Dursox is a metal-free, high durability corrosion resistant coating that is ideal for protecting precision parts that need high tolerance and high heat resistance.
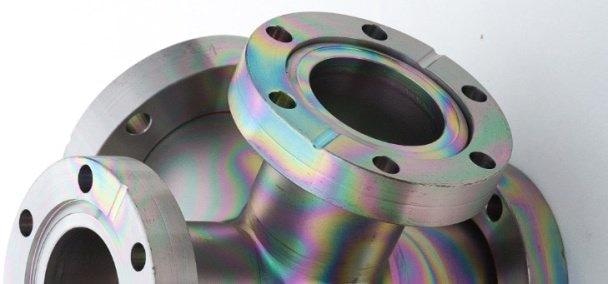
Is Dursox™ Metal Free?
X-ray photoelectron spectroscopy (XPS) was used to test if Dursox is metal free. The coating surface was irradiated with X-rays and the material coming off was analyzed. The analysis showed that Dursox consists of oxygen, carbon, silicon, and no metals. Since the coating is amorphous, it allows the coating to bend without cracking, enabling its use in high stress applications like compression seal fittings and high-pressure cylinders.
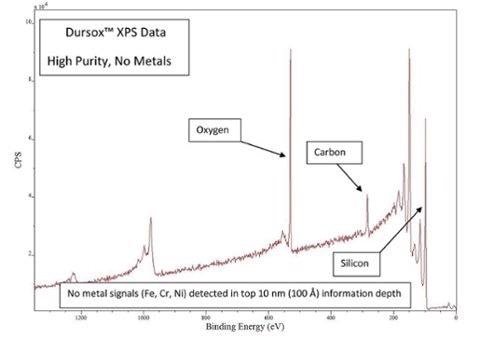
No Metal — Check. But Is It Corrosion Resistant?
The ASTM G31 hydrochloric acid immersion test was used to show the coating’s corrosion resistance. There was about 80% reduction in corrosion after 72 hours of testing compared to uncoated 316L stainless steel.
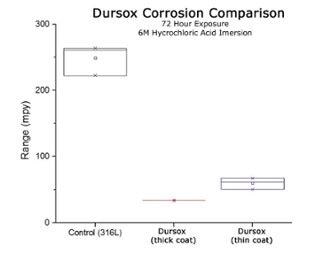
To check for metal ion contamination, an uncoated test sample was immersed in hydrochloric acid. If the clear acid turns green, it is a sign of chloride corrosion of the stainless steel and metal leaching, an example of metal ion contamination.
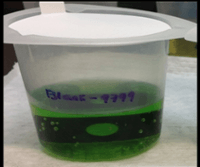
Several applications such as semiconductor processing and analytical testing are very sensitive to this contamination and lead to high maintenance costs, reduced yields, and low product quality.
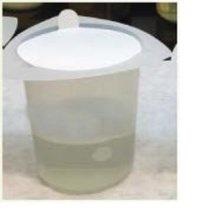
Dursox-coated samples, on the other hand, leave the beaker clear, i.e., no metal leaching. This gives accurate test results, improved flow path durability, lower maintenance, and good product quality.
Benefits
A Dursox coating makes important surfaces non-reactive and corrosion resistant, improving yield and preventing contamination during the process. This coating is better than ceramic coatings like yttria with higher stability, better adhesion, and higher durability. It is perfect for applications such as high purity gas transfer flow paths, high purity applications that require no corrosion, and in precision instrumentation.
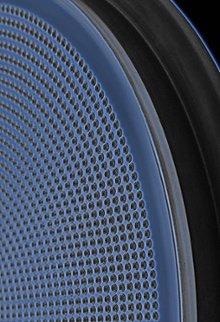
. |
. |
Etch |
High purity coating eliminates ion contamination in corrosive etch gas streams. |
Atomic Layer Deposition (ALD) |
Enhance purity by coating of all chambers and equipment. Reduces carryover, burn-in, and corrosion. |
Ozone |
Stabilize flow path to assure ozone purity. |
Gas Transfer |
Prevent ion contamination, assure high purity gases. |
Chemical-Mechanical Planarization (CMP) |
Increase lubricity, prevent sticking and cut downtime. |
Epitaxy |
Significantly reduces contamination and maintenance caused by corrosion |
Specifications
Dursox is a dry coating that will withstand high temperatures and extreme processing environments. It’s CVD coating technology is moisture-free and deposits a thin, high tolerance silicon coating on metals, glass, and ceramics.
Substrate compatibility |
SS alloys, ceramics, glass, titanium, most exotic metals,
TIG/MIG welds, vacuum-nickel brazed areas |
Allowable temperature range |
-210 to 1400 °C |
Typical thickness |
400–1600 nm |
Allowable pH exposure |
0–14 |
Coefficient of friction |
0.378 |
Contact angle |
40 ° |
Wear resistance |
6.13 (304 SS 13.81) |
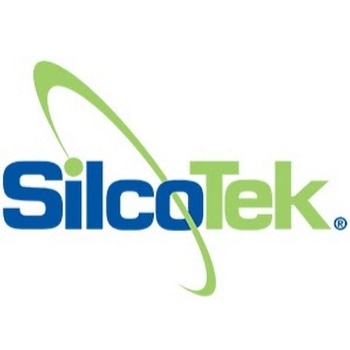
This information has been sourced, reviewed and adapted from materials provided by SilcoTek.
For more information on this source, please visit SilcoTek.