Interview conducted by Mychealla RiceJul 3 2018
In this interview, Eric Dabe from Nel Hydrogen talks to AZoM about hydrogenation, the products that are generated from it and the advantages it can provide.
What is hydrogenation?
Hydrogenation is a chemical reaction between molecular hydrogen and an element or compound, ordinarily in the presence of a catalyst. The reaction may be one in which hydrogen simply adds to a double or triple bond connecting two atoms in the structure of the molecule or one in which the addition of hydrogen results in dissociation (breaking up) of the molecule (called hydrogenolysis, or destructive hydrogenation).
The catalysts most commonly used for hydrogenation reactions are the metals nickel, platinum and palladium and their oxides. For high-pressure hydrogenations, copper chromite and nickel supported on kieselguhr (loose or porous diatomite) are extensively used.
.jpg)
Hydrogenation is a chemical reaction between molecular hydrogen and another compound or element. Image Credits: shutterstock.com/SararwutJaimassiri
What products are made using hydrogenation?
Hydrogenation is widely used in the industry. Hydrogenation is used to solidify, preserve or purify many products, raw materials, or ingredients. Ammonia, fuels (hydrocarbons), alcohols, pharmaceuticals, margarine, polyols, various polymers and chemicals (hydrogen chloride and hydrogen peroxide) are products treated using a hydrogenation process.
The most commonly hydrogenated product is vegetable oil. Hydrogenation converts vegetable oil from a liquid to a solid or semi-solid fat. D-Sorbitol syrup is made by hydrolysis of starches to make dextrose, the dextrose is then hydrogenated to create sorbitol or sugar alcohol. In the Petroleum Industry hydrogenation is used in a process called hydrocracking which breaks heavy crude’s long hydrogen carbon chains into lighter petroleum products like diesel, gasoline and jet fuel.
.jpg)
Vegetable oil is one of the components that is converted from Hydrogenation. Image Credits: shutterstock.com/NaypongStudio
How is hydrogen used in hydrogenation?
Hydrogen is usually used as reducing agent and will lose its electron in a chemical redox reaction. However, it behaves as an oxidizing agent when reacting with metals.
What are the different types of Industrial hydrogenation and what are their hydrogen requirements?
A Batch Hydrogenation Reactor: is a large pressurized vessel that contains a heating element or jacket and an agitator. The substrate is heated and the catalyst is suspended in the substrate. Hydrogen is then introduced at pressure and agitation is used to ensure complete blending of the chemical starting material, hydrogen and catalyst particles.
The process requires heat to initiate, but may become exothermic once hydrogenation has begun in earnest. The hydrogenated substance is then filtered to remove the catalyst particulate. This method of hydrogenation is commonly used for processing edible fats, and manufacturing pharmaceuticals. Batch reactors require that the delivery rate of hydrogen to the reactor vary depending on the stage of hydrogenation completeness.
A Continuous Flow/Tubular/Fixed Bed Reactor: is a tube-shaped reactor with an integrated heating element and a fixed catalyst bed. The hydrogen is introduced at high pressure and distributed throughout the substance as a gas. The heated substrate is circulated through the reactor at pressure, exposing the hydrogen and substance to the fixed catalyst bed.
Any unused hydrogen is recycled. This is the most efficient hydrogenation reactor design, it is employed in petroleum purification, and in small and large scale pharmaceutical manufacturing applications. This reactor design requires large volumes of hydrogen at high pressure.
.jpg)
Hydrogenation is used in applications such as pharmaceutical manufacturing. Image Credit: shutterstock.com/Gorodenkoff
Where do most process owners source their hydrogen?
Process owners may obtain their hydrogen supply from an industrial gas company as delivered hydrogen, or by leasing on-site generation equipment. Another way process owners can source hydrogen is through a merchant hydrogen supplier.
In this model process owners purchase their hydrogen from an industrial company that has a surplus hydrogen supply, or produces hydrogen as a by-product in their process (e.g. electrolysis of Sodium Chloride NaCl to make chlorine gas, and lye).
Alternatively, the process owner might invest in its own hydrogen production plant (water electrolysis, Steam Methane Reformer, ammonia/methanol cracker), which will generate a sufficient quantity of hydrogen to satisfy their gas needs (captive hydrogen).
What advantages does on-site hydrogen generation provide hydrogenation facilities?
On-site hydrogen generation via electrolysis is an advantageous source of hydrogen gas for many reasons. Electrolysis allows process owners to control their own hydrogen production, tightly monitoring hydrogen quality and production volume. Facilities only produce as much hydrogen as they need, thus reducing stored hydrogen inventory and improving facility safety conditions.
Facilities who opt for on-site generation will never risk a hydrogen shortage or late or a missed delivery by an industrial gas distributor. Electrolysis’s variable cost is tied solely to the cost of electricity and water, offering process owners greater control of their hydrogen production costs vs the market driven costs of distributed hydrogen.
.jpg)
ImageCredit: shutterstock.com/SararwutJaimassiri
Where can process owners go to learn more about how on-site hydrogen generation via Electrolysis can improve their hydrogenation operations?
Hydrogenation process owners should visit https://nelhydrogen.com/ to learn more about the benefits of on-site hydrogen generation via Electrolysis.
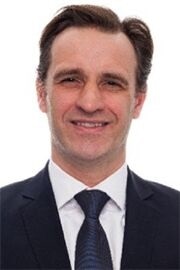
About Eric Dabe
Eric Dabe has a master degree in industrial engineering at the Gramme Institute in Liège, Belgium, and has been working for Nel Hydrogen since 2005.
Eric started his career as a proposal manager for Nel, and has been a sales director since 2007. Eric has over a decade of expertise in alkaline electrolysis technologies and is currently responsible for Europe, sub-Saharan Africa, Eurasia, Central Asia, and Russia.
Disclaimer: The views expressed here are those of the interviewee and do not necessarily represent the views of AZoM.com Limited (T/A) AZoNetwork, the owner and operator of this website. This disclaimer forms part of the Terms and Conditions of use of this website.