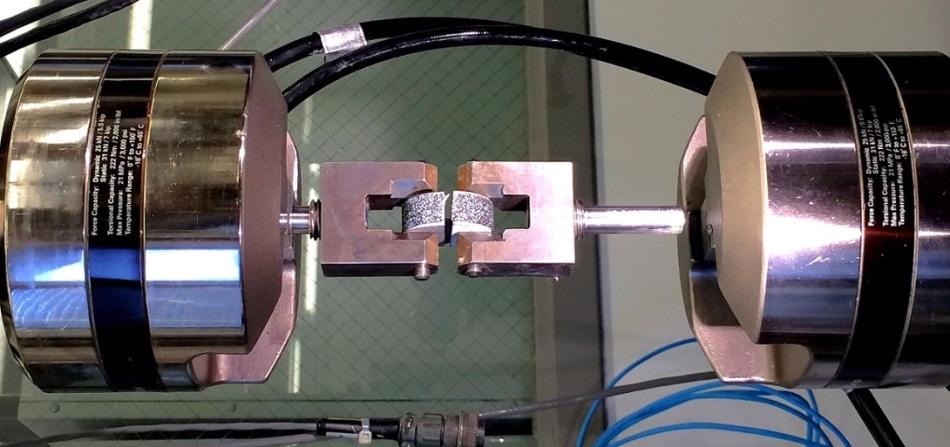
Dursan® is proprietary and patent pending coating designed to improve durability, inertness, fouling and corrosion resistance of products. It is NSF certified and FDA compliant, and has applications ranging from precision instrumentation to complex industrial applications.
The coating’s manufacturer, SilcoTek recently tasked their Research & Development team with thoroughly testing the coating’s durability, strength and bend resistance through a series of gruelling tests and experiments.
What About Wear Resistant CVD Coatings?
CVD coatings are designed to be thin, which could lead some people to think that they are not as resistant to wear as their thicker counterparts. The team tested Dursan® against uncoated stainless steel in a comparative pin-on-disk wear test, concluding that Dursan® was not only more wear resistant than the stainless steel, but also had a higher surface lubricity. This makes the wear resistant coating an ideal solution for both wear prone surfaces and valve components.
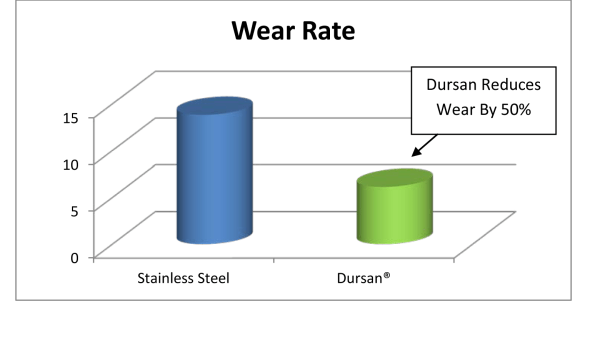
Mechanical Properties of Coating
The team also tested the tensile strength of an uncoated 316 stainless steel rod with a 1“ diameter against a similar rod that had been coated with Dursan®. The samples were pulled to test their ultimate tensile strength, with the untreated rod failing during this process. The following video shows an example of the kind of test performed.
Test results showed that the Dursan® coating performed at or above the uncoated material in ultimate tensile performance, with the Dursan® coated rod failing at 96,000 psi at ambient temperature.
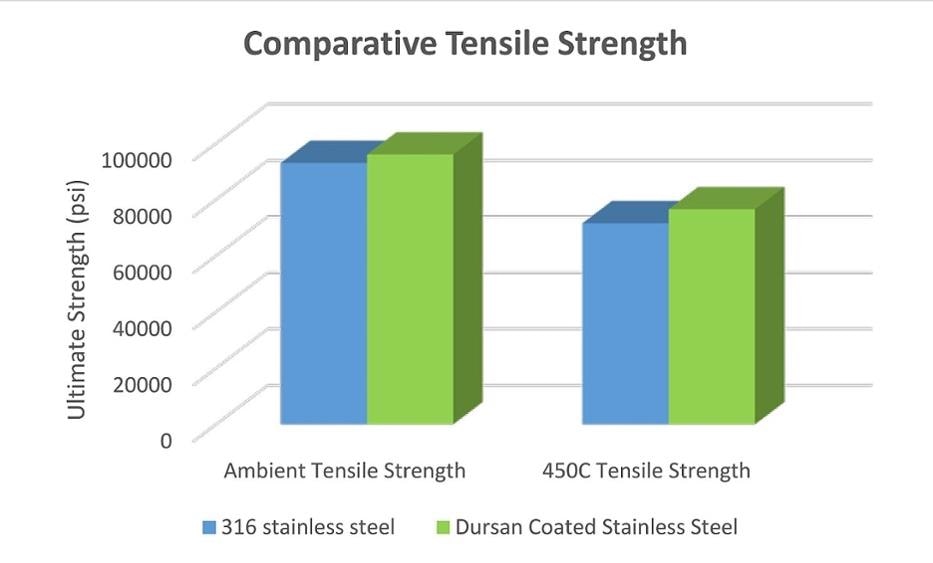
The test was repeated at 450 °C to check for changes in the relative tensile strength of the rod. Here the ultimate tensile strength was reduced as was expected, but with the strength of the Dursan® coated rod dropping only 20% compared to a drop of 23% for its uncoated counterpart.
Comparative tensile strength
Material |
Ambient Tensile Strength |
450C Tensile Strength |
316 stainless steel |
93000 |
71500 |
Dursan® Coated Stainless Steel |
96000 |
76500 |
Crush Testing
Next, the team coated a foil sheet with Dursan® then crushed this alongside a stainless steel ball to check that the coating would continue to adhere to the surface. A coated stainless steel foil sheet was compared next to a painted foil sheet, with both being balled up to test for flaking of the coating. In both cases, the coating continued to adhere to the surfaces.
Bend it, Smash it, Ball it up - SilcoTek® Coatings Won't Flake like Paint
A press was then used to crush a coated stainless steel ball in order to see if this increased pressure would result in flaking. The coating continued to remain in place during this test and additionally, the test was varied by bending a coated tube, again yielding similar results and showing no evidence of flaking.
Lastly, a coated sample was heated with a flame to test for potential burning, flaking, oxidization or even combustibility. Once again, the coating was able to withstand the extreme temperatures, as can be seen in the video below.
The Flexibility of SilcoTek® Coating Solutions
While the Dursan® coated sample glowed bright red during heating, it then cooled with no obvious damage or oxidization. However, the stainless steel sample was highly oxidized following exposure to the heat, and the PTFE sample was severely damaged.
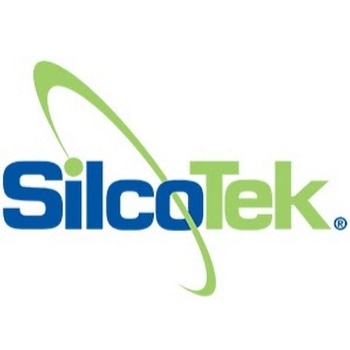
This information has been sourced, reviewed and adapted from materials provided by SilcoTek.
For more information on this source, please visit SilcoTek.