Quality control of raw materials as well as of intermediate and finished products is all part of the production process of high-quality cement. Samples are taken, processed and analyzed at each production stage to determine the material’s chemical composition.
A useful addition to XRF analyzers is the fast, reliable, and accurate determination of sulfur and carbon using elemental analyzers based on combustion technology. Except for size reduction, no additional sample preparation is required for inspecting a sample with an elemental analyzer. Contrary to XRF analysis, the element content of sulfur and carbon can be determined from as low as ppm range up to 100% and the results are typically acquired within one or two minutes when using combustion technology.
Elemental Analysis by Combustion
Based on the sample matrix (for example fuel or cement), a wide range of elemental analyzers is used to determine the sulfur and carbon content. Generally, elemental analyzers ignite the sample in an oxygen stream and determine the released gases such as SO2 and CO2 with infrared cells. Usually, inorganic samples that have low sulfur content and carbon content (like cement) are combusted in an induction furnace at temperatures as high as 2200 °C. First, a laboratory mill is used to reduce the particle size of samples like gypsum, cement clinker, lime, or raw mix down to 200 µm or less. Next, a small, representative sample of roughly 200 mg is taken and weighed into a ceramic crucible and this is followed by adding some accelerators (1 g of iron and tungsten) to the crucible.
It takes about 60 seconds for complete analysis of the carbon and sulfur content of the sample. Organic samples (e.g. fuels) have different combustion behavior, and hence they cannot be processed in an induction furnace. Fuels are generally used in the cement industry (coke, coal, secondary fuels) and contain a much higher carbon content than that of cement. They can only be determined with a resistance furnace at temperatures of approximately 1300 °C.
The particle size of a secondary fuel sample was reduced down to about 200 µm and this reduction can be easily achieved in an ultra centrifugal mill such as the ZM 200 from Retsch. Following this, 500 mg of representative sample can be directly examined without adding any accelerators. It takes less than two minutes to obtain the carbon and sulfur content. Also, it is the lab personnel that have to decide whether an elemental analyzer with resistance or induction is most appropriate to meet their needs.
Shown in Figure 1, ELTRA’s CS-2000 elemental analyzer is the only instrument in the market in which these two combustion techniques are integrated (Eltra Dual Furnace Technology) and hence, it can be used for different analytical applications in a cement plant.

Figure 1. ELTRA’s CS-2000 elemental analyzer allows for determination of C and S in both organic and inorganic samples.
Application Example Cement
Owing to the large production capacities of cement (hundreds of millions of tons) across the world, there is a need for reliable determination of sulfur and carbon for quality control purposes. For instance, a cement with excess sulfur content could be destroyed due to the chemical reaction of sulfuric acid. In the cement sector, the sulfur content is usually certified as SO3 content and the carbon content is given as CO2 content. The CS-2000’s software offers results in different notifications (C, CO2, S, SO3, and SO4).
In the induction furnace of the CS-2000 analyzer, approximately 10 cement samples (sample weight of about 200 mg) were inspected. The size was reduced to approximately 200 µm for sample preparation, and prior to each measurement approximately 1 g of iron and tungsten was added. It took about one minute to complete each measurement and the low standard deviation of the sulfur and carbon content indicates the performance of the ELTRA CS-2000 induction furnace:
Analytical values of 10 measurements of cement |
% CO2 |
6,01 +- 0,04 |
% SO3 |
2,61 +- 0,04 |
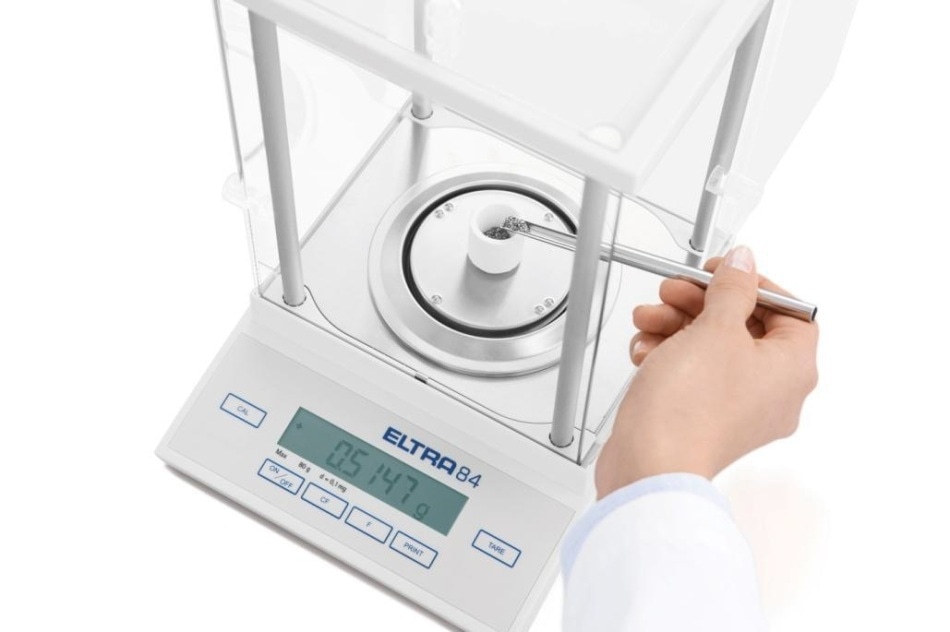
Figure 2. Weighing in the sample.
Application Example Fuels
During the production process of cement, generally different fuels are used. The released sulfur content of these fuels is a critical parameter for processing the combustion gas desulfurization. While coal has a relatively high sulfur content up to 5%, secondary fuels like biomass or wood have a low sulfur content of just 0.02%. Such samples with significantly varying sulfur content can be precisely and reliably analyzed by the combustion furnace of the CS-2000.
Using the CS-2000’s resistance furnace, both coal and wood samples were analyzed 10 times, each with a nominal weight of approximately 200 mg. The time taken for analysis was roughly 120 seconds, and the size was reduced down to 200 µm for sample preparation.
Analytical values of 10 measurements of wood |
% C |
49,86 +- 0,18 |
% S |
0,02 +- 0,001 |
Analytical values of 10 measurements of coal |
% C |
64,42 +- 0,07 |
% S |
0,56 +- 0,002 |
Conclusion
For the quality control of fuels, cement and other samples elemental analyzers based on combustion technology ensure fast, reliable and precise analysis of the sulfur and carbon content and are therefore a valuable addition to XRF analysis . ELTRA’s CS-2000 elemental analyzer, with its combination of induction and resistance furnaces, is unique in the market and covers a broad range of applications for carbon and sulfur determination in both inorganic and organic samples.
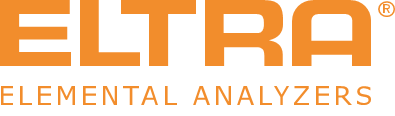
This information has been sourced, reviewed and adapted from materials provided by ELTRA GmbH.
For more information on this source, please visit ELTRA GmbH.