation from abrasion, cutting or friction melting poses a significant threat, and future development may improve the performance in these areas, figure 3. Reducing weight is also where future innovation may lie. For example, a comparison between nylon yarn and a spider’s drag line, shows that improvements in strength and energy absorption properties are possible, figure 2. 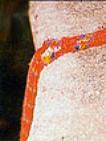 | Figure 3. Kernmantel rope abraded on a stone edge. | Materials for Climbing Equipment Mechanical Properties There are a number of important properties that materials used to make climbing hardware must exhibit. Apart from having a good strength to weight ratio, good hardness and fracture toughness characteristics are required. This is as a result of use in an environment in which abrasion and impacts are common and surface defects in highly stressed components are likely to occur. Therefore, materials with good resistance to impacts, as well as high fracture propagation resistance are preferable. For these reasons, developments in high-strength reinforced plastics have not been used in the climbing industry, although there could be advantages in using materials such as reinforced PEEK for specific applications. Corrosion Resistance Corrosion resistance is also an important requirement, particularly for equipment such as pegs or bolts left ‘in-situ’ at popular climbing areas. Rapid environmental degradation in high chloride environments such as sea cliffs can make equipment extremely dangerous, and the failure of such components is relatively common. Summary Great advances have been made in materials and designs over the past 100 years, but the quest for stronger, lighter and innovative designs continues. Advances in computer aided design (CAD) and finite element methods have only recently been applied to mountaineering equipment and provide an exciting opportunity for the designer. Similarly, future advances in polymers and composites will inevitably provide further improvements in both the performances of current products and lead to the development of new equipment for the sport |