Interview conducted by Mychealla RiceNov 27 2017
In this interview, Dr Michael B. Simpson Industry Manager, at ABB Measurement & Analytics talks to AZoM about their new on-line optical spectrometers for process optimization in oil and gas applications.
Why is process control and optimization so critical in refining, petrochemicals and downstream oil and gas?
Refineries face a very difficult balancing act in the context of a highly dynamic problem. Planning and scheduling the arrival of crude oil feedstocks with optimum crude qualities, at best cost and availability, with best potential for crude blending to fit the refinery crude distillation profile, whilst simultaneously meeting the market requirements for specific final blend ed products, in the right volume, just matching product specification requirements without excessive giveaway or need for prolonged demurrage is a significant challenge.
To do so with maximized profitability adds an extra dimension of complexity. In typical refining operations there are multiple levels of optimization starting at the whole-refinery LP model level and cascading down through planning and scheduling to individual process unit APC systems.
What are the key problems in refining? How can ABB help?
Refinery operations fall into four main operational sectors:
- distillation / fractionation,
- naphtha conversion,
- heavy oil upgrading
- final product blending
In addition there is a significant utilities infrastructure. Each of these areas present their own challenges. These may include distillation cut-point and rundown quality, catalyst or furnace severity control, energy requirements, hydrogen demand, variable process unit feed quality, changing requirements for unit rundown quality and of course optimization of final product quality during off-sites blending.
Introduction to TALYS continuous process analyzer
What tools and methods are commonly used?
Optimization requires control, and this can only be achieved if process information is available either through direct measurement or through inferential process models. At any level, there needs to be a basic measurement input to the control system.
This can be from a multiplicity of field measurement devices, feeding mass-flow, pressure & process temperature data into a complex inferential model, from which process stream qualities are derived and used to run the unit APC system.
Alternatively direct measurement process analysers can be used to determine stream qualities directly. These can be relatively simple physical analysers typically dedicated to a single process stream parameter or more complex spectroscopic or chromatographic analysers capable of providing multi-property data across multiple streams.
What’s special about optical methods for process stream analysis?
Whilst physical property analysers have the advantage of a rather direct link between their principle of measurement and the target property (for example an on-line distillation analyser does just what it says – it functions using a test distillation of sample) – this very directness often leads to a high degree of mechanical complexity, rather slow response and very significant maintenance demands and subsequent high cost of ownership.
This effect is multiplied across the necessarily large installed park of numerous different analysers, all with their own maintenance, spares and training needs, required to provide complete input to the unit APC system.
Analysers based on optical spectroscopic methods, on the other hand generally have a common and simple basic principle of operation, for all measured properties, and are characterised by very rapid response (typical stream cycle times less than 1 minute) and very high precision (typically multiple times better than physical property analysers on the similar application).
These attributes (fast, precise) are highly valuable as input data for APC systems, allowing tight closed-loop control and optimization.
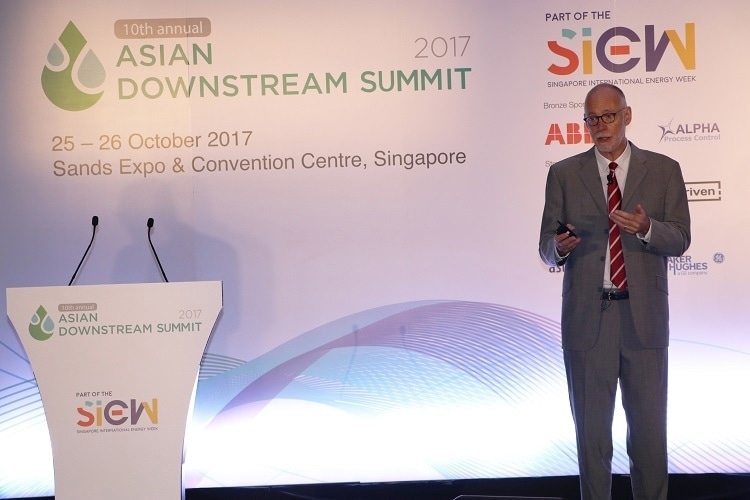
Tell us about the benefits of ABB’s range of On-Line Analyzers? What applications will benefit from the products?
ABB provides a range of on-line process FT-NIR analyser packages designed for use across a wide range of refinery applications and process units. The most significant applications are those covering the control and optimization of either very high volume operations (distillation, final product blending) or very high value process units (alkylation, catalytic reforming, hydrocracking).
FT-NIR works extremely well for the characterization of hydrocarbon liquid stream bulk properties, which can be chemical composition (e.g. PIONA, BTX) but also physical, ignition or cold-flow properties (e.g. D86 distillation, Kinematic Viscosity, Octane, Cloud Point etc.).
In addition to FT-NIR there is another ABB optical spectroscopic measurement technique (namely TDLS-ICOS) which is highly applicable to ultra-trace impurity measurement in gas-phase streams, which can be applied to certain critical downstream oil & gas measurements. These include ppm and sub-ppm level measurement of H2S, CO2, O2, C2H2 and NH3 in streams such as hydrogen recovery, steam-cracker ethylene product and bio-methane.
How can On-line FT-NIR and other analyzers help provide real-time data for the optimization of naphtha steam-cracking furnaces?
Steam-cracking of liquid naphtha feed is still an important and economically attractive source for global ethylene and propylene demand. The primary process control objective is real time furnace optimization, to best fit the furnace gas-make with the downstream quench, compressor and product separation capacities, whilst also maximising furnace run length by control of furnace tube coking.
This requires good real-time naphtha feed quality information, since naphtha feed transitions impact both the above parameters. On-line process FT-NIR is able to meet this need in a way which process GCs find difficult due to their extended elution times and hence very long cycle times for full PIONA analysis coupled with heavy routine maintenance requirements.
The FT-NIR analyser can feed forward to the furnace real-time optimizer PIONA, C-number breakdown and distillation curve properties within a 1 minute cycle time.
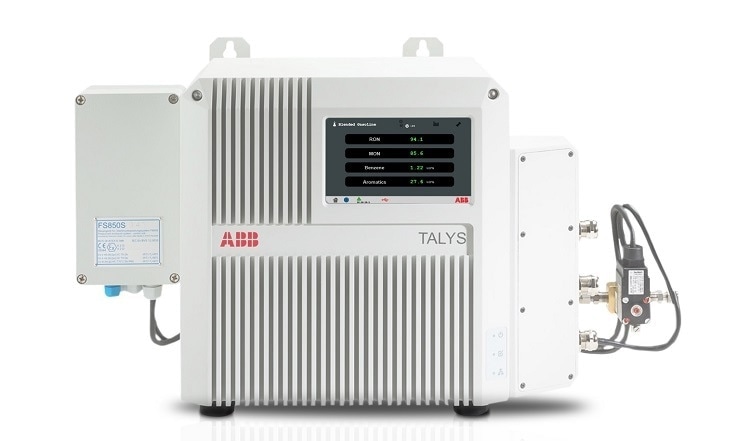
Image Credit: ABB Ltd.
What are the advantages of FT-NIR as a multi-stream, multi-property analytical method for CDU optimization?
Crude Distillation Units are sometimes quite good examples of cases where inferential process models based on simple physical transmitter data can work well, because at least in principle it’s possible to have a good rigorous chemical engineering model of the distillation column.
However there are often economically critical quality parameters which need to be monitored and controlled carefully across specific rundown stream cut-points. For example between LGO and HGO or LN and Overhead.
On-line FT-NIR analysers can be configured very flexibly – from simple single-stream analysers (example: TALYS ASP400-Ex) to multi-channel analysers (example: FTPA2000-HP260X) which allow the specific operationally critical direct process stream quality measurements needed for any particular CDU to be set up for implementation.
Getting the cut-point boundaries right, even during significant crude feed quality transitions can have huge economic benefits, due to the high-volume throughput of the CDU.
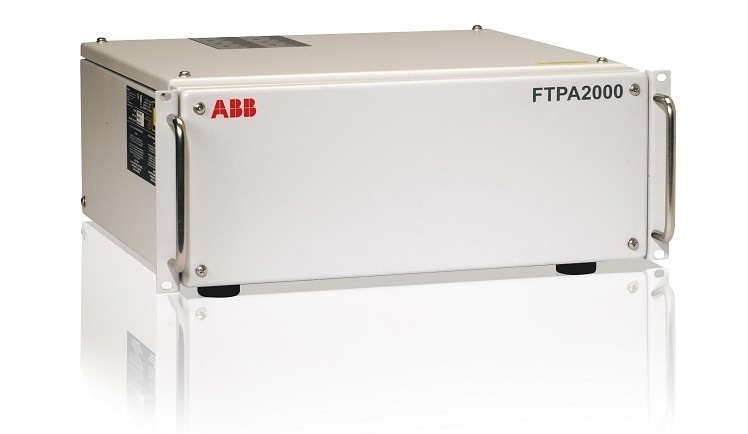
Image Credit: ABB Ltd.
How will ABB TALYS handle the optimization of CCR catalytic reforming units to balance requirements for gasoline growth, aromatic demand and refinery hydrogen balance?
Although the CCR catalytic reforming unit is one of the most ubiquitous, familiar and well-used process units, forming part of the naphtha conversion complex on nearly every refinery, in today’s economically dynamic environment it can still pose optimization challenges.
The CCR is classically a source of high-octane reformate used as MOGAS blending component – but it also generates net-gas hydrogen (and is one of the only hydrogen-generating standard process units) and its reformate product is high in useful aromatics / BTX components.
This means that flexible operation of the CCR (to maximise octane barrels, to achieve optimum BTX qualities and a petrochemicals feed, to match hydrogen net-gas production to help the refinery hydrogen balance or to gain longest catalyst run-lengths) can only be achieved with good real-time feed, product and net-gas stream quality data.
A combination of optical spectroscopic (FT-NIR) and solid-state (Sensor) techniques for heavy naphtha feed PIONA, product reformate RON, aromatics %, benzene %, BTX breakdown and net-gas hydrogen % can be used to achieve this.
Where can our readers go to find out more?
To find out more please visit our site http://new.abb.com/products/measurement-products
For more information on the products please visit http://new.abb.com/products/measurement-products/analytical/ft-ir-and-ft-nir-analyzers/process-spectrometers/talys-asp400-series & http://new.abb.com/products/measurement-products/analytical/ft-ir-and-ft-nir-analyzers/process-spectrometers/ftpa2000-hp260x
About Dr Michael B. Simpson
Dr Michael B. Simpson has been involved with on-line FT-NIR and other optical spectroscopic technologies for over 20 years, working with ABB as Applications Chemist, Technical Support.
For the past 10 years as Industry Manager responsible globally for the Refining, Petrochemicals and Downstream Oil & Gas business sector with the process on-line FT-NIR analysers available from ABB PMU Quebec, Measurement & Analytics.
Dr Michael B. Simpson has a background in chemistry and analytical spectroscopy.
Disclaimer: The views expressed here are those of the interviewee and do not necessarily represent the views of AZoM.com Limited (T/A) AZoNetwork, the owner and operator of this website. This disclaimer forms part of the Terms and Conditions of use of this website.