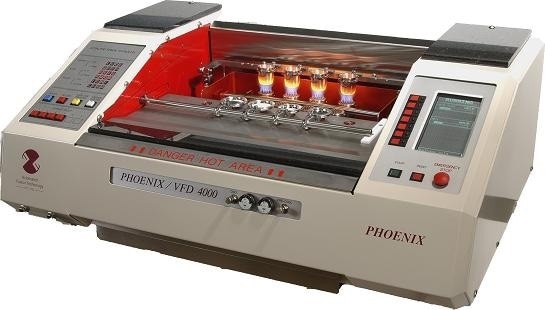
Tools and Materials
- A Phoenix (gas fusion machine)
- Phoenix moulds in Pt95/Au5 (AM7@60 g– bead = Ø39/41 mm x h3 mm)
- Phoenix crucibles in Pt95/Au5 (AC2@40 g)
- Long tongs (20 cm) with plastic tips (to prevent scratching the crucible and the mould)
- An ultrasonic cleaner (with heating)
- A plastic spatula to mix the flux and the sample together
- A micropipette to add the Non-wetting (releasing) agents
- A weighing pan or other
- A weighing spatula to weigh the sample
- A spoon-spatula to weigh the oxidizer and the flux
- An analytical balance with a weighing range of about 200 g and a precision of 0.1 mg
Note: 95% Platinum 5% Gold (Pt/Au): Universally accepted material of choice for crucible and casting moulds for spectrographic analysis by x-ray fluorescence (XRF).
Note: Never touch the casting surface with tongs: any scratches will be on the glass bead measurement surface.
The Chemicals
- The citric acid (a 20% solution to clean the crucibles and the moulds)
- The Non-wetting (releasing) agents: Lithium Bromide (solution 250 g/l)
Note: An iodide or bromide may be used to facilitate the release of the fluid melt from the crucible, ensuring less hang-up of melt and making cleaning easier. The solidified bead releases more freely from the mould (fewer repeats, less mould scratching).
- The oxidizer: LiNO3; 99.98+%
- The flux: FLUX LT66:LM34; 99.99+% (m.p. 875 °C)
Preparations of Casting Powders
Weigh 0.9000 g of dried (or ignited) and grinded Iron Ore, 9.0000 g of borate flux and 0.5000 g oxidizer and mix them together. The mixture is thoroughly mixed to be sure the contact between oxidizer and sample is perfect (about 1 minute). Then, the mixture is transferred into the crucible.
Note: Ensure that no powder is left on the flat rim of the crucible (the remaining powder can interfere with the casting).
- The non-wetting agent should be added on top of the mixture powder
- The crucible containing the powder should be placed into the auto-lock crucible holder
- The mould should be placed on the ring mould holder
- The desired program has to be loaded and then the start button has to be pressed (hold for about 5 seconds)
- The bead should be removed from the mould once the fusion is complete
Note: Never touch the measurement side with your fingers (the side that faced the casting dish surface).
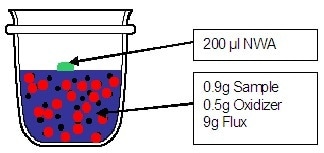
Fusion Program Settings
Program 1
|
Function |
Time |
**Temperature |
Swirl Speed |
Swirl Frequency |
0 |
Ignition: |
5 sec. |
- |
|
|
1 |
Prewarming (pilot heating) |
0 sec. |
300 °C |
|
|
2 |
Premelt: (preheating step): |
250 sec. |
800 °C |
|
|
3 |
Melting (without swirling): |
100 sec. |
1100 °C |
|
|
4 |
Melting (with swirling): |
300 sec. |
1100 °C |
85% |
*15 sec. |
|
Mould heating: |
80 sec |
1050 °C |
|
|
5 |
Pouring: |
25 sec. |
- |
|
|
6 |
Pre Cooling: |
60 sec. |
- |
|
|
7 |
Cooling: |
240 sec. |
- |
|
|
|
TOTAL TIME: |
16 min 20 sec. |
|
|
|
*Clock Wise (CW) – Stop and Counter Clock Wise (CCW) sequence.
** for the flame temperature add about 250 °C
Comments
All Iron Ore to be fused using this technique should be of fine particle size that is less than 100 µm.
The Lithium Nitrate is chosen instead of Sodium Nitrate to analyze the Na.
Why an Oxidation Treatment?
Direct fusion of non-fully oxidized samples in molten borate flux is not possible. The primary reasons are that non-fully oxidized will not immediately dissolve and they will attack and destroy the crucible metal. The present technique overcomes both problems to accomplish the successful fusion of Iron Ore.
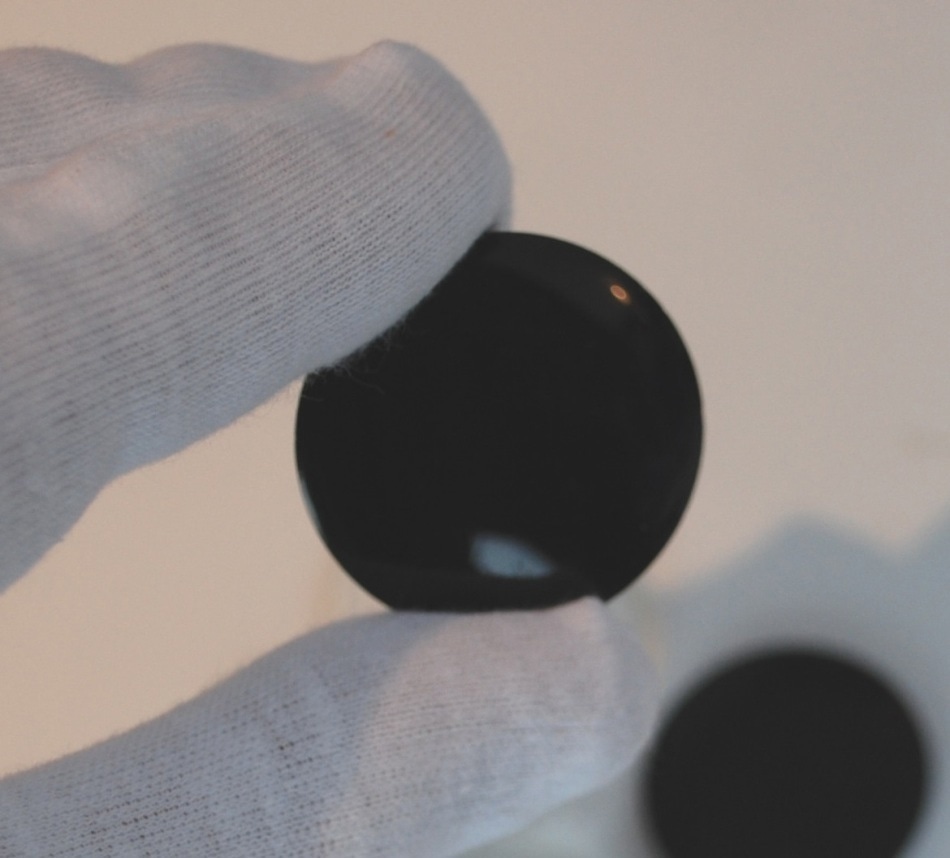
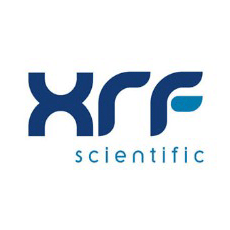
This information has been sourced, reviewed and adapted from materials provided by XRF Scientific.
For more information on this source, please visit XRF Scientific.