H.C. Starck Solutions has years of experience in producing premium, high performance materials that provide suitable solutions to challenging applications in the electronics industry. The company’s advanced materials and technologies create value-added solutions for thermal management applications.
Custom-Engineered Thermal Management Materials
The Fabricated Products Group of H.C. Starck Solutions develops custom-engineered thermal management materials, which are widely employed in the electronics industry. H.C. Starck Solutions' engineered composite materials, tungsten and molybdenum materials, and laminates are customized for these applications.
The company produces materials that have high thermal conductivity and low and controlled coefficient of thermal expansion. These thermal management properties help in dissipating the heat from high power density devices. The engineering staff at H.C. Starck Solutions are expert in designing highly engineered materials that meet the exact needs of each application.
Cu/Mo/Cu Laminates
Cu/Mo/Cu laminates developed by H.C. Starck Solutions have an adjustable coefficient of thermal expansion that can be correlated with a range of semiconductor substrates while simultaneously maintaining high thermal conductivity. These aspects make them a perfect choice for high power devices where significant heat is produced.
.jpg)
Figure 1. In-plane Coefficient of Thermal Expansion, ppm/K
Cu/Mo/Cu laminates also have moderate thermal conductivity and low thermal and electrical resistance. They are suitable for Si-based devices as well as for large area power devices with significant heat generation.
Thermal conductivity and the coefficient of thermal expansion-mismatch of a given die are some of the key parameters involved in selecting a heat spreader material. These two parameters can be calculated by introducing a Thermal Compatibility Factor for a given heat spreader material in a simple equation: ? (Heat Spreader) / A CTE (Die - Heat Spreader). The ensuing ratio may be utilized to assess the compatibility of a heat spreader material with a given die. A high compatibility factor results from a low coefficient of thermal expansion-mismatch and a high thermal conductivity value.
Innovative Research and Development
H.C. Starck Solutions is dedicated to innovation and research and has high-tech laboratories to innovate, improve, and refine its materials and products. The company’s research and development programs are shaped through a continuous feedback from customers. H.C. Starck strives to develop innovative products to advance the thermal management industry.
The company produces thermal management components for HB-LEDs and laser diodes, such as Cu/Mo/Cu laminates, Mo-Cu composites, and plated molybdenum and tungsten flat products. By increasing the thermal conductivity of the heat dissipating components, the efficiency and reliability of semiconductor devices can be enhanced while matching their coefficients of thermal expansion to semiconductor substrates.
Finite element modeling is used as a computational tool by H.C. Starck Solutions to design custom-made products for unique applications that demand effective heat removal under severe conditions. With high-tech modeling capability, H.C. Starck Solutions address customers’ needs by optimizing its present products or designing new products in a timely manner.
.jpg)
Figure 2. Single device on Cu I Mo I Cu base plate
.jpg)
Figure 3. Four devices tightly placed on Cu / Mo / Cu base plate
Value-Added Solutions for Thermal Management Products
Technological advancements require materials with characteristics that cannot be achieved as a monolithic system. To this end, H.C. Starck Solutions applies different engineering techniques to develop a range of products by combining different types of materials.
These materials have special properties that are suitable for a wide range of applications such as power semiconductors, power controls for hybrid vehicles, HB LEDs, automotive headlamps, and electronic packaging.
Tungsten and Molybdenum Discs and Squares
Tungsten and molybdenum discs and squares are utilized as contact materials in thyristors, transistors, and silicon controlled rectifier diodes. These materials have moderate thermal conductivity and similar coefficients of thermal expansion to silicon, and thus prove ideal for large area power devices where significant amount of heat is produced.
Laminate Products
H.C. Starck Solutions has developed two clad material systems, wherein molybdenum has been used as the main constituent of the laminate. The main benefits of these systems are high mechanical rigidity, good thermal conductivity, suitable Coefficient of Thermal Expansion, and excellent adhesion and corrosion resistance properties. These laminate products have been approved for aerospace and military applications.
.jpg)
Figure 4. Copper / molybdenum / copper laminates
Composite Products
Technological advancements in high power equipment have placed significant demands on the packaging materials. H.C. Starck Solutions manufactures molybdenum and metal-metal matrix composites that tend to reduce stress in the package and allows the electronics to function in the preferred manner.
Electroplating
H.C. Starck Solutions’ electroplating capabilities add value to its thermal management components. The company has electroplating facilities that deal in silver, gold, ruthenium, rhodium, electroless and electrolytic nickel coatings.
A number of techniques are available, including physical vapor deposition for barrel plating, single or double-sided coating. The company also offers specialty coatings for etch-resistance, solder-wetting, electrical contacts, and protective layers.
Conclusion
This technical brief clearly demonstrates the benefits of refractory metal-based products that provide value-added solutions for thermal management applications.
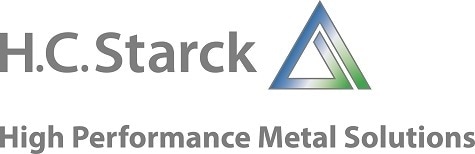
This information has been sourced, reviewed and adapted from materials provided by H.C. Starck Solutions.
For more information on this source, please visit H.C. Starck Solutions.