In scanning electron microscopy, the deposition of electron beam induced hydrocarbon contamination is considered to be a persistent problem. Deposition of contamination on a sample is usually an unwanted and negative effect (even though it has been controlled and employed positively to manufacture atomic force microscope (AFM) probes). Many times the vacuum readings appear relatively good but the electron beam still leaves alarming contamination marks on the sample.
This means that, in a CD-SEM, it is not possible to carry out repeated measurements without extra, sometimes unacceptably high measurement errors resulting from "carry-over." Carryover refers to the increase in dimension size due to the deposition of hydrocarbon contamination deposited by the electron beam on the edges of the structure under measurement.
The hydrocarbon moieties being deposited are from a wide range of sources including the stage lubricants, vacuum system and the sample itself. During the time necessary for even one measurement, the sample may change and the extent of this change is unknown unless a perfect contamination measurement technique is found and regular monitoring is applied.
In an earlier report, some of the causes of contamination in laboratory scanning electron microscopes (SEMs) were studied and potential solutions were presented (Postek, 1996). This article expands upon that earlier study and offers an additional active monitoring and control approach to solving this problem.
Materials and Methods
A Hitachi2 S-4700 laboratory SEM, a Hitachi S6280-H CD-SEM and an S-806 tilt SEM were used throughout this study. The two latter instruments were provided with 150 mm wafer stages. The CD-SEM was provided with two Ebara dry pumps and two turbomolecular pumps. The tilt SEM had two rotary pumps and one turbomolecular pump.
The S-4700 laboratory SEM was equipped with the factory-installed pumps: one diffusion and two rotary mechanical pumps. The samples employed in the study were clean wafers or diced chips from wafers made with different processes used in silicon integrated circuit technology. In this study, the amount and rate of contamination deposited on these samples were explored and some of the possible methods of reducing the effects of contamination, including a new anti-contamination apparatus, known as Evactron™, were also explored.
Evactron™
The Evactron2 is an automatic plasma cleaning and vacuum monitoring system. The system is capable of measuring the vacuum level and by the use of valves it also controls the pressure of the gases introduced into the chamber needed for plasma cleaning. It has an in-built power supply to drive a plasma-generating head. The schematic diagram of the Evactron cleaning head is shown in Figure 1. The unit is mounted on the wall of the SEM sample chamber and comprises of a controller capable of being configured to automatically control the whole cleaning process.
The cleaning procedure is carried out at much higher pressure (40-100 Pa) than the normal operating pressure (10-3 - 10-4 Pa) of the specimen chamber. The cleaning cycle begins with the closing of the necessary valves in order to separate the specimen chamber from the electron optics. In the best case, the specimen chamber can just be separated from the diffusion or turbo-molecular pump. In other cases, based on the design of the vacuum system the procedure will vary. The next step is to let gas (clean, filtered, room air or oxygen-argon mixture for faster cleaning) into the specimen chamber and then stabilize the pressure at its optimal value of 80 Pa.
After reaching this point, the high (13.56 MHz) frequency power is applied to the cleaning head for a few minutes. The time duration and the power applied depend on the size of the chamber. A gentle plasma cleaning is provided by this procedure. The nascent oxygen present in the chamber rapidly reacts with the residues in the vacuum and the products are pumped out. To accelerate this step, it is beneficial to use a clean N2 flush. In the case of an oxygen-argon gas mixture this step is compulsory. This procedure can effortlessly be made completely automatic, thus the user only has to start the unit and wait until it has finished and the SEM is ready for its regular work schedule.
Certain commercial equipment is identified in this report in order to adequately describe the experimental procedure. Such identification does not imply recommendation or endorsement by the National Institute of Standards and Technology, and it does not even imply that the equipment identified is essentially the best available for the purpose. EVACTRON is a trademark of XEI Scientific.
.jpg)
Figure 1. Schematic diagram of the Evactron cleaning head.
Results
The contamination deposition behavior of two CD-SEMs is illustrated in Figure 2. The same UV photoresist wafer was examined by each instrument. The instruments were programmed to go to a particular isolated line and without moving the sample perform 50 (so-called static repeatability) measurements. While one instrument was capable of reporting the 50 repeated measurements to within less than 2 nm change in the linewidth, the values attained with the other tool shifted close to 8 nm. Typically, linewidth measurements are performed from repeated line scans or averaged images (which exhibit similar behavior).
Thus, the deposition of contamination can invalidate the data since an SEM with a severe contamination problem does not have the potential to measure the line without changing the width. This may take place even after a single scan. The case of a positive carry-over is specifically suspicious, because that may be a sign of severe contamination.
Precise measurements need the measurement and understanding of the contamination rate. Valid dimensional measurements cannot be done without measuring the rate of contamination, which in effect is a measurement error. Additionally, it is possible for a thick layer of beam-induced contamination to act as a resist and those locations that were measured with the SEM may not etch at the same rate as similar undisturbed areas during subsequent processing.
.jpg)
Figure 2. The results of 50 repeated line width measurements with two different CD-SEMs with the same UV photoresist wafer.
It has been suspected that the contamination layer developed by the electron beam comes from two sources: the sample surface and the vacuum. Reimer (1993) describes a process of drift of large molecular weight molecules under the electron bombardment. The deposition of the contamination layer is considered to be a dynamic process. Molecules arrive at and leave the sample surface simultaneously. The amount of contamination deposited depends on the electron dose, (that is, the length of time the beam dwells on the sample). The contamination becomes thicker when the dwell time gets extended.
This process is illustrated by Figures 3 and 4. In the case of Figure 3, the (5 kV, 10 pA) electron beam was left on a clean, etched silicon sample for two hours at high magnification. Viewed at lower magnification, the extremely heavy deposition of contamination is formed as a "sculpture" with a peak at the upper left corner. The electron beam produced the frame of the structure since it dwelled longer at the edges before the sync pulses arrived and initiated the horizontal and frame scans.
Additionally, just before the frame scan started the electron beam dwelled a bit more at the upper left corner, thus the beam remained stationary at that point for the longest time overall and formed a rather taller contamination peak (not unlike an e-beam deposited AFM probe). The drifting of the beam and/or the sample stage during the long irradiation time resulted in the structure appearing to be distorted.
The presence of the vertical line (originally the left edge of the frame) close to the middle of the contamination-induced frame obviously proves that once contamination has been deposited, the electron beam cannot remove it. If viewed in real time at high magnification, the operator does not voluntarily see the contamination. The image that is displayed on the viewing screen is about 20% smaller than this frame hence, the electron beam usually over-scans a bigger area on the sample than the electron beam displays on the screen. Thus, the most disturbing part of the contamination deposited at high magnification refers to the fact that the effect of contamination is usually not observed by the operator except when going back to lower magnifications.
.jpg)
Figure 3. Contamination formed on a silicon wafer sample during 2 hours of continuous electron beam bombardment. The left image was taken with 60° sample tilt and the 3-dimensional structure of the contamination can be observed.
Figure 4 displays an etched silicon "grass" sample at 50000 times magnification. This sample was bombarded with a 5 kV, 10 pA electron beam at 500000 times magnification. The area displayed on the screen of the SEM at this magnification is marked close to the center of the image. The 500000 times magnification image is introduced at the lower right corner. The typical frame-like contamination mark is not visible any longer; the dynamic process developed only a circle at this greatly high magnification. For 10 minutes, the electron beam was left on the sample.
.jpg)
Figure 4. Etched silicon "grass" sample at 50000 times magnification, which was bombarded with a 5 kV, 10 pA electron beam at 500000 times magnification
Figure 5 displays two images taken with CD-SEM. In this case, the (800 V, 3 pA) electron beam bombarded the sample for six minutes. During this time the beam drift/sample and the contamination resulted in the enlargement of the corner section by about 0.15 µm. Similar effects can occur in shorter times, in severe cases even in a few seconds.
The extent that deposited contamination contributes to measurement errors in CDSEMs will continue to be unknown unless the operator is aware of this problem and consistent correct examinations and measurement of the contamination rate is executed.
.jpg)
Figure 5. X and Y enlargement of the corner region due to contamination and drift in a CD-SEM. 800 V, 3 pA electron beam bombardment for 6 minutes.
Anti-contamination Devices
Clearly, electron beam induced contamination is considered to be a real problem in scanning electron microscopy and no instrument is completely free of this problem. Even dry pumped instruments are capable of depositing contamination (generally at a much lower rate). Contamination also results from hydrocarbons brought into the proximity of the electron beam by the specimen itself. The extent of the problem could be revealed by regular contamination rate measurements, but if the errors due to contamination are excessively high, something has to be done to alleviate the problem.
One possibility with specific SEMs is the use of a liquid nitrogen anti-contamination device. An anti-contamination device is basically a small, flat metal piece placed above the sample surface that is kept at liquid nitrogen temperatures. The anti-contamination device, by working essentially as a getter pump or cold trap, collects the good part of the contaminants. Thus, the localized sample contamination rate, at the sample, is reduced.
However, it should be noted that the trapped contaminants are released once the device is allowed to warm-up. Figure 6 shows an etched silicon "grass" sample viewed at 50000 times magnification in an instrument provided with a liquid nitrogen anti-contamination device. This sample was bombarded two times at two different locations at 100000 times magnification for 10 minutes (@ 5 kV, 10 pA). The left image of Figure 6 was collected without liquid nitrogen added to the device, and the right image was taken with the same conditions but with the anti-contamination device completely charged with liquid nitrogen. The amount of contamination is definitely reduced, but it still remains high.
.jpg)
Figure 6. Two locations of a silicon "grass" sample irradiated for 10 minutes without (left) and with (right) the application of liquid N2 to cool the anti-contamination device (50000x).
Evactron Cleaning
Figure 7 displays two images of the same silicon "grass" sample viewed in the same scanning electron microscope as Figure 6. For the sake of easy comparison, the left image is the same as the image on the left of Figure 6 but the right image was taken after the Evactron unit was turned on and the cleaning procedure applied for 10 minutes. On the right side of Figure 7, where the Evactron anti-contamination device was employed, the amount of contamination is significantly reduced. The amount deposited is also far less than even with the liquid nitrogen-cooled anti-contamination device.
A cold field emission gun instrument was the SEM that was used to take the images in Figure 7. It was provided with a liquid nitrogen cold trap above the water-cooled baffle on top of the diffusion pump. This instrument was also provided with a gaseous nitrogen leak system where needle valves in the fore lines of the mechanical pumps are set to about 2 Pa.
This intentionally inhibits the rotary pumps from reaching their ultimate vacuum (Postek, 1996). This leak is small enough to keep the pump efficiently backing the diffusion pump or pump-down the specimen exchange chamber without compromising the ultimate chamber vacuum. However, the endless streaming of nitrogen molecules into the line reduces the potential of backstreaming of oil from the rotary pumps. This simple system offers an effective mechanism for lowering instrument-induced contamination but in a number of cases, as shown here, may not be sufficient.
.jpg)
Figure 7. Two locations of a silicon "grass" sample irradiated for 10 minutes before (left) and after (right) the use of Evactron anti-contamination device. 50000x
CD-SEMs are usually equipped with oil-free fore line pumps and turbomolecular pumps in order to provide a cleaner, better vacuum. Even with these pumps, a number of SEMs are not clean enough and disturbing contamination deposition takes place. Regular monitoring and if necessary, instrument cleaning has to be performed. For monitoring, two possible ways can be followed:
- Measure the rate of contamination with the Evactron, which reveals the cleanliness of the vacuum.
- Measure the effect on dimensional measurement by measuring the change taking place during repeated measurements.
The rate measurement is more beneficial in general, but it may not be as applicable for all samples. This is because varied samples made of different materials are inclined to contaminate at different rates and the samples themselves are sources of the contaminating molecules as well. Another possibility for sample dimensional change that must be acknowledged is that the sample under test can become distorted by the electron beam exposure itself (Postek et al., 1989). Hence, it is necessary to properly assess the distinction between change due to contribution from contamination deposition and electron beam induced change.
Following several Evactron treatments, the vacuum begins to remain clean for prolonged time periods and the frequency of necessary Evactron treatments becomes less. However, since the cleanliness of the vacuum relies also on the cleanliness and nature of samples going through the system, steady monitoring of the contamination rate can specify when another cleaning cycle must take place.
Figure 8 displays an image taken with a tilt wafer SEM. Before the Evactron cleaning, it was impossible to work without majorly contaminating the sample. The instrument went through a series of 10 minutes Evactron cleanings. After the cleanings, only a minimal amount of contamination developed under the electron beam. This is demonstrated by the light contamination mark on the clean, freshly etched polysilicon sample.
.jpg)
Figure 8. Tilt wafer SEM. Minimal contamination mark on a polysilicon sample after treatment, 15 minutes dwell time at 30000x magnification, @5 kV.
Sample Cleaning
After contamination has been deposited on a sample, it is possible to remove it to some extent with in situ oxygen plasma cleaning by using the Evactron. This cleaning procedure is demonstrated on a silicon "grass" sample in Figure 9. Both locations of the sample were irradiated for 10 minutes. The left image of Figure 9 is the untreated sample. The image on the right of Figure 9 was taken after a 60-minute treatment of the sample with the Evactron anti-contamination device. It is significant to highlight that long treatment of the sample may also modify the "clean" areas as well.
.jpg)
Figure 9. Silicon grass sample that was irradiated for 10 minutes. The left image was taken after contamination deposition and is shown untreated. The image on the right was taken after a 60-minute in-situ treatment of the sample with Evactron anti-contamination device. 50000x
Conclusions
Contamination of different samples under the electron beam has been proven to cause measurement errors in CD-SEMs and laboratories. The extent of the error is not known unless steady monitoring of the contamination rate is executed. Removal of the contaminating molecules must take place based on the severity of the problem. This article described a new cleaning method employing an active plasma system that was studied to be effective in cleaning the vacuum of the specimen chamber of laboratory and production metrology SEMs.
References and Further Reading
- Postek, M. T. 1996. An approach to the reduction of hydrocarbon contamination in the SEM. SCANNING 18:269-274
- Postek, M. T. 1989. Scanning Electron Microscope-based Metrological Electron Microscope System and New Prototype SEM Magnification Standard. Scanning Microscopy 3(4):1087-1099
- Reimer, L.: Image Formation in Low-Voltage Electron Microscopy SPIE Opt. Eng.Press; Volume TT 12 (1993) ISBN 0-8194-1206-6
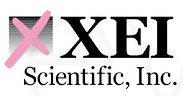
This information has been sourced, reviewed and adapted from materials provided by XEI Scientific.
For more information on this source, please visit XEI Scientific.