Powder coatings, substances that are decorative, protective, or both, are developed by applying a coating powder to a substrate and then fusing the coating into a continuous film by applying heat or radiant energy. Coating powders are finely divided organic polymer particles that generally contain additives, fillers, and pigments which remain finely divided during storage under appropriate conditions.
Contrary to liquid coatings that may contain volatile organic solvents, powder coatings can obtain the similar or better characteristics of quality, corrosion resistance, and durability. Powder coatings have reduced production costs compared to liquid coatings, because this process is highly efficient and requires less labor and energy. Since powder coatings have no volatile organic solvents, they reduce waste disposal and eliminate organic solvent emissions.
A wide range of factors affect the performance of a powder coating. Powder particle size can have a significant impact on several properties, including handling, charging, delivery, and coating characteristics. The powder coating formulations may differ depending on application requirements of object shape, thickness, and ambient conditions.
The Process
The powder coating process starts with application of a charge to an object's surface, usually by an electrical ground. At first, the powder coating is given a charge that is opposite to the charge applied to the object, and then the powder is directed toward the object in an air stream under pressure. When the powder particle comes closer to the charged object, electrostatic attraction controls and attaches the powder to the item. Initial handling, recovery, and recycling of the powder can increase fines, which can deposit in pumps or nozzles during normal processing. These deposits can cause uneven delivery under application pressure, resulting in uneven or blotchy films. Production and deposition of fines, caused by particle attrition due to high pressure in the process, can cause the process to shut down completely.
Since fines can be charged more efficiently, the overall charge profile of the powder can also be affected by the amount of fines. When there are no sufficient fines, wraparound can be reduced because fines can be easily influenced by an electrostatic field. Coarse particles have greater mass, and hence they have a lower charge/mass ratio. This reduces the efficiency while tracing the electrical field around the object, resulting in incomplete or marginal coating. The fines have high charge/mass ratio. This can result in a thinner film thickness because the buildup of coating is limited to the electrical field, which reduces as the thickness of the film increases.
The Problem
Particle size strongly influences film thickness because fines generate thin initial powder coats and coarse particles generate thick initial powder coats. Hence, the heated coats melt at different rates and reduce the final coating smoothness. This phenomenon is commonly known as "orange peel" in the coatings industry. Orange peel can also be linked to the electrostatic process or rheological factors of the powder that are highly dependent upon particle size.
The Solution
It is very clear that the importance of particle size to powder processing must not be underestimated. Microtrac MRB particle size analyzers are capable of measuring powder coatings in the dry state. Normally, the powder coatings are smaller than 250 µm, or 60 mesh, U.S. The SRA150 or SRA200 analyzer can be employed, depending on the overall particle size requirements. The SRA150 analyzer is able to measure particles as small as 0.7 µm, and it can be employed in applications where fines smaller than 4 µm are necessary. The advantage of dry measurement of the coatings is the ability to use the material as a dry powder. However, low-energy dry-dispersion systems should be used in order to avoid biasing the reported particle size to fine sizes. This could result in inadvertent milling changes or recycling of the recovered powder.
As shown below, the data for a powder coating can be depicted graphically or numerically. In order to enhance the capability of laser diffraction measurement, the data may be stored in the computer for later recovery. The data is stored in true dBasecompatible format instead of cumbersome text files, which are used by many other particle size analyzers. This makes data recovery and data evaluation processes significantly easier.
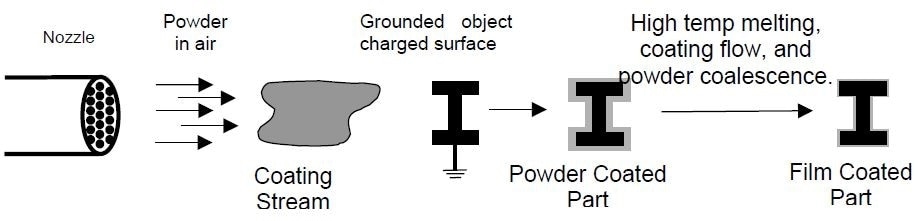
In addition to easy data recovery, operators can also perform more advanced data analysis using standard programs, such as Microsoft Excel, FoxPro, dBase, or Lotus 1-2-3.
Microtrac MRB particle analyzers use a proprietary algorithm that enables direct conversion of scattered light into a volume distribution. The patented silicon detector array, developed by Honeywell and specifically employed in Microtrac MRB analyzers, makes the measurement fast, easy, and precise. Production carried out under ISO 9000 certification assures the unsurpassed consistency and quality of all components to customers. Microtrac MRB, with expert knowledge and more than two decades of laser diffraction experience in all facets of particle size, computer technology, and electronics, assures the best possible technical support to its customers.
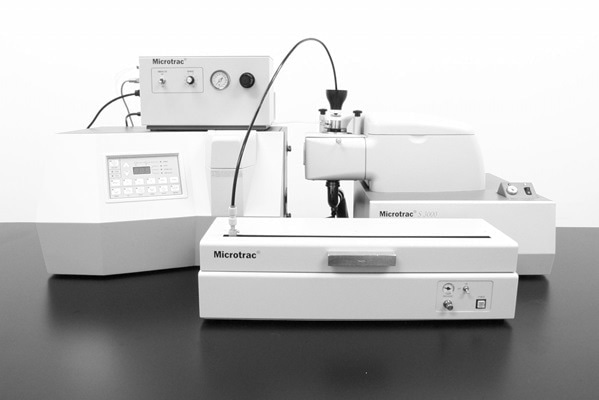
Microtrac MRB S3000 with Vibratory or Linear Dry Powder Feeder
Capabilities
- Full database management capability, which can be exported to all popular spreadsheets
- Measures multi-modal distributions without assumptions or curve fitting
- Portable and small
- Simplicity of operation
- Modular, convenient design
- Includes dry powder vibratory feeder for typical particle size distributions
- Optional linear dry feeder for broad particle size distributions

This information has been sourced, reviewed and adapted from materials provided by Microtrac MRB.
For more information on this source, please visit Microtrac MRB.