Interview conducted by Mychealla RiceNov 23 2017
In this interview, Stephen Browning, Structural Engineer from Strongwell talks to AZoM about the current industry methods for making these connections focusing on the mechanical connections and a combination of mechanical and bonded connections.
What are the current industry methods for making connections between composites and between composites and other materials such as metals, wood, concrete and plastics?
The primary method for pultruded composite connection to other composites, as well as other materials, is mechanical connections such as bolts, screws, and rivets. Bonding alone using adhesives is not typical, but bonding with adhesives and installing bolts, screws or rivets is common.
Why are mechanical connections the preferred method?
Mechanical connections are preferred because they were established as the standard for pultruded structural shapes at the onset of manufacturing pultruded composites. Connection methods were adopted from the steel industry, tested for strength, and then published – there is historical precedence and proven performance using mechanical connections.
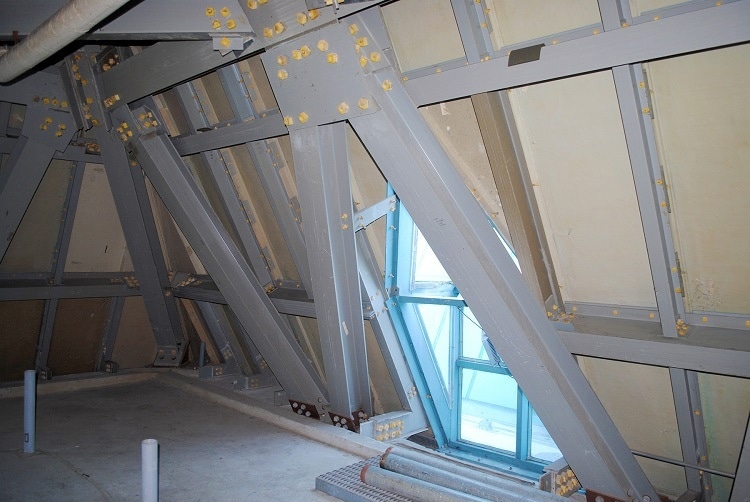
When designing mechanical connections, engineers refer to them as bearing-type connections? Why?
Bearing-type connections are connections where the bolt, screw, or rivet “bear” on the inside of the pultruded composite drilled hole. Forces in the connection are transferred through this contact between the mechanical connector and pultruded composite.
How do you determine the strengths of these connections? Why is this important?
Strength is determined from the pin-bearing strength of the pultruded composite, and this strength is determined by following an ASTM Test Standard. Known strength is important since engineers need the pultruded composite strength to design connections.
Mechanical connections include resistance to tensile and compressive forces, but what about the well-known rigid, or semi-rigid, steel connection (“moment connection”) that offers rotational strength, bearing and shear strength and stiffness in a mechanical connection?
This type of connection has yet to be developed by the pultruded composites industry. It can be achieved, but design methods need to be developed. Braced frames using x-bracing or knee-braces are the current, typical construction type for pultruded composite structures.
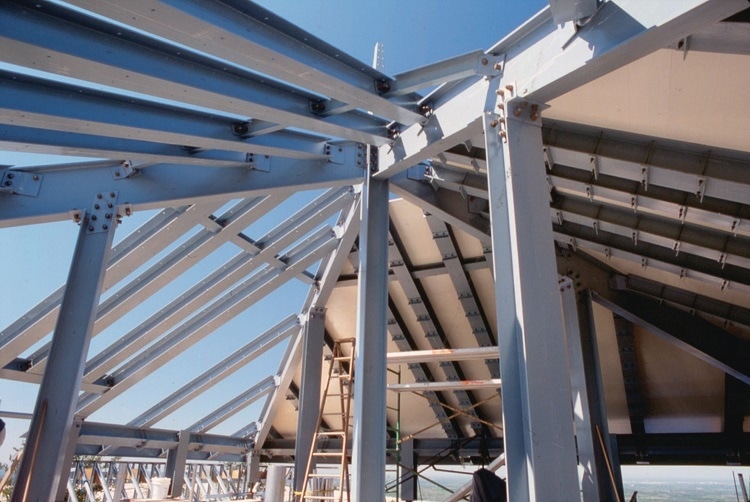
Why would the pultruded composites industry benefit from having a semi-rigid composite design and manufacturing? Why is it difficult and uncommon in this industry?
Methods for rigid, or semi-rigid connections, as seen in the steel industry, would be beneficial for conditions where the structure cannot have x-bracing or knee-braces, and this condition does occasionally occur. It’s uncommon simply because a design method has yet to be standardized and published.
Why are epoxy and resins often an exception?
With respect to pultruded composites, adhesives alone in connections are often the exception due to the long-term reliability of this type of connection being in question, and the requirements for achieving a reliable bonded connection. Other factors include loading, the type of structure in question, the life expectancy of the structure, etc.
Additionally, consideration of environmental conditions such as humidity and temperature are critical for bonded connections, and often require these connections to be performed indoors and allowed to cure over time. Mechanical connections can be completed quickly, compared to bonding alone, with little or no regard for environmental conditions.
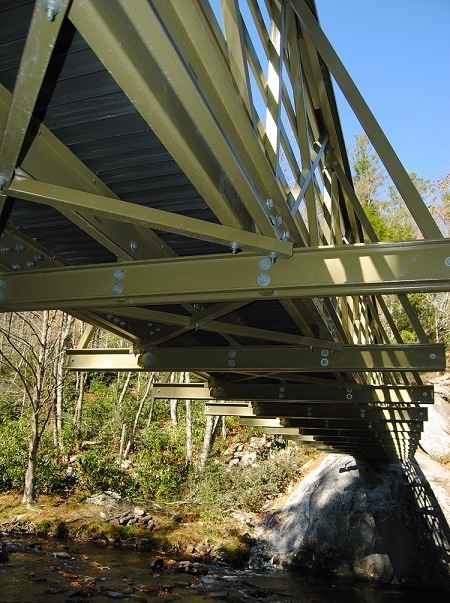
What is a common method for increasing the strength and durability of a traditional mechanical connection?
A common method for increasing strength and durability of a traditional mechanical method is to include bonding of the pultruded composites with the mechanical connection. This allows for an increase in strength, and structural redundancy in a bonded and bolted connection, for example.
Why are epoxy resins often used in connections between composites and between composites and other materials assembled with bolts and adhesives?
From what I have observed, epoxy resins are a commonly chosen adhesive; however, other adhesives are available such as urethanes and methyl methacrylates, which often are chosen due to limitations of epoxy adhesives.
Brittle behaviour, chemical exposure, in-service temperature exposure, and strength are typical subjects of concern when choosing an adhesive.
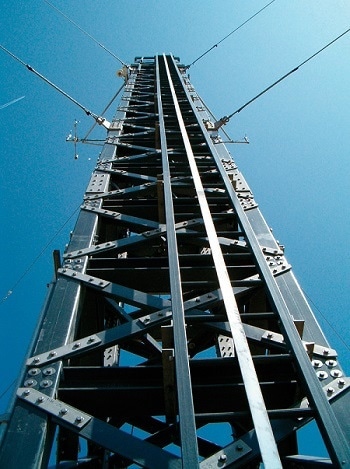
Why is reliability of bonded connections more difficult to achieve when using epoxy resins or similar resins?
The two main contributing factors are environmental conditions during assembly of pultruded composites and the service conditions while the pultruded composite structure is in use. As mentioned previously, humidity, temperature, and preparation of the connection are critical factors to be considered for achieving a successful bonded connection.
Mechanical connections can be completed quickly, compared to bonding alone, with little or no regard to environmental conditions.
Where can our readers go to find out more?
More information can be found on the American Composites Manufacturing Association website and participating company websites, such as the Strongwell website.
About Stephen Browning
Stephen Browning is a licensed professional engineer with approximately 17-years of experience in structural analysis and design, including wood, steel, concrete and pultruded composites.
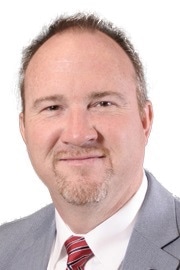
Currently, he is the structural engineer located at the Strongwell Corporate Offices in Bristol, Virginia.
Disclaimer: The views expressed here are those of the interviewee and do not necessarily represent the views of AZoM.com Limited (T/A) AZoNetwork, the owner and operator of this website. This disclaimer forms part of the Terms and Conditions of use of this website.