Optical Emission Spectroscopy, or OES, is a reliable and extensively used analytical technique used to establish the elemental composition of a wide range of metals.
The type of samples which can be analyzed using OES include samples from the melt in primary and secondary metal production, and in the metals processing industries bolts, tubes, wires, rods, plates and so on.
OES uses the part of the electromagnetic spectrum — the visible spectrum and part of the ultraviolet spectrum. That’s from 130 nanometers up to around 800 nanometers, in terms of wavelength.
.jpg)
Electromagnetic Radiation Spectrum
OES is capable of analyzing a wide range of elements from Lithium to Uranium in solid metal examples covering an extensive concentration range, providing low detection limits, high precision, and very high accuracy.
The elements and concentrations that can be determined by OES analyzers depend on the material being tested and the type of analyzer used.
.jpg)
How Does Optical Emission Spectroscopy Work?
There are three major components of OES analyzers: the first is an electrical source to trigger atoms within a metallic sample so that they produce characteristic light, or optical emission, lines, requiring a small part of the sample to be heated to thousands of degrees Celsius. This is achieved using an electrical high voltage source in the spectrometer through an electrode. The difference in electrical potential between the electrode and sample generates an electrical discharge, which enters the sample and causes the material at the surface to heat and vaporize. The atoms of the material are subsequently excited, emitting the element-characteristic emission lines.
It is possible to produce two forms of electrical discharge, either an arc which is an on/off event just like a lightning strike, or a spark which is a series of multi-discharge events where the electrode’s voltage is switched on and off. Based on the element measured and the accuracy required, these two modes of operation are employed.
An optical system is the second component. The light - the multiple optical emission lines from the vaporized sample called plasma — enters the spectrometer. The incoming light is split into element-specific wavelengths by a diffraction grading in the spectrometer and the intensity of light for each element-specific wavelength is measured by a corresponding detector. The intensity measured is proportional to the concentration offset element in the sample.
.jpg)
A computer system is the third component. The computer system obtains the measured intensities and processes this data through a predefined calibration to produce elemental concentrations. The user interface guarantees minimal operator intervention with clearly displayed results, which can be either printed or stored for future reference.
How to Generate Element-Specific Optical Emission Lines from a Metallic Sample?
When an atom interacts with the energy of an electrical discharge, some of the electrons in the outer shells of the atom are ejected. Since outer-shell electrons are further away from the nucleus, they are less tightly bound to the nucleus of the atom and hence require less input energy. The ejected electrons make the atom unstable by creating a vacancy.
In order to restore stability, electrons from higher orbits which are further away from the nucleus drop down to fill the vacancy. As the electrons move between the two energy levels or shells, excess energy is released and this is emitted in the form of element-specific light or optical emission.
.jpg)
.jpg)
.jpg)
.jpg)
.jpg)
.jpg)
.jpg)
.jpg)
.jpg)
.jpg)
.jpg)
.jpg)
A series of spectral lines, which correspond to different electron transitions between the different energy levels or shells, is emitted by every element. Each transition generates a particular optical emission line with a fixed wavelength or energy of radiation.
For a typical metallic sample containing manganese, iron, nickel, chromium, vanadium, etc., each element emits many wavelengths, resulting in a line-rich spectrum. For instance, iron emits just over 8000 different wavelengths, which means it is important to select the optimum emission line for a given element in a sample.
The atoms emit the characteristic light, which is transmitted to the optical system where it gets separated into its spectral wavelengths by the high-tech grading containing up to 3600 grooves per millimeter.
.jpg)
Next, the detectors collect the individual spectral line peak signals and process them to create a spectrum that shows the light intensity peaks versus their wavelengths. This implies that OES offers qualitative information about the sample measured, but it is also a quantitative technique.
The element is identified by the peak wavelength, and its quantity in the sample is indicated by its peak area or intensity. This information can then be used by the analyzer to calculate the elemental composition of sample based on a calibration with certified reference material. The time taken by the entire process, from pressing a start button or a trigger to getting the analysis results, can be either 3 seconds or it can be up to 30 seconds for complete accurate quantitative analysis; it all relies on the type of analyzer used, the range of elements quantified, and the concentrations of those elements.
OES has many advantages when compared to other analytical techniques: it is fast, quite easy to use, and measures a broad range of elements and concentrations in various types of materials, including significant elements such as carbon, phosphorous, sulfur, nitrogen, and boron. When measuring low levels of trace and tramp elements, OES is very accurate and relatively low-cost when compared to other methods.
OES is the preferred method for trace analysis of metals. At present, OES is the only method which can analyze nitrogen and carbon on site, out of the laboratory.
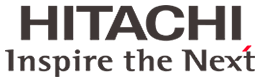
This information has been sourced, reviewed and adapted from materials provided by Hitachi High-Tech Analytical Science.
For more information on this source, please visit Hitachi High-Tech Analytical Science.