A solid sample material has to always be sufficiently prepared by homogenization and size reduction before exposure to physical or chemical analysis. Care should be taken that the analysis sample completely represents the original material and that the sample preparation process is performed reproducibly. Only then meaningful results are guaranteed. Most sample materials can be minimized to the desired analytical fineness at room temperature if a mill with a suitable size reduction principle (cutting, shearing, friction, impact, pressure) is chosen.
On the other hand, there are restrictions for size reduction at room temperature, for instance when even a small increase in temperature affects the sample in a negative way; or when the material is very elastic and the above mentioned size reduction principles only cause deformation. Cryogenic or cold grinding has proved to be the most ideal solution for these types of samples. This involves grinding aids such as dry ice (-78 °C) or liquid nitrogen (-196 °C) that are capable of embrittling the sample by cooling and making it break more easily. An additional advantage is that the volatile components of the sample can be preserved. This article describes which sample materials cryogenic grinding is appropriate, which laboratory mills are suitable, and which other factors those have to be taken into consideration.
For Which Materials is Cryogenic Grinding Advisable?
Samples with Elastic Behavior
It can be seen that a number of polymers (plastics such as PA, PET, PP etc.), as well as other materials, show visco-elastic behavior during grinding which results in a plastic deformation. This signifies that a crack initiation - and hence a break-up - does not happen. Elastomers like silicone rubber tires and baking dishes, which are used at room temperature due to their flexibility, have a so-called glass transition temperature far below room temperature. The elastic plastic sample’s temperature falls below the glass transition temperature if they are immersed in liquid nitrogen; this lowers the material’s ability to resist a high mechanical stress by either viscous flow or elastic-plastic behavior. If this pre-cooled material is then ground in a mill, brittle breaking behavior is shown by the sample. Although hard plastics are brittle at room temperature, cryogenic grinding can be applied to them too. The sample temperature should not exceed the glass transition temperature in order to achieve a successful size reduction process.
.jpg)
Samples with Volatile Components
Materials with volatile components like solvents (PCP, PCB, benzene, toluene etc.) are hard to prepare properly for analysis as a temperature rise during grinding may result in a loss of the analytes. The increased particle surface that result from the grinding process further enhances the emission of volatiles. The low temperature of dry ice or liquid nitrogen significantly lowers the high vapor pressure of the components and embrittles the sample matrix. Thus the volatile components are not largely affected by the relative temperature increase which occurs during the grinding process.
Biological and Medical Samples
For instance, if biological samples are prepared, for subsequent extraction of nucleic acids from human/animal tissue, plants, bacteria, or yeast, they may react extremely temperature-sensitive during and after the process and may even be destroyed. In such conditions, cryogenic grinding helps to enhance the process by embrittling groups of cells and cell walls, making them disrupt more effortlessly and slowing down the subsequent decomposition of the cell fragments. Undesired cell reactions are virtually “frozen” by immersing the sample into LN2 so that cell activities can be observed later.
.jpg)
Sticky or Tough Food Samples
Sticky or tough sample materials like marzipan, wine gum, raisins, or cheese simply clump together when ground at room temperature and are not adequately homogenized. The low temperature of the cryogenic process prevents the sample from clumping so that it is completely homogenized and suitable for analysis.
.jpg)
Overview Applications
Sample |
Mill |
Accessories |
Feed quantity |
Grinding time |
Speed |
Final fineness (d90) |
Gummy bears |
MM 400 |
- 2 grinding jars stainless steel 50 ml
- 2 grinding balls 25 mm stainless steel
- CryoKit, liquid nitrogen
|
10 pieces |
1 min |
30 Hz |
< 300 µm |
Caoutchouc |
CryoMill |
- grinding jar stainless steel 50 ml
- grinding ball 25 mm stainless steel
- liquid nitrogen
|
4 g |
2 min |
30 Hz |
< 500 µm |
E. coli bacteria |
CryoMill |
- grinding jar stainless steel 50 ml
- grinding ball 25 mm stainless steel
- liquid nitrogen
|
10 ml frozen cell pellets |
2 min |
30 Hz |
complete cell disruption |
Plastic granulate |
ZM 200 |
- 12-tooth push fit rotor
- distance sieve 0.5 mm
- cyclone
- liquid nitrogen
|
40 g |
20 s |
18,000 min-1 |
< 500 µm |
Refuse-derived fuels |
ZM 200 |
- 12-tooth push fit rotor
- distance sieve 0.75 mm
- cyclone
- 300 g dry ice
|
150 g |
30 s |
18,000 min-1 |
< 0.75 mm |
Wine gum |
GM 300 |
- grinding container stainless steel
- full metal knife
- cryo lid with aperture
- dry ice
|
500 g |
40 s and 20 s |
1000 min-1 and 4000 min-1 |
< 0.8 mm |
Rubber duck |
SM 300 |
- parallel section rotor
- 2 mm bottom sieve
- liquid nitrogen
|
5 pieces |
40 s |
3000 min-1 |
< 2 mm |
Pills with liquid filling |
RM 200 |
- mortar and pestle stainless steel
- liquid nitrogen
|
40 pieces |
3 min |
100 min-1 |
< 250 µm |
Suitable Lab Mills for Cryogenic Grinding
A number of aspects have to be taken into consideration while selecting a suitable laboratory mill for cryogenic grinding. While, the sample volume is critical for the decision, the feed size and preferred final fineness are important factors as well. The mixer mills CryoMill and MM 400 are specifically developed for processing small sample volumes. These mills often attain finer grind sizes, even with intricate plastic samples, than for example rotor mills as the sample is left behind inside the closed grinding jar for a longer period when compared to the open grinding chamber of the rotor mills. The sample is continuously cooled during the entire grinding process, in the CryoMill even with a constant temperature of -196 °C.
Mortar grinders, rotor mills, cutting mills or knife mills process significantly larger volumes and feed sizes than mixer mills. However, the size reduction principles of these mills generally produce larger grind sizes, particularly when grinding plastics. The Knife Mill GRINDOMIX GM 300 is suitable for cryogenic grinding mostly of food samples, with the limitation that no liquid nitrogen but only dry ice can be used as the mill is not designed for temperatures as low as -196 °C. However, cutting and rotor mills accept liquid nitrogen as well as dry ice as grinding aids. Due to the extremely low temperature, liquid nitrogen is especially suitable for materials with a glass transition temperature below -50 °C. One advantage of dry ice is that it evaporates less quickly than liquid nitrogen; also, it can be mixed with the sample for grinding thus extending the cooling effect. This is especially advantageous for materials of low thermal capacity which are incapable of holding low temperature, for instance thin plastic foils. Sample feeding with dry ice is often easier, particularly if the particles are smaller than 1 mm, instead of extracting the material from liquid nitrogen. Furthermore, it is safer to handle dry ice because the danger of asphyxiation, for instance, is much negligible. In addition, dry ice does not splash during grinding as it is mixed thoroughly with the sample material. Irrespective of these aspects, suitable safety regulations should always be observed when handling cryogenic grinding aids. The following section describes a range of laboratory mills ideal for cryogenic grinding.
Mixer Mills MM 400 and CryoMill
.jpg)
Mixer Mill MM 400
.jpg)
CryoMill with 50 liter tank
The mixer mills CryoMill and MM 400 are perfectly suited for homogenizing small sample volumes with a maximum feed size of 8 mm. These mills have two, respectively one, grinding stations into which the screw-top grinding jars - filled with grinding balls and sample - are safely clamped for grinding. The closed grinding jars, and hence the sample, are embrittled with liquid nitrogen.
Appropriate grinding jars of the MM 400 are made of PTFE or steel; one time use vials of 1.5, 2 and 5 ml are also available. It should be kept in mind that no liquid nitrogen should be enclosed in the grinding jars. The frictional heat of the grinding process causes LN2 to enter the gaseous phase, leading to a significant pressure increase within the grinding jar. Using tongs the closed grinding jar is placed for 2 to 3 minutes in an insulation container filled with liquid nitrogen and is then clamped into the MM 400. Because of the high energy input and the resulting frictional heat, the grinding process should not take more than 3 minutes to prevent the sample from warming up and to maintain its breaking properties. These should be interrupted by intermediate cooling of the closed grinding jars in case longer grinding times are needed.
In contrast with the MM 400, the CryoMill has the advantage of offering continuous cooling of the grinding jar with liquid nitrogen, lowering the temperature of jar and sample to -196 °C within minutes. Thus a consistent temperature of -196 °C is ensured even for long grinding times without the demand for intermediate cooling cycles. In addition, the user at no point comes into contact with liquid nitrogen which makes operation of the CryoMill user friendly and safe. The automatic pre-cooling function guarantees that the grinding process does not begin before a temperature of -196 °C is achieved and maintained. For heavy-metal-free grinding a zirconium oxide grinding jar is available.
Ultra Centrifugal Mill ZM 200
.jpg)
Ultra Centrifugal Mill ZM 200 with cyclone
The Ultra Centrifugal Mill ZM 200 is another mill which is completely suitable for cryogenic grinding as it accepts larger sample volumes than the mixer mills. This high-speed rotor mill is even capable of pulverizing some types of elastomers, such as polystyrene, without cooling. However, in most cases embrittlement of the material is required. The sample, which can be granulate or pre-cut molded parts, is immersed directly into a container filled with LN2 and is then slowly but continuously fed into the hopper of the ZM 200 using a steel spoon. If the sample is extremely heat-sensitive or has a high fat content, embrittlement generally enhances the grinding process as the cooling counteracts the frictional heat effects. When dry ice is used as grinding aid, this has to be mixed with the sample in a 2:1 ratio and then the ZM 200 pulverizes the complete mixture. Dry ice is pure carbon dioxide and thus evaporates from the sample without residues. It is recommended to use a cassette along with a cyclone to ensure that CO2 and residues of LN2 evaporate during the grinding process.
Cutting Mill SM 300
The abovementioned aspects affecting the choice of a grinding aid are also applicable when performing cryogenic grinding in the Cutting Mill SM 300. This mill is especially suitable for processing tough materials such as bitumen or shoe soles and accepts larger feed sizes than the ZM 200. Even embrittled and roughly cut car tires can be homogenized with the SM 300. The embrittled sample material is rather hard; thus it is recommended to use the 6-disc rotor as it works more like a shredder. It can also be used to cut heterogeneous samples such as frozen chicken parts including bones. For grinding thin plastic foil, which is usually a part of refuse-derived fuels, it is recommended to use dry ice due to the continuous cooling effect during the grinding process.
Knife Mill GRINDOMIX GM 300
.jpg)
Knife Mill GRINDOMIX GM 300 with steel container
Tough and sticky food samples such as marzipan, wine gum, raisins, or cheese are perfectly homogenized with the Knife Mill GRINDOMIX GM 300. Even chocolate, which easily becomes paste-like when processed at room temperature, can be effectively pulverized cryogenically. The sample is then mixed with dry ice in a ratio of 1:2; after a few minutes it is completely cooled and the grinding process starts. The dry ice keeps the sample cool throughout. It should be taken care that no plastic accessories are used when carrying out cryogenic grinding in the GM 300 as these could be damaged during the process. Suitable accessories include a grinding container of stainless steel, a full metal knife and a lid with aperture to allow evaporation of the gaseous carbon dioxide.
Mortar Grinder RM 200
Pressure and friction are used to pulverize samples in a mortar grinder and these samples are submitted to the grinding process for as long as it takes to attain the desired final fineness. The Mortar Grinder RM 200 is not a closed system; it is possible to add liquid nitrogen or dry ice during the grinding process via a window in the cover. Cryogenic applications require pestle and mortar that are made of stainless steel. For instance, a mortar grinder can successfully pulverize tablets with liquid filling.
Overview RETSCH Mills for Cryogenic Grinding
Mill |
Feed size 1,2 |
Max. feed quantity 1,2 |
Final fineness 1,2 |
Remark |
CryoMill |
< 8 mm |
1 x 20 ml |
50 µm |
- Continuous grinding under cryogenic conditions
- User comes at no point into contact with LN2
- Zirconium oxide grinding jar available for cryogenic applications
|
MM 400 |
< 8 mm |
2 x 20 ml |
100 µm |
- Sample is placed in leak-free grinding jar of steel or PTFE and embrittled before grinding
- Intermediate cooling may be necessary
|
ZM 200 |
< 10 mm |
4000 ml |
300 µm |
- Embrittlement with LN2, e. g. of samples with glass transition temperature < -80 °C
- Dry ice is best suited for materials with low thermal capacity
- Dry ice is preferably used for samples with a particle size < 1 mm
- Use of cyclone is mandatory
|
GM 300 |
< 40 mm |
2000 ml |
500 µm |
- Dry ice is best suited for materials with low thermal capacity
- Dry ice cools the sample during grinding
- Full metal knife used together with stainless steel grinding container and a special cryo lid
|
SM 300 |
< 80 mm |
4000 ml |
2000 µm |
- Cryogenic grinding only with 6-disc rotor and cyclone
- Bottom sieves 2 – 20 mm suitable for cryogenic applications
|
RM 200 |
< 8 mm |
< 190 ml |
10 µm |
- Dry ice or LN2 can be added during grinding
- Only use mortar and pestle made of stainless steel
|
1 Depending on sample material and grinding parameters
2 Volume may differ for applications without cryogenic grinding aids
Conclusion
For many materials pulverization with dry ice or liquid nitrogen is the only possible way of obtaining a sample that suits subsequent analysis. It is shown that a range of laboratory mills which allow for efficient and gentle cryogenic sample preparation is offered by RETSCH. Their use significantly lowers both the labor and cost required for low-temperature grinding. A selection of suitable accessories ensures that the grinding process is performed with safety.
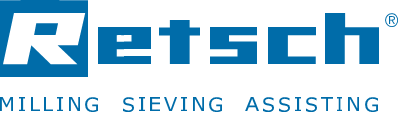
This information has been sourced, reviewed and adapted from materials provided by RETSCH GmbH.
For more information on this source, please visit RETSCH GmbH.