Introduction
Adhesives have become essential in today’s world and are used in a number of applications. In the automotive industry, windshields, seating elements, front consoles, and car body parts are glued with special automotive adhesives which have resulted in considerable weight savings. In medicine cyanoacrylate, which is popular for its use as superglue, is applied for rapid bonding of wounds. Currently, adhesives with tailored properties in terms of strength and curing time are available for various applications. Modern adhesives are often complex mixtures of various resins, solvents, additives, and fillers. For consistent product quality, it is essential to inspect both the raw materials and the finished product and to test both physical and chemical properties.
FT-IR spectroscopy is a useful analytical technique for a variety of questions in the development, production and quality control of adhesives. The method is ideally suited for both the testing of quality and identity of the incoming raw materials and the examination and quantification of the finished product. In the product development, IR-spectroscopy allows for the analysis of the composition of a competitive product and for the monitoring of the curing process of an adhesive. The IR microscopy is a powerful technique for failure analysis, as it can analyze and visualize even the smallest product defects in the micrometer range.
Keywords |
Instrumentation and Software |
Adhesives |
LUMOS FTIR microscope |
Quality control |
ALPHA II FTIR spectrometer |
Failure analysis |
OPUS spectroscopic software |
Reaction monitoring |
|
Reverse engineering |
|
Bruker provides the right equipment for product development, incoming goods inspection, and quality control with the ALPHA II FTIR spectrometer. The spectrum of a substance can be measured within seconds with no sample preparation, consumables, or reagents.
By using the LUMOS FTIR microscope, even microscopic samples such as particles, defects, and inclusions can be analyzed often without any sample preparation. The spatially resolved investigation of adhesives is especially helpful in the analysis of product defects since the cause for the defects is usually punctual inhomogeneities, impurities, or inclusions.
Incoming Goods Inspection with the ALPHA II FTIR Spectrometer
Figure 1 shows the ALPHA II which is a very compact spectrometer that can be adjusted to various requirements via interchangeable measurement modules. The most commonly used measurement technique is the so-called attenuated total reflection (ATR). The ATR technique is a very comfortable and fast measuring method as there is no need for sample preparation. For measuring an IR spectrum, the sample only needs to be brought into contact with the ATR crystal. For checking the identity of a raw material, the spectrum is automatically compared against one or more reference spectra using the quick compare function of the OPUS spectroscopy software.
.jpg)
Figure 1. LUMOS FTIR microscope and ALPHA II FTIR spectrometer (detail).
This example illustrates the quality control of an amine curing agent of a two-component epoxy resin using the OPUS quick compare function. In Figure 2, the incoming raw material (blue spectrum) is compared against a previously measured spectrum of a reference sample (red spectrum). A correlation value of over 99% shows that the sample spectrum is in very good agreement with the reference spectrum. Since the correlation of the sample and reference spectrum is higher than the predefined threshold value of 98%, the sample is rated with an “OK.”
In addition to the shown comparison against one single reference spectrum, comparison against an average spectrum of many reference spectra is also possible in order to model product tolerances. As a third option, comparison against a set of different substances can also be done.
.jpg)
Figure 2. Incoming goods control: The result of the spectra comparison of an amine hardener (blue) against an according reference spectrum (red) verifies the correct identity of the material.
Measurement of the Curing Time of an Adhesive with the ALPHA II Spectrometer
This example shows the reaction monitoring of an adhesive with the ALPHA II spectrometer. By using the reaction monitoring function of OPUS, one can monitor the whole curing process with a time resolution down to one second.
The following section shows the curing of a plastic adhesive. The adhesive is mainly made up of acetone, butyl acetate, and poly methyl methacrylate (PMMA). For the measurement, a small drop of the adhesive was placed on the diamond crystal of the ATR unit. A spectrum was then automatically measured every 30 seconds. The temporal evolution of the components PMMA and butyl acetate is shown in Figure 3.
The evaluation was performed by integrating the spectral bands that are specific for PMMA (1144 cm-1) and butyl acetate (1040 cm-1). The concentration of PMMA (blue curve) increases as expected because of the evaporation of the solvent whereas the concentration of butyl acetate (red) shows an increase before the continuous decrease. This increase is due to the fast evaporation of the acetone in the first minutes. As a result, the concentration of the slowly evaporating butyl acetate increases initially. At the end, after the complete evaporation of the acetone, the butyl acetate concentration also decreases. The 3D-plot in Figure 3 (left) illustrates the temporal evolution of the butyl acetate-band around 1040 cm-1.
.jpg)
Figure 3. Screenshot of a reaction monitoring of the curing of a plastic glue. Left: 3D plot of the spectra vs. time. Right: Concentration change of butyl acetate (red) and PMMA (blue) calculated from the spectral change during the curing process.
Reverse Engineering of an Adhesive
The analysis of competitive products can aid the development of own products and can help identifying patent infringement. The spectrum search in reference libraries is used to identify the unknown materials. The OPUS spectroscopy software also has a mixture analysis function to identify single components in complex mixtures. This example illustrates the analysis of a multi-purpose glue with an unknown composition. A drop of the glue was placed on the diamond crystal of the ATR unit, measured and finally evaluated with the mixture algorithm. Figure 4 shows the result of the mixture analysis:
.jpg)
Figure 4. Result of a mixture analysis of an unknown adhesive. The composite spectrum (blue) calculated from the identified components shows a good match with the sample spectrum (red). The difference spectrum between composite and sample is shown in green.
The composite spectrum (shown in blue), calculated from the identified single component spectra, has a very good agreement with the measured query spectrum. Thus, the difference spectrum (green) from the query- and composite-spectrum shows only small deviations. In summary, it is a water-based adhesive with acrylate polymers.
Failure Analysis with the LUMOS FTIR Microscope
The LUMOS FTIR microscope (Figure 1) is a powerful tool for the analysis of product defects. It allows for the measurement of an IR-spectrum anywhere on the sample with high lateral resolution and thereby identifying the chemical composition of a defect. Thanks to the brilliant performance of the LUMOS when measuring in ATR, the FTIR microscope can analyze most samples without preparation. By virtue of its intuitive user guidance and complete automation, the LUMOS is very easy to operate.
Here, the sample is a piece of hardened adhesive on a piece of PET-foil, which shows microscopically small white needle-like crystals.
For the investigation, the sample was secured in a sample holder and a smooth sample cross section was produced using a scalpel. As the defect was only barely visible with unpolarized light, the LUMOS’ motorized polarizers were employed for contrast enhancement. In the following, an automated grid measurement analyzed a sample area of 375 x 250 μm where 15 x 10 points were measured with an aperture size set to 25 x 25 μm. The spectra acquired can be converted into so-called chemical images by mathematical methods (integration, cluster analysis, factorization), which help to conclude the local chemical composition of the sample. Figure 5 shows representative spectra of the pure adhesive in blue and crystalline defect in red.
The enlarged view reveals the spectral differences and also the band at 1680 cm-1 which has been integrated to visualize the chemical image in Figure 6.
.jpg)
Figure 5. Spectra of the hardened adhesive (blue) and the crystals (red) show distinct differences.
.jpg)
Figure 6. Superimposed chemical image on top of the visual microscopic image of an adhesive layer. The chemical image was generated by integration of a spectral band around 1680 cm-1 which is characteristic for crystals that were formed inside the layer.
Based on the additional band at 3267 cm-1 it can be concluded that the contamination is possibly due to a nitrogen-containing compound (e.g. an amide).
The crystalline substance’s spectrum was compared with a reference substance’s spectrum which was suspected to be the cause of the defect (Figure 7). Since the crystals’ specific spectral characteristics are completely different from those of the reference spectrum, it is obvious that the suspected substance was not the reason for the observed product failure.
.jpg)
Figure 7. Spectrum of the crystals in the defect (red) in comparison with a reference sample (black). The specific spectral characteristics of the crystals are different from those of the reference spectrum.
Conclusion
The FTIR spectrometer ALPHA II provides a variety of possible applications in adhesive analysis. Moreover, FTIR spectroscopy enables monitoring the analysis of competitive products and the reaction of adhesives in addition to quality control of the product and incoming goods inspection. Using the LUMOS FTIR imaging microscope, inclusions and defects in adhesive surfaces can be analyzed with an achievable resolution in the range of only a few micrometers.
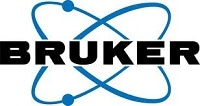
This information has been sourced, reviewed and adapted from materials provided by Bruker Optics.
For more information on this source, please visit Bruker Optics.