
Even a few years back, standard CO2 lasers were utilized by major manufacturers in factories for welding applications. Massive systems installed in separate rooms away from the actual production process supplied the energy for what was comparatively new laser welding technology at that time. Since then, there have been continuous developments, and modern systems are increasingly using solid-state lasers, which offer a range of major advantages.
People who know all about this can be found in tranquil Heubach, the headquarters of EMAG Automation, located a few kilometers from Schwäbisch Gmünd: they deal with laser technology every single day.
In 2008, we started to use solid-state lasers on our systems because the benefits they deliver compared to the established CO2 lasers are simply overwhelming.
Dr. Andreas Mootz, CEO of EMAG Automation GmbH
Dr. Mootz added,“We were definitely the pioneers who made solid lasers the tool of choice for welding precision parts such as gearbox components. The requirements on the system and process technology, in particular, and the requirements for clamping and equipment are much higher than with the CO2 laser.”
Benefit 1: Lower Operating Costs
Considering the running costs of laser welding systems, two components are mainly focused – the energy consumption of the laser and the cost of the gas, differentiated between the laser gas (laser medium) and the shielding gas for stabilizing the welding process. Besides gas consumption, expensive gas logistics increases the cost. The use of solid lasers such as the disk or fiber laser is enough to eliminate these issues. Most applications on EMAG systems use compressed air as the process gas, which does not impact the quality of the weld, although it produces a thin oxide coating on its surface.
In addition, the CO2 laser cannot compete with the solid-state laser in terms of energy consumption. A CO2 laser requires 56 kW of electric current to generate a laser capacity of 4 kW, whereas a solid-state laser just requires 17 kW, saving up to 70% of energy. Furthermore, a solid laser needs much less cooling. As a whole, a solid-state laser consumes approximately one-quarter the energy of a CO2 laser.
Benefit 2: System Layout
As laser welding systems often operate with short cycle times, usually just a few seconds, a massive part throughput rate is made possible. Integrating these laser welding systems into the material flow within the production process is therefore a significant factor.
The beam is guided on CO2 laser systems, or simply put the laser beam is “transported” to the welding lens by mirror systems. Therefore, the beam source, cooling units and machining station(s) must be close together. This leads to a series of drawbacks like the complicated feed and discharge of the parts for welding which makes it difficult to supply several welding stations with the same laser source. In practice, when disk or fiber laser welding systems are used, these problems do not occur because the space requirement is so low that they can be easily incorporated into existing production lines. The real laser source may be up to 50 meters from the system, as the beam can be guided with relative ease thanks to the transport fibers enabling the welding stations to be perfectly integrated into the material flow.
Benefit 3: Quality and Speed
Although falling costs and a better system layout are major benefits, it is pointless if the quality of the weld does not match that produced by a CO2 laser. Apart from this example, the welding speed can even be increased in many applications. This reduces both the cycle time and heat warping in the workpiece.
To conclude with, fiber / disk laser technology is more efficient than CO2 laser technology and has a faster welding speed. This means that disk or fiber lasers fully meet the present demands of component production for fuel-saving and lightweight motor vehicles.
No Laser Without Shadows
So far, only the benefits of using solid lasers were discussed, but are there any drawbacks?
Actually, we cannot say that there are any drawbacks compared to the use of CO2 lasers; what we have are challenges that must be overcome.
Dr. Andreas Mootz
Dr. Mootz added, “For example, the use of solid lasers makes for much greater precision than in the past. A beam position accuracy of less than 50 micrometers places heavy demands on the machine, workpiece holders and clamping devices, as well as on the focus and alignment of the laser’s lens.” EMAG ELC systems fully satisfy these demands. For example, when considering the increase of weld spatter through the use of solid-state lasers, perfectly customized tools are developed to fully cover the component. The question of retooling times arises when machining for different components. To address this, EMAG has found a simple but efficient solution on the ELC 160 system which features a tool bridge with up to three different tool sets and an integrated flue gas extractor, which enables performing retooling in a matter of seconds and is perfect for the highly flexible and highly productive manufacture of gearbox parts in large volumes.
It has been found that there is practically no alternative to the use of solid-state lasers on production laser welding systems for the manufacture of powertrain components. However, their use needs extensive expertise to package the benefits in a highly efficient laser system such as EMAG’s ELC series systems. This is a challenge that the experts in Heubach successfully master every day.
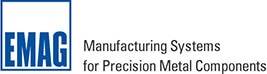
This information has been sourced, reviewed and adapted from materials provided by EMAG LLC USA.
For more information on this source, please visit EMAG LLC USA.
Laser Production Technology for Powertrain Components - Gas Lasers Vs Solid-State

The ELC 250 DUO – a compact laser production center for machining differential housings. The duo version of the ELC has twin spindles. This two-station mode allows the working spindles to be loaded and unloaded during the machining time.

Machining area of the ELC 160 laser welding machine for welding gears. The gear is heated, joined and laser-welded at up to three stations.

Laser welding a synchronizer to a gear. Half the running costs due to the new fiber laser in the ELC 160.