High temperature vacuum furnaces are mainly used for heat treatment of samples under partial gas atmospheres and at low pressure (down to 10-6 mbar). The bottom is lowered in the bottom loader version and pushed out from the furnace. It then pivots forward to allow easy loading. This design not only makes the useable volume accessible from all sides but also enables the exact placement of sample thermocouples which measure the sample temperature.
The HTBL series from Carbolite Gero is available for temperatures as high as 2200 °C and for working spaces with volumes from 50 l to 200 l. The furnaces are specifically designed for operation under vacuum. Any pressure between 10 and 1000 mbar can be controlled through an integrated pressure control with a precision of about ± 2 mbar. The pressure control works independently of the supplied gas volume which can be defined for each level of the process. At low pressure, for instance, both high and low gas volumes can be supplied. The pressure control offsets the resulting uncertainty.
The furnaces are also equipped with optical pyrometers and redundant thermocouples to guarantee high process stability. The controller performs plausibility checks independently and, if the optical pyrometers and thermocouples deliver improbable measurement results, switches to the redundant measuring unit. These thermocouples are used from room temperature up to 1200 °C but over that temperature all thermocouples are automatically removed from the furnace for protection, and the system automatically switches to operation with optical pyrometers.
These have a measuring range from 350 °C to 2200 °C. The sample batch can be closely monitored and the temperature profile can be recorded by using four independent optical pyrometers per furnace. Combined with a Siemens controller S7-300 (SPS), the exacting thermal processes can be reliably programed, monitored and controlled. Following this, the process data are viewed on the integrated PC monitor (WIN CC).
Features
- Graphite and metallic versions available, based on required atmosphere, maximum temperature, and cross contamination with sample
- Water-cooled container with useable volumes up to 200 l
- High vacuum up to 5 x 10-6 mbar
- Ultrapure process chamber
- Hydrogen partial pressure between 10 and 1000 mbar possible
- Sample accessible from all sides
Application Examples HTBL
Annealing, hardening, quenching, tempering, degassing, brazing, siliconization, pyrolysis, rapid prototyping, carbonization, sintering, debinding, sublimation, synthesis, and drying.
Synergies Between Research and Industry
CARBOLITE GERO, along with the German Aerospace Centre “Deutsche Zentrum für Luft- und Raumfahrt (DLR)” in Stuttgart, Germany, has built two high temperature vacuum furnaces for industrial production of carbon/carbon-silicon/carbon components through siliconization ad pyrolysis for the Norwegian customer Nammo Raufoss AS.
The furnaces are used for running high temperature processes in the production of mechanically and thermally heavily strained functional components made of fiber-reinforced ceramics.
Material
The finished C/C-SiC material includes load-bearing C/C bundles that are embedded in a SiC matrix. Typical characteristics of C/C-SiC materials are as follows:
- Damage-tolerant (not brittle)
- High temperature and thermal shock resistance
- High mechanical strength at high temperatures
- Very low thermal expansion
- Very high abrasion and corrosion resistance
- Low density (1.9 g/cm³)
- Inner protection against oxidation
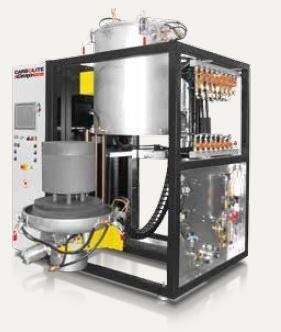
HTBL 50 GR
Method
1. After mixing the carbon fibers with (mostly phenolic) resin, the components are pressed into a rough form and are polymerized at 190 °C.
2. The following step involves carbonizing or pyrolizing the components in a protective vacuum or gas furnace. When heat is applied under nitrogen, the exhaust gases from pyrolysis are removed from the component and are fully combusted in an exhaust gas burner. The separate heating from the gas supply to the burner helps to prevent unnecessary accumulations. The atmosphere is changed from nitrogen to vacuum at about 900 °C and carbonization is performed up to a maximum temperature of 1650 °C.
3. After cooling down, the open-porous C/C (carbon/carbon) components generated by pyrolysis are removed from the furnace for quality control.
4. Next, the C/C components are introduced into a siliconization furnace and stacked in crucibles on the base plate. The component as well as the required amount of granulated silicon for the siliconization process is weighed in the crucible. Above the crucible, a retort is mounted to protect the furnace from the silicon vapor which is generated at working temperature. The actual siliconization process occurs at temperatures above the melting point of silicon (about 1650 °C). The process is carried out in vacuum; the liquid silicon infiltrates the porous C/C component exclusively through capillary forces. Therefore, the component is completely saturated with liquid silicon which reacts to SiC with a small part of the carbon at the inside contact surfaces.
Distinctive Features
The unique bottom loader design with additional floor heating guarantees optimum temperature distribution within the furnaces. With the help of a graphite retort, the gas supply can be adjusted in a way to avoid contamination to a great extent. Not even the gas outlets require cleaning. All pyrolysis products are combusted. Due to the fully automatic process, the only operational activities are loading and unloading the furnace.
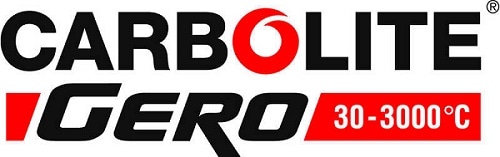
This information has been sourced, reviewed and adapted from materials provided by CARBOLITE GERO Ltd.
For more information on this source, please visit CARBOLITE GERO.