Residues and particulates are main types of contamination found in the pharmaceutical sector.
These may be produced from a broad range of sources including undissolved residuals in buffer and media solutions, packaging and a variety of system components such as seals and gaskets. Contamination can also occur due to side reactions related to the manufacture of the product, including detergent residues and charred products or from degradation or maintenance of the processing equipment such as lubricant oils, metal corrosion or scoring of Teflon gaskets. Particulates have been noticed to contain a broad range of materials including glass, aluminum, plastics, rubber and wood-based products.
Particulates can spread to the nearby air volume of a clean room by transport attached to people or containers or through airborne contamination. This can then cause contamination of both the manufacturing area and the products. These particles, if carried over to the final drug product, can have negative effects such as blockages of blood vessels, impairment of microcirculation, damage to various organs, phlebitis etc. The FDA stipulates documentation and investigation of unanticipated particles or adulterated drugs1, and has held companies responsible for failing to perform satisfactory investigations for violations involving particle contamination2.
Identifying and understanding the source of particulates is critical to controlling their spread. Once the source is established, then elimination of the particulate contamination becomes considerably simpler. Incidentally, FTIR-microscopy and SEM-EDX are robust tools for identifying particles, as well as giving information about size, shape and surface topography. The following analyzes were done using a FTIR-Microscope (Thermo Nicolet iN10 MX FTIR microscope) and a SEM-EDX (Tescan Vega S 3 LMU with EDAX Octane Plus EDX detector) to test the chemistry of a brown colored particle found in a steel bioreactor as well as a brown residue on the surface of the same steel reactor.
FTIR microscopy and SEM-EDX could identify the brown residue as iron oxide/iron hydroxide (rust). It was also able to establish that the brown particle was made up of a mixture of rust (iron oxide/hydroxide) and poly(tetrafluoroethylene) (PTFE, Teflon). By comparing the results of the brown residue and the brown particle, SEM-EDX and FTIR microscopy were able to reveal that particle source was consistent with degradation of the metal container. These methods were also able to reveal that the particle was chiefly composed of Teflon, which was correlated with the material specifications to a larger stirring apparatus composed of Teflon.
The article below provides the test results for samples described as:
1. Brown Residue
2. Brown Particle
The following tests were conducted:
1. Fourier Transform Infrared Spectroscopy Microscopy (FTIR-Micro)
2. Scanning Electron Microscopy with Energy Dispersive X-Ray Spectroscopy (SEM/EDX)
Objective
The reason behind this analysis was to detect a brown particle which was found in a bioreactor. A brown residue was also noticed in the reactor and it was desired to determine if the particle was chemically related to the residue.
Summary of Results
The results of FTIR-Micro and SEM-EDX for Brown Residue and Brown Particle are summarized in Table 1. It was discovered that Brown Residue (illustrated in Figure 1) was consistent with iron oxide/hydroxide (rust). Brown Particle (illustrated in Figure 1) was discovered to have an FTIR spectrum most consistent with a chemical composition of poly(tetrafluoroethylene) (PTFE) and iron oxide. FTIR and SEM-EDX maps attained of the Brown Particle match particles of iron oxide embedded in a PTFE fragment. The chemical composition of the brown particle was discovered to correlate with the material specifications of a larger stirring apparatus composed of PTFE.
Table 1. Particle Identifications.
Sample Name |
FTIR Best Match |
SEM major Elements |
Brown Residue |
Iron oxide/hydroxide |
Fe, O, Ni |
Brown Particle |
Iron oxide,/hydroxide PTFE |
F, Fe, C, O |
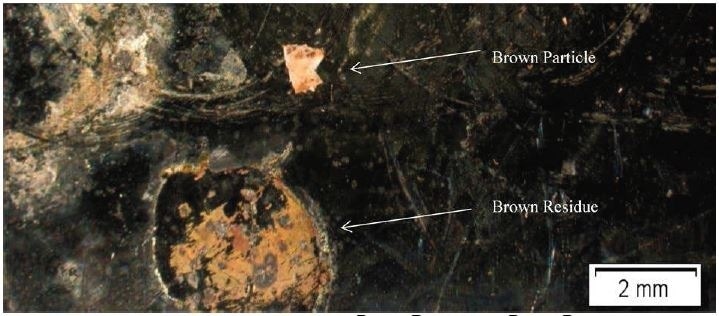
Figure 1. Optical Micrograph of Brown Particle and Brown Residue.
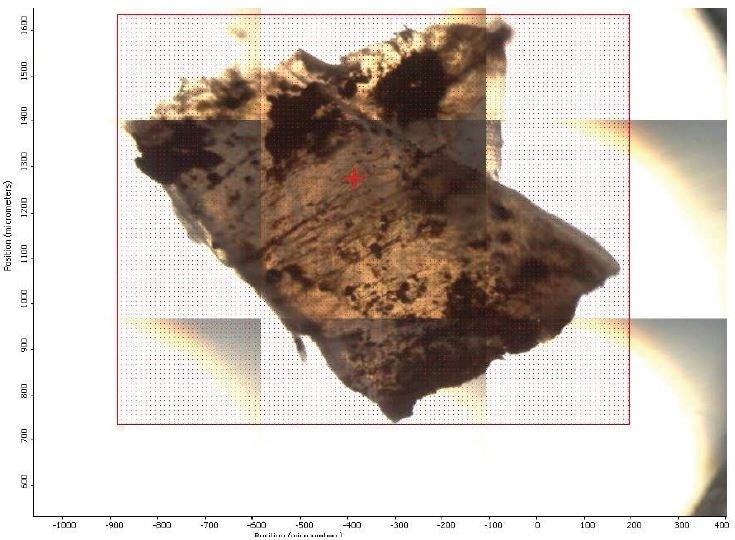
Figure 2. FTIR micrograph of mapped area.
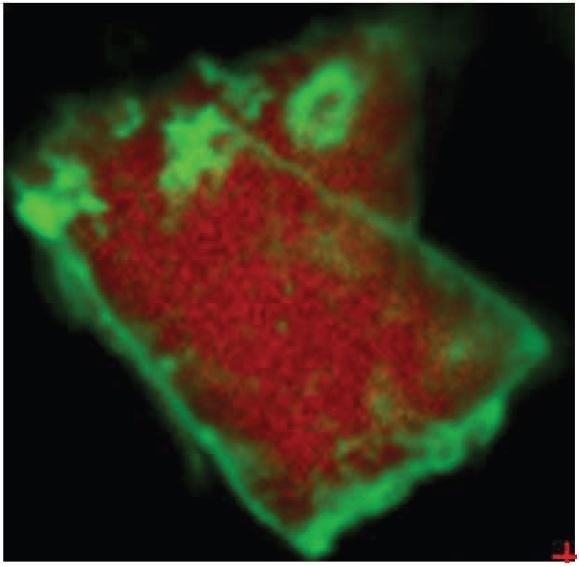
Figure 3. Overlay of iron oxide absorbances (green) and PTFE absorbances (red).
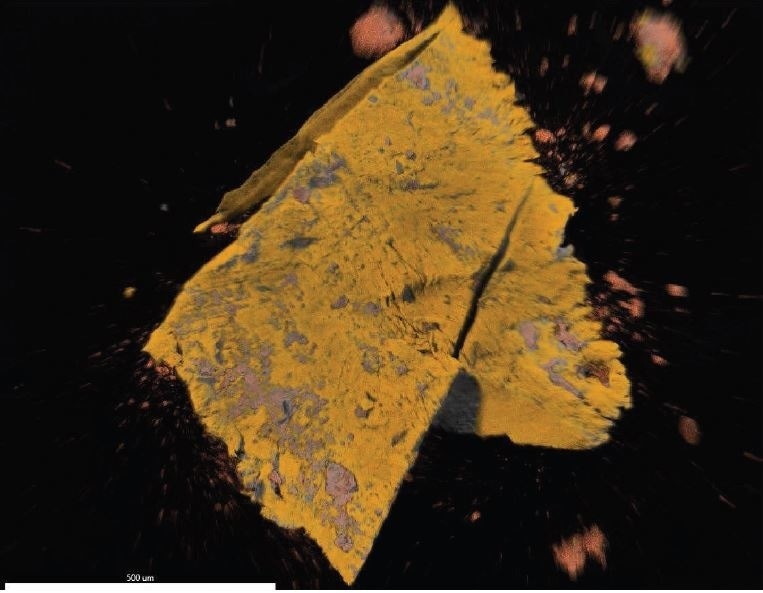
Figure 4. EDX map overlay of Fluorine (yellow, correlates with PTFE) and Iron (reddishorange, correlates with iron oxide).
Please click here if you would like more information on the product in this article or a quote
Individual Test Results
A summary of the individual test results is given below. All additional data, including spectra, have been included in the data section of this article.
Brown Residue
FTIR-Microscopy
Brown Residue was received as a brown stain on a metal surface as illustrated in Figure 1. A portion was removed and deposited on a sampling cell as illustrated in Figure 5.
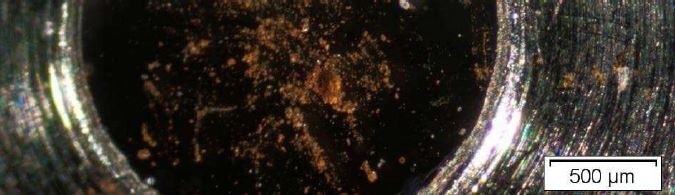
Figure 5. Optical Micrograph of Brown Residue on a sampling cell.
Results
It was discovered that Brown Residue was consistent with iron oxide/hydroxide. Specific absorbance assignments for Brown Residue are given in Table 2. Figure 6 shows an overlay of Brown Residue and iron oxide/hydroxide. This identification is additionally confirmed by the SEM-EDX.
Table 2. FTIR Peaks and Identifications of Brown Residue.
IR Frequency (cm-1) |
Possible Functional Group |
Possible Source |
3480 |
O-H stretch |
Iron Oxide/Hydroxide |
1541, 1427, 1345 |
Fe-O comb/overtone |
Iron Oxide/Hydroxide |
804 |
Fe-OH stretch |
Iron Oxide/Hydroxide |
~675 |
Fe-O stretch |
Iron Oxide/Hydroxide |
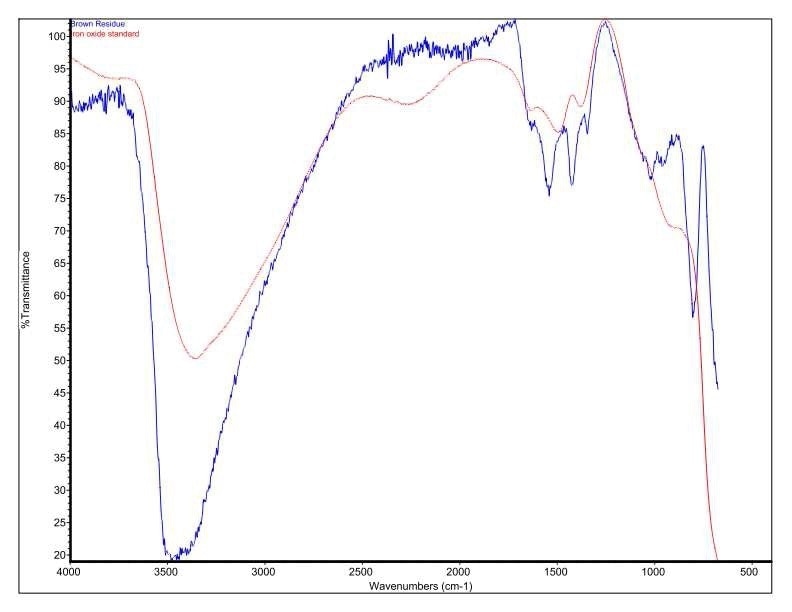
Figure 6. Overlay of Brown Residue and an iron oxide/hydroxide standard.
SEM-EDX
Brown Residue was tested by SEM-EDX at one sampling location and a control location. Figures 7-8 illustrate the SEM-EDX images and the elemental composition of each sampling location is summarized in Tables 3-4. Figure 9 illustrates the secondary electron (SE) and backscattered electron (BSE) images of the sample. Brown Residue revealed the presence of O, Fe, and Ni. This is in keeping with the FTIR identification of iron oxide/hydroxide. The occurrence of Ni indicates that the reactor composition is consistent with steel.
Table 3. Elemental concentration at area 1 (control) on Brown Residue.
Element |
Atomic Number |
Series |
Weight % |
Mole % |
% Error |
Carbon |
6 |
K |
79.06 |
83.41 |
6.28 |
Oxygen |
8 |
K |
20.94 |
16.59 |
23.72 |
Table 4. Elemental concentration at area 6 on Brown Residue.
Element |
Atomic Number |
Series |
Weight % |
Mole % |
% Error |
Carbon |
6 |
K |
17.62 |
33.42 |
15.62 |
Oxygen |
8 |
K |
32.11 |
45.72 |
15.43 |
Nickel |
28 |
L |
9.29 |
3.60 |
19.13 |
Sodium |
11 |
K |
0.27 |
0.27 |
42.12 |
Aluminum |
13 |
K |
0.26 |
0.22 |
25.74 |
Chlorine |
17 |
K |
1.13 |
0.73 |
12.12 |
Iron |
26 |
K |
39.31 |
16.04 |
4.26 |
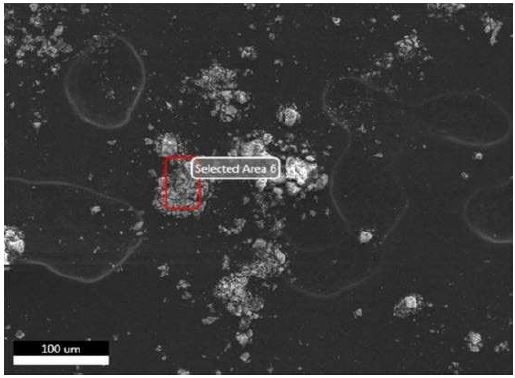
Figure 7. SEM-EDX image of all sampling locations analyzed of Brown Residue.
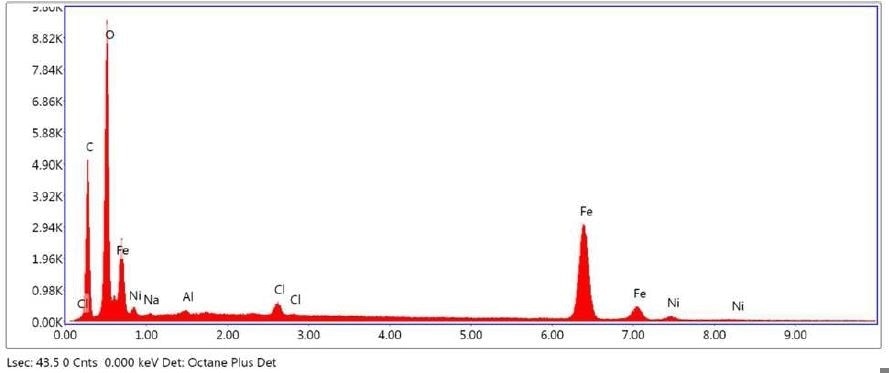
Figure 8. SEM-EDX elemental abundance of area 6 analyzed of Brown Residue.
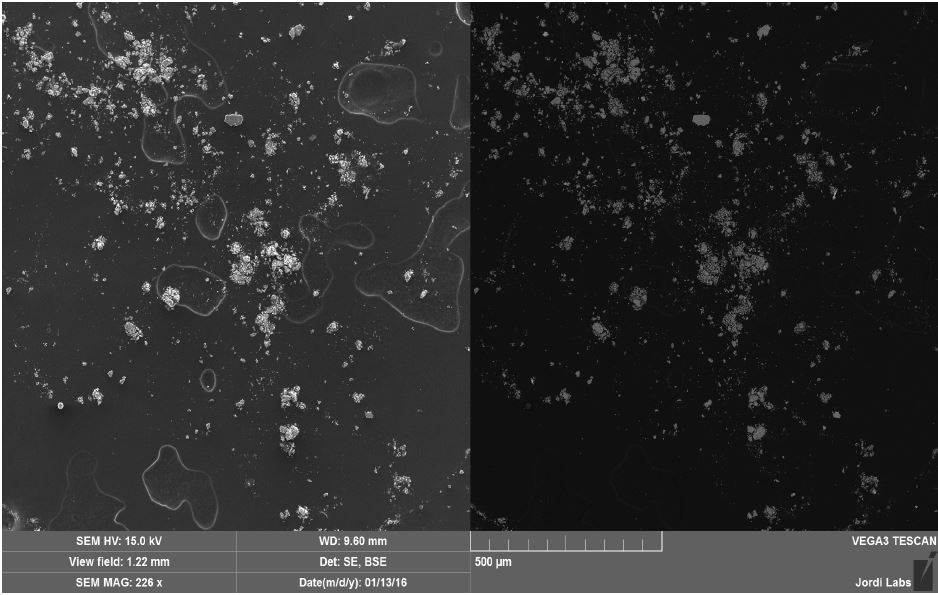
Figure 9. SEM SE (left) and BSE (right) images of Brown Residue.
Brown Particle
FTIR-Microscopy
Brown Particle was received as a white and brown particle on a metal surface as illustrated in Figure 1. The particle was then deposited on a sample cell as illustrated in Figure 10.
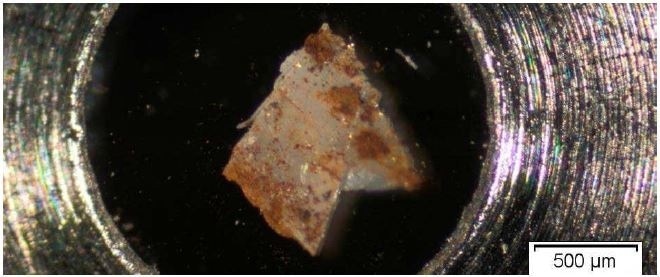
Figure 10. Optical Micrograph of Brown Particle on a sample cell.
Results
It was discovered that Brown Particle was in keeping with a mixture of PTFE and iron oxide. Specific absorbance assignments for Brown Particle are given in Table 2. An overlay of the FTIR spectrum of the Brown Particle in the Brown area, the Brown Particle in the White Area and the Brown Residue can be viewed in Figure 11. An overlay of the FTIR spectrum of the Brown Particle in the Brown area, the Brown Particle in the White Area and PTFE can be viewed in Figure 12.
It was also observed that the brown areas showed stronger absorbances consistent with the spectrum from brown residue, while the white areas were more consistent with PTFE. An area map was obtained to show the distribution of iron oxide and PTFE in the Brown Particle. Figures 13-14 illustrate the resulting iron oxide and PTFE heat maps, which suggest Brown Particle is in keeping with iron oxide embedded in a PTFE matrix.
Table 5. FTIR Peaks and Identifications of Brown Particle
IR Frequency (cm-1) |
Possible Functional Group |
Possible Source |
Brown Residue
(shown in Table 2) |
Brown Particle
Brown area |
Brown Particle
White area |
3480 |
3371 |
N/O |
O-H stretch |
Brown Residue |
1541, 1427, 1345 |
1557, 1426 |
1550, 1448 |
Fe-O comb/overtone |
Brown Residue |
N/O |
1275-1150 |
1275-1150 |
C-F stretch |
PTFE |
804 |
781 |
776 |
Fe-OH stretch |
Brown Residue |
~675 |
~675 |
720 |
Fe-O stretch |
Brown Residue |
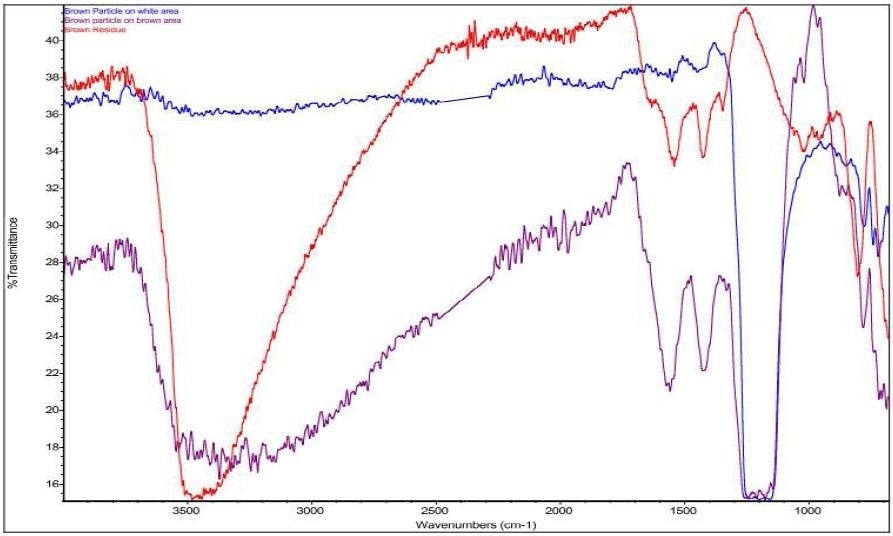
Figure 11. Overlay of Brown Particle on white area (blue), Brown Particle on brown area (purple), and Brown Residue (red).
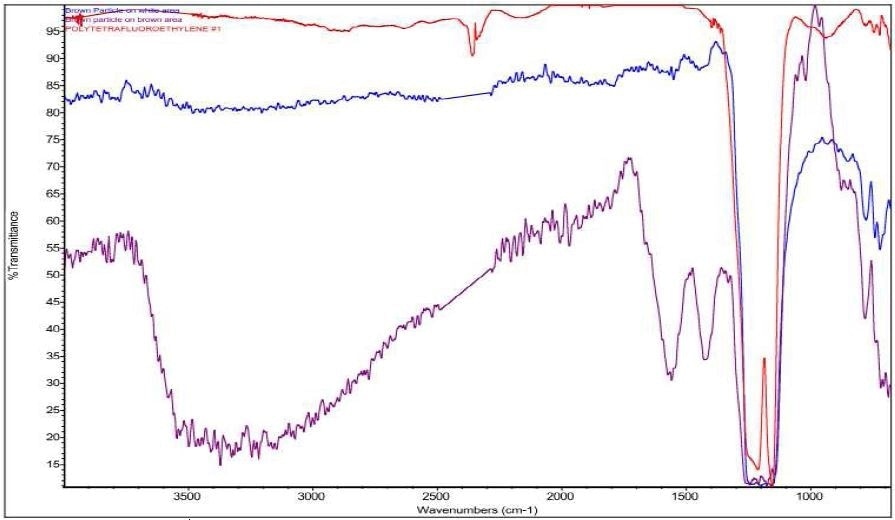
Figure 12. Overlay of Brown Particle on white area (blue), Brown Particle on brown area (purple), and PTFE (red).
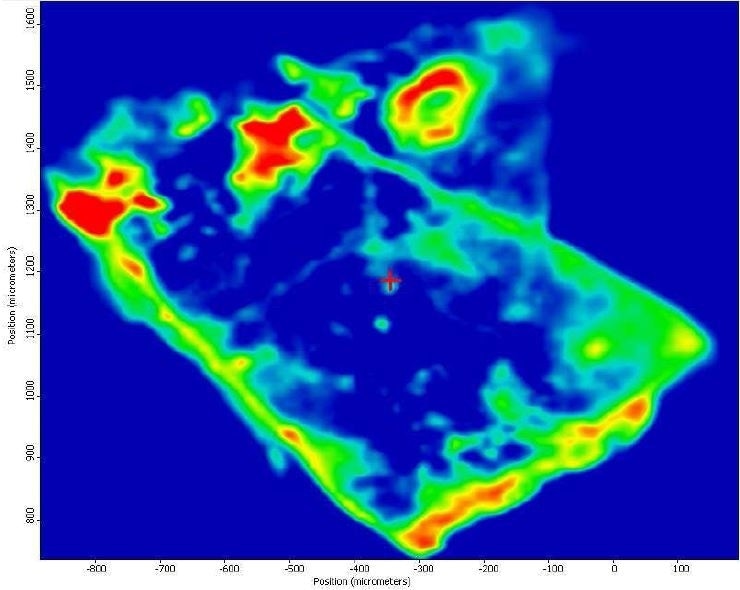
Figure 13. FTIR heat map of iron oxide absorbances (red is a strong absorbance, blue is weak).
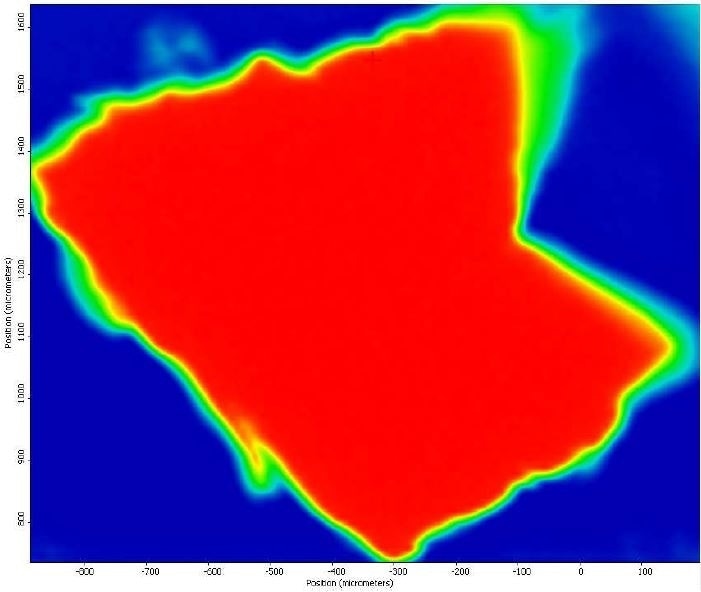
Figure 14. FTIR heat map of PTFE absorbances (red is a strong absorbance, blue is weak).
SEM-EDX
Brown Particle was tested by SEM-EDX at a control location and two sampling locations. A spectrum was taken over a large area to establish the general chemistry of the sample, and a smaller area was obtained on a brown portion. Figure 15 illustrates the secondary electron (SE) and backscattered electron (BSE) images of the sample. It was also noticed that one of the bright areas has moved off the particle after the attainment of an area map as illustrated in Figure 16. This shows that one of the bright particles (observed by FTIR to be iron oxide/hydroxide) was not embedded, but instead resting on the surface, and was forced off by electrostatic repulsion when exposed to a strong electron beam. Furthermore, an EDX map was obtained. Individual elemental maps can be viewed in Figure 19-Figure 22. Figures 23-26 illustrate the SEM-EDX images and the elemental composition of each sampling location is tabulated in Tables 6-8. It was noticed that greater concentrations of F are localized where Fe is not seen as well as the inverse as illustrated in Figure 17. When this relationship is compared with the acquired FTIR map, it is can be seen the surface of the PTFE particle is embedded with iron oxide particles because FTIR tests the chemistry of the whole thickness of the sample, while SEM-EDX is a surface sensitive method. This is in relation to the results observed by FTIR microscopy. An overlay of oxygen and the iron distribution can also be viewed in Figure 18, and generally are seen in the same areas of the image signifying iron is present as iron oxide/hydroxide.
Table 6. Elemental concentration at area 1 (control) on Brown Particle.
Element |
Atomic Number |
Series |
Weight % |
Mole % |
% Error |
Carbon |
6 |
K |
74.66 |
79.69 |
7.60 |
Oxygen |
8 |
K |
25.34 |
20.31 |
22.40 |
Table 7. Elemental concentration at area 3 on Brown Particle.
Element |
Atomic Number |
Series |
Weight % |
Mole % |
% Error |
Carbon |
6 |
K |
8.63 |
14.95 |
16.04 |
Oxygen |
8 |
K |
41.67 |
54.23 |
15.39 |
Fluorine |
9 |
K |
15.76 |
17.27 |
15.65 |
Sodium |
11 |
K |
1.40 |
1.27 |
7.68 |
Aluminium |
13 |
K |
0.14 |
0.11 |
34.83 |
Silicon |
14 |
K |
0.16 |
0.12 |
30.85 |
Sulfur |
16 |
K |
0.16 |
0.10 |
34.22 |
Chlorine |
17 |
K |
0.38 |
0.22 |
19.00 |
Iron |
26 |
K |
26.30 |
9.81 |
5.56 |
Nickel |
28 |
K |
5.40 |
1.92 |
11.52 |
Table 8. Elemental concentration at area 3 on Brown Particle.
Element |
Atomic Number |
Series |
Weight % |
Mole % |
% Error |
Carbon |
6 |
K |
24.06 |
35.02 |
23.86 |
Oxygen |
8 |
K |
18.59 |
20.32 |
25.75 |
Fluorine |
9 |
K |
44.06 |
40.55 |
16.94 |
Nickel |
28 |
L |
11.46 |
3.41 |
13.05 |
Aluminium |
13 |
K |
0.38 |
0.24 |
14.05 |
Iron |
26 |
K |
1.45 |
0.45 |
23.69 |
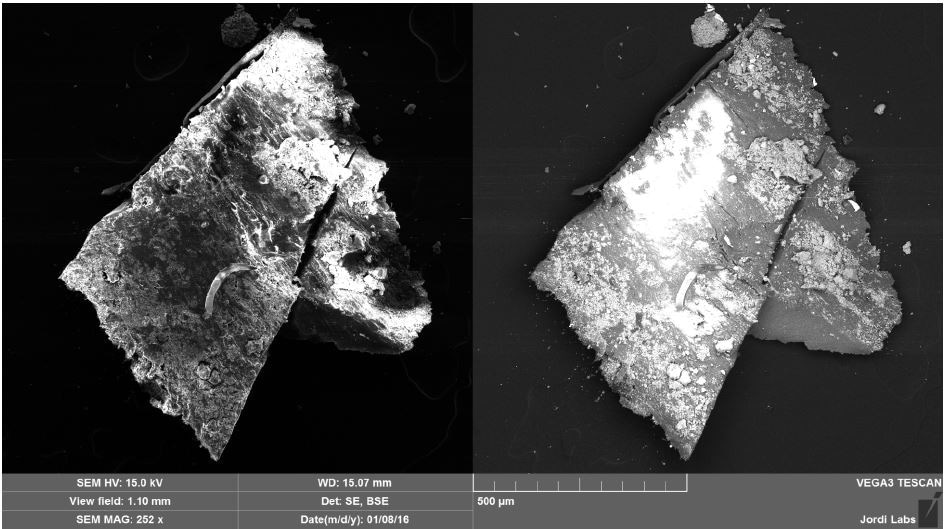
Figure 15. SEM SE (left) and BSE (right) images of Brown Particle before mapping.
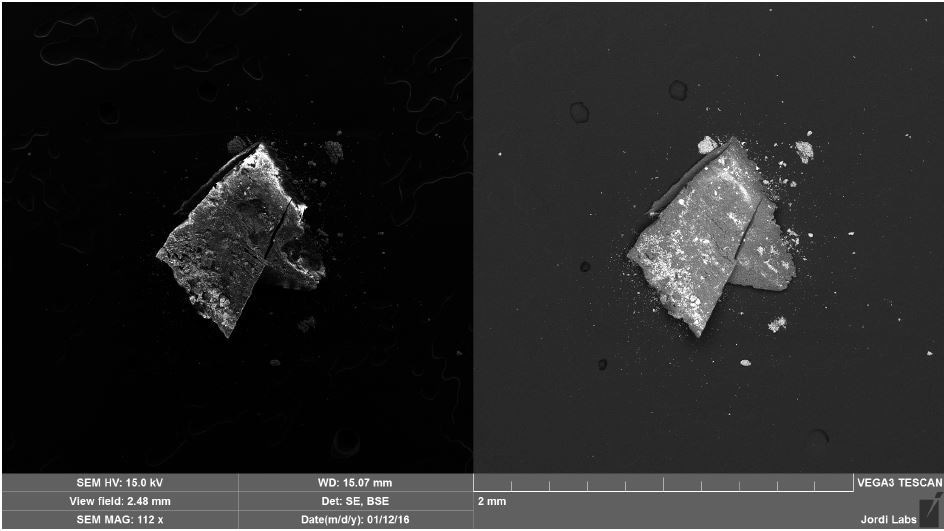
Figure 16. SEM SE (left) and BSE (right) images of Brown Particle after mapping.
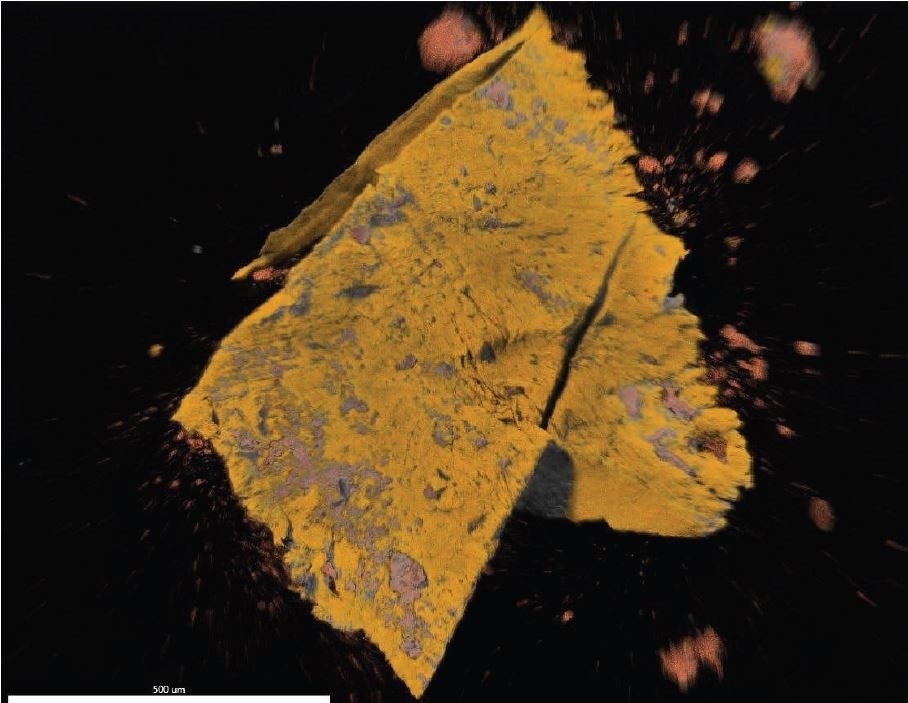
Figure 17. EDX map overlay of Fluorine (yellow) and Iron (reddish-orange).
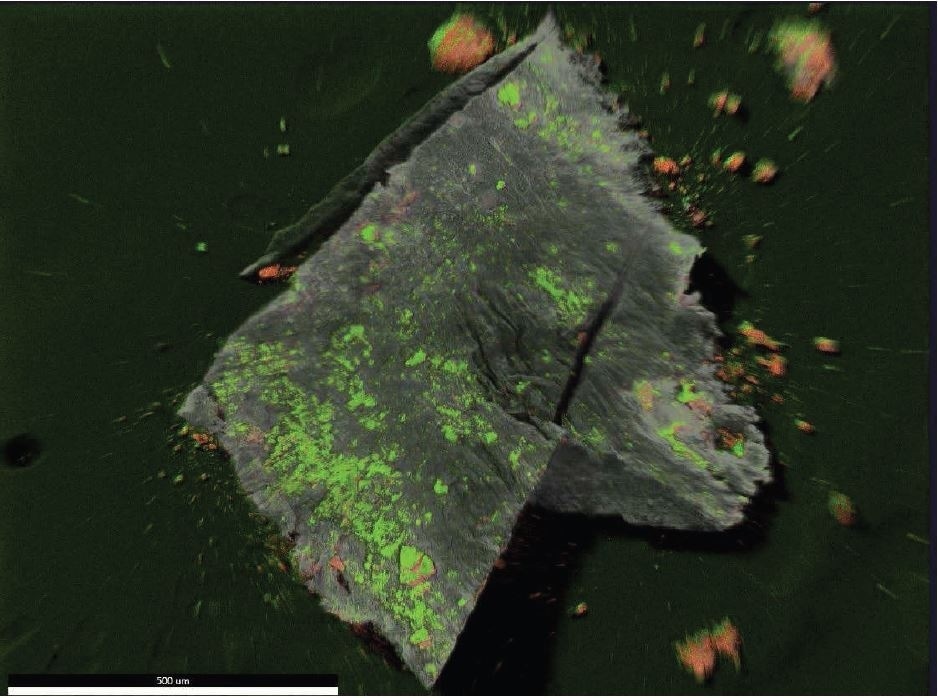
Figure 18. EDX map overlay of Oxygen (green) and Iron (reddish-orange).
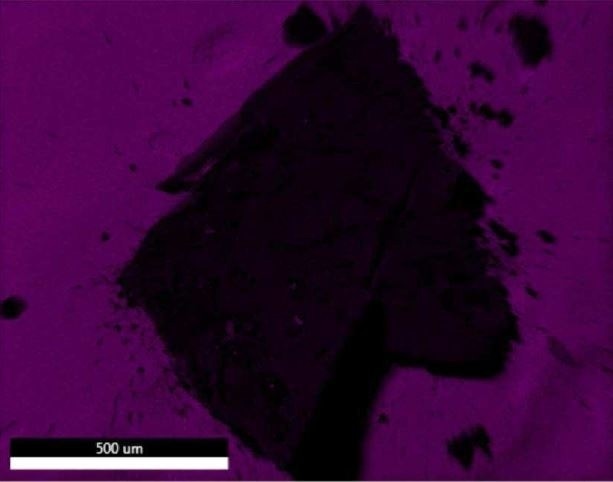
Figure 19. EDX map of Carbon.
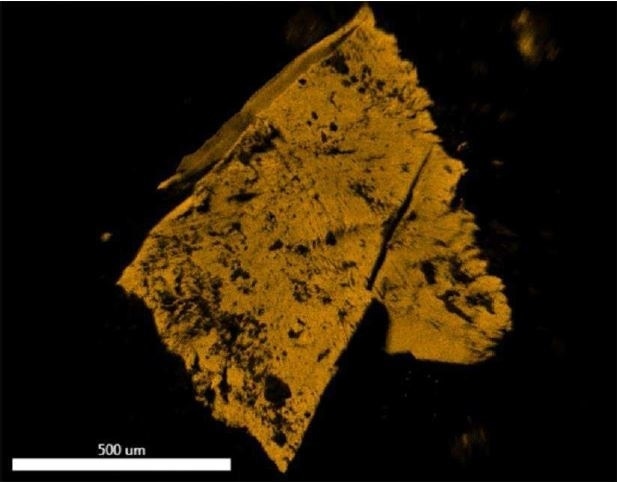
Figure 20. EDX map of Fluorine.
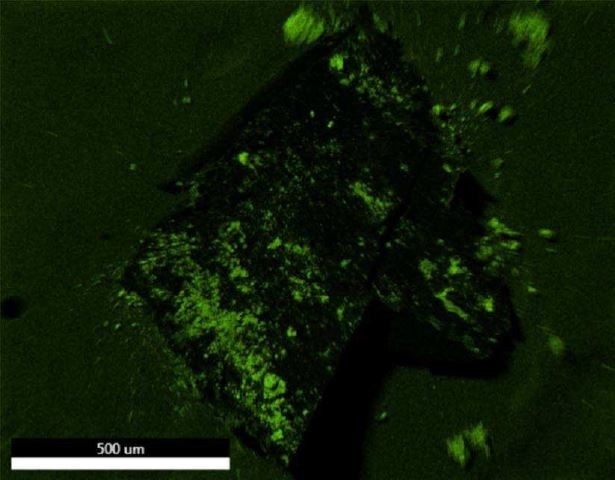
Figure 21. EDX map of Oxygen.
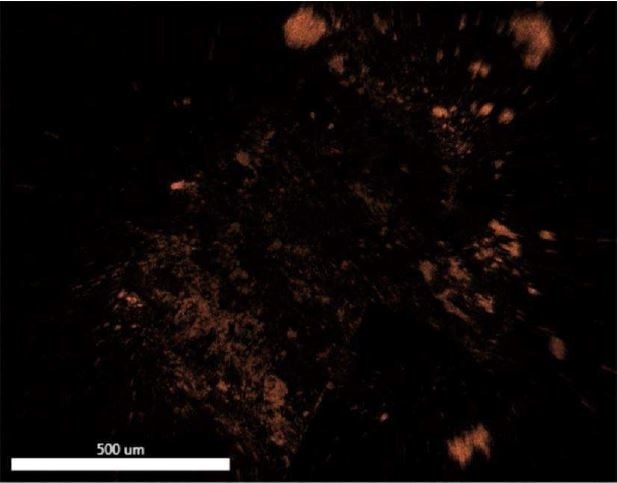
Figure 22. EDX map of Iron.
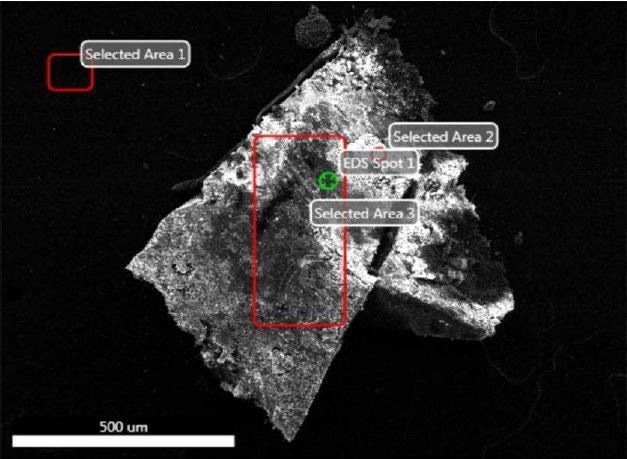
Figure 23. SEM-EDX image of all sampling locations analyzed of Brown Particle.
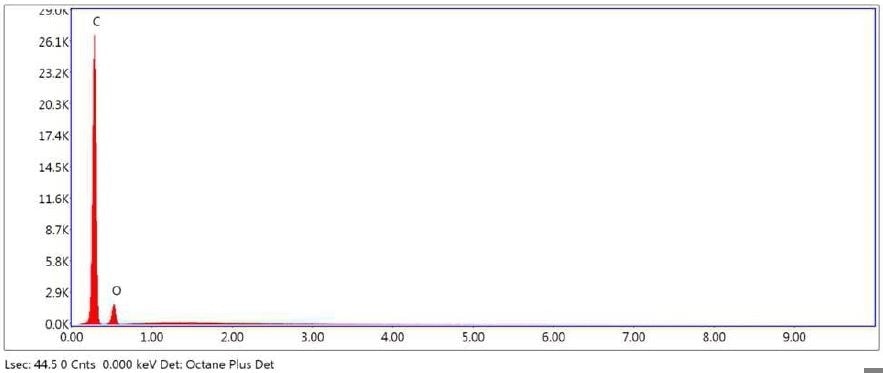
Figure 24. SEM-EDX elemental abundance of area 1 (control) analyzed of Brown Particle.
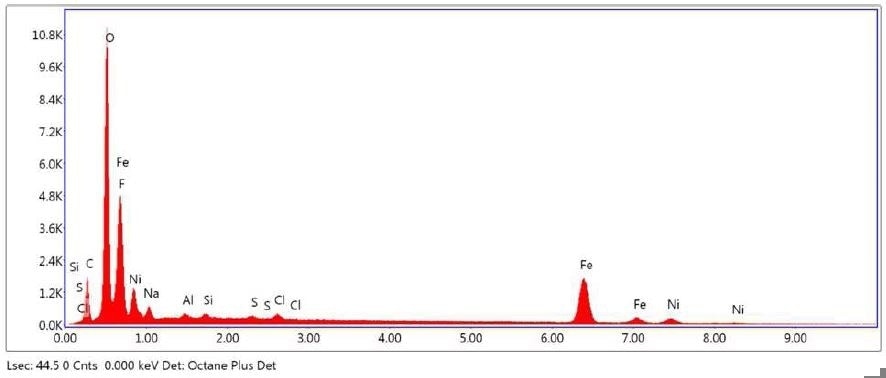
Figure 25. SEM-EDX elemental abundance of area 2 analyzed of Brown Particle.
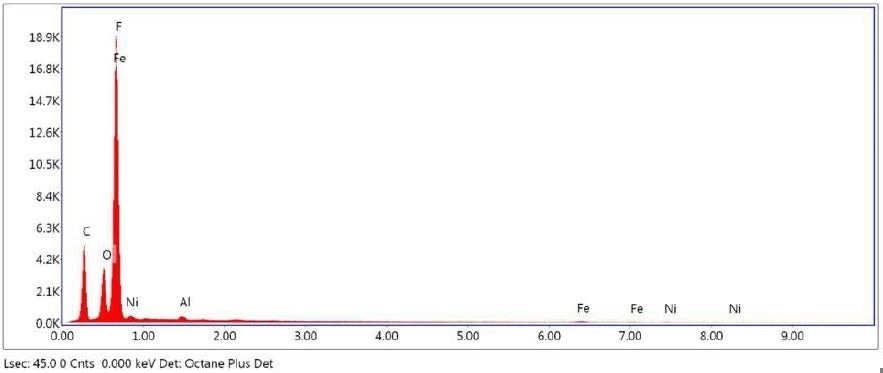
Figure 26. SEM-EDX elemental abundance of area 3 analyzed of Brown Particle.
Analysis Conditions
The Jordi report provides information on the techniques used including instrument type, solvents, sample preparation, temperatures, etc. The specific conditions have been removed for this case study.
References
1 FDA Regulation 21 CFR 211 Subpart E
2 FDA fines drug manufacturer $500 million for violations including insufficient investigation of rejected lots http://www.fda.gov/Drugs/GuidanceComplianceRegulatoryInformation/EnforcementActivitiesbyFDA/ucm118411.htm
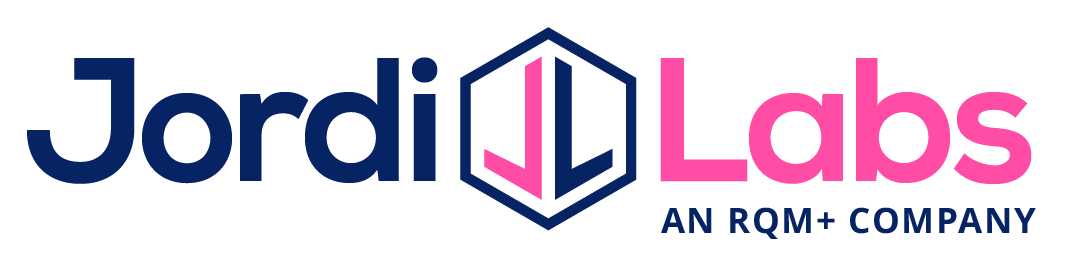
This information has been sourced, reviewed and adapted from materials provided by Jordi Labs.
For more information on this source, please visit Jordi Labs.