The times, they are a changing sang Bob Dylan about the altering political landscape in the 1960s. His words ring true today, but could now be applied to the state of manufacturing industry as it enters a new millennium. The growing power of computers has been the catalyst for major transformations in the sector, such as the changes in machining practice and the growth in CNC technology. More recently, there has been a change in philosophy in component manufacturing, paralleling the benefits of computation. There is a discernible move away from the energy inefficient and wasteful practice of machining off material, towards more efficient net-shape fabrication. This in turn has allowed production engineers and product designers to improve productivity, lower manufacturing costs and improve product performance. These innovative technologies, which include net-shape manufacturing, microtechnology, rapid prototyping and rapid manufacturing technologies, are helping manufacturers address the demands of the modern marketplace. Powder Injection Moulding One net-shape manufacturing technique, powder injection moulding (PIM), is proving particularly beneficial for making metal, ceramic and cermet components. The latest improvements to the PIM process are broadening its range of applications, enabling the use of ceramics and metals in an increasingly wide variety of complex components. Process Overview PIM uses sinterable powders to manufacture very intricate components. Unlike traditional press-and-sinter powder metallurgy processes, PIM could potentially allow the economic mass production of dense, net-shaped metal, ceramic and cermet components. These ran be geometrically intricate and be produced to close dimensional tolerance. History PIM technology was first used in the 1930s for injection moulding ceramic sheaths to mass produce spark plug insulators. The process was adopted by the investment casting industry in which it is still used for manufacturing ceramic cores. However, PIM attracted little other interest until it was used for the moulding of metal powders in the mid 1970s. This novel application of what was considered a low tech process to a diverse range of particulate systems initiated considerable worldwide research in the following years. The research strengthened the science and knowledge base of PIM, and it is now recognised as a sophisticated, interdisciplinary technology. There is a particular science associated with every stage of the process, which is shown in figure 1. 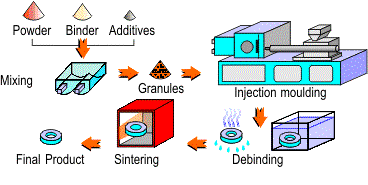 | Figure 1. The powder injection moulding process | Raw Materials The fine sinterable particulates used in the PIM process are mixed with a pliable binder material, which is usually a mixture of thermoplastic polymers, processing aids and a surfactant. The mixture is then heated to form a molten mass of material, which is injected under pressure into a closed mould. The pressure in the cavity is essentially hydrostatic - this produces a homogeneous density distribution in the moulding that can be retained during solidification if the process is controlled carefully. Moulding During injection, the molten material solidifies rapidly and becomes rigid in the mould cavity. This so-called ‘green’ moulding is an exact positive replica of the cavity, including all relevant geometric features. Debinding and Sintering In the final stage of the PIM process, the green moulding undergoes debinding to remove the binder material, and, is then sintered to achieve optimum properties. Sintering the component to its full theoretical density makes it shrink considerably - for a composition containing a volume fraction of solids of 0.65, shrinkage of 13% is typical. Advantages of PIM Geometrical Advantages PIM offers several benefits in component manufacturing. The most advantageous is its ability to mass produce net-shaped components that are geometrically complex. The process gives great versatility and freedom in the design of advanced ceramic, metal, cermet and composite components. Designs previously rejected as too difficult or expensive to manufacture using other production techniques are made commercially possible. Features such as re-entrant angles, multi-shaped blind holes, screw threads, surface profiles, perpendicular holes, undercuts and intricate cavities are all possible using the technology. Economy and Scrap Recycling The prudent use of materials and equipment makes PIM very economical. Machining is eliminated or considerably reduced. In most of the various PIM processes, scrap produced in the form of feed systems, chippings or rejects can be recycled. This is particularly beneficial considering the high cost of some of the materials used. Another bonus is that cermets and ceramics, which are hard and difficult to process, are readily available as fine particulates at a reasonable cost, making them ideal for PIM processing. Fine particles are necessary for achieving high sintered densities in components. Materials Flexibility Another feature of the PIM process is the flexibility of the material composition. Intricately shaped components can be made with a wide range of consistent and reproducible densities. Components can be sintered specifically to create low density structures, which find uses in investment casting cores, insulation, filters, solid oxide fuel cells, substrates for catalysts and pre-forms for the manufacture of electronic packaging and lightweight structural ceramic/metal matrix composites. Blending two or more sinterable particulate systems enables complex components to be formed from novel alloy compositions, such as in situ metal matrix composites and aluminides. Formulations and Binder Issues Debinding Despite all these benefits, there is still room for improvement in the PIM process. Growth in the use of PIM has been inhibited by (often misguided) perceptions of poor dimensional control and protracted debinding time. These are addressed by the latest technology of advanced low pressure moulding, which uses lower injection pressures and higher volume fractions of solids to give improved products. Debinding Time Debinding time for PIM components is roughly proportional to the square of section thickness - a 6mm thick section is typically quoted as needing 24 hours for debinding. However, a factor often overlooked is the amount of binder in the system. Improved dimensional control and quicker debinding of components can both be tackled by reducing the proportion of binder in the material. Having less binder means that a shorter debinding time is needed to remove it, and at the same time means that the particles of ceramic or metal are packed closer together in the green moulding. Such close packing reduces the chance of particle movement during debinding and reduces shrinkage during sintering. As a result, product dimensions can be controlled more closely to improved tolerances. Effects of Reducing Binder Content Reducing the level of binder can cause difficulties though - it usually has an adverse effect on the rheology of the material being injected into the mould. Most problems in PIM are caused by a poor appreciation of composition rheology and thermal-rheology interactions. So to enhance the process, the level of solids must be maximised without compromising the rheology. PIM compositions should ideally have low viscosity and Herschel Buckley attributes - yield stress and pseudoplastic or shear-thinning characteristics. Effect of Maximising Solids Contents There is a maximum level of solids that can be used, above which the material loses reasonable flow properties. This level is determined by the physico-chemical characteristics of the particulates and binder system. In general, increasing the volume fraction of spherical particles above 0.4 has an adverse effect on rheology, as shown by figure 2. The data is derived from a theoretical treatment of heavily filled liquids by Farris. It embodies all that is needed to be known for developing highly concentrated PIM materials. 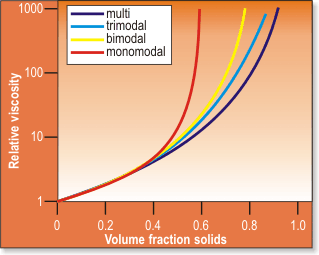 | Figure 2. Effect of particle volume fraction on composition viscosity. | Formulations with high solids contents have advantages such as: • Lower fired/sintered shrinkage • Closer dimensional control. Leading to tighter tolerances • Reduced probability of distortion during debinding • Improved handling strength after debinding • Reduction of debinding time • Reduced firing temperature/time • Reduced grain growth • Improved structural integrity Particle Size Distributions Figure 2 gives two important clues to producing compositions with high levels of particulates. Firstly, a composition with a high solids content can be made while maintaining good rheological properties by increasing the number of different powders used, so creating a wider particle size distribution. However, this approach is rarely used by PIM processors. The industry has seemingly resigned itself to processing compositions with a maximum solids volume fraction of 0.65, considering anything greater than this to be problematical. This attitude partly arises from hasty conclusions in early research on PIM rather than experience. Powder metallurgists generally frown on the principle of mixing particles from small and large size ranges to increase the packing density, as this can lead to preferential grain growth during sintering. Grain growth is detrimental to the properties of the material. However, experience shows that most commercial powders have Gaussian size distributions and so it is possible to mix two powders of similar average size to produce a system in which neighbouring particles do not differ greatly in size. Grain growth is not a problem in these systems. Binders The first step to producing materials for PIM with high levels of particulates therefore is to use a blend of particles with similar sizes, effectively increasing the packing density of the particulate system. In reality, the advantages offered by such an approach can only be realised if a compatible binder is used. Binder systems need to be tailored to each particulate system, as shown from dealing with batch to batch variation in particulate materials. Even subtle differences in particle size distributions, which change the specific surface area of the material, need changes in surfactant concentration. Binder Systems Apart from a few companies that use novel aqueous or solvent based binders, the PIM industry uses two different binder systems. One is based on thermoplastics, commonly low molecular weight polyethylene and polypropylene or, more recently, polyacetal. The other binder systems are wax-based. Polyacetal based binders, patented by BASF, offer a novel way of reducing debinding time polyacetal depolymerises on exposure to an acidic atmosphere which can give rapid debinding if correctly controlled. However, the high viscosity of polyacetal limits the particle volume fraction to no more than 0.6. Melt Viscosity The second clue from figure 2 to forming highly concentrated particulate systems is that the viscosities of compositions are minimised if a wide range of particle sizes are mixed with a low viscosity binder. The relative viscosity is the ratio of the viscosity of the filled system to the viscosity of the base binder system. Relative viscosity increases significantly with solids concentration, and this is almost independent of the number of particle fractions. As the viscosity of the material for PIM needs to be as low as possible, a low viscosity binder is therefore needed. Polyolefin thermoplastic resin binder systems typically have melt viscosities greater than 500 N.m-2s, and so are not useful for forming highly concentrated low viscosity compositions. By contrast, waxes have low molecular weights, low melting points, and melt viscosities of no more than 1Nm-2s - almost three orders of magnitude less than polyolefin resins. The Market for Powder Injection Moulded Parts Metal Injection Moulded Parts A decade ago the market for ceramic and metal PIM products was limited. Products served niche applications and worldwide annual sales totalled no more than $80 million. The enhanced mechanical properties offered by metal PIM products makes them natural competitors in the plastic and alloy die cast components market. However, metal injection moulded (MIM) products have replaced very few traditional plastic and die casting components. Instead a whole new market has grown for MIM products, mainly for complex miniature components. Ceramic Injection Moulded Parts The inherent hardness of ceramics means that manufacturing intricately shaped ceramic components by standard machining processes is very expensive. Prior to PIM, intricately shaped ceramics had a limited market and were only used as a last resort in applications that required their specific properties. Applying PIM technology to advanced ceramics has broadened the use of these materials. Sales of Powder Injection Moulded Products PIM technology has matured and grown rapidly in the past decade. Sales of PIM products now total $700 million and at the current annual growth rate of 22% this is forecast to reach $2.1 billion in the next ten years. The process has deservedly earned recognition as a viable manufacturing technology, and a diverse range of PIM products are used in the chemical, metal casting, ceramics, textile, aerospace, automotive, electronic, medical and communications industries. Summary The PIM process complements the evolution in advanced materials that are now being used in consumer products - injection moulded materials range from 316L stainless steel to more exotic examples such as boron nitride. At the same time, PIM products have become more sophisticated and are used in a diverse range of applications from wear resistant guides and orthodontics to electronics packaging. Sadly, despite the substantial advantages offered by PIM, the application of the technology in the UK is well behind that in mainland Europe, the US and Asia. |