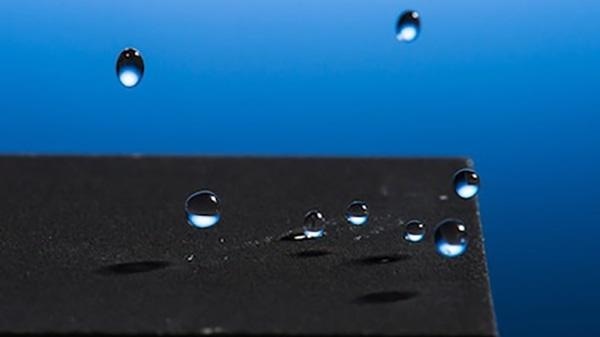
How does one go about improving high temperature hydrophobicity and oleophobicity in fuel injector and combustion applications? This question has been answered by SilcoTek through the development of their new high temperature moisture and oil repelling coating, capable of withstanding temperatures of up to 300C.
The article will feature information on:
- How SilcoTek’s new Notak coating impacts surface energy, hydrophobicity, oleophobicity and fouling resistance
- How altering surface energy is able to subsequently alter moisture resistance, hydrophobicity and oleophobicity
- The advantages of a hydrophobic coating surface
- The advantages of an oleophobic coating surface
The newest coating from SilcoTek, Notak, demonstrated significant improvement in hydrophobicity and oleophobicity when compared to an uncoated DLC surface. Furthermore, Notak remained stable when exposed to high temperatures for an extended period of time, in this case over 24 hours. The surface energy seems to have remained stable during this time, as indicated by both the hydrophobicity and oleophobicity contact angle remaining unchanged.
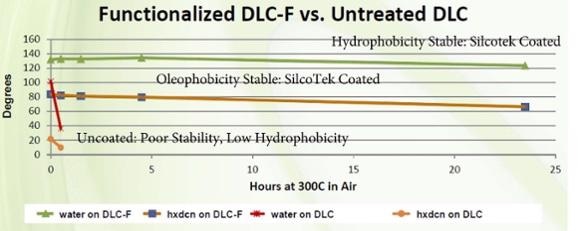
SilcoTek coatings represent the ideal solution for companies looking for a hydrophobic and oleophobic coating for use in even the most challenging of environments. Applications for such coatings could include:
- Analytical sampling
- Refining/petrochemical
- Oil and Gas exploration and transport
- Automotive
- Aerospace
- Heat exchangers
- Process sampling
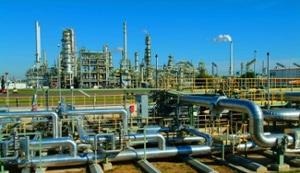
Information pertaining to the prevention of fouling and management of moisture resistance can be viewed on SilcoTek’s “webinar”:
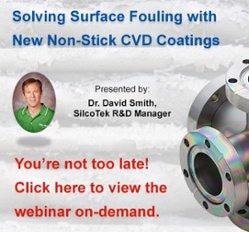
"Solving Surface Fouling with New Non-Stick CVD Coatings"
SilcoTek’s inert, highly durable and highly tolerant coatings can be applied to high precision components for use in the most extreme conditions and demanding environments:
- Fuel injectors
- Nozzles
- Probes
- Separators
- Downhole tools

About Hydrophobicity and Oleophobicity: a Comparison
What constitutes a hydrophobic surface? A hydrophobic surface is one which is water-repellent, with a low surface energy which is resistant to wetting. In order to classify as hydrophobic a material must have a moisture contact angle of a water droplet exceeding 90 degrees. Should this angle exceed 150 degrees then the material is instead classed as superhydrophobic. In this case water will jump right off the surface, as can be seen in this video:
There exist many benefits of a hydrophobic, moisture-repelling surface, including:
- Prevention of surface icing
- Improved corrosion resistance
- Produced water filtration & management
- Improved moisture detection instrumentation
- Management of moisture contamination in liquid natural gas systems
- Prevention of condenser & evaporator fouling
- Prevent moisture contamination in heat trace tubing
- Improved reliability in continuous emissions monitors (CEMS)
- HPLC medical diagnostics improved separation & corrosion resistance
- Prevent contamination in analytical sample transfer systems
How Do I Get a Surface to Match My Desired Moisture Level of Moisture Resistance?
It is not necessary to make dramatic changes to material or product construction in order to alter the level of moisture performance. Instead, SilcoTek offer silicon barrier coatings, available in a wide range, each offering differing water management capabilities. For example, if it is a corrosion-resistant or inert coating, with a low surface contact angle that you are looking for then try the Silconert 1000 or Silcolloy. If, alternatively, you are looking for an inert coating that’s not overly moisture repellent then try the Silconert 2000. Looking for a maximally water repellent coating? In that case try the Dursan, or the new Notak. It is worth noting, however, that the new Notak is still in pre-production Beta testing and therefore the capacity to supply this coating is currently limited. If you’re uncertain as to the coating needed for your application then the SilcoTek technical service team ought to be able to offer guidance.
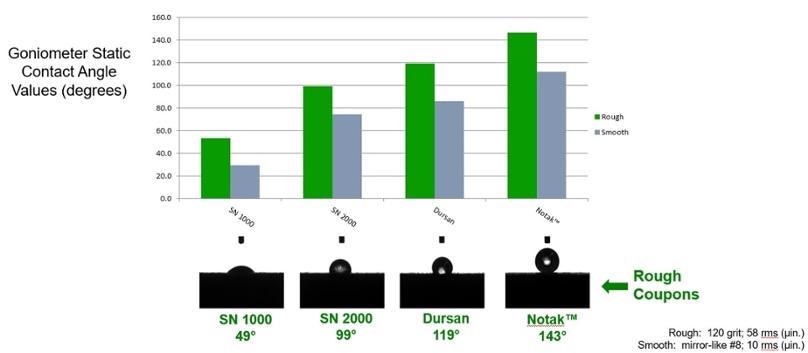
The above graph represents a comparison of each of SilcoTek’s coatings compared with stainless steel, and demonstrates that each of these coatings has specific features corresponding to specific applications. Further information on these applications can be found by accessing SilcoTek’s application guide:
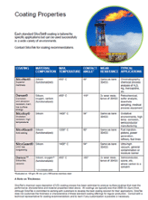
Hydrophilic Surfaces
It is not only hydrophobic surfaces which have their uses, however. Hydrophilic surfaces have their benefits as well. Hydrophilic surfaces are those with high surface energy which attract water and allow wetting of their surface. Normally hydrophilic surfaces will have a contact angle with a water droplet of less than 90 degrees. A wide variety of surfaces tend to be somewhat water friendly, including glass, steel, stainless steel and various coatings and paints.
Some of the benefits of hydrophilic surfaces include:
- Improved separation in medical diagnostics (application dependent)
- Improve acceptance of In-body devices
- Improved efficiency in heat transfer devices & heat exchangers
- Improve surface interaction in filtration devices (application dependent)
High Temperature Oleophobicity
Liquids such as oil, or organic solvents, with a low surface tension can be used to wet the surface for maximum lubrication of solvation. What, however, if you are looking to separate organics or simply don’t want the surface to wet? Hydrophobic materials such as PTFE aren’t effective in repelling oil. Here is an example of what oil and hexadecane look like when placed on a PTFE surface.

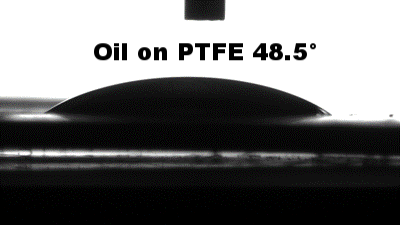
SilcoTek bonded their new Notak coating onto a stainless steel surface in order to examine whether the contact angle would increase. They found that the inclusion of Notak did indeed have a big impact on the contact angle, thus rendering stainless steel an oleophobic material.
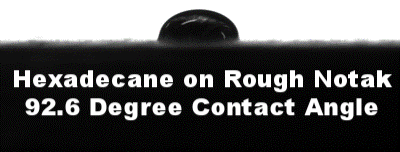
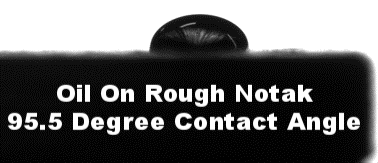
The surfaces of materials used in refining or cleaning processes can be expected to be exposed to elevated temperatures. PTFE can fail during many high temperature applications, whereas Notak has been demonstrated to continue to perform at high temperatures. SilcoTek exposed their new Notak coating to temperatures as high as 300 degrees for several hours in order to investigate the impact of high temperatures to the wettability, oleophobicity and contact angle. As mentioned, Notak demonstrated consistent scores, whereas PTFE fails at 250C. The graph below demonstrates the contact angle readings over a 90 hour test:
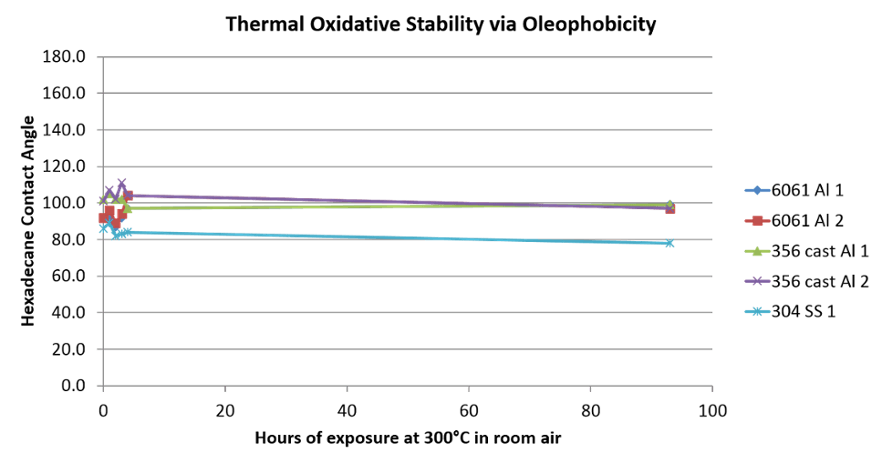
The contribution of surface energy and its relationship to process fluids can have far ranging impacts. Surface interaction can impact corrosion, fouling, analytical sampling results, filtration and medical device performance. So it's important to understand how to manage the energy of critical flow path surfaces. Get some informative and helpful tips on ways to prevent fouling, change surface energy, & improve surface performance.
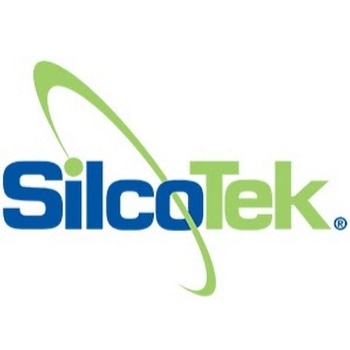
This information has been sourced, reviewed and adapted from materials provided by SilcoTek.
For more information on this source, please visit SilcoTek.