The Evactron® Anti-Contaminator has been shown to be very successful in eliminating labile hydrocarbon contamination from Electron Microscope chambers1. Also, Evactron Plasma cleaning has been shown to enhance Carbon analysis by X-ray spectrometry2. There are no reports of damage or failure of X-ray windows from Oxygen Radicals developed in the Evactron A-C by operators who have EDS detectors on their SEM systems.
In order to show that the Evactron A-C cleaning will not damage the thinnest MOXTEK™ Ultra Thin window (the AP3.3 EDS window), XEI Scientific and MOXTEK™ carried out window exposure tests on the effects of Evactron A-C cleaning. In these tests, several AP3.3 were exposed to the oxygen radical flow in 20-80 hour continuous exposures for several run periods of a total of over 160 hours. During the tests, a 500X and helium leak detector was used to examine the windows for leaks, and light microscopy was also used to look for any sign of damage.
The compact RF plasma device, Evactron A-C, creates oxygen radicals from an air bleed into the Oxygen Radical Source. Mounted on an SEM chamber accessory port, the ORS (Oxygen Radical Source) creates localized plasma. Instead of bombarding the surface with ions, the ORS plasma cleans by chemical reaction. The organics and hydrocarbons are ashed into H2O, CO2, and CO molecules by free radicals.
These are then readily pumped by the roughing pump. From the ORS, the oxygen radicals flow towards the roughing pump through the chamber by the pumping differential. The Evactron process is gentle so as to meet the requirements of cleaning the insides of delicate vacuum instruments. Cleaning with oxygen radicals is very useful for eliminating organics in the gas phase and those adsorbed on the walls and other chamber surfaces, including specimens.
The cleaning process gradually attacks polymer films or heavy and polymerized contamination deposits. The low level of polymer attack is due to the high concentration of C-C single bonds in polymers and the low concentration of oxygen radicals. A first step hydride extraction is involved in the mechanism of the oxygen radical attack on organic molecules. This leads to the creation of reactive sites on the carbon skeletons that are prone to further oxidation. Without hydride extraction, the oxidation of the C-C single bonds in polymers has an extremely low reaction rate.
.jpg)
Figure 1. MOXTEK™ test windows #3 & #4 shown beside test chamber #2. Window #3 is in the CF 275 flange and window #4 is in the MOXTEK™ engineering mount. Both have been exposed to 160 hours of Evactron cleaning and both are He leak-tight. The Evactron ORS oxygen Radical Source is mounted to the side port of the test chamber.
Previous tests conducted on Aluminum (Al) by Walck et al (3) using XPS indicate no growth of the Al2O3 oxide layer over short periods of 10-20 minutes. Al film is used for coating the MOXTEK™ windows. Any attack on the windows would have to start with an attack on the Al film. The resulting Al2O3 can powder off and produce a hole. This can be identified by the presence of light leaks observed by transmission optical microscopy. MOKTEK uses He leak detection and optical microscopy to test windows. All the windows left the factory with He Leak rates below the baseline rate of 2.2x10-10 millibar Lit/sec.
Experimental Framework
The first three MOXTEK™ AP3.3 EDS Windows were mounted onto a CF 2.75” flange with a hole in the center, the flange was then placed in the Evactron test vacuum chamber, at the same location each testing period, in the oxygen radical flow. Being the thinnest MOXTEK™ window, AP3.3 offers the best light element x-ray transmission. The front surface of the AP3.3 window is 30 nm Al film. It acts as a secondary gas barrier and blocks photons.
The windows were positioned in the area of maximum cleaning oxygen radical concentration in two distinct XEI Scientific test chambers, pumped, by an oil rotary pump. Test chamber #1 was roughly 14"Ø x 16" high. Test chamber #2 was an 11” cube with observation windows on the side. In order to equalize the pressure, the windows were mounted on a circular flange with a hole behind the window. A small clearance was provided to the vacuum relief passage to minimize oxygen radical interaction with the window backside.
The Evactron A-C was operated under XEI Scientific's recommended operating conditions of 0.6 Torr and 10 Watts of RF power at 13.56 MHz with room air as the feed gas. The first test window was exposed to the oxygen radical flow in approximately 30-hour continuous exposures for five-run periods, for a total of 160 hours. Extra windows were exposed for longer periods to hunt for a maximum exposure limit.
The flanges/windows were tested for damage and leaks after each exposure to oxygen radical flow. The windows were then tested for a detectable helium leak, with the limit of detection at 3x10-10 mbar L/seconds. After each oxygen radical exposure run period, pictures of the window were also taken and examined for any sign of degradation in the window.
Results
Window 1: Some pinhole light leaks were noted, after 40 hours of continuous exposure (Figures 1 and 2.) There was no increase in the size of these light leaks in subsequent examinations at 70, 100, 127, and 160 hours. A small leak of 0.6x10-10 millibar Lit/sec appeared in the first window after 100 hours of exposure.
This was because of handling damage as detected by microscopy at MOXTEK™. Although the leak was within MOXTEK™ quality standards, it raised a question about the data. Two more exposures did not worsen the leak, but the testing was stopped on the first window after 160 hours of exposure in favor of testing a second window. The tests were performed in test chamber 1.
.jpg)
Figure 2. A transmission mode micrograph closes up of window 1 shows a multitude of small light leaks after the first 40 hours of exposure to Evactron cleaning. No Vacuum leak was found. The light leaks did not change with increasing exposure time and were not repeated on other windows. The dark area is the underlying support grid.
After an initial exposure of 40 hours, window #2 was destroyed while shipping back to Moxtek. In test chamber 2, window #3 was exposed for three exposures as follows: 60 hours, 24 hours, and 62 Hours (146 hours total). A small number of light leaks (65) were found in the Al coating after the last exposure. There was no increase in He leak. This was the highest amount of damage observed on any of the test windows and was not repeated on the other windows.
Instead of being mounted on the CF 40 flange, the fourth and fifth windows were mounted in smaller MOXTEK™ “engineering” mounts. XEI Scientific achieved its own leak detection equipment and an optical microscope to speed the testing. The exposures were carried out in test chamber #1.
.jpg)
Figure 3. Interior of Chamber #1 showing Evactron plasma pink glow during Evactron cleaning exposure of window #5. A quartz thin film thickness monitor is also shown in the chamber placed on a pedestal beside the window.
Window #4 was exposed to 20 hours of cleaning between each examination by light microscopy. Until 160 hours of exposure, no light leaks were noted. At the 160th hour, one pinhole light leak was observed. No vacuum leak was found by He leak detection.
In order to see if results are affected by the length of exposure to Evactron Cleaning, Window #5 was exposed to three long periods of continuous exposure. At the end of the first exposure of 66 hours, no pinholes were observed. After another 46 hours of continuous exposure, 112 hours total, no light leaks were visible - even after a second examination was done following rapping the mounting rim to dislodge any loose Alumina from the surface. No light leaks were visible even after another 48 hours of exposure (160 hours total).
Discussion
Window failures caused by vacuum leakage did not occur during the periods tested of about 160 hours on all the windows. Although the results on window 3 suggest that the duration of Evactron cleaning may impact the rate at which pinholes appear in the Al Coating of the window, the test on window #5 did not confirm this result.
Compared to shorter exposures, continuous Evactron cleaning may cause more window light leaks and add up to the same exposure. In fact, continuous exposure may be more rigorous than multiple exposures for the following three reasons:
- Normally, hydrocarbon contamination is trapped within the chamber by the cold window surface. This protects the Al window from oxygen radicals during short cleaning periods.
- Test windows are subjected to higher oxygen radical concentrations through continuous exposure. Thus, additional damage may occur because surface hydrocarbon contamination entering the vacuum chamber between sample exchange cycles is not present.
- Attacks on the Al crystal structure may rely on openings or weak points in the Al2O3 oxide coating. Once the exposure to Evactron cleaning is stopped, these weak spots may heal.
Vacuum leaks are the usual mode of failure for MOXTEK™ UTW windows. Causes of vacuum leaks can be determined under the microscope by MOXTEK™ Inc. Microscopy easily detects vacuum failures caused by workmanship errors, materials failure, impacts, or corrosion. As a part of quality assurance by MOXTEK™ Inc., leak detection is carried out on each new window. None of the Evactron cleaned windows except window #1 showed an increase in vacuum leakage.
Window #1 showed evidence of mechanical damage after shipping and this was blamed for the small increase in the He leak rate. Moreover, Evactron cleaning did not increase the leak on this window. Although it is not known how much continuous Evactron cleaning would be required to create a vacuum leak, from the known polymer decay rates and appearance of the windows due to Evactron cleaning, XEI estimates it would be well over 200 hours and maybe more than 500 hours of continuous exposure.
There is no specification for Light Leaks in MOXTEK™ UTW windows. Light leaks can increase the background on EDS detectors during Evactron cleaning and may expose the underlying polymer film to corrosion. The multitude of small light leaks on window #1, visible after the first cleaning, did not increase in size with additional cleaning. A multitude of light leaks was seen on window #1 after the initial cleaning. No such defect was seen on other windows. The results imply that if the UTW is exposed to extreme Evactron cleaning and light leaks indeed start to appear, the first indication would be a rise in the background levels in the EDS X-ray spectrum.
The Evactron A-C cleaning cycles have a duration time of 2 to 5 minutes under the recommended and usual operating conditions. The number of cleaning cycles differs widely from SEM to SEM and from one lab to another. In most labs, Evactron cleaning is carried out only when image quality starts to deteriorate. In some cases, Evactron cleaning is carried out on a daily basis. Using cleaning periods of 5 minutes, 160 hours of exposure is equivalent to 1,920 cleaning cycles. If there are 5 SEM operating days/week with 1 cleaning cycle/day, then the total test period of 160 hours is equivalent to 8.7 years of 5 minute daily exposures.
Conclusions
No adverse effects were observed on the leak tightness and mechanical structure of the four AP3.3 MOXTEK™ windows after 160 hours of exposure. Evactron testing time periods were selected to extend far beyond the normal expected lifetime of an AP3.3 window at normal Evactron cleaning periods. In order to suppress contamination buildup and retain image quality, the Evactron A-C operates 5 minutes a week on a typical analytical SEM. Evactron A-C cleaning may be required more frequently in situations where contamination is introduced to the system daily.
The total Evactron A-C use per year would be about 22 hours in the extreme case of daily cleaning at 5 minutes/day. About 4 ½ years is required to achieve 100 hours of exposure. MOXTEK™ windows offer a guarantee for 16 months against failures caused by workmanship and materials and usually last for a number of years before replacement.
While 160 hours of cleaning caused light leaks on four different Moxtex windows, it did not cause the windows to fail vacuum leak tests. The total test time of 160 hours is well over the exposure time a window would see during its normal Evactron A-C cleaning periods and normal life. As long as XEI Scientific recommended cleaning practices are followed, the use of Evactron Cleaning is safe for MOXTEK™ UTW windows.
XEI Recommendations
XEI Scientific recommends the following cleaning practices:
- Evactron Cleaning should never be used overnight.
- Evactron clean for no more than 30 minutes daily.
- Evactron clean only when contamination affects light element x-ray sensitivity or image quality
- On SEMs fitted with MOXTEK™ UTW equipped detectors, Evactron clean for 5 minutes periods or less and vent the chamber between cleanings
If these recommendations are followed, it will result in the UTW window lasting its anticipated normal lifetime of more than 5 years without any trouble.
References and Further Reading
- N. Sullivan et al, A STUDY OF THE EFFECTIVENESS OF THE REMOVAL OF HYDROCARBON CONTAMINATION BY OXIDATIVE CLEANING INSIDE THE SEM. Microscopy and Microanalysis 8 (suppl. 2)(2002) 720CD
- P. Rolland et al, IMPROVED CARBON ANALYSIS WITH EVACTRON PLASMA CLEANING, Microscopy and Microanalysis 2004
- Walck et Al, XPS EVALUATION OF SAMPLES SURFACE CLEANED BY THE XEI EVACTRON®, Microscopy and Microanalysis 7 (suppl. 2)(2001)
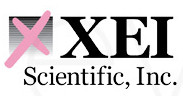
This information has been sourced, reviewed and adapted from materials provided by XEI Scientific.
For more information on this source, please visit XEI Scientific.