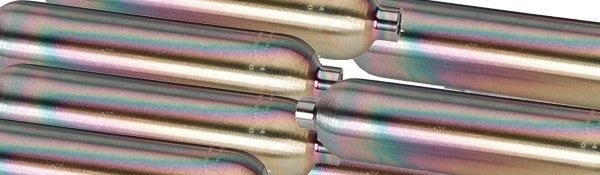
Making a new coating consists of 3 major steps: formulating the coating chemistry, setting up the process, and developing the application.
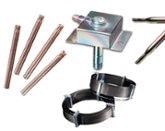
The Details of How to Make a New Coating
Making a new coating is the combined effort of R&D, engineering, manufacturing, quality, sales, and marketing right from the beginning as it is important to determine if customers need the coating you are making.
Coating Chemistry
A key part of coating development is understanding how different molecules interact and how they can enhance material properties. To do this, a well-staffed lab with PhDs and skilled technicians is necessary. Coating suppliers who do not have a lab might do experiments on the shop floor, which is not recommended at all. The lab should have all the necessary equipment to measure coating thickness, adhesion, composition, etc. Access to university materials testing labs is a big plus.
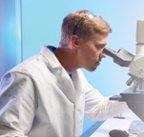
All new coatings start with an idea for a particular performance goal. After the initial formulation, a formal project plan detailing the key milestones, market research, test plan, coating objectives, etc. is prepared. Next is optimizing the coating, which requires the right tools, instruments, and materials. A staff of engineers with access to CAD software and a machine shop to develop the tooling is very helpful here, as is statistical analysis software for optimizing coating performance.
Once all this is done, it is time to develop the process.
Developing a Coating Process
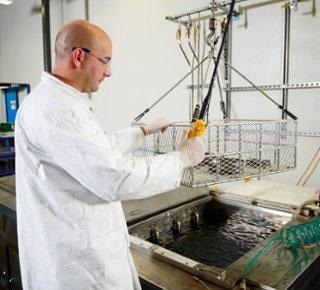
The process of making a coating starts early on during coating development, with the R&D team working with engineering, manufacturing, and quality to design the process. Developing a new coating process requires:
- Process design
- Material specifications
- Tooling design and specification
- Oven design and automation
- Chemical delivery system
- Statistical optimization software
- Process quality specs and quality inspection plan
- Process control plan
- Surface preparation spec
- Handling procedures
- Manufacturing technician training
- Ramp-up plan
Developing the Application
Along with developing the coating, the marketing and sales team work to target specific market segments and develop applications. This can sometimes take years, and evolve as more results are obtained.
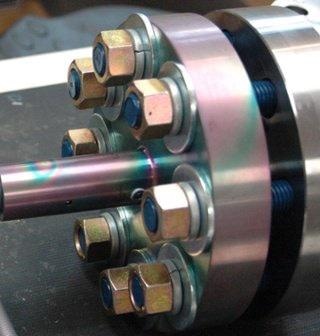
An example is the SilcoNert 2000 coating, initially called Sulfinert as it was targeted to customers in the sulfur analysis market. The coating was very effective in enhancing low-level sulfur detection. Quite a while after this, it was observed that the coating also prevented surface adsorption of many compounds and was inert. So, it was also named Siltek. After the company was spun off, the name SilcoNert was used.
Since then, coatings are released based on a few known applications, but they are continually evaluated throughout their life for other applications. This happens by conducting several experiments with interested partners. Some are easy, for example conducting salt spray testing for off-shore oil and gas applications. Some may take years, such as preventing certain protein markers from binding to stainless steel and causing contamination and carry-over.
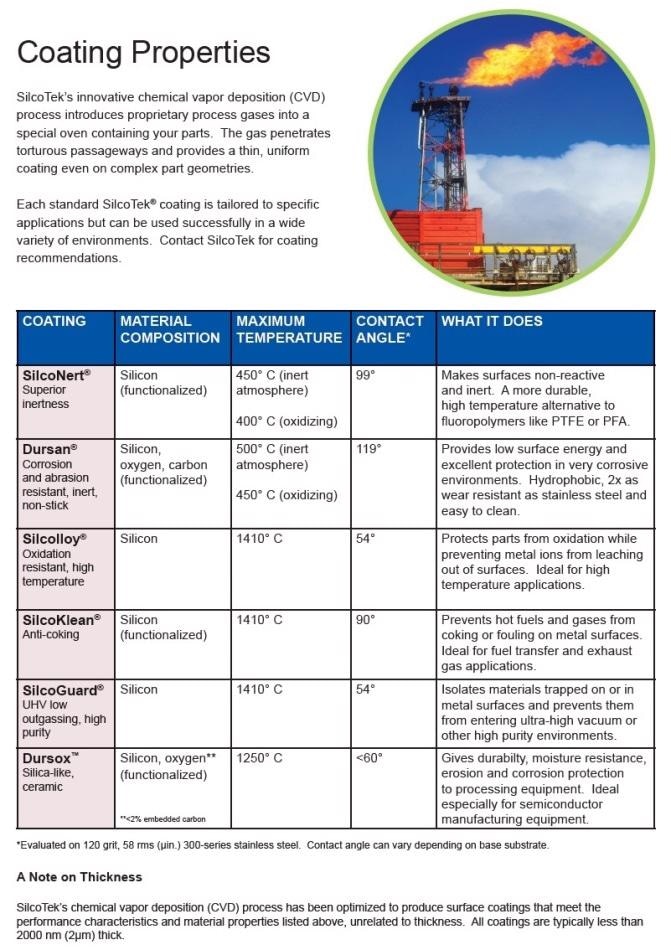
Once the process is approved, and the coating has been tested in a few key applications, the relevant data is made available and the marketing team takes over to create sales tools, literature, and website information.
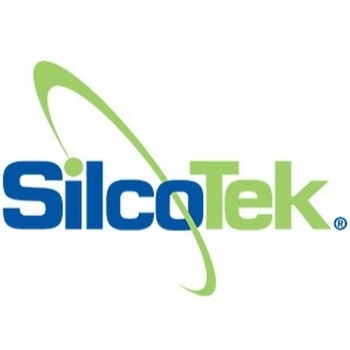
This information has been sourced, reviewed and adapted from materials provided by SilcoTek.
For more information on this source, please visit SilcoTek.