Multiple tool inserts, typically between 40 and 60, are usually brazed individually onto a single drill bit, especially when used in down-hole fixed-cutter, hammer, or rock drill rebuild and manufacturing. These inserts could either be tungsten carbide inserts (TCI) or polycrystalline diamond compact (PCD).
An excellent technique for preheating the drill and for preparing the torch brazing of the diamond inserts is induction heating. With drill bits varying in diameters (from 8-20”/ 203-508 mm), it may take between 10 to 30 minutes for the drill bit to heat up. During this time, the insert area for the brazing process is also prepared. The torch is then used to trim the temperature of each individual joint to 790 °C (1454 °F) to flow the braze.
The melting temperature of the insert brazing’s silver and copper eutectic alloy is at 790 °C (1454 °F) which is below the melting temperature of the usual silver or copper. This lowered melting temperature ensures that the diamond bit does not overheat during brazing, while maintaining a strong joint formation to the drill bit.
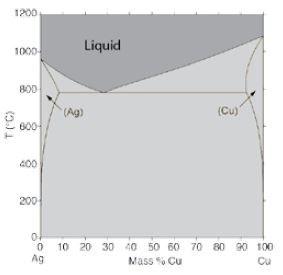
Because the PCD or TCI inserts are primarily used as the drilling tool cutter, they are expected to wear out after some certain period of use. In order to recalibrate the performance of the tool, induction heating may be used. This process allows the inserts to be removed for rebuilding the drill bit.
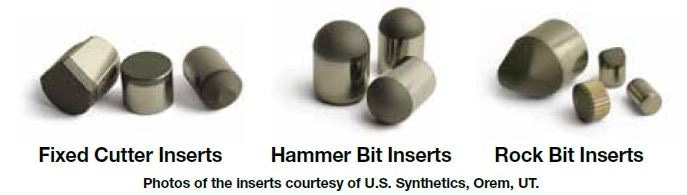
Benefits of Induction Preheating for Brazing or De-brazing
- Safety: preheating cannot be done using a hot furnace or an open flame
- Better efficiency: instantly turns on or off, prevents long flames or overheating
- Throughout: preheating time reduced by induction heating
- Better quality with braze temperature control
- Repeatability: efficiently operates with a consistent, precise quality
- Easy integration into a lean manufacturing process
- Small footprint: compact, able to free up factory floor space
Induction heating is the recommended preheating method for any PCD brazing process as it ensures safety, manufacturing efficiency and throughput, and part quality.
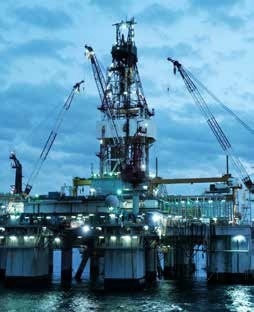
Brazing Diamond or Carbide Inserts Onto Down-Hole Drill Bits
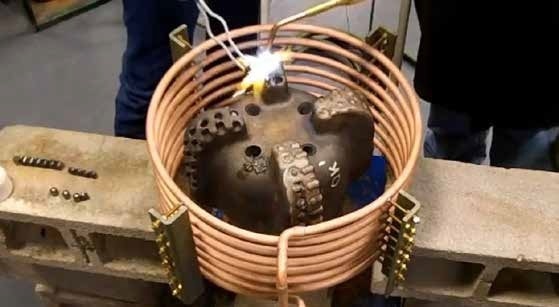
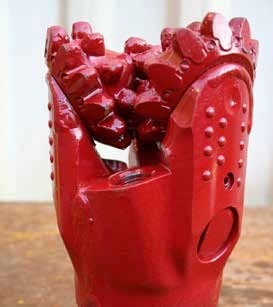
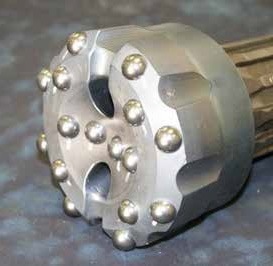
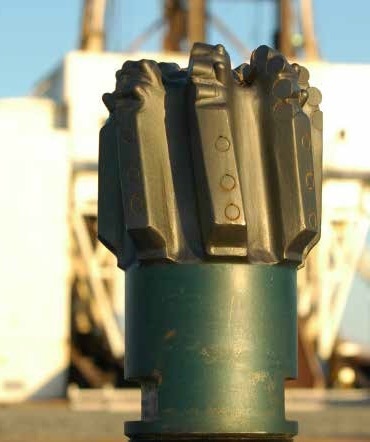
Reducing the Risk of Injury
An open-flame torch or large gas-fired oven is typically used to preheat down-hole drill bits (up to a temperature of 600 °C/1100 °F for insert brazing. Both of these methods, however, are time consuming and unsafe, risking injury to operators by exposing them to an open flame or hot drill bits. Using induction heating removes any safety risk because such method does not use gas torches or ovens during the heating process; furthermore, induction heating allows the final PCD to be brazed without moving the drill bit.
Improving Efficiency and Reducing Costs
In induction heating, the heat is generated from inside the drill bit. Comparably, torches and ovens heat up from the outside, are less efficient, and take more time to preheat the drill bit. Often, heating a drill bit to 600 °C/1100 °F would take two hours using ovens or torches; however, with induction heating, the heating time would only take about 30 minutes.
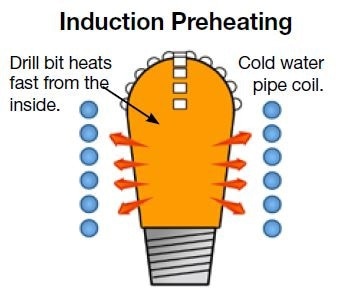
Drill bit is safely preheated to 600 °C (1100 °F) in a quarter of the time, and with instant on/off heating.
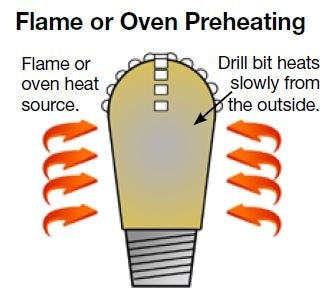
Preheating with torches or ovens expose operators to hot inefficient heat sources.
Ambrell Induction Heating Systems at a Glance
Ambrell promotes a wide power and frequency range with its EASYHEAT™ and EKOHEAT® systems. Regardless of the drill bit that needs brazing, Ambrell’s wide range of systems ensures productivity, efficiency, and cost maximization. Each Ambrell system is equipped with multiple capacitor and tap transformer configurations, ensuring versatile performance for every single use. Additionally, the systems offer efficient power conversion to minimize energy consumption, user-friendly mechanisms that feature agile frequency tuning for repeatable heating, and small footprint size for easier integration into any operational process.
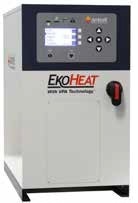
EKOHEAT 30 and 45 and 50 kW
Used in preheating smaller drill bits for insert brazing.
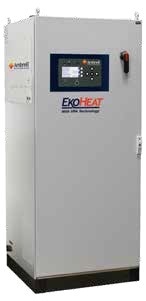
EKOHEAT 125 and 250 kW
Used in preheating the larger down-hole drill bits for insert brazing.
System Inclusions
- Easy integration into the production process (up to 30 mins in some systems) using a remote workhead
- Wide frequency range, allowing more drill bit sizes to be heated within the same induction system
- Multiple capacitor and tap transformer configurations for a more versatile system in comparison with other induction heating products from competitors
- Agile frequency tuning for accurate, repeatable heating
- Efficient power conversion that minimizes energy consumption
- Expert coil designs to maximize power delivery and save production time
- User-friendly interface in five languages (EN, ES, FR, DE, IT)
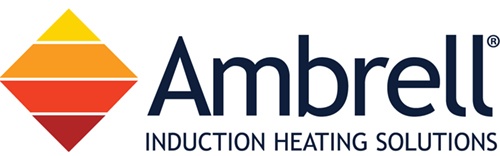
This information has been sourced, reviewed and adapted from materials provided by Ambrell Induction Heating Solutions.
For more information on this source, please visit Ambrell Induction Heating Solutions.