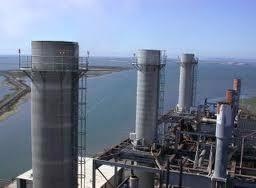
Metal filters are an essential component in process and environmental quality, but due to the nature of their job, they can become clogged and fouled with particulates. This fouling prevents proper flow through the filter and can lead to disruption of normal operations. This article will talk about steps that can be taken to reduce fouling and improve filter performance, and how to save a lot of money while doing so.
In this article you will learn:
- How the surface energy, lubricity and fouling properties of a surface can be altered through a silicon CVD coating
- How coatings like Dursan and Notak can reduce filtration differential pressure.
- How metal filters can be used for a long time by applying an anti-fouling filter, which also prevents membrane fouling.
How Silicon Coatings Change the Surface Properties of Metal Filters
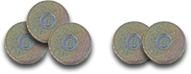
Silcotek uses their patented chemical vapor deposition process to bond coatings such as Dursan and Notak™ to the surface of metal filters. This coating passes through the filter and creates a micro barrier coating across the filter, that bonds and penetrates deep within the material to create a corrosion and fouling resistant surface with high lubricity. This coating can even be applied to sintered metal frits. The image below shows the depth profile of the sputtering process and the way in which the silicon bonds to the stainless-steel filter surface.
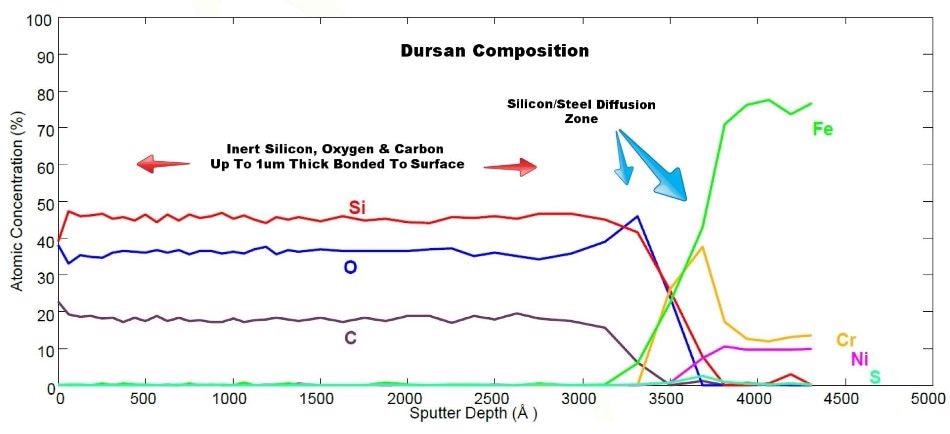
Once the bond has taken, the filter will behave with the properties of the surface coating, with enhanced corrosion resistance, fouling resistance, lubricity, surface energy/ hydrophobicity.
Wear and Friction Data
Under a pin-on-disc wear test, Dursan (carboxysilane) was compared to an oxidized stainless-steel surface. The test showed a 50% reduction in wear rate and a 35% reduction in coefficient of friction of the Dursan over the stainless steel. This leads to a treated filter with a greatly improved efficiency and wear resistance.
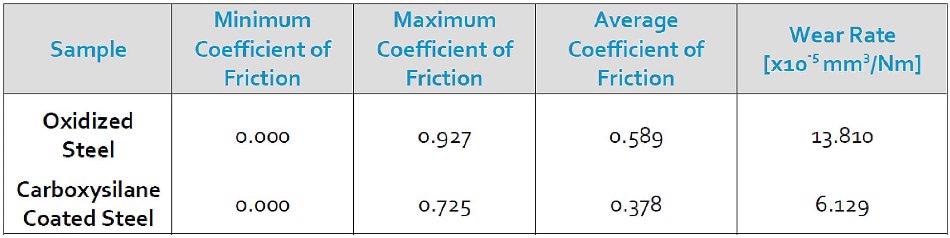
Carbon Coking Fouling Resistance
Silcotek coatings and coatings applied with a surfactant were examined in coking and fouling studies. This reduced fouling by 50% or greater, lessening the particulate binding effect and enabling easier cleaning of the filter.
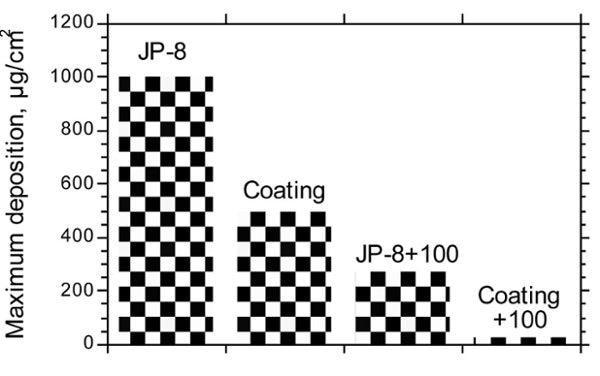
Corrosion Resistance
A Dursan coated surface was compared against silicon and uncoated stainless steel for corrosion resistance in the ASTM G31 immersion test. It was found that the Dursan coated surface had a corrosion resistance and order of magnitude greater than the other coatings, greatly improving metal filter durability.
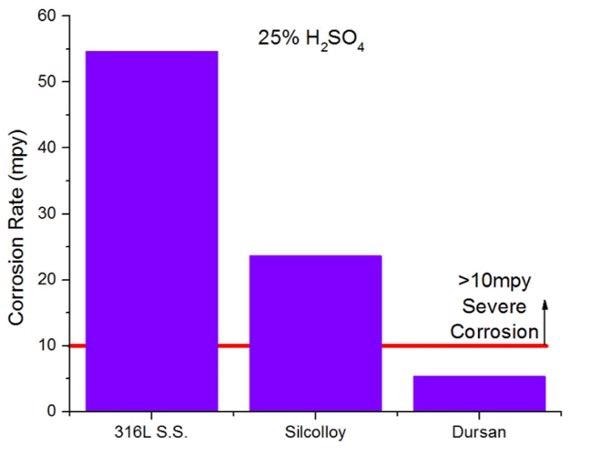
Surface Energy
Surfaces with a low surface energy will reduce the particulate bond energy and make cleaning the filter much easier, so it is important that surface energy management is taken into account. Of any silicon surface tested, those such as Notak™ (F-Dursan in the graph) offer the lowest surface energy and highest contact angle, with a reduction in surface energy of over 80% when compared to stainless steel.
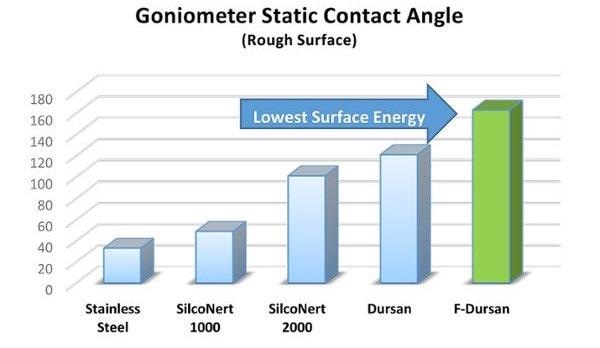
What's it all Mean? How Does a Low Friction Low Surface Energy Surface Prevent Membrane Fouling?
How does having a low surface energy, high lubricity filter surface lead to fouling prevention and improved filter performance? Consulting the graph below, it can be seen that when comparing the differential pressure of the uncoated filter (top 2 lines) with a Dursan-coated filter, the coated filter had nearly twice the life and half the differential pressure of the uncoated filter. Conclusive evidence that Dursan or other Silcotek coatings can aid in increasing the lifetime of your metal filter while reducing energy loss and system back pressure.
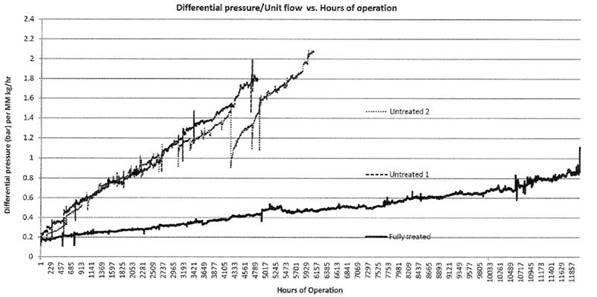
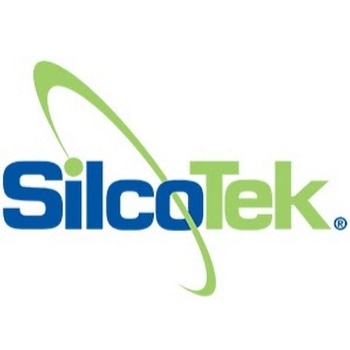
This information has been sourced, reviewed and adapted from materials provided by SilcoTek.
For more information on this source, please visit SilcoTek.