The use of electroless nickel (EN) plating as a method for providing lightweight materials with higher durability, greater corrosion performance, and enhanced fuel efficiencies was introduced more than five decades ago. The method was rapidly implemented into the transportation, aerospace, and automotive industries and was also considered to be an alternative to plating with chrome due to its ability to satisfy engineering requirements for environmental regulation.
.jpg)
Image Credit: FM Callahan
In today’s transportation industry, EN applications have been broadly accepted for parts such as valve bleeds, break pins, aluminum fuel filters, fuel injection systems, bearings, and gear assemblies. One more important benefit of EN is its potential to make deposits of uniform thickness despite the complex geometries and shapes of the piece.
Microspot X-Ray Fluorescence for Quality Control and Screening of a Plating Process
X-ray fluorescence (XRF) instruments have been a field-tested technique for determining coating thickness and elemental composition for relatively large features and bulk materials. Since prevalent microspot XRF instruments are increasingly specialized to meet more demanding analytical requirements, they measure small samples and features by minimizing a large primary X-ray beam down to the micrometer level. This allows the measurement of more complicated applications, such as multi-layer coating systems and alloy coatings. Since microspot XRF allows non-destructive measurement of composition and thickness, it is an appropriate testing method. It needs only a few seconds to provide real-time, repeatable, and accurate analysis without using purge gases or chemicals.
Determining Coating Thickness and Chemical Composition Simultaneously
Developments to microspot XRF, for instance, high-definition silicon drift detectors (SDD) have also enabled the measurement of phosphorous as well as nickel content directly under air path, thereby allowing simultaneous determination of both the chemical composition and the coating thickness.
Microspot XRF has transformed into an important method to enable critical coating thickness analysis for quality control through the entire EN process. It assists in precisely measuring the deposition when the sought-after result is to make an alloy of phosphorus and nickel in differing ratios. As the chemical and physical characteristics of EN critically rely on the basic phosphorus content (%P), it is significant to verify the concentration of phosphorous to ensure a homogeneous distribution of the coating thickness and to achieve the desired phosphorous content accordingly.
XRF inspires engineers dedicated to quality control/assurance standards to measure the coating thickness at any stage of the plating process, starting from incoming inspection up to the final quality check. The application of XRF analysis through the entire plating process leads to various advantages such as compliance to standards and cost optimization. It also assists in ensuring smooth functionality and longer service life of the finished product or assembly. Most significantly, XRF analysis can help manufacturers to prevent expensive recalls of products and components, and it can save a company from irrevocable damage due to product failures.
As a latest addition, the high-performance FT150 analyzer, consisting of a polycapillary optic with a beam size of <20 µm, enables non-destructive, precision analysis of electroless nickel coatings used in the electronics industry. Its versatile, robust design is appropriate even for the highly difficult industrial conditions. Further information on the coatings products of Hitachi High-Tech can be obtained from the company website.
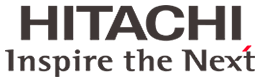
This information has been sourced, reviewed and adapted from materials provided by Hitachi High-Tech Analytical Science.
For more information on this source, please visit Hitachi High-Tech Analytical Science.