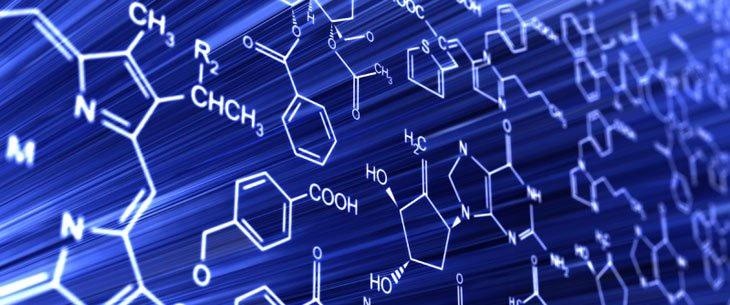
Bioseparation life sciences and HPLC applications cannot tolerate test uncertainty. A bioinert sampling flow path is critical for consistent bioseparations in medical diagnostics and HPLC studies. With continued use and use of aggressive chemicals, surfaces and test flow paths can corrode and degrade. Pitted surfaces cause sticky molecules like proteins to adhere to the surfaces, causing contamination and carry over.
Key Factors to Consider When Selecting a Coating for Bioinert Applications
Stainless steel is a common flow path material in medical diagnostics. But, it is prone to corrosion and can cause biomolecules to stick on its surface. Hence, different types of coatings are used to improve its performance. Commonly used coating materials like fluoropolymers (PEEK, AF1600) are not suitable for high durability applications, complex geometries, or small bore surfaces like needles, valves, and fittings. Several key factors are taken into account when selecting a bioinert coating.
Factors to Consider When Selecting Bioinert Materials
- No interaction with metal, improving analytical sensitivity
- Non-toxic, inert, and made using environmentally friendly processes
- Prevents non-specific protein binding for target proteins, prevents false positives
- Rust resistant and durable
- No change in part tolerance or performance upon coating
Dursan®, a carboxysilane CVD coating that is inert, non-sticky, and non-toxic, prevents protein binding, corrosion, and fouling in bioseparation applications. This was also proved by a recent study by Abbot Labs published in Applied Surface Science. A comparative analysis using a quartz crystal microbalance with dissipation monitoring of the Dursan coating showed a tremendous reduction in protein surface adsorption, preventing carry over and false positive results.
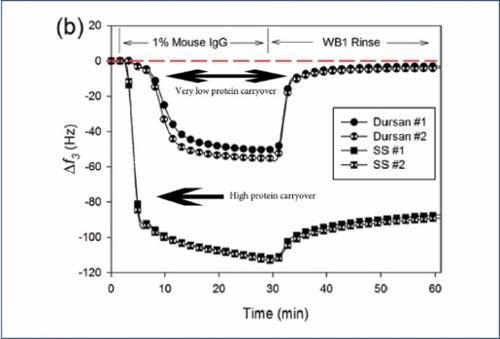
How Corrosion Resistance Can Improve Bioinertness
A pitted surface can hinder analyte flow and cause adherence of contaminants, resulting in significant system maintenance and failure. A chemical vapor deposited carboxysilane coating prevents analyte interaction with the stainless steel surface while maintaining part tolerance, and improves rust resistance by an order of magnitude. Hence, a high performance bioinert surface can protect the surface against pitting and improve rust resistance of stainless steel.
Dursan performs better than other coatings in ASTM bleach immersion studies. The coating prevents corrosive analytes or cleaning agents from contacting the surface.
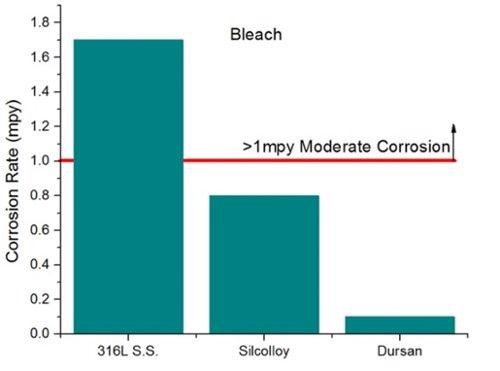
Prevent Fouling
Test accuracy and system flow performance can be improved by preventing buildup or fouling in flow paths. Dursan improves the rinse performance of surfactants, eliminating potential buildup. The benefits of an anti-fouling surface are:
- Biomolecules don’t stick to the surface
- A non-stick surface improves analytical sensitivity and reliability
- Reduce instrument downtime and increase efficiency
- Allow for complete rinsing with a non-ionic surfactant
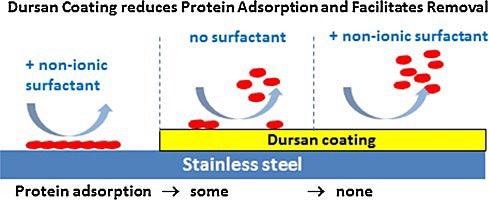
Coat Places Most Coatings Can't Reach
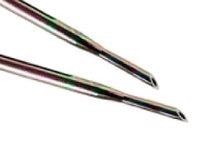
A coating should be able to work within the HPLC system tolerance and architecture, i.e., coat the inside and outside of flow path needles, tubes, and fittings without changing the flow or function. Such coatings should also not change the part tolerance or dimensions significantly.
Coating Durability
Surfaces of analytical instruments must survive hundreds of cycles of injection, abrasion, and surface wear but remain non-reactive. Coatings should not flake or crack under impact or flexion.
Abrasion Resistance Demonstration - Dursan® from SilcoTek®
Coating Applications for Optimizing Bioseparation
Some typical applications for high durability inert coatings in bioinert applications are:
Clinical chemistry and immunoassay analyzers, precision stainless steel tubing, mandrels, plungers, extrusion tips, dies, chemical vessels/containers, wires, wire coils, wire forms, guide wires, curettes, cannulas, screws, prostheses, plates, needles, syringes, sensor probes, catheters, knives, surgical tools, and lab surfaces
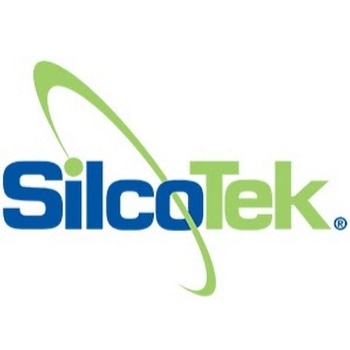
This information has been sourced, reviewed and adapted from materials provided by SilcoTek.
For more information on this source, please visit SilcoTek.