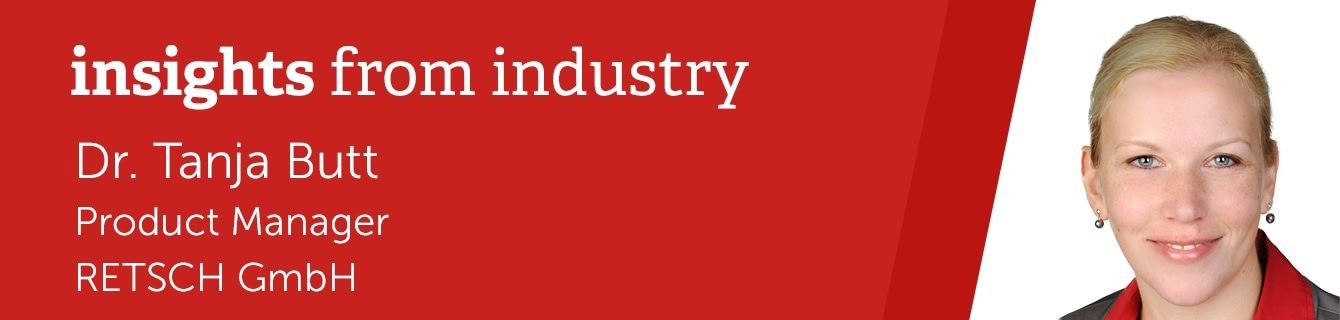
Grinding materials to a nano-scale is an important aspect of quality control and R&D. AZoM speaks to Dr. Tanja Butt from RETSCH GmbH about the benefits of using High Energy Ball Mills instead of Planetary Ball Mills.
What was the background for the development of your High Energy Ball Mill, the Emax?
In laboratories worldwide, Planetary Ball Mills are frequently used, for both, quality control and R&D. They have a reputation to be the best mills to grind semi-hard to brittle samples to very fine particles in the nanometer range < 100 µm, always depending on the sample´s properties. However, such grinding processes can easily take several hours, again, depending on the sample material. With increasing speed, which means also increasing energy input, the chance to obtain actual nano-sized particles increases, but also the risk of warming and rising pressure inside the grinding jars. A practical solution to avoid that problem – especially for temperature-sensitive materials - is to interrupt the grinding process and work with cool down breaks. This, however, increases the total process time usually by factor 2-4. Furthermore, the energy input of Planetary Ball Mills is limited, again due to the warming effects and forces inside the machines. Consequently, not all materials can be ground to nanometer size. To offer a solution, RETSCH developed the High Energy Ball Mill Emax – which is able to grind many different substances to particle sizes < 100 µm and usually in a much shorter time than required by other ball mills. Ideally, the grinding breaks can be skipped altogether, which results in enormous time savings.
What is the working principle of the Emax?
The Emax is an entirely new type of ball mill for high energy milling. The unique combination of high friction and impact results in extremely fine particles within a very short process time. The high energy input is a result of the extreme speed of 2000 min-1 and the optimized jar design. Thanks to the revolutionary cooling system with water, the high energy input is effectively used for the grinding process without overheating the sample. Due to the special grinding jar geometry in combination with the circular movement of the jar – with fixed orientation - the sample is thoroughly mixed which results in a narrow particle size distribution. The grinding jar supports are mounted on two discs respectively which turn in the same direction. As a result, the jars move on a circular course without changing their orientation. The interplay of jar geometry and movement causes strong friction between grinding balls, sample material and jar walls as well as a rapid acceleration which lets the balls impact with great force on the sample at the rounded ends of the jars. This significantly improves the mixing of the particles resulting in smaller grind sizes and a narrower particle size distribution than has been possible to achieve in ball mills so far. The time required to obtain a specific particle size is often less than in a Planetary Ball Mill, even in processes where no interruption in the grinding times are required in Planetary Ball Mills, thanks to the more efficient grinding mechanism.
High Energy Ball Mill Emax #RETSCH #highenergyballmill #laboratoryinstruments
How does the Emax combat cooling interruptions?
The greatest challenge when developing a high energy ball mill is keeping the temperature under control as the enormous size reduction energy leads to considerable heat built-up inside the grinding jar. RETSCH solved this problem with an innovative integrated water cooling system. Hence, the Emax usually doesn’t require cooling breaks which are typical for long-term processes in conventional ball mills, even at low speed. This dramatically reduces the grinding time. The cooling system cools the grinding jars via the jar brackets. This is very effective because heat is more easily discharged into water than into air. The user can choose between 3 cooling modes: in addition to the internal cooling, the mill can be connected to a chiller or the tap to further reduce the temperature. For temperature-sensitive samples, the Emax has a great benefit over Planetary Ball Mills. The software allows the user to carry out the grinding process within a defined temperature range, i. e. it is possible to define a minimum and a maximum temperature. On reaching the maximum temperature, the mill automatically interrupts the grinding process and resumes it when the jar has cooled down to the minimum temperature.
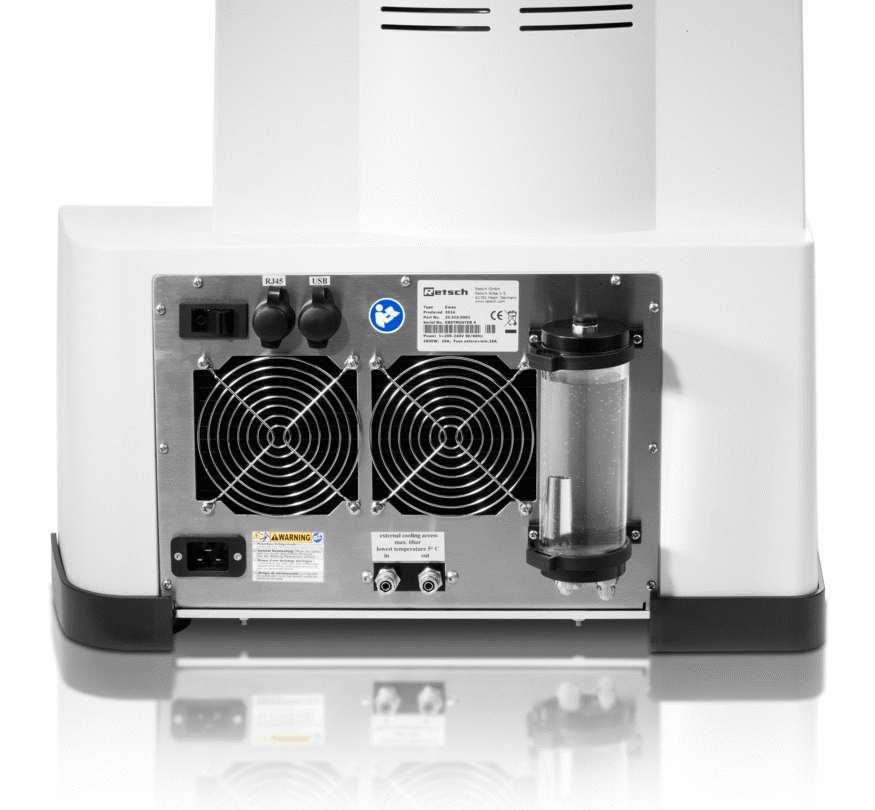
Behind view of the Emax (Credits: RETSCH GmbH)
Where is the benefit (despite the time saving thanks to the more efficient grinding mechanism) over Planetary Ball Mills, if the operator decides to operate the Emax also with grinding breaks?
When using conventional ball mills the adequate cycles of grinding and cooling need to be ascertained by empirical trials. This may lead to degeneration of the sample or to unnecessarily long processing times. The Emax, in contrast, allows for variable cycles of grinding and cooling within the defined temperature limits. Thus, the entire size reduction process remains reproducible and is carried out in the shortest possible time.
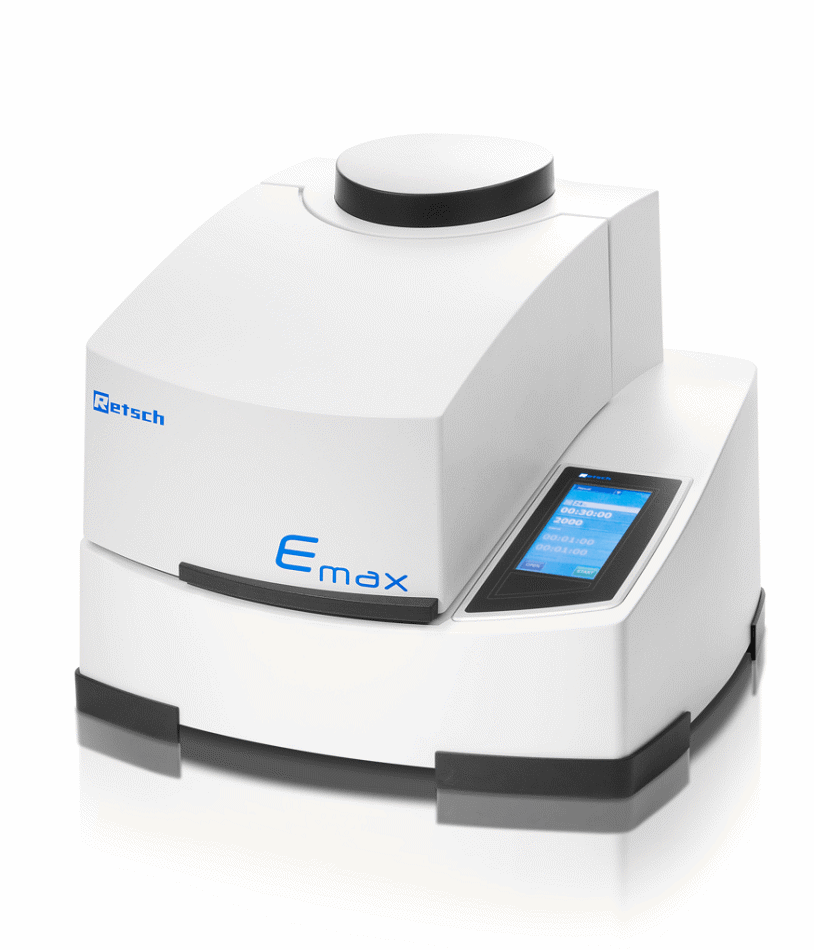
Emax (Credits: RETSCH GmbH)
What final particle sizes can be obtained by using the Emax?
The final size of a certain material always depends on the sample´s chemical and physical properties. Hard and brittle samples like quartz or some types of pigments can truly be ground to a nanometer size which means D90 < 100 nm! For example, barium titanate or titanium dioxide can be pulverized to D90 < 90 nm. Other, more difficult materials, like the lubricant graphite, can be ground to smaller sizes (D90 = 2.8 µm) than in a Planetary Ball Mill. In principle, the Emax reaches final sizes similar to or better than those which are obtained in Planetary Ball Mills.
How simple is the Emax to use and to clean, what about safety?
Special focus was placed on operating convenience and safety when developing the Emax. The grinding jar lids with integrated safety closure, which are simply screwed onto the jars, ensure absolute tightness for wet grinding processes or in cases of pressure increase inside the jar. The grinding jars are quickly and easily placed in the mill and are safely clamped with the ergonomic hand wheel. A sensor monitors the correct position of the jars before starting the machine. Possible imbalances are permanently monitored; if they become too strong the mill stops automatically and the remaining grinding time is displayed. Grinding parameters such as speed, time, interval operation or temperature control are quickly and conveniently set via the color touchscreen. The temperature is displayed during the entire grinding process. The user can store up to 10 grinding programs for routine operations.
High Energy Ball Mill Emax - Handling #RETSCH #highenergyballmill #laboratoryinstruments
Are there any other areas except grinding in which the Emax performs well?
Yes, definitely! A huge application field for the Emax is mechanical alloying mainly for R&D. For materials which cannot be alloyed by fusion, mechanical alloying is carried out in ball mills which provide high energy input through impact and friction. Trials have shown that the alloying process in the Emax takes considerably less time than in, for example, a Planetary Ball Mill. Further advantages include a better transformation rate as well as less amorphous particles and less caking of sample material in the jar.
Which equipment is available for the Emax?
A wide selection of accessories makes the High Energy Ball Mill a versatile instrument.There are grinding jars of three different materials – stainless steel, zirconium oxide and tungsten carbide - ensuring contamination-free sample preparation. The first two materials are available in 50 ml jars and in 125 ml jars, tungsten carbide is available 50 ml jar. RETSCH offers a special aeration cover for the grinding jars designed for applications where a special atmosphere is to be maintained in the jar. The grinding balls are available in stainless steel, tungsten carbide and zirconium oxide. Sizes range from 0.1 mm to 15 mm, depending on the material. By selecting the adequate ball numbers and sizes, a wealth of applications can be covered. By continuously measuring pressure and temperature the processes and reactions which take place inside the grinding jar during grinding can be monitored and recorded.
What advantages does the Emax have over Planetary Ball Mills?
The Emax is not a Planetary Ball Mill – it is much more. Higher speed, less warming, finer particles, faster grinding procedures. The high energy input in combination with the unique cooling system provides perfect conditions for effective mechanical alloying or grinding down to the nanometer range. To sum it up, the Emax is faster - finer -cooler!
Why should our users use RETSCH products?
With more than 100 years of experience RETSCH is the leading solution provider for size reduction and particle sizing technology worldwide. Our philosophy is based on customer orientation and leading-edge technology. This is reflected in instruments whose high-quality components are designed for perfect interaction. Our products not only guarantee representative and reproducible results for size reduction and particle analysis but also allow for easy and comfortable operation. With RETSCH you get: First class product quality thanks to advanced manufacturing methods; Comprehensive application support including free test grindings and product trainings; Excellent sales and service network throughout the world.
videoanimation emax 640x360
Where can our readers find out more about the Emax and RETSCH?
The RETSCH website www.retsch.com provides all the details, including a product video of the Emax and an application database. We can also be found at many different trade shows all around the world or people may visit one of our end-user workshops or seminars. To keep our customers up to date with the latest dates and news, we send out a newsletter on a regular basis.
About Dr. Tanja Butt
Dr. Tanja Butt studied Biology at the University of Duesseldorf, Germany, and graduated with a Diploma in Biology. After that she earned her PhD in biotechnology at the Forschungszentrum Juelich, Germany. Later, she worked in R&D and project management for different institutions. She joined Retsch in 2013 as Product Manager for the whole milling and sieving product range.
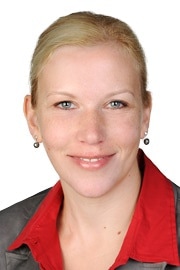
Disclaimer: The views expressed here are those of the interviewee and do not necessarily represent the views of AZoM.com Limited (T/A) AZoNetwork, the owner and operator of this website. This disclaimer forms part of the Terms and Conditions of use of this website.