According to IHS Markit, the U.S. manufacturing index increased from 56.5 to 56.6 in May, and Bloomberg reported earlier this year that factories in the UK, Germany, Canada, France, and China were finding it hard to meet the demand.
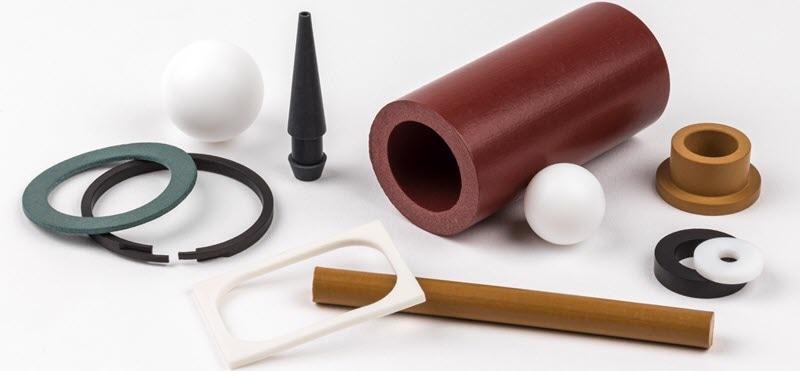
Manufacturing Challenges
Manufacturing is an integral part of people’s lives and crucial to economies. We rely on critical parts in our machinery and products they make to work optimally. Even if a single part fails, it can prove costly in many aspects — from loss of capacity and factory downtime to contamination of products, recalls, and other serious effects. According to the International Society of Automation, downtime is projected to cost the manufacturing industry nearly $650 billion per annum.
At the same time, there are several applications that pose challenging conditions, for example, exposure to chemicals, dry and continuous running, high friction and wear, and extreme temperatures with temperature fluctuation.
Benefits of Rulon® PTFE Material
Rulon® PTFE fluorpolymers is a versatile and high-performance material, which belongs to the series of proprietary, homogenous filled materials that provide low friction and high wear life. This material is often used in industrial applications, and can tolerate adverse conditions such as aggressive chemicals, dry running, and abrasion with the potential to work under extreme pressure and temperature ranges. Over a period of time, several Rulon® grades have been developed for particular custom applications because they can be custom made into wear components, cup seals, piston rings, bearings, and other major parts.
Following are some examples where Rulon® parts are used in critical applications:
- For bearings employed in industrial agitators, pumps, and mixers and also in food and pharmaceutical sectors where it is important to choose the bearing material because contamination can occur when this material wears and disintegrates into formulations
- For piston cup seals used in industrial flow dispensing meters to determine fuels where any differences can lead to financial loss to the consumer or retailer and also for medical portable oxygen concentrators for lifetime operation and sealing precision
- For bonded bearings used in aerospace jet engine thrust reverser because of their resistance to wear, low coefficient of friction, and ability to tolerate short periods of extreme heat
- For slide bearings used in seismic base isolation systems, where a combination of laminated bearing and sliding mechanism operates to absorb strong tremors
While many formulations of Rulon® material such as custom grades are available, only few can fulfill most requirements, including:
- Rulon® LR material is used in bearing applications because it is resistant to high creep and abrasion. It is also suitable for continuous, rotating, non-lubricated sliding, and oscillating applications.
- Rulon® 641 material is an FDA-compliant material and is the only filled PTFE material that has USP Class VI approval for direct contact with human fluids and tissue. This material is frequently used in bearings in food and pharmaceutical industries and can tolerate stringent sanitation requirements. It is also self-lubricating and resistant to stains.
- With one of the lowest levels of coefficient friction in reinforced PTFE materials, Rulon® J material is often used in start and stop applications, for instance in transportation and railway. This material is certified for mass transit in aircraft and trains for specific safety requirements related to smoke, flammability, and toxicity.
Rulon® 123, W2, XL, 142, 488, 957, and 1439 are other popular grades.
Is Rulon® PTFE Solution the Best Material for Specific Application?
The following factors should be considered to find out whether Rulon® material is appropriate for a specific application:
- If a part fails, the system also fails
- Limited or short life leads to increased maintenance
- It has to execute one or more of the following functions:
- Reduce friction
- Reduce weight without affecting performance
- Withstand very high wear
- Provide self-lubrication of the part
- Tolerate very low or high-level temperatures
- Tolerate corrosion from chemicals
How Can You Tell The “Real” Rulon® Material?
Since the early 1950s, Omniseal Solutions has been the exclusive developer of Rulon® material, developing the first blended PTFE material - Rulon® A. The company manufactures the material in-house, which ensures reliable and high-quality standards, right from testing resin at the manufacturing facility to assuring the highest levels of precision monitoring in every step through to the final product phase for each formulation.
All materials are tested for porosity, crystallinity, and molecular weight. Even if one of these requirements is slightly modified, it can possibly improve one property but affect another; hence, it is very important to maintain strict controls. Users are advised to be careful of counterfeit Rulon® suppliers. Omniseal Solutions is the only company that provides genuine Rulon® material.
Omniseal Solutions has a long history of working with developers and OEMs at organizations to adapt Rulon® material and other polymer solutions for their specific requirements. The fluoropolymers are used in infrastructure, transportation, various industrial applications, and also in challenging space applications such as the Mars Rover Curiosity and International Space Station.

This information has been sourced, reviewed and adapted from materials provided by Omniseal Solutions.
For more information on this source, please visit Omniseal Solutions.