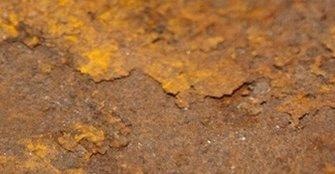
How much does a corrosion resistant coating cost? What is the real cost of buying and maintaining a corrosion resistant surface? Hint — purchasing a cheap one may prove to be the most expensive option.
Corrosion is not just a maintenance issue. It can have numerous adverse effects like poor product yield, damage to costly instrumentation, product contamination, and low productivity. In extreme cases, corrosion can become a real damper on profitability. According to US Government studies, corrosion costs the US $276+ billion per annum, and that’s why there's a massive market in corrosion control. But what is the real cost of applying a corrosion solution?
In this article, you can learn:
- How Silcolloy® and Dursan® corrosion-resistant coatings perform compared to superalloys and stainless steel
- Factors to look into when comparing corrosion-resistant materials or coatings
- Obtain a relative cost of different corrosion-resistant materials
- How life cycle costs can be a huge factor in choosing a corrosion-resistant material
First Consideration — Is the Corrosion Solution Effective?
Before getting into a discussion about the real cost of a specific corrosion solution, it is a good idea to ascertain if the material or coating in question is resistant to chemicals and effective in limiting or preventing corrosion. A comparison of the efficacy of corrosion-resistant materials under different corrosive and temperature conditions is required.
The ASTM G31 immersion test (refer figure below) involves the comparison of an uncoated 316L coupon with Dursan and Silcolloy coated coupons. The coupons were placed in a 20% HCl heated to 50 °C. After seven hours, the coupons were taken out, cleaned, and weighed. Based on weight loss, corrosion rates were calculated. The baseline corrosion solution, stainless steel, showed signs of a very high corrosion rate. If used under similar conditions, it would require repeated maintenance and could possibly impact production if employed in vital performance areas. The Silcolloy coupon had considerably less corrosion but would probably require systematic maintenance. The Dursan coupon had around 1% of the corrosion rate than that of stainless steel, revealing potential benefits to operations cost and maintenance.
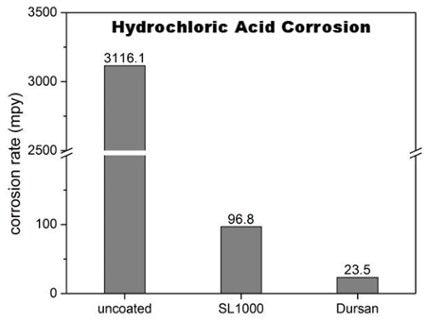
Comparative ASTM G31 immersion testing in a sulfuric acid solution reveals comparable performance with the Dursan-coated coupon performing remarkably in the application with orders of magnitude reduction in corrosion rate.
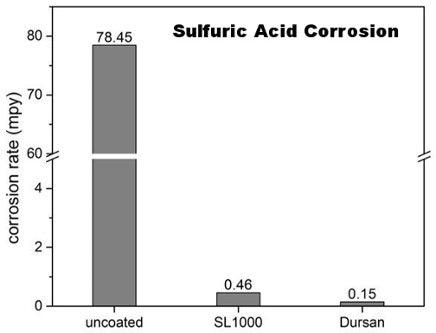
Images of the sulfuric acid test can be seen below. The uncoated 316L coupon is considerably damaged by the sulfuric acid. Furthermore, the acid solution is tainted by the stainless steel, making the fluid turn green. The coated coupons remain intact and the sulfuric acid solution stays uncontaminated. This could safeguard process fluids from impurity and enhance yields.
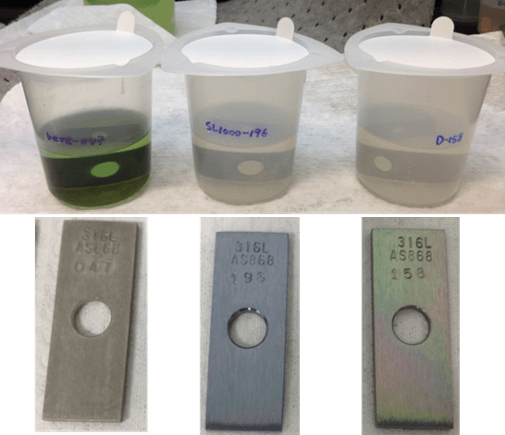
Next, some superalloys were tested for performance. In this comparison, coupons were immersed into 6M HCl for 24 hours and then the corrosion rate was measured. The superalloys, C22 and C276, performed very well, followed by the Silcolloy and Dursan-coated coupons.

The performance of a range of surfaces was compared, and superalloys were noted to perform the best, followed by Dursan coated stainless steel, and lastly stainless steel. Therefore, can it be concluded that the most economical corrosion solution is superalloys? Well, perhaps yes and perhaps no, as it all depends on the application. A comparison of the cost of a range of corrosion resistant products would be useful.
How Much Vs. How Effective? The Cost-Benefit of Corrosion Resistant CVD Coatings
A comparison of the cost of a valve made using a superalloy, Dursan-coated, and stainless steel is required. The stainless steel valve is the most inexpensive, a fraction of the cost of superalloy or Dursan valve. However, the poor corrosion resistance of the stainless steel must be kept in mind. Poor performance could result in the user swapping that cheap valve 10 times during the useful life of the system or project. That makes the stainless steel valve the most expensive at $370.00.
Moreover, that doesn’t include the labor cost related to changing the valve and the lost productivity while the product or process is down. Based on application, the Dursan coated stainless steel valve offers a good blend of enhanced corrosion performance and cost. For a 4x cost increase, one can obtain more than a 10X enhancement in corrosion resistance. The superalloy valve costs around 8x more but does not greatly enhance corrosion performance when compared to the Dursan valve (based on ASTM G31 tests).
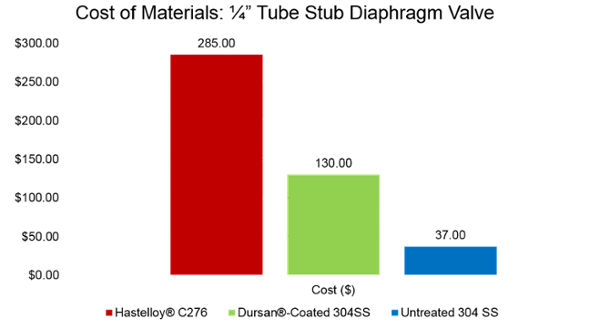
Comparing the life cycle cost of working a standard stack sampling system reveals that after considering capital cost and component replacement cost; Silcolloy or Dursan coated stainless steel surfaces are the obvious cost leader when compared to untreated stainless steel and high-performance alloys.
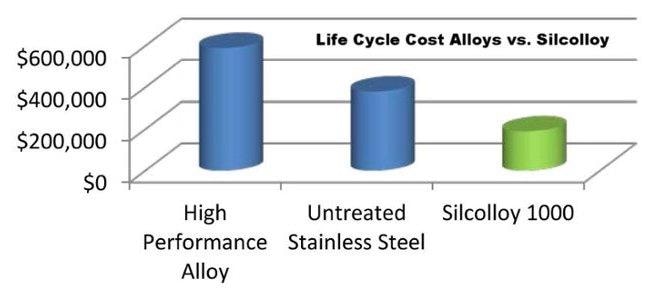
The Big Concern — Picking the Best Corrosion Resistant Material for the Application
Factors to take into consideration when calculating the real cost of a specific corrosion solution include:
- An application’s criticality. If one cannot meet the expense of downtime or a corrosion failure, the superalloy may be a good cover against failure.
- Duration of service. How long will the part be in use? If the part is meant to be used for just a few weeks, a stainless steel component may perform quite well. For intermediate duration or long-term use, Dursan or a high-performance alloy may be a more suitable and economical solution.
- How vulnerable is the process to contamination? If ion contamination or corrosion particulates jeopardize yield or product quality, it may be best to coat the flow path irrespective of length of use. For very high sensitivity to metal ion contamination, coating a high-performance alloy with Silcolloy or Dursan may be the most economical solution. Silcolloy and Dursan do not have metals, making a totally metal-free and corrosion-resistant surface.
- Ease of replacement. How easy is the part to swap? Ease of access may factor in choosing an economical corrosion solution.
- Cost of part. If the part is a costly instrument probe, it would be very cost effective to coat the part using Dursan.
It's obvious that material cost is not the sole factor when choosing a cost-effective corrosion solution. All factors must be carefully considered before selecting a corrosion resistant product.
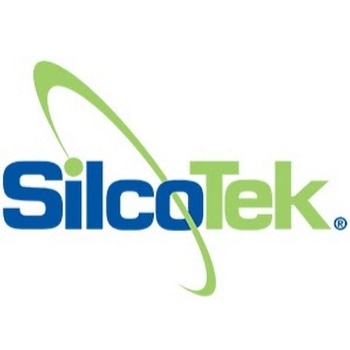
This information has been sourced, reviewed and adapted from materials provided by SilcoTek.
For more information on this source, please visit SilcoTek.