Duplex steels were first developed in the 1970s, and since then, their use has gradually increased. They are used particularly in the oil and gas industry, in the paper industry, for water systems, and for chemical tankers, where the content of much more costly nickel can be reduced by adding nitrogen, and production costs can therefore be reduced. This has meant that in the past 10 years, there has been a two-fold increase in the production of duplex steels. However, the quality of duplex steels must be strictly controlled as they are used in applications that are important for safety. Positive material identification (PMI) and precise material verification are provided by optical emission spectrometry (OES) technology to prevent serious consequences of material mix-ups.
.jpg)
Duplex, hyper-duplex, and super-duplex steels have a ferritic and austenitic structure, hence the term “duplex.” These are classified as stainless steels and can be distinguished from other steels by their excellent corrosion resistance, high structural stability, and outstanding weldability characteristics.
Elements |
C % |
Cr % |
Ni % |
Mo % |
N % |
Duplex |
<0.03 |
~20 |
~5 |
~3 |
0.08 – 0.22 |
Super-duplex |
<0.03 |
~25 |
~7 |
~4 |
0.15 – 0.4 |
Hyper-duplex |
<0.03 |
~30 |
~7.5 |
~4 |
0.3 – 0.6 |
Average composition of typical duplex, super-duplex, and hyper-duplex steels.
The Important Role of OES
The high nitrogen content is a characteristic of duplex steels, which significantly increases their solid solution strengthening and corrosion resistant properties due to the pronounced formation of austenite. As a result, duplex steels can be easily identified through the nitrogen content. On site, this can be achieved only with OES technology, whereas in the laboratory, the benefits of OES technology, as opposed to the combustion method, include complete analysis, significantly easier specimen preparation, and relatively lower operating costs.
In situations where lab analysis is not possible (for example, petrochemical plants, unwieldy items), the combination of UVTouch smart probe and PMI-MASTER Smart portable spark spectrometer from Hitachi High-Tech Analytical Science can be applied to perform a high-performance analysis on site, including the measurement of nitrogen. Optimized excitation, dynamic spectrum evaluation, and the patented optics in lightweight construction allow analysis at close to laboratory level.
In a laboratory setting, the smallest stationary OES analyzer, for example, Hitachi High-Tech Analytical Science’s FOUNDRY-MASTER, has a working range of 0.05%–1.2% as well as a precision level that is only seen in relatively larger spark spectrometers.
The Basics of Duplex Steel Composition
Chromium (Cr), Molybdenum (Mo), Nitrogen (N), and Nickel (Ni) are four alloying elements that are responsible for the main properties. Cr is a ferrite former and gives the required corrosion resistance even at very high temperatures. Mo supports the effects of Cr and significantly increases the resistance against crevice and pitting corrosion in chloride-containing environment. While Mo is also a ferrite former, its concentration is often restricted at 7.5% maximum.
The cheap alloying element Nitrogen has a major effect on the properties, but it also supports corrosion resistance and considerably boosts the strength and toughness of the Duplex Steel. Nitrogen also plays an important role during fabrication—it delays intermetallic phase forming and thus conserves the dual microstructure during the fabrication steps. It is a strong austenitic former and hence can replace some costly Nickel in the alloy.
The last alloying element Ni is the austenitic stabilizer which causes the crystal structure to change from body-centered cubic (ferritic) to face-centered cubic (austenitic). A typical chemical composition of duplex steel (1.4462, S32205) includes 22.5% Cr, 0.03% C, 0.18% N, and 3.25% Mo.
Due to their better corrosion resistance and higher strength, duplex and super-duplex steels are being used more and more often in apparatus and pipeline construction over the last few years, either as base materials or also for the entire welded structures. Since duplex steel is easy to distinguish based on the nitrogen content, we use a spark spectrometer from Hitachi High-Tech, FOUNDRY-MASTER Optimum, for testing.
Guido Odenthal, Engineering Office, Odenthal
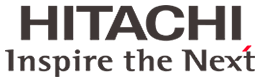
This information has been sourced, reviewed and adapted from materials provided by Hitachi High-Tech Analytical Science.
For more information on this source, please visit Hitachi High-Tech Analytical Science.